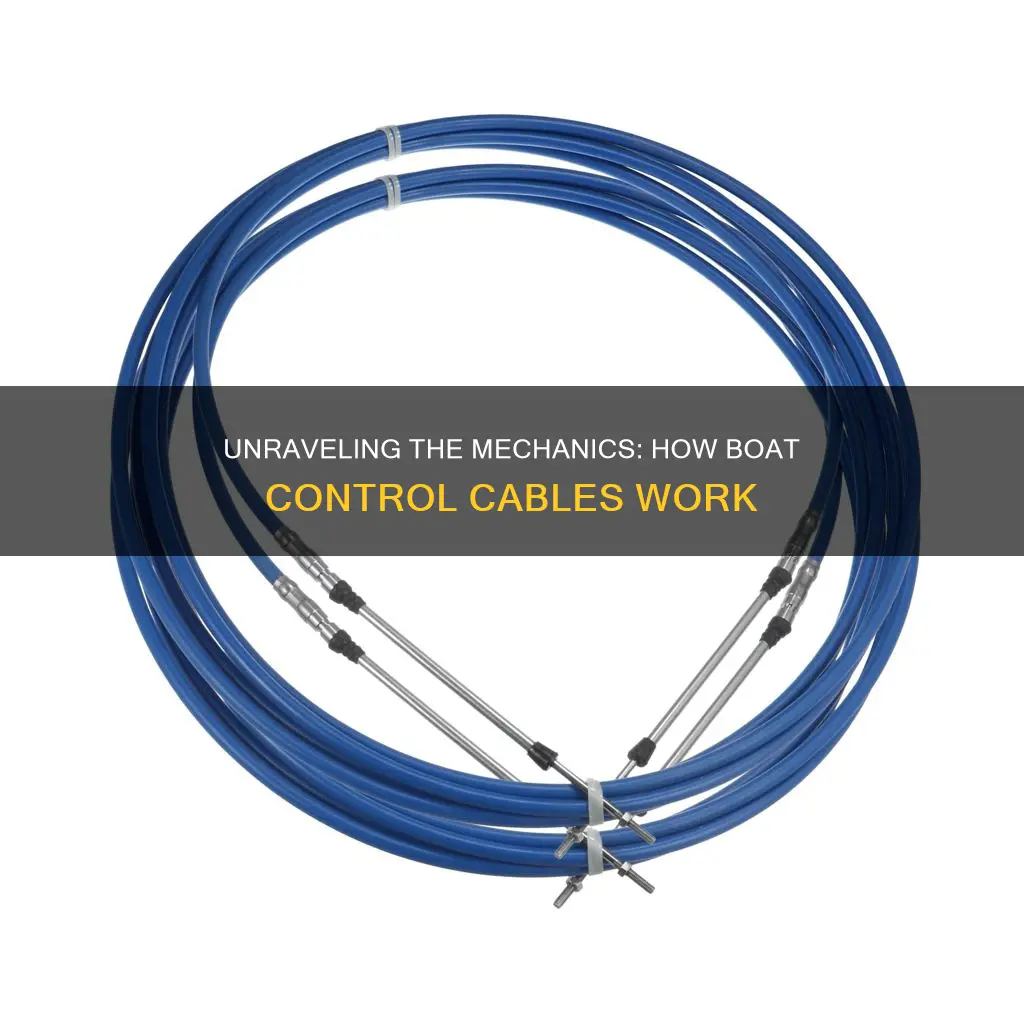
A boat control cable is an essential component in the operation of various watercraft, enabling precise control and maneuverability. This system utilizes a series of pulleys, sheaves, and cables to transmit the operator's commands from the helm to the vessel's steering mechanism. By engaging the control cable, the operator can initiate steering movements, adjusting the boat's direction and course. Understanding the mechanics of this cable system is crucial for boat owners and operators to ensure safe and efficient navigation, allowing for smooth and responsive control of the vessel.
What You'll Learn
- Construction: The cable is made of a core, insulation, and protective layers
- Material: Materials like steel, aluminum, or synthetic fibers are used for strength
- Sheathing: Protects the cable from abrasion, moisture, and environmental damage
- Sheave Design: The sheave's diameter and groove shape affect cable movement and load capacity
- Tensile Strength: The cable's ability to withstand pulling forces without breaking is crucial
Construction: The cable is made of a core, insulation, and protective layers
The construction of a boat control cable is a critical aspect of its functionality, ensuring reliable and safe operation. At its core, the cable is designed with a robust and durable material, typically a metal alloy, which provides the necessary strength and flexibility. This core is the central element that transmits the force required to operate the boat's controls, such as the steering wheel or throttle.
Insulation plays a vital role in the cable's construction. It is placed around the core to prevent electrical conductivity and ensure the cable's integrity. This insulation is made from materials like rubber or plastic, chosen for their ability to withstand the harsh marine environment, including exposure to water, salt, and varying temperatures. The insulation also helps to protect the core from damage and ensures that the cable can withstand the mechanical stresses it will endure during operation.
