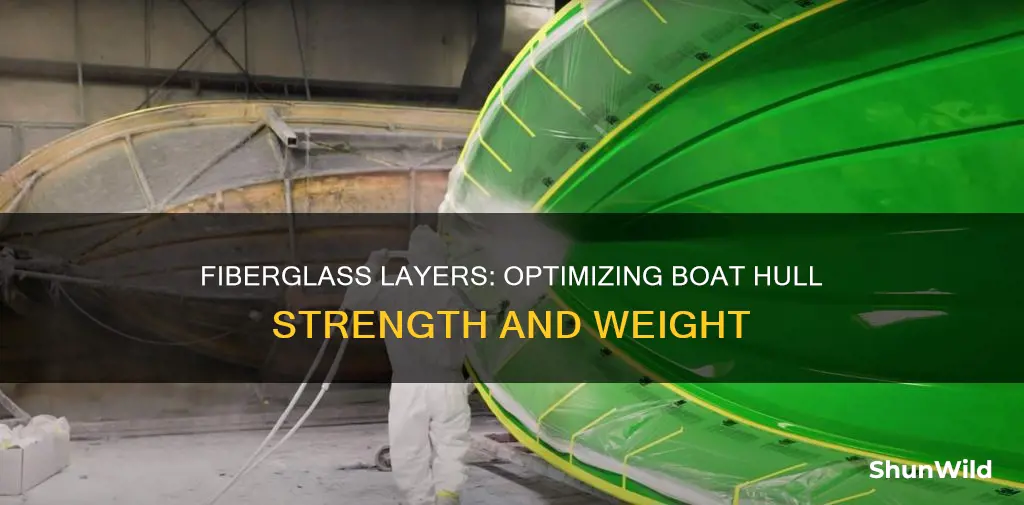
When it comes to building a boat hull, the choice of fiberglass layers is a critical decision. The number of layers of fiberglass used in the construction can significantly impact the boat's performance, durability, and overall quality. In this article, we will explore the factors to consider when determining how many layers of fiberglass are appropriate for your boat hull, including the type of boat, the desired level of strength, and the environmental conditions it will encounter. Understanding these considerations will help you make an informed decision to ensure your boat hull is built to last.
What You'll Learn
- Hull Material: Choose the right fiberglass type for your boat's needs
- Thickness Considerations: Determine the required thickness based on boat size and design
- Layer Placement: Plan the placement of fiberglass layers for structural integrity
- Reinforcement Techniques: Use techniques like vacu-bagging for strong bonds and even distribution
- Environmental Factors: Account for environmental conditions to select appropriate fiberglass layers
Hull Material: Choose the right fiberglass type for your boat's needs
When it comes to boat building, the choice of hull material is crucial, and fiberglass is a popular and versatile option. The number of layers of fiberglass used in the hull construction can significantly impact the boat's performance, durability, and overall quality. Here's a guide to help you understand the considerations and benefits of different fiberglass layers for your boat's hull.
The thickness and arrangement of fiberglass layers play a vital role in determining the boat's structural integrity. Typically, a boat hull requires multiple layers of fiberglass to create a strong and lightweight structure. The number of layers can vary depending on the boat's size, intended use, and desired level of performance. For smaller recreational boats, a standard number of layers, often around 4-6, is sufficient to provide strength and rigidity. These layers are usually arranged in a woven or mat pattern, ensuring even distribution of the material.
For larger, high-performance boats, such as racing yachts or commercial vessels, the number of fiberglass layers can be significantly higher. These boats demand exceptional structural strength and often utilize advanced construction techniques. In these cases, the hull may consist of 8 or more layers of fiberglass, carefully laid and bonded to create a robust and lightweight shell. The additional layers contribute to improved impact resistance, structural integrity, and the ability to withstand the stresses of marine environments.
The choice of fiberglass type is another critical factor. There are various types of fiberglass available, each with unique properties. For instance, woven fiberglass is strong and provides excellent structural support, making it ideal for the core layers of the hull. On the other hand, mat fiberglass is more flexible and can be used for layering, adding additional strength without adding excessive weight. The specific type of fiberglass used can also influence the boat's finish, with options ranging from smooth to textured surfaces.
In summary, the number of fiberglass layers in a boat hull is a critical design consideration. It directly impacts the boat's performance, durability, and overall construction quality. Whether you're building a small recreational boat or a large, high-performance vessel, understanding the relationship between layer count and hull material is essential. By carefully selecting the appropriate number and type of fiberglass layers, boat builders can create vessels that meet specific performance requirements while ensuring a long-lasting and reliable marine experience.
Get a Lost Boat Title in North Carolina
You may want to see also
Thickness Considerations: Determine the required thickness based on boat size and design
When it comes to constructing a boat hull, determining the appropriate thickness of fiberglass layers is a critical aspect of the design process. The thickness of each layer directly influences the structural integrity, strength, and overall performance of the boat. This consideration is especially important for larger vessels, where the load-bearing capacity and stability are paramount.
