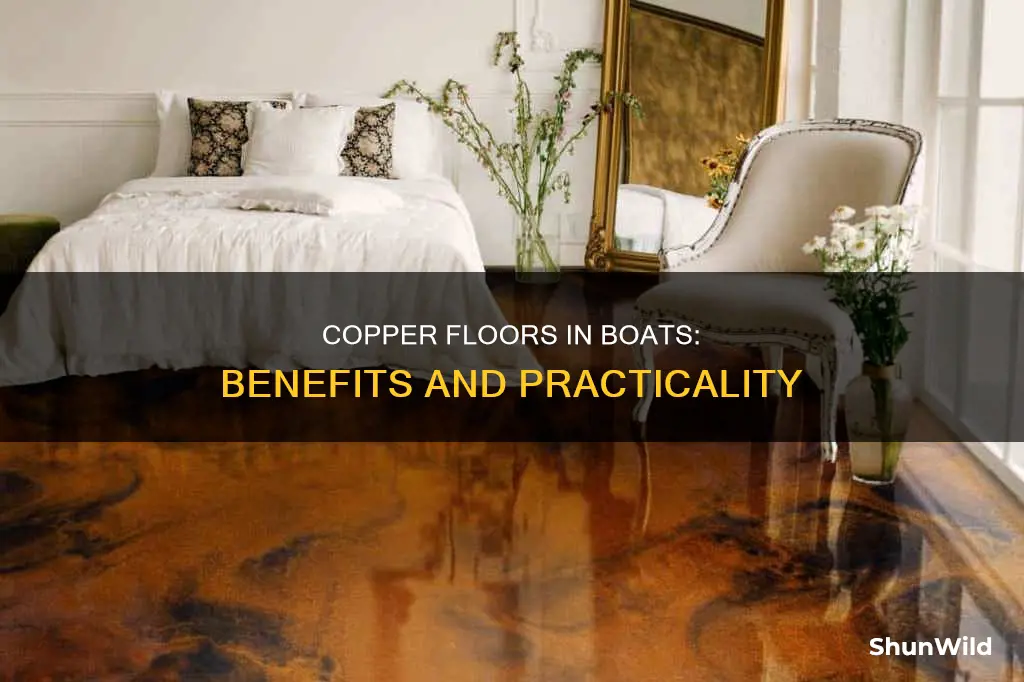
Copper floors, or sheathing, in boats is a method of protecting the hull of a wooden vessel from deterioration caused by shipworm, barnacles, and other marine growth. Copper was found to be more effective than traditional wood and lead sheathing methods, which slowed ships down and reacted badly with iron bolts, respectively. The use of copper sheathing was pioneered by the Royal Navy in the 18th century, and its implementation was accelerated due to the American war. Copper floors create a poisonous film when in contact with water, which prevents marine growth and keeps the hull clean, thus increasing the speed and longevity of the ship.
What You'll Learn
- Copper floors protect the hull from shipworm, barnacles and other marine growth
- Copper floors can be glued to the boat's hull as an alternative to antifoul
- Copper floors are an expensive solution but can last a decade or more
- Copper floors are hassle-free, environmentally friendly and easy to maintain
- Copper floors can be made by stirring a high concentration of copper powder into an epoxy matrix
Copper floors protect the hull from shipworm, barnacles and other marine growth
Copper floors, or copper sheathing, are used to protect the hull of a wooden vessel from shipworm, barnacles and other marine growth. The copper is affixed to the surface of the hull, below the waterline. This method was pioneered and developed by the Royal Navy during the 18th century, although the use of copper to protect ships dates back even further, with the ancient Chinese using copper plates and the ancient Greeks using lead plates.
Copper sheathing works by producing a poisonous film, composed mainly of copper oxychloride, when it comes into contact with water. This film deters marine organisms from attaching themselves to the ship. As the film is slightly soluble, it gradually washes away, ensuring that there is no way for marine life to attach itself to the ship.
In addition to its effectiveness, copper sheathing also offers other benefits such as fuel savings and reduced maintenance costs. Without the need for coatings or cathodic protection, copper-clad hulls can stay at sea for longer periods without the need for cleaning and repairs to the underwater hull. This makes copper sheathing a very attractive option for naval fleets and commercial vessels.
