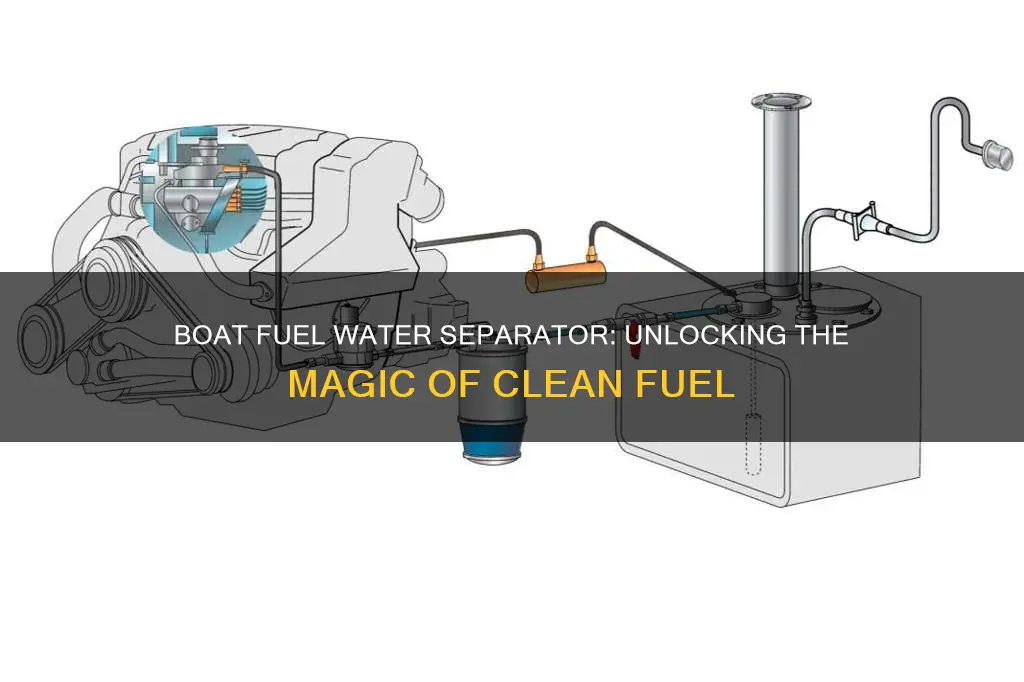
A boat fuel water separator is a crucial component in marine fuel systems, designed to remove water and contaminants from the fuel, ensuring optimal engine performance and longevity. This device operates based on the principle of gravitational separation, where the fuel and water are layered due to their different densities. The separator typically consists of a cylindrical chamber with a filter and a collection area. As the fuel enters, it flows through the filter, which traps any water droplets and sediment, preventing them from reaching the engine. The separated water then accumulates at the bottom of the chamber, which can be drained separately, while the clean fuel continues its journey to the engine, maintaining the vessel's smooth operation.
What You'll Learn
- Principle: The separator uses centrifugal force to separate water from fuel by spinning contaminants out
- Filtration: A filter element captures contaminants, preventing them from re-entering the fuel stream
- Sediment Removal: Gravity-based systems remove sediment and water droplets from the fuel
- Chemical Treatment: Some separators use chemicals to neutralize contaminants and improve separation efficiency
- Monitoring: Sensors and indicators provide real-time feedback on separator performance and fuel quality
Principle: The separator uses centrifugal force to separate water from fuel by spinning contaminants out
The principle behind a boat fuel water separator is a clever application of centrifugal force, a fundamental concept in physics. When a boat's engine operates, it generates a significant amount of fuel and water mixture, often containing contaminants like sediment, water, and other impurities. The separator's primary function is to remove these unwanted elements, ensuring that only clean fuel reaches the engine, thus improving performance and longevity.
This innovative device operates on a simple yet effective mechanism. As the boat's engine runs, the fuel water separator is integrated into the fuel system, where it acts as a filter. When the engine is in operation, the separator is spun rapidly, creating a centrifugal force. This force acts on the contaminants present in the fuel, causing them to move outward and away from the center. The spinning motion effectively separates the water and other impurities from the clean fuel.
The key to this process is the separator's design, which includes a spinning mechanism and a specialized container. As the boat's engine operates, the fuel is forced into the separator, where it encounters the spinning motion. The centrifugal force pushes the water and contaminants to the outer walls of the container, leaving the clean fuel in the center. This separation is crucial as it prevents the engine from ingesting water, which can lead to performance issues and potential damage.
Over time, the separator collects the separated contaminants, which can be drained or removed manually. This ensures that the separator remains effective and continues to provide clean fuel to the engine. Regular maintenance and cleaning of the separator are essential to guarantee its optimal performance. By utilizing centrifugal force, this technology offers a reliable and efficient way to manage fuel quality, ensuring a boat's engine operates smoothly and reliably.