The size of the boat is a primary factor in determining the required thickness. Larger boats, such as yachts or commercial vessels, typically demand thicker fiberglass layers compared to smaller recreational boats. This is because bigger boats often carry more weight, experience greater forces during operation, and are exposed to more challenging environmental conditions. For instance, a 30-foot yacht might require layers of fiberglass that are 1/8th of an inch thick, while a smaller 15-foot fishing boat could get away with 1/16th of an inch.
The design of the boat also plays a significant role in thickness considerations. Different boat designs have unique structural requirements. For example, a high-performance racing boat might need thinner layers of fiberglass to reduce weight and enhance aerodynamics, while a sturdy workboat designed for heavy-duty tasks may require thicker layers to withstand the rigors of industrial use. The shape and curvature of the hull also influence the number of layers and their thickness. Complex curves and contours may necessitate more layers to ensure proper bonding and structural integrity.
In addition to boat size and design, the intended use and operating environment are essential factors. Boats used in rough seas or extreme weather conditions may require thicker fiberglass layers to provide additional protection against impact, corrosion, and structural fatigue. On the other hand, boats used for leisurely cruising in calm waters might benefit from thinner layers to optimize fuel efficiency and reduce weight.
It is crucial to consult with experienced boat builders and engineers to determine the optimal thickness for your specific boat project. They can provide valuable insights based on their knowledge of boat design, materials, and industry standards. By carefully considering these factors, you can ensure that your boat hull is constructed with the right thickness of fiberglass layers, resulting in a sturdy, durable, and high-performing vessel.
Who is Nicole from Fresh Off the Boat?
You may want to see also
Layer Placement: Plan the placement of fiberglass layers for structural integrity
When it comes to constructing a boat hull, the strategic placement of fiberglass layers is crucial for achieving structural integrity and optimal performance. This process involves careful planning and consideration of various factors to ensure the hull's strength, durability, and overall safety. Here's a detailed guide on how to approach layer placement:
Understanding the Hull Design: Begin by thoroughly understanding the boat's hull design and its intended purpose. Different hull shapes and sizes require specific fiberglass layer arrangements. For instance, a high-performance racing boat might demand a stiffer construction, while a cruising vessel may prioritize comfort and fuel efficiency. Study the design specifications, including the hull's curvature, thickness, and any unique features like stringers or bulkheads. This knowledge will guide your layer placement decisions.
Layer Orientation: The orientation of fiberglass layers is critical to the hull's structural performance. Typically, layers are placed at different angles to the hull's longitudinal axis to create a composite material with enhanced strength. Common orientations include 0-degree (parallel to the hull), 45-degree, and 90-degree layers. For instance, 0-degree layers provide strength in the primary load direction, while 45-degree layers offer additional strength in both directions, making them ideal for areas prone to twisting forces.
Layer Density and Thickness: The number of layers and their thickness are essential considerations. More layers generally result in increased strength, but they also add weight. A typical boat hull might have 4 to 6 layers, with the placement of each layer carefully planned to avoid overlapping in critical areas. Thicker layers are often used in load-bearing zones, such as the keel and stringers, while thinner layers can be employed in less demanding areas. The goal is to create a balanced structure that minimizes weight while maintaining structural integrity.
Strategic Placement: Layer placement should follow a logical pattern, starting from the bottom and working upwards. Begin with the core layers, typically placed near the hull's centerline, providing a strong foundation. Then, add layers around the core, gradually moving towards the outer skin. Pay close attention to areas prone to stress, such as the chines, transom, and hull sides. These regions may require additional layers or thicker glassing to reinforce weak spots. Ensure that layers are properly bonded and aligned, using appropriate adhesives and techniques.
Reinforcement Techniques: Consider incorporating reinforcement techniques to enhance structural integrity. For instance, you can use carbon fiber or kevlar layers in high-stress areas to add strength without significantly increasing weight. Additionally, stringers and bulkheads should be properly integrated into the fiberglass layers to distribute loads effectively. These structural elements provide additional support, especially in longer hulls, ensuring the boat can withstand various loads and conditions.
By carefully planning the placement of fiberglass layers, boat builders can create a robust and lightweight hull, ensuring the vessel's structural integrity and overall performance. This process requires a deep understanding of boat design, material properties, and engineering principles to achieve the desired outcome.
Lake James Boat Launching: Top Spots to Know
You may want to see also
Reinforcement Techniques: Use techniques like vacu-bagging for strong bonds and even distribution
When it comes to reinforcing a boat hull with fiberglass, achieving strong bonds and even distribution is crucial for the structural integrity of the vessel. One effective technique to accomplish this is vacu-bagging, a process that utilizes a vacuum to ensure precise and uniform application of the fiberglass material.