Protective layers are then added to safeguard the cable from external elements and potential hazards. These layers can include a protective jacket made of materials like PVC or a braided cover, which provides an additional barrier against abrasion, impact, and UV radiation. The protective layers also contribute to the cable's overall flexibility, allowing it to bend and move without compromising its structural integrity.
In some cases, boat control cables may also incorporate specialized components. For instance, they might feature a built-in strain relief mechanism to absorb tension and prevent damage to the core. Additionally, some cables are designed with a braided construction, where multiple strands of the core material are intertwined, offering enhanced flexibility and reducing the risk of core damage.
The construction of these cables is a precise process, requiring careful selection of materials and manufacturing techniques to ensure they meet the demanding requirements of marine environments. By utilizing a core, insulation, and protective layers, these cables are designed to provide reliable control systems for boats, ensuring safe and efficient operation.
Painting Boat Propellers: The Manufacturing Process Explained
You may want to see also
Material: Materials like steel, aluminum, or synthetic fibers are used for strength
The strength and durability of a boat control cable are heavily dependent on the materials used in its construction. These cables are designed to withstand the rigorous demands of marine environments, providing precise control and communication between the boat's helm and various systems. Here's a detailed look at the materials commonly employed:
Steel: One of the most traditional and robust materials for control cables is steel. It offers exceptional strength and corrosion resistance, making it ideal for heavy-duty applications. Steel cables are known for their ability to handle high tension and are often used in larger boats or those exposed to saltwater conditions. The material's inherent strength ensures that the cable can transmit force effectively, allowing for smooth and responsive control of the vessel.
Aluminum: In contrast to steel, aluminum provides a lighter-weight alternative without compromising on strength. This material is particularly useful for smaller boats or applications where weight reduction is crucial. Aluminum cables offer excellent corrosion resistance, ensuring they remain reliable over extended periods. Despite being lighter, aluminum cables can still transmit force efficiently, making them a popular choice for recreational boats and smaller vessels.
Synthetic Fibers: Modern advancements in materials science have led to the development of synthetic fibers, which are now widely used in control cables. These fibers, often made from materials like polyester or Kevlar, offer a unique combination of strength, flexibility, and lightweight properties. Synthetic cables are highly resistant to abrasion and can withstand the harsh marine environment. Their flexibility allows for easier installation and routing, while their strength ensures that the cable can handle the required load without compromising performance.
The choice of material depends on various factors, including the boat's size, intended use, and environmental conditions. For instance, steel cables are often preferred for commercial fishing vessels due to their strength and longevity. In contrast, aluminum and synthetic fiber cables might be more suitable for leisure boats or those requiring lightweight solutions. Each material brings its own set of advantages, ensuring that boat control cables can meet the diverse needs of different marine applications.
Applying Boat Registration Numbers: Achieving Even Spacing
You may want to see also
Sheathing: Protects the cable from abrasion, moisture, and environmental damage
Sheathing is a critical component of boat control cables, providing essential protection against various environmental factors. This protective layer is typically made from materials like PVC, rubber, or synthetic compounds, carefully chosen for their durability and resistance to wear and tear. The primary purpose of sheathing is to safeguard the inner cable structure, ensuring its longevity and reliability in harsh marine environments.
In the context of boat control cables, abrasion is a significant concern, especially when the cable is exposed to the constant movement and friction of the vessel's operation. Sheathing acts as a robust barrier, preventing the inner cable from being worn down by rubbing against other surfaces, such as the boat's hull, anchor lines, or even the cable's own bends and turns. This protection is vital to maintain the cable's integrity and ensure it can withstand the physical demands of its function.
Moisture is another critical factor that sheathing effectively combats. Boat control cables are often exposed to saltwater, which can be highly corrosive and detrimental to the cable's internal components. The sheathing material is designed to be waterproof, creating a barrier that keeps moisture and saltwater from penetrating the cable. This protection is essential to prevent corrosion, which could lead to cable failure and potential hazards on the boat.
Environmental damage is a broad term encompassing various external threats. Sheathing provides a shield against these dangers, including UV radiation from the sun, which can degrade materials over time, and extreme temperatures that could cause the cable to become brittle or flexible. By offering this comprehensive protection, sheathing ensures that the cable remains functional and safe to use, even in the most challenging marine conditions.
In summary, sheathing is a vital feature of boat control cables, serving as a protective layer that safeguards against abrasion, moisture, and environmental damage. Its presence ensures the cable's longevity, reliability, and overall performance, making it an indispensable component in the operation of boats and marine vessels. Understanding the role of sheathing highlights the intricate design considerations that go into creating effective and safe boat control systems.
Did Jennifer Connelly Sail in Top Gun?
You may want to see also
Sheave Design: The sheave's diameter and groove shape affect cable movement and load capacity
The design of sheaves, which are pulleys used in cable-driven systems, plays a crucial role in determining the efficiency and performance of a boat's control cable mechanism. Sheaves come in various sizes and shapes, each tailored to specific applications and load requirements. One of the primary factors influencing cable movement and load capacity is the sheave's diameter. A larger sheave diameter provides a greater radius, which results in a longer path for the cable to follow around the sheave. This increased radius reduces the cable's tendency to slip or jam, especially under heavy loads. When the cable wraps around a sheave with a larger diameter, it experiences less friction, allowing for smoother and more controlled movement. This is particularly important in boat control systems, where precise adjustments are required for steering and maneuvering.