In summary, the boat fuel water separator's principle is to harness the power of centrifugal force to separate water and contaminants from fuel. This process is a vital component of boat maintenance, ensuring that the engine receives only the cleanest fuel, thereby enhancing its performance and extending its lifespan. Understanding this principle highlights the ingenuity of marine engineering and the importance of proper fuel management.
How to Know It's Time to Replace Your Boat Throttle Cable
You may want to see also
Filtration: A filter element captures contaminants, preventing them from re-entering the fuel stream
A boat fuel water separator is a crucial component designed to maintain the purity of the fuel system, ensuring optimal performance and longevity. At its core, the filtration process is a critical aspect that prevents contaminants from re-entering the fuel stream, which could lead to engine damage and reduced efficiency.
The filtration system operates on a simple yet effective principle. It employs a specialized filter element, typically made of a fine mesh or porous material, such as sintered metal or a synthetic fiber. This filter element is strategically positioned within the separator, creating a barrier between the fuel and the water or contaminants. As the fuel, often containing water and other impurities, passes through this filter, the contaminants are physically trapped. The filter's intricate structure ensures that even the smallest particles, such as sediment, rust, and microbial growth, are captured, leaving behind clean, pure fuel.
The design of the filter element is crucial to its effectiveness. It must have a high surface area to maximize the contact between the fuel and the filter media, ensuring efficient contaminant removal. Additionally, the filter's porosity is carefully selected to allow fuel to pass through while retaining impurities. This precision in design ensures that the filter can handle the flow rate required for the boat's engine without compromising its ability to capture contaminants.
Once the contaminants are trapped, they are isolated from the fuel stream, preventing their re-entry. This isolation is achieved through a series of design features, such as a sealed chamber or a dedicated collection area within the separator. Over time, the trapped contaminants accumulate, and regular maintenance, including filter replacement or cleaning, is necessary to ensure the separator's continued effectiveness.
In summary, the filtration process in a boat fuel water separator is a critical defense mechanism against engine-damaging contaminants. By employing a carefully designed filter element, the separator captures and isolates impurities, ensuring that only clean fuel reaches the engine, thus promoting optimal performance and extending the life of the marine vessel's propulsion system.
The Victura: A Runabout Boat with a Storied Past
You may want to see also
Sediment Removal: Gravity-based systems remove sediment and water droplets from the fuel
Sediment removal is a critical aspect of maintaining a boat's fuel system, ensuring optimal performance and longevity. Gravity-based systems are an effective method to achieve this, offering a simple yet powerful solution. These systems operate on the principle of utilizing the natural force of gravity to separate sediment and water droplets from the fuel.
The process begins with the fuel entering the separator, which is typically a cylindrical or rectangular container with a specific design. Inside this container, a series of baffles or plates are strategically arranged to create a path that encourages sediment settling. As the fuel flows through this path, the heavier particles, such as sediment and water droplets, start to descend due to gravity. This settling process is crucial as it allows the cleaner fuel to remain at the top, ready for use.
The design of the separator plays a vital role in its efficiency. The baffles or plates are angled to promote the movement of fuel and sediment in a circular motion. This motion ensures that the sediment accumulates at the lowest point of the separator, forming a layer that can be easily removed. The fuel, now separated from the sediment, continues its journey through the system, ready to power the boat's engine.
Regular maintenance is essential to keep these gravity-based systems effective. Over time, the accumulated sediment can build up, reducing the separator's capacity and potentially leading to engine issues. Therefore, it is recommended to inspect and clean the separator periodically. This involves removing the sediment layer and ensuring that the system is free from any blockages, allowing for optimal fuel flow.
In summary, gravity-based sediment removal systems provide a reliable and straightforward approach to maintaining a boat's fuel quality. By leveraging the natural force of gravity, these systems effectively separate sediment and water, ensuring that only clean fuel reaches the engine. Regular maintenance further enhances the system's performance, contributing to the overall reliability and efficiency of the boat's power source.
Venture Boat Trailers: Worth the Investment?
You may want to see also
Chemical Treatment: Some separators use chemicals to neutralize contaminants and improve separation efficiency
Chemical treatment is an essential component of fuel water separators, especially in marine environments where fuel and water contamination is a significant concern. These separators employ a range of chemical processes to ensure that the fuel remains clean and free from harmful substances, thus maintaining the performance and longevity of the engine. The primary goal of chemical treatment is to neutralize and remove contaminants that could otherwise cause engine damage or performance issues.
One common chemical process used in these separators is the addition of dispersants. Dispersants are substances that break down large, insoluble particles into smaller, more manageable droplets. When fuel and water are mixed, large particles of contaminants like rust, sediment, and organic matter can form. Dispersants work by surrounding these particles, preventing them from aggregating and settling at the bottom of the separator. This ensures that the fuel remains clean and clear, ready for use.
