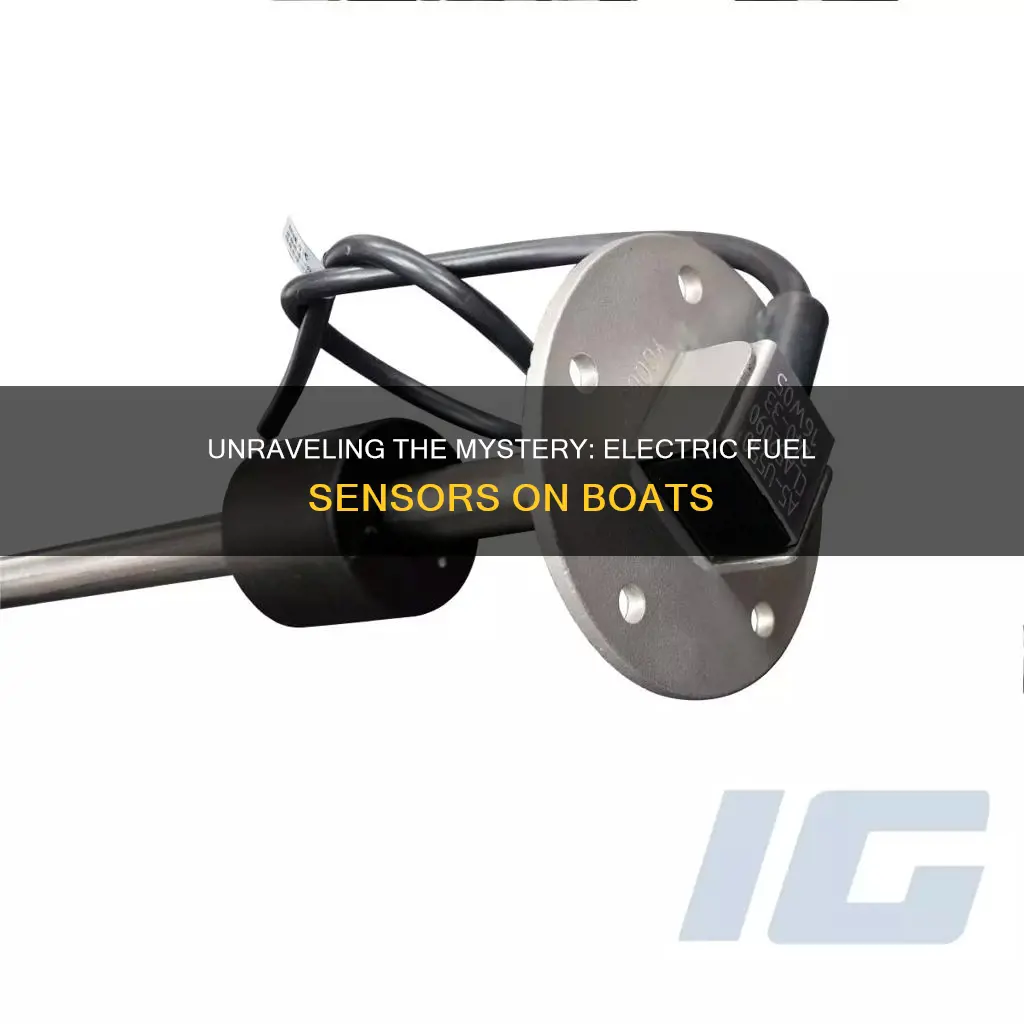
An electric fuel sensor is a crucial component in the fuel management system of boats, ensuring accurate fuel level readings and efficient operation. This sensor operates by utilizing a floating mechanism that is directly connected to the fuel tank. As the fuel level changes, the float rises or falls, which is then translated into an electrical signal. This signal is sent to the boat's dashboard or fuel management system, providing real-time data on the fuel level. The sensor's precision and reliability are essential for safe navigation and efficient fuel consumption, making it a vital part of any boat's fuel management setup.
