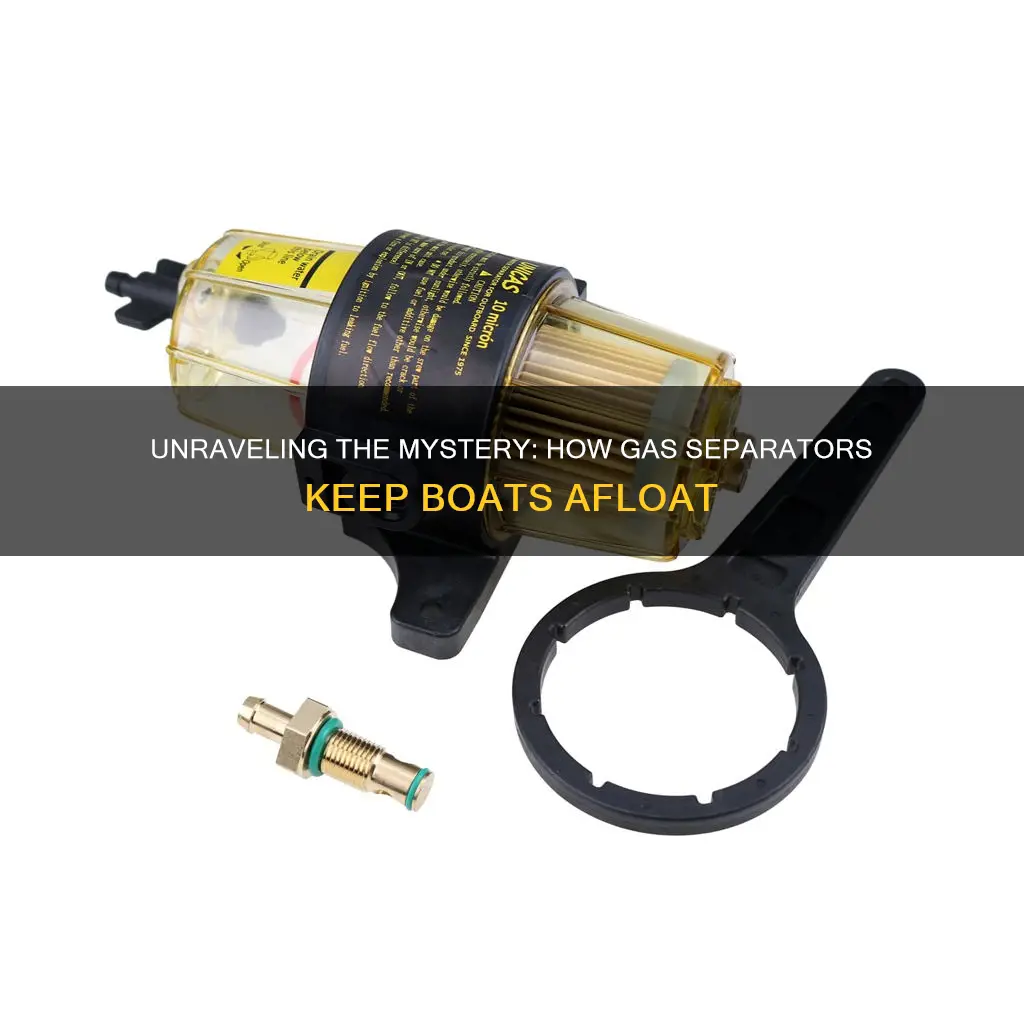
Boat gas separators are essential components in marine engines, designed to improve fuel efficiency and reduce emissions. These devices work by separating the liquid fuel from the vapor phase in the fuel tank, ensuring a cleaner and more efficient combustion process. The separator utilizes a series of filters and chambers to capture and condense the vapor, allowing only the liquid fuel to pass through and be delivered to the engine. This process not only enhances engine performance but also contributes to a more environmentally friendly operation by minimizing the release of harmful pollutants. Understanding the inner workings of these separators is crucial for boat owners and operators to maintain their vessels and optimize their fuel systems.
What You'll Learn
- Principle: Gas separators use centrifugal force to separate water and gas in boat engines
- Design: They feature a cylindrical bowl with a spinning impeller
- Operation: The impeller spins, creating a vortex that separates gas and water
- Maintenance: Regular cleaning and replacement of filters are essential for optimal performance
- Advantages: Gas separators improve engine efficiency and reduce emissions
Principle: Gas separators use centrifugal force to separate water and gas in boat engines
Boat gas separators, also known as water separators, are essential components in marine engine systems, designed to manage the unique challenges posed by water and gas mixtures in marine environments. The principle behind these separators is the utilization of centrifugal force to effectively separate water and gas, ensuring optimal engine performance and longevity.
