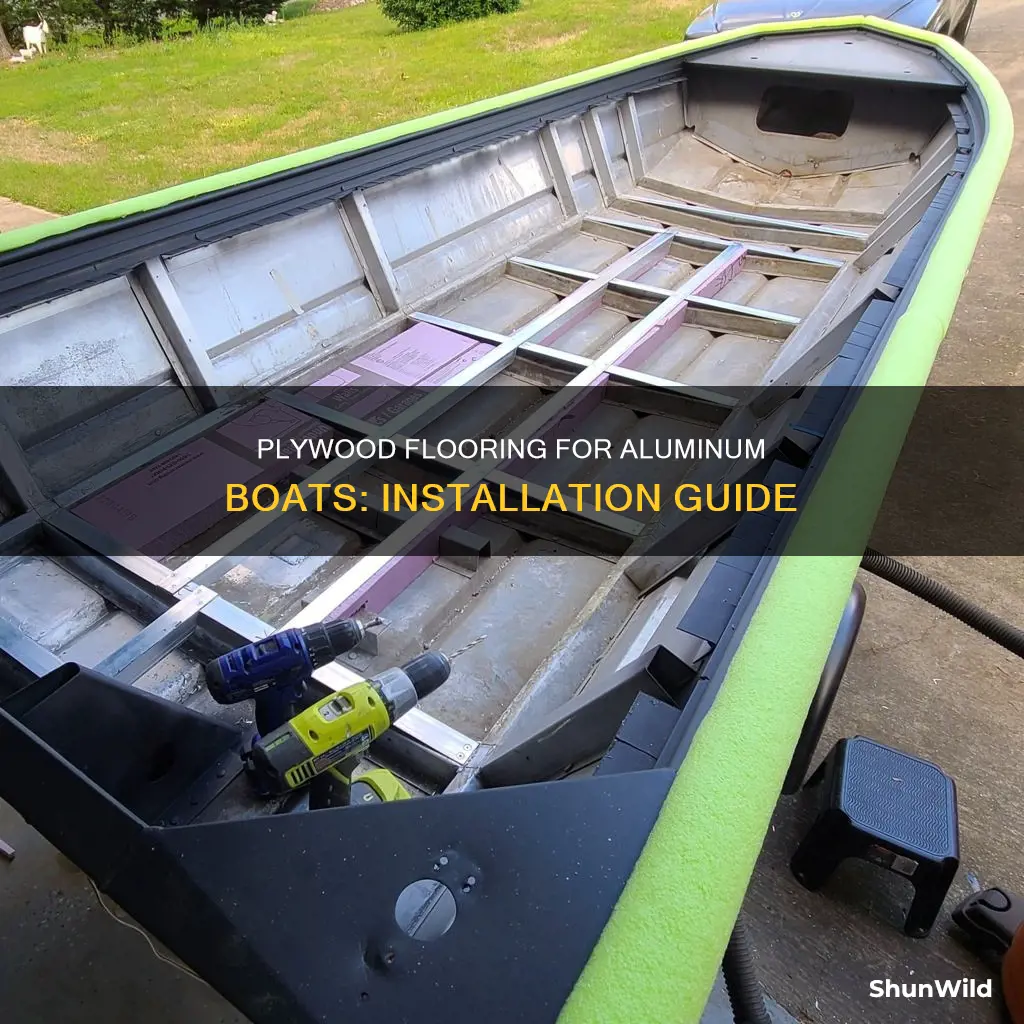
If you're looking to replace the plywood floor in your aluminium boat, there are a few things you should know. First, it's important to use the right type of plywood. Marine-grade plywood is often recommended, as it is made with better materials, has no internal voids, and uses waterproof glue. While it is more expensive than other types of plywood, it will last longer and provide a stronger, more secure floor for your boat.
Another option is to use exterior-grade plywood, which can be sealed with epoxy resin or polyurethane to help it last longer. However, exterior-grade plywood may not have the same level of water resistance as marine-grade plywood. It's also important to avoid using pressure-treated plywood, as the chemicals used in the treatment can corrode aluminium and damage your boat.
Once you've chosen the right type of plywood, you'll need to cut it to fit your boat and seal it with paint, epoxy, or another type of coating. You'll also need to decide on a floor covering, such as vinyl or carpet, and use the appropriate glue to attach it to the plywood. Finally, you'll need to install the new floor in your boat, using rivets or screws to secure it in place.