The groove shape of the sheave is another critical design consideration. Sheave grooves are typically V-shaped, with the depth and angle of the V influencing the cable's grip and movement. A deeper V-shape provides a stronger grip on the cable, preventing it from slipping or coming off the sheave, even under high tension. This is essential for maintaining control and stability in boat applications, where sudden movements and varying loads are common. Additionally, the groove's angle affects the cable's angle of wrap, which in turn impacts the sheave's load-carrying capacity. A steeper V-angle allows the cable to wrap more tightly around the sheave, increasing the sheave's ability to handle heavy loads without excessive cable wear.
Sheave diameter and groove design are interrelated, as they collectively influence the cable's path and the sheave's load-carrying capability. A larger sheave diameter often requires a deeper and steeper groove to ensure optimal cable grip and movement. This combination ensures that the cable remains securely on the sheave, even when subjected to significant forces. For instance, in a boat's steering system, a larger sheave diameter might be paired with a modified groove shape to accommodate the increased load and provide precise control during turns.
In summary, sheave design is a critical aspect of boat control cable systems. The diameter and groove shape of sheaves directly impact cable movement and load capacity. Larger sheave diameters reduce slipping and improve efficiency, while V-shaped grooves with appropriate depth and angle ensure a secure grip on the cable. Understanding these design considerations allows engineers and boat owners to select the right sheave sizes and configurations, ensuring optimal performance and safety in various marine applications.
The Ultimate Range of Your Boat
You may want to see also
Tensile Strength: The cable's ability to withstand pulling forces without breaking is crucial
Tensile strength is a critical property of boat control cables, ensuring their functionality and safety in various marine applications. This attribute refers to the maximum stress a cable can endure before it fails, typically measured in pounds per square inch (psi) or newtons per square millimeter (N/mm²). The higher the tensile strength, the more robust and durable the cable is, capable of withstanding the forces exerted during operation without compromising its structural integrity.
In the context of boat control systems, cables play a vital role in transmitting power and signals between the vessel and various control mechanisms, such as winches, rudders, and steering wheels. These cables must be designed to handle the dynamic and often harsh conditions of marine environments, including exposure to saltwater, varying temperatures, and mechanical stresses. The tensile strength of the cable directly influences its ability to resist breaking, ensuring that it can endure the pulling forces generated during normal operation and emergency maneuvers.
For instance, in a typical boat control setup, the cable connects the steering wheel or tiller to the steering gear or rudder. During steering maneuvers, the cable is subjected to pulling forces as it transmits the operator's input to the steering mechanism. If the cable's tensile strength is insufficient, it may stretch, deform, or even snap, leading to loss of control or, in extreme cases, causing the vessel to veer off course or capsize. Therefore, selecting cables with appropriate tensile strength is essential to guarantee reliable and safe operation.
Manufacturers achieve high tensile strength through various means, including the use of high-quality materials, advanced braiding techniques, and specialized coatings. For example, stainless steel cables are renowned for their exceptional tensile strength and corrosion resistance, making them ideal for marine applications. Additionally, the cable's cross-sectional area and diameter also play a role in determining its strength, with thicker cables generally offering higher tensile strength.
In summary, tensile strength is a fundamental aspect of boat control cables, ensuring their reliability and safety in demanding marine environments. By understanding and selecting cables with adequate tensile strength, boat owners and operators can ensure smooth and secure control of their vessels, even in challenging conditions.
Xpress X-60: A Boat Worth Buying?
You may want to see also
Frequently asked questions
A boat control cable, also known as a steering cable, is a crucial component in the steering system of boats, especially in larger vessels like ships and yachts. It is a metal or synthetic cable that transmits the force from the steering wheel or tiller to the steering gear or rudder, allowing the operator to control the direction of the boat. The cable is typically made of high-strength materials to ensure it can withstand the forces exerted during steering maneuvers.
The cable works by transferring the rotational motion of the steering wheel or tiller to the steering gear. When the operator turns the wheel or moves the tiller, the cable pulls or pushes on the steering gear, which is connected to the rudder or steering mechanism. This mechanical connection enables the boat to change direction, making it possible for the operator to navigate the vessel.
Yes, there are various types of control cables employed in different boat designs. One common type is the wire rope cable, which is strong and flexible, making it suitable for heavy-duty applications. Another type is the synthetic cable, often made from materials like braided polyester or Kevlar, offering lightweight and corrosion-resistant properties. The choice of cable material depends on factors such as boat size, intended use, and environmental conditions.
Regular maintenance and inspection are essential to ensure the cable's reliability and safety. It is recommended to check the cable for any signs of wear, damage, or corrosion regularly. Look for frayed or damaged sections, rusting, or excessive play in the cable. Proper lubrication at the cable's fittings can help reduce friction and wear. Additionally, keeping the cable clean and free from debris is crucial. If any issues are found, it is best to consult a marine mechanic or specialist to repair or replace the cable to maintain optimal steering performance.