When a boat engine operates, it generates a mixture of air, fuel, and water vapor. This mixture enters the gas separator, where the magic of separation begins. The separator's design incorporates a spinning mechanism, often driven by the engine's own power or an auxiliary motor. As the engine runs, the mixture is directed into the separator, and here's where centrifugal force comes into play. The spinning motion creates a powerful centrifugal force, which acts on the water droplets and gas particles.
Water, being denser than gas, tends to move outward and away from the center of the separator due to the centrifugal force. This movement causes the water droplets to separate from the gas mixture. The separated water then accumulates in a designated collection chamber, often with a drain valve for easy removal. Meanwhile, the gas, which is less dense, remains in the center and continues its journey through the separator.
The gas separator's design ensures that the separated gas is directed back into the engine's intake system, where it can be properly mixed with fuel and ignited. This process ensures that the engine receives a clean and dry fuel-air mixture, free from water contamination. By removing water, the separator prevents potential engine damage caused by water-induced corrosion and the formation of explosive mixtures.
In summary, the principle of gas separators in boat engines relies on the application of centrifugal force to separate water and gas. This innovative design allows for efficient water removal, ensuring a reliable and robust engine system, even in the challenging marine environment. Understanding and implementing this principle is crucial for maintaining the performance and longevity of boat engines.
Sailing the Oceans: A Beginner's Guide to Boat Voyage
You may want to see also
Design: They feature a cylindrical bowl with a spinning impeller
Boat gas separators, also known as fuel filters or separators, are essential components in marine fuel systems, designed to remove contaminants and improve the quality of the fuel. The design of these separators is crucial to their functionality, and one of the most common and effective designs is the cylindrical bowl with a spinning impeller.
The cylindrical bowl is a key element in this design. It is typically made of durable materials such as aluminum or stainless steel, ensuring it can withstand the harsh marine environment. This bowl is designed to be mounted in the fuel line, often between the fuel tank and the engine. When fuel flows through the separator, it enters the bowl, where the magic happens.
Inside the bowl, a spinning impeller is strategically positioned. This impeller is an essential component that utilizes centrifugal force to separate contaminants from the fuel. As the fuel enters the bowl, it is directed towards the impeller by the bowl's design, which often includes a series of baffles or vanes to guide the flow. The impeller's rotation creates a spinning motion in the fuel, causing contaminants to move outward due to centrifugal force.
The spinning impeller is designed with a series of blades or vanes that extend radially from its center. As the impeller rotates, these blades create a vortex, pulling contaminants such as water, sediment, and debris away from the clean fuel. The clean fuel, now separated from impurities, is directed back into the fuel line, ready to be delivered to the engine.
This design is highly effective because it takes advantage of the natural principles of centrifugation. By spinning the fuel, the impeller effectively separates the contaminants, which tend to remain in the outer layer of the vortex, from the clean fuel, which remains in the inner layer. This process ensures that the fuel supplied to the engine is of high quality, reducing the risk of engine damage caused by contaminated fuel.
Ischia to Capri: A Quick Boat Trip
You may want to see also
Operation: The impeller spins, creating a vortex that separates gas and water
The operation of a boat gas separator, also known as a separator or a fuel filter, is a crucial component in the fuel system of a vessel. When the impeller spins, it initiates a process that effectively separates gas and water, ensuring cleaner fuel for the engine. Here's a detailed explanation of this process:
As the impeller rotates, it creates a powerful vortex within the separator's chamber. This vortex is a swirling motion that plays a vital role in the separation process. The impeller's design, often with a series of blades or vanes, is engineered to optimize this vortex. When fuel, which typically contains a mixture of gasoline, water, and contaminants, enters the separator, it is directed towards the impeller. The spinning motion of the impeller causes the fuel to accelerate and enter the vortex.
Within the vortex, the gas and water separation occurs. The high-speed vortex creates a centrifugal force that pushes the heavier water droplets and contaminants outward, away from the center of the vortex. This centrifugal force is a result of the impeller's rotation, which generates a strong radial acceleration. As a consequence, the water droplets, being denser than the gas, are forced to the walls of the separator, where they can be collected and drained.
The gas, being less dense, remains in the center of the vortex and is drawn upwards. This upward movement is facilitated by the impeller's design, which creates a path for the gas to rise. As the gas rises, it can be directed into the engine's fuel system, ensuring that only the desired gas component is supplied to the engine. This process effectively removes water and contaminants, improving the fuel's quality.