Another critical chemical process is the use of inhibitors. Inhibitors are compounds that prevent or slow down chemical reactions, particularly those that can lead to corrosion and degradation of the fuel. For example, fuel can contain water, which can lead to the formation of acidic compounds that corrode engine components. Inhibitors neutralize these acidic substances, protecting the fuel and the engine from corrosion. They also help to maintain the fuel's stability and prevent the growth of microorganisms, ensuring that the fuel remains in optimal condition.
In some cases, separators may also use chelating agents, which are chemicals that bind to metal ions and form stable, soluble complexes. This process helps to remove heavy metals and other metallic contaminants from the fuel. By effectively capturing and neutralizing these harmful substances, chelating agents contribute to the overall cleanliness and safety of the fuel system.
The use of chemicals in fuel water separators is a precise and controlled process. The specific chemicals and their concentrations are carefully selected to ensure they do not harm the fuel or the environment. Regular maintenance and monitoring of the chemical treatment system are essential to guarantee its effectiveness. This includes testing the fuel's quality, checking the chemical levels, and replacing or replenishing the chemicals as needed to maintain optimal performance.
The Open Boat: Shark as a Symbol of Nature's Indifference
You may want to see also
Monitoring: Sensors and indicators provide real-time feedback on separator performance and fuel quality
Monitoring the performance of a boat fuel water separator is crucial for ensuring optimal operation and maintaining fuel quality. This is achieved through the use of sensors and indicators that provide real-time feedback on various parameters. Here's how these components contribute to effective monitoring:
Sensors play a vital role in gathering data from different parts of the separator. They are strategically placed to measure critical parameters such as fuel flow rate, water content, and sediment levels. For instance, fuel flow sensors detect the rate at which fuel passes through the separator, ensuring that the separation process is efficient. Water content sensors measure the amount of water present in the fuel, allowing for the identification of potential contamination issues. Sediment sensors, often in the form of filters or sensors, monitor the accumulation of particles and debris, which can affect the separator's performance and fuel quality.
Real-time feedback is essential for prompt issue identification. Sensors continuously monitor the fuel and water streams, providing instant data on their conditions. If the water content sensor detects an unusually high level of water, it triggers an alert, indicating a potential problem with the separator's separation efficiency. Similarly, sediment sensors can detect blockages or excessive buildup, prompting maintenance actions to prevent performance degradation.
Indicators are visual or audible signals that convey the status of the separator and fuel quality. These can include warning lights, gauges, or alarms. For example, a warning light might indicate when the separator is overloaded or when maintenance is required. Gauges can display the current water content or fuel flow rate, allowing operators to make informed decisions. Audible alarms can notify the crew of critical issues, ensuring a swift response to potential problems.
The integration of sensors and indicators allows for a comprehensive monitoring system. By analyzing the data from these components, operators can make real-time adjustments to optimize the separator's performance. This might involve changing filtration settings, adjusting flow rates, or implementing maintenance procedures to ensure the separator operates efficiently and effectively. Regular monitoring also helps in identifying trends and patterns, enabling proactive measures to prevent fuel contamination and maintain the overall health of the boat's fuel system.
In summary, sensors and indicators are indispensable tools for monitoring the performance of a boat fuel water separator. They provide critical data, enable prompt issue identification, and facilitate real-time adjustments to maintain fuel quality and separator efficiency. By relying on these monitoring systems, boat operators can ensure a reliable and safe fuel supply during their journeys.
Mastering Boat Sailing with Fluctuating Currents: Miles Traveled
You may want to see also
Frequently asked questions
A boat fuel water separator is a device designed to remove water and contaminants from the fuel system of a boat's engine. It is an essential component for maintaining the performance and longevity of marine engines, especially in areas with poor fuel quality or high water content.
The separator operates based on the principle of phase separation. It typically consists of a container with a built-in filter and a separator element. When fuel is drawn from the tank, it passes through the filter, which captures larger contaminants like dirt and debris. The separator element then uses centrifugal force to separate water droplets from the fuel, allowing clean fuel to continue its journey to the engine while the water and contaminants are collected at the bottom of the container.
Marine environments often expose fuel systems to water, which can lead to engine damage over time. Water in fuel can cause corrosion, reduce engine performance, and even lead to costly repairs. A fuel water separator prevents these issues by ensuring that only clean, dry fuel reaches the engine, thus improving overall engine efficiency and reliability.
Yes, fuel water separators are versatile and can be used for both gasoline and diesel engines. They are particularly beneficial for diesel engines, as diesel fuel is more susceptible to water contamination. However, it's important to choose a separator designed for the specific type of fuel and engine system to ensure optimal performance and compatibility.