What You'll Learn
- Design and Placement: Sensors are strategically positioned in fuel tanks to detect fuel levels accurately
- Electromagnetic Field: The sensor emits a magnetic field that interacts with the fuel, allowing for precise measurements
- Signal Processing: Advanced algorithms interpret sensor data, converting it into usable fuel level information
- Calibration: Regular calibration ensures the sensor provides accurate readings, compensating for environmental factors
- Display and Alerts: Boat systems display fuel levels and issue alerts when fuel is low, enhancing safety
Design and Placement: Sensors are strategically positioned in fuel tanks to detect fuel levels accurately
The design and placement of electric fuel sensors on boats are crucial for accurate fuel level detection, ensuring optimal performance and safety. These sensors are strategically positioned within the fuel tanks to provide real-time data on the vessel's fuel status. The primary goal is to offer precise measurements, allowing the boat's systems to function efficiently while preventing potential issues related to low fuel.
One common design approach is to use a float-based sensor. This type of sensor consists of a small, lightweight float that is attached to a wire or rod. The float is designed to move up and down as the fuel level changes, causing the wire or rod to extend or retract. This mechanical action is then converted into an electrical signal, which can be read by the boat's fuel management system. The float's position is critical, as it should be placed in a location that accurately represents the fuel level, avoiding any obstructions or fuel sloshing that could lead to inaccurate readings.
Another method involves using a pressure sensor, which measures the fuel's pressure and calculates the fuel level based on the principles of hydrostatic pressure. This type of sensor is often used in larger vessels or where space is limited. The pressure sensor is typically mounted on the side of the fuel tank, ensuring it is in contact with the fuel and providing a direct measurement of the fuel's height. This design requires careful consideration of the sensor's placement to avoid any interference with the fuel's natural movement.
In both designs, the sensors are connected to the boat's fuel management system, which processes the data and provides visual indicators or warnings to the operator. This system can display the current fuel level, alert the user when the fuel is low, and even calculate the remaining range based on the vessel's consumption. Proper placement ensures that the sensors provide accurate readings, allowing the system to function optimally.
Additionally, the sensors' design should consider factors like corrosion resistance, especially in marine environments, and the ability to withstand temperature variations. Modern fuel sensors often incorporate smart technologies, such as microcontrollers, to enhance accuracy and provide additional data, such as fuel temperature and quality. These sensors can be integrated into the boat's overall monitoring system, offering a comprehensive view of the vessel's fuel management.
The Intricate Art of Crafting Boat Sails
You may want to see also
Electromagnetic Field: The sensor emits a magnetic field that interacts with the fuel, allowing for precise measurements
An electric fuel sensor on a boat utilizes the principle of electromagnetic interaction to measure the amount of fuel present in the tank. This type of sensor is a critical component in fuel management systems, ensuring accurate fuel level monitoring and preventing potential issues related to fuel depletion or overflow. The core functionality of this sensor revolves around its ability to emit and detect electromagnetic fields, which is a key aspect of its operation.
The sensor's design involves a coil of wire, often made of a conductive material, which generates a magnetic field when an electric current passes through it. This magnetic field is a fundamental tool for fuel measurement. When the sensor is placed in the fuel tank, the magnetic field interacts with the fuel, which is typically a conductive liquid or mixture. The interaction between the magnetic field and the fuel is based on the principle of electromagnetic induction.
As the fuel moves within the tank, it becomes a part of the electromagnetic circuit. The magnetic field induces an electric current in the fuel, and this induced current is directly proportional to the fuel's conductivity and the strength of the magnetic field. By measuring this induced current, the sensor can determine the fuel's presence and quantity. The more fuel present, the stronger the induced current, providing a precise measurement of the fuel level.
