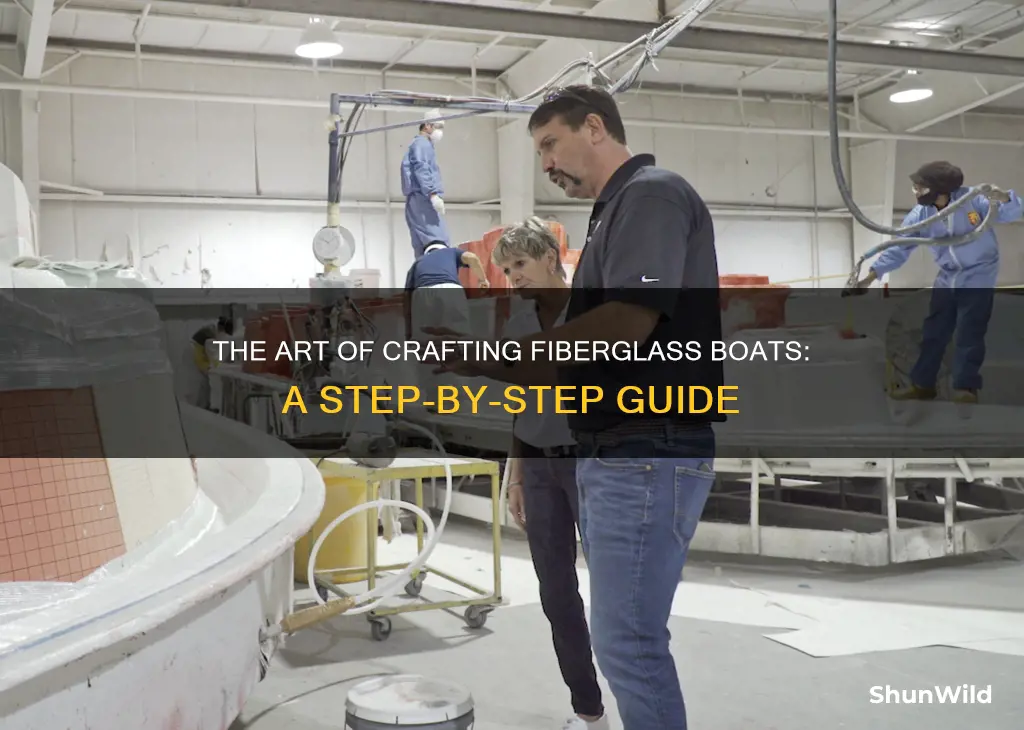
Fiberglass boats are a popular choice for recreational boating, known for their durability, lightweight construction, and sleek design. The manufacturing process of these boats involves several intricate steps. It begins with the design phase, where engineers and designers create detailed blueprints, ensuring the boat's structural integrity and aesthetic appeal. Once the design is finalized, the production process starts with the creation of a mold, typically made from a durable material like epoxy resin. This mold is then used to form the boat's hull, which is carefully constructed layer by layer using fiberglass cloth and resin. Skilled technicians hand-lay the fiberglass, ensuring a smooth and seamless surface. After the hull is cured, additional components such as the deck, cabin, and other accessories are added, all while maintaining the structural integrity and strength of the boat. The final stage involves finishing touches, including painting, interior fitting, and final inspections to ensure the boat meets the highest quality standards.
What You'll Learn
- Fiberglass Material: Specially formulated resins and fibers are combined to create the lightweight, strong material
- Molding Process: Liquid resin is poured into a mold, which is then cured to form the boat's shape
- Layering Technique: Multiple layers of fiberglass cloth and resin are applied to build strength and durability
- Reinforcement Methods: Additional materials like carbon fiber or Kevlar are used to enhance structural integrity
- Finishing Touches: Sanding, painting, and polishing give the boat its final smooth and glossy appearance
Fiberglass Material: Specially formulated resins and fibers are combined to create the lightweight, strong material
Fiberglass is a versatile and widely used composite material, renowned for its exceptional properties in the marine industry. The process of creating fiberglass begins with the careful selection and combination of specific resins and fibers, which are the key components that contribute to its unique characteristics.
Resins, typically epoxy or polyester, serve as the binding agent in the fiberglass matrix. These resins are carefully formulated to possess excellent adhesive properties, allowing them to bond strongly with the fibers and other materials. The choice of resin depends on the desired performance and environmental conditions the fiberglass will encounter. For instance, epoxy resins offer superior bonding and durability, making them ideal for high-performance applications, while polyester resins are known for their ease of use and lower cost.
Fiberglass fibers, often made from glass, are the reinforcing agents that provide the material with its strength and rigidity. These fibers are meticulously arranged and woven into a mat or cloth, ensuring a consistent distribution of material. The glass fibers can be either continuous or chopped, with the latter providing better impact resistance. The fibers are then coated with the chosen resin, creating a homogeneous mixture. This process is carefully controlled to ensure the fibers are evenly dispersed, resulting in a smooth and uniform material.