Vacu-bagging involves creating a mold or form for the hull section, which is then covered with a layer of fiberglass cloth or mat. The key to its success lies in the application of a vacuum bag, a specialized bag made of flexible material. This bag is placed over the fiberglass, creating a tight seal. The vacuum is then applied, pulling the fiberglass material evenly across the surface, ensuring no gaps or voids. This technique provides a smooth and consistent finish, eliminating the risk of air bubbles or uneven layers.
The process begins with preparing the hull section by ensuring it is clean, dry, and free of any contaminants. A release agent is applied to the surface to prevent the fiberglass from sticking. The fiberglass cloth or mat is carefully laid out, following the hull's contours, and then the vacuum bag is positioned over it. The vacuum is activated, drawing the material tightly against the hull. This step requires precision to ensure full coverage and a seamless bond.
After the vacu-bagging process, the fiberglass layer is cured according to the manufacturer's instructions. This typically involves exposure to heat and/or sunlight, depending on the type of resin used. Curing ensures that the resin hardens and bonds the fiberglass to the hull, creating a strong and durable structure.
By employing vacu-bagging, boat builders can achieve a high level of reinforcement, ensuring that the fiberglass layers adhere firmly and uniformly to the hull. This technique is particularly useful for complex hull shapes and areas where traditional hand-layup methods might be challenging to execute flawlessly. It provides a consistent and reliable method for reinforcing boat hulls, contributing to their overall strength and longevity.
Mounting Back-to-Back Boat Seats: A Step-by-Step Guide
You may want to see also
Environmental Factors: Account for environmental conditions to select appropriate fiberglass layers
When considering the environmental factors that influence the number of fiberglass layers for a boat hull, several key elements come into play. Firstly, the climate in which the boat will operate is crucial. Boats in regions with extreme temperatures, whether hot or cold, will require additional insulation to maintain structural integrity and passenger comfort. For instance, a boat operating in arctic waters will need more layers of fiberglass to withstand the cold and prevent structural damage. Similarly, boats in tropical climates may require layers to protect against corrosion and UV damage from the sun.
The water conditions are another critical factor. Boats in saltwater environments face the challenge of corrosion, so additional layers of fiberglass can act as a protective barrier, especially in areas prone to erosion or cavitation. For freshwater boats, the focus might be on preventing osmosis and the potential for water absorption, which can lead to structural issues over time.
The type of boat and its intended use also play a significant role. High-performance boats or those used for racing may require more layers of fiberglass to handle the stress and vibrations associated with high-speed operations. Conversely, leisure boats might prioritize comfort and aesthetics, where the number of layers can be optimized for insulation and soundproofing.
Furthermore, the boat's design and construction method are essential considerations. Boats with complex shapes or those constructed using advanced techniques like vacuum-bagging may require specific layering patterns to ensure structural integrity and smooth surfaces. The choice of fiberglass type, such as woven or mat, can also impact the layering process, with different materials offering varying levels of strength and flexibility.
In summary, environmental factors, including climate, water conditions, and the boat's intended use, significantly influence the selection of fiberglass layers. Each factor demands a tailored approach to ensure the boat's hull is robust, durable, and capable of withstanding the specific challenges posed by its operating environment. Understanding these factors is essential for boat builders and owners to make informed decisions about fiberglass layering.
A Guide to Identifying Boat Titles in Minnesota
You may want to see also
Frequently asked questions
The number of layers can vary depending on the boat's design, size, and intended use. For a standard recreational boat, a common practice is to use 6 to 8 layers of fiberglass, with each layer consisting of multiple plies. This provides a good balance between strength, stiffness, and flexibility for the hull structure.
Several factors influence the layer count. The boat's design and intended load-bearing capacity are crucial. For high-performance or heavy-duty boats, more layers might be required to handle additional stress. The thickness and type of fiberglass fabric (e.g., woven, mat, or cloth) also play a role, as thicker or specialized fabrics may need more layers for optimal performance.
While additional layers can enhance the hull's structural integrity and reduce the risk of damage, it doesn't necessarily guarantee improved performance. The arrangement and orientation of the layers are equally important. Proper bonding, reinforcement in critical areas, and a well-designed hull shape are key to achieving the desired performance characteristics.
Excessive layers can lead to increased weight, which may negatively impact the boat's overall performance and fuel efficiency. Additionally, more layers can make the hull construction process more complex and time-consuming. It's essential to strike a balance between structural integrity and practicality.
Consulting with experienced boat builders or marine engineers is recommended. They can assess your boat's specifications, intended use, and design requirements to advise on the optimal layer count. Additionally, following manufacturer guidelines and industry standards can provide a good starting point for your fiberglass hull construction.