This operation is a critical aspect of maintaining a boat's engine performance and longevity. By separating gas and water, the separator prevents potential issues caused by water and contaminants, such as engine damage, reduced performance, and increased maintenance requirements. The spinning impeller is the key to this efficient separation process, making it an essential component in the overall functionality of a boat's fuel system.
Istanbul to Greece: A Boat Trip Adventure
You may want to see also
Maintenance: Regular cleaning and replacement of filters are essential for optimal performance
Maintaining your boat gas separator is crucial to ensure its effectiveness and longevity. One of the most critical aspects of this maintenance is regular cleaning and filter replacement. Over time, the separator's filters accumulate contaminants, including water, sediment, and debris, which can hinder its performance. Neglecting this maintenance can lead to reduced efficiency, engine issues, and potential safety hazards.
The primary function of a gas separator is to remove impurities from the fuel, ensuring a clean and dry supply reaches the engine. When the separator's filters become clogged, they can no longer effectively separate water and contaminants from the fuel. This results in a compromised fuel supply, leading to potential engine problems such as misfires, reduced power, and even damage to critical engine components.
Regular cleaning is a straightforward process. It involves removing the separator's filters and using a suitable cleaning agent to wash away accumulated contaminants. This should be done periodically, depending on usage and environmental factors. For instance, if your boat operates in dirty or dusty conditions, more frequent cleaning may be necessary. After cleaning, ensure the filters are thoroughly dried before reinstalling them.
Filter replacement is another critical maintenance task. Over time, even with regular cleaning, filters can become permanently damaged or saturated with contaminants. When this happens, they must be replaced. Check the manufacturer's guidelines for recommended filter replacement intervals, as these can vary depending on the model and usage. Replacing filters at the right time ensures that the gas separator continues to function optimally, providing clean fuel to your boat's engine.
In summary, regular cleaning and filter replacement are vital maintenance tasks for boat gas separators. By keeping the separator clean and replacing filters as needed, you can maintain a reliable and efficient fuel supply to your boat's engine, ensuring smooth and safe operation during your aquatic adventures. Remember, proper maintenance not only extends the life of your equipment but also contributes to a safer and more enjoyable boating experience.
Attaching Dock Wheels to a Boat Lift: Easy Steps
You may want to see also
Advantages: Gas separators improve engine efficiency and reduce emissions
Gas separators, also known as fuel gas separators or fuel filters, are essential components in boat engines, offering a range of advantages that contribute to improved performance and environmental sustainability. One of the primary benefits is the enhancement of engine efficiency. These separators play a crucial role in ensuring that the fuel supplied to the engine is clean and free from contaminants. By removing water, dirt, and other impurities, gas separators prevent the formation of harmful fuel-water emulsions, which can lead to engine misfires and reduced power output. This results in a more efficient combustion process, allowing the engine to operate at its peak performance.
In addition to efficiency gains, gas separators significantly contribute to reducing emissions. Boat engines, particularly older models, can produce substantial amounts of pollutants, including carbon monoxide, hydrocarbons, and sulfur oxides. The separators' ability to filter out contaminants means that the fuel entering the engine is cleaner, leading to a more complete combustion process. This, in turn, minimizes the release of harmful gases into the atmosphere, making boat operations more environmentally friendly.
The design of gas separators often includes a sediment bowl or a filter element that captures contaminants. Over time, these separators may become clogged with accumulated dirt and debris, requiring regular maintenance or replacement. However, this maintenance is crucial to ensure the separators' effectiveness. By keeping the fuel system clean, gas separators help extend the lifespan of the engine, as they prevent the buildup of corrosive substances that can damage internal engine components.
Furthermore, the use of gas separators can lead to cost savings in the long run. By improving engine efficiency, these devices can help reduce fuel consumption, resulting in lower fuel costs for boat owners. Additionally, the reduction in emissions may lead to compliance with environmental regulations, potentially avoiding fines and penalties for non-compliance.
In summary, gas separators are vital components in boat engines, offering a multitude of advantages. They improve engine efficiency by ensuring clean fuel delivery, leading to better performance and longer engine life. Simultaneously, they contribute to environmental sustainability by reducing emissions and minimizing the release of pollutants. Regular maintenance and replacement of these separators are essential to ensure their effectiveness and maximize the benefits they provide to boat operators.
Stern Drive Boat: Locating the Shift Cable
You may want to see also