This method of measurement is highly accurate and reliable. The sensor can detect even small changes in the fuel level, ensuring that the boat's operator is aware of any fuel level fluctuations. The electromagnetic field-based sensor is designed to be non-invasive, meaning it does not require direct contact with the fuel, and it operates without any mechanical moving parts, ensuring a long-lasting and maintenance-free solution.
In summary, the electric fuel sensor's electromagnetic field interaction with the fuel is a sophisticated and effective method for fuel level monitoring. This technology enables precise measurements, ensuring the boat's fuel system operates optimally and safely. Understanding this principle is essential for anyone looking to maintain or troubleshoot fuel sensors on boats or similar applications.
Launching a Small Aluminum Boat: A Step-by-Step Guide
You may want to see also
Signal Processing: Advanced algorithms interpret sensor data, converting it into usable fuel level information
The electric fuel sensor on a boat is a critical component for monitoring fuel levels, ensuring safe and efficient operation. These sensors utilize advanced signal processing techniques to provide accurate and reliable fuel level data. Here's an overview of how they work:
Sensor Technology: At its core, the electric fuel sensor employs a capacitive or inductive principle. It typically consists of a metal probe or coil that interacts with the fuel. When the sensor is immersed in fuel, the electrical properties of the fuel change, allowing the sensor to detect and measure these variations. Capacitive sensors use an electric field to measure fuel properties, while inductive sensors rely on electromagnetic induction.
Data Acquisition: As the fuel level changes, the sensor's output signal varies accordingly. This signal could be in the form of a voltage, current, or frequency change. For instance, a capacitive sensor might measure the dielectric constant of the fuel, which is directly related to its level. The sensor's output is a representation of this change, providing a raw data point.
Signal Processing: This is where the magic happens. Advanced algorithms are employed to interpret the sensor's raw data. These algorithms are designed to filter out noise, correct for environmental factors, and derive meaningful fuel level information. They analyze the sensor's output, considering factors like temperature, pressure, and fuel type to ensure accuracy. For example, an algorithm might use a look-up table or a mathematical model to correlate the sensor's reading with the actual fuel level.
Fuel Level Interpretation: The processed data is then converted into a usable format. This could be a simple fuel level percentage or a more detailed representation, such as a digital display or a signal that triggers an alarm when the fuel is low. Advanced systems might also provide additional information, like fuel consumption rates or estimated running times, based on the interpreted sensor data.
Calibration and Accuracy: Calibration is a critical aspect of signal processing. Sensors are calibrated to ensure they provide accurate readings under various conditions. This process involves adjusting the algorithms to account for any deviations in the sensor's performance, ensuring reliable fuel level monitoring. Regular maintenance and calibration are essential to maintaining the sensor's accuracy over time.
Bass Boat Driving: Easy or Tricky?
You may want to see also
Calibration: Regular calibration ensures the sensor provides accurate readings, compensating for environmental factors
Regular calibration is a critical process in maintaining the accuracy and reliability of electric fuel sensors on boats. Over time, environmental factors can impact the sensor's performance, leading to potential inaccuracies in fuel level readings. Calibration serves as a corrective measure to ensure the sensor compensates for these external influences, providing users with precise and dependable data.
The calibration process involves adjusting the sensor's settings to match the specific conditions it operates in. This is particularly important for boats, as they are exposed to various environmental variables, such as temperature fluctuations, pressure changes, and the unique characteristics of marine environments. By calibrating the sensor regularly, you can account for these factors and ensure that the fuel level readings are accurate and reliable.
During calibration, the sensor's output is compared against known standards or reference points. This comparison allows technicians or users to identify any deviations or discrepancies in the sensor's readings. Adjustments are then made to the sensor's settings, such as gain, offset, or temperature compensation, to bring the sensor's performance back into alignment with the expected accuracy. This process ensures that the sensor can accurately measure fuel levels, even in the presence of environmental challenges.