Characteristics | Values |
---|---|
Plywood type | Marine-grade plywood, exterior-grade plywood, pressure-treated plywood, MDO plywood, HDO plywood, aluminium diamond plate, Thermolite, MDO plywood, fibreglass resin, epoxy resin, poly resin, aluminium sheet |
Plywood thickness | 1/2", 3/4", 3/8" |
Plywood coating | Epoxy resin, fibreglass resin, oil-based paint, marine sealant, bedliner material, poly urethane, vinyl, carpet, indoor/outdoor glue, marine silicone, floor covering glue |
Fasteners | Solid aluminium rivets, stainless steel staples, stainless steel screws, pop rivets |
Tools | Air compressor, air hammer, staple gun, pop rivet gun, safety glasses, hearing protection, leather gloves, tape measure, circular saw, jig saw, drill, tapered punch set, rivet set tool, bucking bar, staple gun, saw horses |
What You'll Learn
Choosing the right plywood
When choosing the right plywood for an aluminium boat, there are several factors to consider, including the type of plywood, the treatment or grade of the plywood, and the intended use. Here are some detailed guidelines to help you select the most suitable plywood for your project:
Type of Plywood:
- Marine-Grade Plywood: Marine-grade plywood is specifically designed for use in water and high-moisture environments. It is crafted from robust woods, such as mahogany or tropical varieties, and is constructed using potent adhesives and advanced bonding techniques. This type of plywood is more expensive but is essential for applications that will be continuously exposed to water. It is also recommended to use marine-grade plywood for boat repairs.
- Exterior-Grade Plywood: Exterior-grade plywood is typically made from softer wood varieties like pine and fir. While it may be suitable for outdoor settings with limited moisture exposure, it is not ideal for continuous contact with water. Exterior-grade plywood is generally less expensive than marine-grade.
Treatment and Grade:
- Pressure-Treated Plywood: Pressure-treated plywood undergoes a chemical treatment to enhance its resistance against rot and pests. However, it may not be suitable for prolonged exposure to water and can emit volatile organic compounds (VOCs), including formaldehyde, which can impact air quality in enclosed spaces.
- Marine-Grade Treatment: Marine-grade plywood uses phenolic formaldehyde adhesive, which emits lower levels of VOCs, making it a safer choice for indoor boat construction.
- Grades A and B: These grades are commonly found in marine-grade plywood and indicate high-quality surfaces with minimal repairs, knots, or splits.
- Grades C and D: These grades are typically found in exterior-grade plywood and may have more significant blemishes, repairs, and knots.
Intended Use:
When selecting plywood for your aluminium boat, consider the intended use and level of moisture exposure. Marine-grade plywood is purpose-built for applications in water and high-moisture conditions, making it the best choice for boat flooring. Exterior-grade plywood, while more affordable, may not withstand continuous water exposure and is more suitable for outdoor settings with limited moisture.
How to Get a Boat Title in Minnesota
You may want to see also
Sealing the plywood
Materials:
- Marine-grade plywood: Ensure you use the same thickness as the previous floor to maintain the proper alignment between the boat seat and hull rivet holes.
- Oil-based paint: Choose a good quality paint designed for this purpose.
- Paintbrush or roller: You can use inexpensive foam brushes or rollers for this task.
- Marine silicone: This will be used to seal rivets and screws.
- Sandpaper: For light sanding between coats of paint.
Process:
- Prepare the plywood: Before sealing, ensure the plywood is cut to size and dry-fitted into your boat. Sand any rough areas and fill any voids or imperfections.
- Seal the plywood: Apply a coat of oil-based paint to all surfaces of the plywood, including the top, bottom, and edges. Allow the paint to dry completely according to the manufacturer's instructions, typically 24 hours. Lightly sand the first coat of paint before applying the second coat for better adhesion.
- Join plywood sections (if necessary): If you have multiple plywood sections, join them together using aluminium straps and rivets. Seal the joints with marine silicone for added protection.
- Allow for drying time: Ensure you allow enough time for the paint to dry completely between coats and before installing the floor. This process may take several days.
- Install the floor: Once the paint is fully cured, proceed with installing the plywood floor in your boat, following the manufacturer's instructions.
- Seal rivets and screws: During the installation process, apply a small dab of marine silicone to each rivet and screw as you secure the plywood to the boat. This will help create a watertight seal and further protect the plywood.
By following these steps and allowing adequate drying time, you will effectively seal the plywood floor of your aluminium boat, ensuring its longevity and protecting it from the elements.
Bass Boat Winner: Randy Howell's Liviston Event
You may want to see also
Removing the old floor
Before you start ripping up the old floor, it's important to take careful measurements of the floor area and the layout of the boat's interior. This will make it easier to cut the new plywood sheets to size and ensure a proper fit. Take note of the location of any floor supports, cross members, and hull rivets that will need to be worked around.
Once you have your measurements, it's time to start removing the old floor. If your boat has bench-style seats, you'll need to remove them to access the floor. Start by drilling out the rivets that secure the seats to the hull. Be sure to have a helper when removing the seats, as they can be heavy and awkward to handle.
With the seats out of the way, you should now have full access to the floor. The old plywood floor is likely held in place by aluminium pop rivets or screws. Remove all the fasteners, being careful not to damage the floor covering. If possible, leave the floor covering (carpet or vinyl) intact, as it can be reused or help in preparing the new floor.