The combination of resins and fibers is a precise art. The resins are mixed with hardeners and catalysts to initiate a chemical reaction, forming a cross-linked polymer network. This network binds the fibers together, creating a strong and lightweight structure. The process involves careful mixing and application techniques to achieve the desired thickness and shape. The material is then cured, typically through exposure to heat or ultraviolet light, which triggers further polymerization and solidifies the fiberglass.
This specialized manufacturing process allows fiberglass to exhibit remarkable properties, including excellent strength-to-weight ratios, corrosion resistance, and the ability to withstand harsh marine environments. The lightweight nature of fiberglass makes it an ideal choice for boat construction, as it reduces the overall weight of the vessel without compromising its structural integrity. The combination of resins and fibers, through precise formulation and manufacturing techniques, results in a material that is both strong and lightweight, making it a preferred choice for building high-performance and durable boats.
Unveiling the Mystery: Feralas' Boat's Destination Revealed
You may want to see also
Molding Process: Liquid resin is poured into a mold, which is then cured to form the boat's shape
The molding process is a crucial step in the construction of fiberglass boats, as it involves shaping the liquid resin into the desired boat form. This process typically begins with the preparation of the mold, which is a critical component in achieving the desired boat shape. The mold is carefully crafted to ensure it accurately represents the intended design, taking into account the specific contours and dimensions of the boat.
Once the mold is ready, the liquid resin is carefully poured into it. This resin is a key material in the boat's construction, providing strength and durability. The resin is typically a specialized type of epoxy or polyester resin, chosen for its ability to bond with the fiberglass fibers and create a robust structure. The pouring process requires precision to ensure an even distribution of the resin within the mold.
After the resin is poured, the mold is closed, creating a sealed environment. This closure step is essential to initiate the curing process. Curing is a chemical reaction that hardens the resin, transforming it into a solid material. The curing process can be accelerated using heat or specific catalysts, depending on the type of resin used. During this stage, the resin undergoes a transformation, forming a strong and lightweight structure that will become the boat's hull and deck.
The curing time can vary depending on the resin type and environmental conditions. Once cured, the mold is carefully opened, revealing the shaped fiberglass boat. This process ensures that the boat's structure is formed around the mold, creating a seamless and precise final product. The molded boat then undergoes further finishing and assembly processes to become a fully functional vessel.
This molding technique is a fundamental aspect of fiberglass boat manufacturing, allowing for the creation of lightweight, durable boats with complex shapes. It showcases the precision and craftsmanship required in the industry to produce high-quality watercraft.
Repairing a Rip in Your Boat Seat: A Step-by-Step Guide
You may want to see also
Layering Technique: Multiple layers of fiberglass cloth and resin are applied to build strength and durability
The layering technique is a fundamental process in the construction of fiberglass boats, ensuring a sturdy and long-lasting vessel. This method involves a meticulous application of multiple layers of fiberglass cloth and resin, each serving a specific purpose in enhancing the boat's overall performance and longevity.
The process begins with a carefully measured amount of resin, which acts as the binding agent. This resin is mixed with hardeners and catalysts to create a compound that, when applied, initiates a chemical reaction, hardening and setting the material. The resin is then spread onto the boat's hull or any desired surface, creating a thin, even layer. This initial layer is crucial as it forms the foundation for subsequent layers and provides a smooth, cohesive base for the fiberglass cloth.
Next, the fiberglass cloth, typically a woven mat or mat-like material, is carefully laid over the resin-coated surface. The cloth is cut to size and shape, ensuring it fits the boat's contours perfectly. This layer adds strength and rigidity to the boat's structure, especially when multiple layers are applied in a specific pattern. The layering technique often involves a crisscross pattern, where each layer is applied at a slight angle to the previous one, creating a woven effect. This design minimizes the risk of delamination and ensures the boat's structural integrity.
As the layering process continues, each subsequent layer is applied with precision. The resin is mixed and applied again, and the fiberglass cloth is carefully positioned, ensuring proper alignment and coverage. This multi-layered approach adds significant strength to the boat, making it capable of withstanding various stresses and loads during operation. The layers also contribute to the boat's overall weight distribution, making it more stable and less prone to structural failure.
The final result of this layering technique is a boat with an exceptionally strong and durable hull. The multiple layers of fiberglass cloth and resin create a robust structure that can handle the rigors of marine environments. This method is widely used in boat manufacturing due to its effectiveness in providing a lightweight yet robust vessel, making it a popular choice for both recreational and commercial boating applications.
Backyard Boat Painting: A Step-by-Step Guide
You may want to see also
Reinforcement Methods: Additional materials like carbon fiber or Kevlar are used to enhance structural integrity
The use of additional materials such as carbon fiber and Kevlar is a crucial aspect of reinforcing the structural integrity of fiberglass boats. These advanced composites offer exceptional strength and stiffness, making them ideal for enhancing the performance and durability of marine vessels. By incorporating these materials, boat manufacturers can create a robust and lightweight structure that can withstand the demanding conditions of the water.