For instance, if a boat's fuel sensor is calibrated regularly, it can effectively account for temperature variations that are common in marine environments. As temperature changes can affect the density of fuel, the sensor's calibration ensures that it provides accurate fuel level readings despite these fluctuations. Similarly, calibration can address other environmental factors, such as pressure changes due to depth or the unique properties of marine fuel, ensuring the sensor's reliability in all operating conditions.
In summary, regular calibration is essential for electric fuel sensors on boats to maintain accuracy and reliability. It enables the sensor to compensate for environmental factors, providing users with precise fuel level data. By following a calibration routine, boat owners and operators can ensure that their fuel sensors deliver dependable performance, contributing to efficient fuel management and overall vessel operation.
Paul Scheer's Departure From Fresh Off the Boat
You may want to see also
Display and Alerts: Boat systems display fuel levels and issue alerts when fuel is low, enhancing safety
Modern boats rely on electric fuel sensors to monitor their fuel levels, ensuring safe and efficient operation. These sensors play a crucial role in providing accurate fuel level information to the boat's systems, which then display this data to the operator. The primary function of these sensors is to detect the amount of fuel in the tank and communicate this information to the boat's electronics.
The electric fuel sensor operates by utilizing a float or a magnetic system. When the fuel level rises, the float moves up, and this movement is detected by the sensor. This mechanical action triggers an electrical signal, which is then processed by the boat's computer system. The sensor's output is typically a voltage or current that varies with the fuel level, allowing for precise measurements. This method ensures that the fuel gauge on the boat's dashboard provides an accurate representation of the remaining fuel.
In addition to displaying fuel levels, these systems often incorporate safety features. When the fuel gauge indicates a low fuel level, the boat's computer can trigger an alert system. This alert can be in the form of a visual warning on the dashboard, an audible beep, or even a text message to the boat's owner or captain. The goal is to notify the operator well in advance, allowing them to take appropriate action, such as refueling, to prevent running out of fuel while on the water.
The integration of these sensors and display systems significantly enhances boat safety. By providing real-time fuel level data, operators can make informed decisions, ensuring they always have enough fuel for their journey. The alerts further emphasize the importance of fuel management, reducing the risk of running out of fuel in remote or hazardous locations. This technology is particularly vital for long-distance boating, where fuel conservation and monitoring are critical for a safe return to the dock.
Furthermore, the electric fuel sensor's accuracy and reliability contribute to the overall efficiency of boat operations. With precise fuel level data, boat owners can optimize their fuel usage, plan refuel stops effectively, and reduce the environmental impact by minimizing fuel consumption. This level of control and awareness is essential for both recreational and commercial boating, ensuring a more sustainable and cost-effective approach to watercraft management.
The Ultimate Smokercraft Millentia 192 Replacement: A New Boat Emerges
You may want to see also
Frequently asked questions
An electric fuel sensor is a crucial component in modern marine engines, designed to monitor and manage the fuel system. Its primary function is to accurately measure the fuel level in the tank, providing real-time data to the engine control unit (ECU). This information is vital for efficient fuel management, ensuring the boat has the right amount of fuel for optimal performance and preventing potential issues like fuel starvation or overfilling.
The sensor operates using a capacitive or ultrasonic technology. In a capacitive sensor, a small electric field is created between two conductive plates, one fixed and the other floating on the fuel surface. As the fuel level changes, the distance between the plates varies, causing a change in capacitance, which is then converted into a fuel level reading. Ultrasonic sensors, on the other hand, emit high-frequency sound waves that bounce off the fuel surface, and the time it takes for the signal to return is used to calculate the fuel level.
Electric fuel sensors offer several advantages over their mechanical counterparts. They provide more accurate and reliable fuel level readings due to their electronic nature and advanced measurement techniques. These sensors can often detect fuel level changes more quickly, ensuring the boat's engine receives the correct amount of fuel even during rapid maneuvers or sudden load changes. Additionally, electric sensors are less prone to mechanical wear and tear, resulting in longer lifespans and reduced maintenance requirements.