Again, enlist the help of a friend to lift the old floor out of the boat, as it can be heavy and cumbersome. Be sure to wear leather gloves when handling the old floor to protect your hands from any loose, rusty staples or sharp edges.
Now it's time to remove the floor covering. Set the old plywood sheets on a couple of sawhorses with the bottom side facing up. Remove the staples around the perimeter of the floor and slowly work the floor covering loose using a putty knife. Depending on the type and amount of glue used, this process can vary in difficulty.
If you plan to reuse the floor covering, clean it thoroughly and remove any remaining staples or pieces of rotted plywood stuck to the covering. Flatten out any creases or folds, as this will make the reinstallation process much easier.
Finding a First Mate: A Captain's Guide to Crew
You may want to see also
Installing the new plywood
Now that you have the new plywood floor cut and dry-fit, there are a few things you'll need to do before permanently installing it. These steps will help ensure your new floor is strong, secure, and will last for many years.
Sealing the Plywood Floor
First, you'll want to seal the plywood. This is important to significantly extend the life of the plywood. If you are making any splices, seal all the surfaces before joining the pieces together. Use good-quality oil-based paint or epoxy resin for this. Apply two coats to all surfaces, top and bottom, allowing the paint to dry for a full 24 hours before applying the second coat.
Splicing Plywood Sections Together (if required)
After the paint has dried, you can join the pieces together if you have splices. Use an aluminium strap and secure it with large flange rivets to the underside of the floor. Space the rivets about 6 to 8 inches apart, ensuring the strap does not touch any of the boat's supports.
Place the plywood upside down on sawhorses and 2x4s for support. Pre-drill the aluminium strap with the rivet holes. With the strap in place, drill the rivet holes through the plywood. Apply a small dab of marine silicone to each hole in the plywood before inserting the rivet. Use washers on the aluminium strap side for added support. Wipe away any excess silicone for a smooth finish.
Installing the Floor Covering
If you are installing a new floor covering, use the old floor covering as a template to mark the new material for cutting. Place the new floor covering face-up on a smooth surface, then place the new floor on top, also face-up. Draw a line 5 to 6 inches from the perimeter of the plywood floor. This will be enough for wrapping and securing the edges.
Cut the floor covering and set the plywood floor on sawhorses, face-up. Apply the appropriate glue for your floor covering type, following the manufacturer's instructions. Lay the new floor covering, face-up, onto the glue. Wrap the excess covering around and under the edges of the plywood, stapling it to the underside. Flip the entire floor over and continue stapling around the perimeter. Use stainless steel staples for durability.
Final Installation
With the new floor ready, it's time to install it in the boat. You'll need help lifting and positioning the floor. If reusing the floor covering, the rivet holes securing the floor to the boat should align with the cross-member support marks on the hull. Make any slight adjustments before drilling holes in the new floor for the pop rivets.
Apply a small dab of marine silicone around each hole before inserting the pop rivet. Install the rivets around the perimeter of the floor and into all the floor supports. Your new floor is now firmly and securely in place!
Finding a Boat Owner: Tips and Tricks
You may want to see also
Finishing touches
Painting and Coating
Before installing the new plywood floor, it is important to seal and paint the plywood to protect it from water damage. Use a good quality oil-based paint or epoxy resin and apply two coats to all surfaces, allowing adequate drying time between coats. You can also use a clear penetrating epoxy to seal the wood, followed by a bedliner material like Durabak for the top surface to provide a non-skid finish. Remember to wear the appropriate safety gear, including gloves, eye protection, and hearing protection when working with power tools and chemicals.
Reinstalling Fixtures
Once the new floor is installed, you can start reinstalling the boat seats, storage compartments, and any other fixtures that were removed. Use stainless steel screws or solid aluminium rivets to secure the fixtures to the new floor and the boat's hull. Make sure to align the rivet holes carefully and use a tapered punch or a "Cleco" tool to ensure a snug fit before installing the rivets. If there are any loose fits between the fixtures and the hull, use a screw and nut to tighten the connection before riveting.
Final Touches
After reinstalling all the fixtures, take the time to inspect your work and make any necessary adjustments. Check that the floor is securely attached and that all rivets and screws are tight. Test the boat on the water to ensure that it handles well and that there are no leaks. Enjoy your newly refurbished boat!
Open Deck Boats: Spacious and Versatile Cruising
You may want to see also
Frequently asked questions
Marine-grade plywood is recommended for aluminium boats. Marine plywood is made out of better materials, has no internal voids, and uses waterproof glue. It is more expensive than exterior-grade plywood but will last longer.
You can seal plywood with epoxy resin, oil-based paint, or polyurethane.
Stainless steel or aluminium hardware is recommended.
Vinyl or carpet are common choices for boat flooring.