Carbon fiber, known for its exceptional strength-to-weight ratio, is often used in critical areas of the boat's structure. It is commonly applied in the form of carbon fiber mats or weaves, which are then bonded to the fiberglass layers. This process creates a highly reinforced section, capable of withstanding significant loads and providing excellent structural stability. The carbon fiber reinforcement is particularly effective in areas prone to high stress, such as the hull stringers, ribs, and deck beams, ensuring the boat's overall strength and rigidity.
Kevlar, another high-performance material, is renowned for its exceptional strength and resistance to impact. It is often utilized in the construction of boat hulls and decks, providing an additional layer of protection against damage. Kevlar's lightweight nature allows for easy integration into the fiberglass structure without adding excessive weight. When combined with fiberglass, it creates a composite material that offers superior strength and impact resistance, making it ideal for areas requiring extra protection, such as the boat's bottom and sides.
The process of incorporating these reinforcing materials involves careful planning and application. The carbon fiber or Kevlar is typically laid up in specific patterns, ensuring optimal load distribution and structural integrity. These materials are often bonded to the fiberglass using specialized adhesives, creating a strong and durable bond. The construction process may also include the use of pre-impregnated carbon fiber or Kevlar fabrics, which are pre-coated with a resin, simplifying the manufacturing process and ensuring a consistent and high-quality finish.
By utilizing carbon fiber and Kevlar in the construction of fiberglass boats, manufacturers can significantly improve the vessel's structural integrity. These materials provide enhanced strength, stiffness, and impact resistance, allowing the boat to withstand the rigors of marine environments. The careful integration of these advanced composites into the fiberglass structure ensures a lightweight yet robust boat, capable of delivering an exceptional performance and longevity.
Finding a Boat: Name Search Techniques
You may want to see also
Finishing Touches: Sanding, painting, and polishing give the boat its final smooth and glossy appearance
The final stages of creating a fiberglass boat involve several meticulous steps to ensure a smooth and glossy finish. Once the boat's structure is complete, the process of refining its surface begins.
Sanding is an essential step to achieve a seamless and professional look. It involves carefully smoothing out any imperfections, such as minor bumps or uneven surfaces, using fine-grit sandpaper. This process requires patience and a gentle touch to avoid damaging the fiberglass. Start with a coarse-grit sandpaper to remove any remaining mold release or excess material, then gradually move to finer grits for a more refined finish. Pay close attention to all surfaces, including the deck, sides, and any intricate details or moldings. After sanding, wipe down the boat to remove any dust and ensure a clean surface for the next step.
Painting is a crucial aspect of the finishing process, transforming the boat's appearance and adding a layer of protection. Prepare the surface by cleaning it thoroughly and ensuring it is free from dust and debris. Prime the fiberglass to create a bond for the paint and enhance its durability. Choose a high-quality marine paint suitable for the specific conditions the boat will encounter. Apply multiple thin coats of paint, allowing sufficient drying time between each layer, to achieve a smooth and even finish. The color and finish options are vast, allowing boat owners to customize their vessel to their desired aesthetic.
Polishing takes the boat's appearance to the next level, adding a high-gloss shine and enhancing its overall appeal. After the paint has cured, use a high-quality marine polish to create a smooth, reflective surface. This process involves applying a polishing compound and buffing it into the paint using a soft cloth or polishing machine. The goal is to remove any minor imperfections and create a deep, glossy finish. Polishing also helps to protect the paint, making it more resistant to UV rays and environmental factors. Regular maintenance and polishing will keep the boat looking its best for years to come.
These finishing touches are vital to the overall quality and appearance of the fiberglass boat. They require skill, attention to detail, and a careful approach to ensure a professional-grade result. With the right techniques and materials, the boat will be transformed into a stunning vessel, ready to hit the waters with style and confidence.
Negotiating Boat Sales: Strategies for a Strong Market
You may want to see also
Frequently asked questions
The process begins with a lightweight, durable material called fiberglass, which is a composite of glass fibers and a plastic resin. These fibers are woven into a mat and then coated with the resin, creating a strong and flexible structure. Other materials such as foam core, balsa wood, and gelcoat are also used to enhance the boat's performance and aesthetics.
The hull, which is the main body of the boat, is typically constructed using a mold or a form. The fiberglass mat is laid over the mold, and the resin is carefully applied to bond the fibers together. This process is repeated layer by layer, creating a sturdy and lightweight hull. The hull is then cured, or hardened, through a process of heating and cooling to ensure its structural integrity.
Core materials like foam or balsa wood are inserted between the layers of fiberglass to provide additional strength and buoyancy. This core structure is crucial for the boat's overall rigidity and stability. It helps distribute the load evenly and reduces the weight of the boat, making it more efficient and easier to handle on the water.
After the hull is constructed, a gelcoat is applied as the top layer. Gelcoat is a clear, protective finish that provides a smooth, glossy surface. It adds color and protects the boat's structure from UV rays, chemicals, and abrasion. The gelcoat is then polished to achieve a high-quality, shiny finish, giving the boat its final aesthetic appeal.