Today, copper is still the most widely used antifouling material, despite the emergence of alternative compounds and metals such as zinc. Modern applications of copper sheathing include Coppercoat, an epoxy-based antifouling option that is effective, hassle-free, and environmentally friendly. Coppercoat can last a decade or more and is a popular choice for larger yachts and commercial vessels.
Fixing Your Boat: Repairing a Speedometer
You may want to see also
Copper floors can be glued to the boat's hull as an alternative to antifoul
Copper floors can be glued to the hull of a boat as an alternative to antifoul. This method of protection for the hull of a wooden vessel was pioneered by the Royal Navy during the 18th century. The copper floors, also known as copper sheathing, protect the boat from attack by shipworm, barnacles, and other marine growth.
The use of copper sheathing was first suggested in 1708, but it was rejected due to its high cost and perceived maintenance difficulties. However, the benefits of copper sheathing became more apparent as deterioration of wooden ship hulls posed significant problems during the Age of Sail. Ships' hulls were under constant attack by marine growth, which adversely affected the ship's speed and handling.
Copper sheathing was found to be an effective solution as it produced a poisonous film when in contact with water, composed mainly of copper oxychloride, which deterred marine organisms. Additionally, as this film was slightly soluble, it gradually washed away, leaving no way for marine life to attach itself to the ship.
Today, copper sheathing is still recognised as an effective method of protecting boat hulls. A modern variation of this technique involves using adhesive-backed copper-nickel foil panels, which can be easily cut and manipulated over the contours of a hull. This method provides the benefits of copper protection while also acting as a barrier to seawater, further protecting the hull from corrosion.
While copper floors glued to a boat's hull can be a more expensive upfront solution, it can last for a decade or more with proper maintenance. This makes it a cost-effective, long-lasting, and environmentally friendly alternative to traditional antifouling methods.
Exploring Italy: Venice to Rome by Boat
You may want to see also
Copper floors are an expensive solution but can last a decade or more
Copper floors, or sheathing, are an effective method of protecting the hull of a wooden vessel from shipworm, barnacles, and other marine growth. While it is an expensive solution upfront, copper sheathing can last a decade or more and brings several benefits.
Copper was first used to protect the hulls of wooden ships in the 18th century by the Royal Navy. The copper plates are affixed to the surface of the hull, below the waterline. When the copper comes into contact with water, it produces a poisonous film, composed mainly of copper oxychloride, that prevents marine organisms from attaching to the ship. This film also gradually washes away, ensuring that nothing can latch onto the ship.
Copper sheathing offers a permanent solution to protecting the hull from corrosion and biofouling, which can increase the frictional drag on the hull and lead to lower speeds and higher fuel consumption. Other methods, such as using corrosion-resisting paints and cathodic protection, are temporary and require frequent replacement, which can be costly and time-consuming.
In addition to its protective properties, copper sheathing can also improve the performance of the vessel. By reducing drag and preventing the build-up of marine growth, copper sheathing can increase the speed and fuel efficiency of the ship. This was demonstrated in trials conducted on the Arco Texas, a crude oil tanker, where the roughness of the copper-sheathed hull was significantly lower than that of a conventionally coated steel hull, resulting in potential improvements in efficiency.
While copper sheathing is expensive, it can be a cost-effective solution in the long run. The upfront cost is offset by the reduced need for maintenance and repairs, as well as the potential fuel savings. For those planning to own their boat for an extended period, copper sheathing can be a worthwhile investment.
Exploring Greece and Cyprus: A Boat's Journey
You may want to see also
Copper floors are hassle-free, environmentally friendly and easy to maintain
Copper floors, or more specifically, copper-nickel (Cu-Ni) floors, offer a hassle-free and environmentally friendly option for boat owners. This material is an ideal choice for boat hulls due to its excellent resistance to corrosion and macrofouling.
One of the biggest advantages of copper floors is their low maintenance requirement. Unlike traditional hull coatings, copper floors do not need to be painted or treated with antifouling agents. This saves boat owners time and money on maintenance and repairs. The copper slowly breaks down over time, exposing new layers of copper and eliminating the need for resanding. Additionally, the copper produces a poisonous film when it comes into contact with water, deterring marine organisms from attaching themselves to the hull. This film also gradually washes away, ensuring that nothing can latch onto the ship.
Copper floors are also environmentally friendly. They eliminate the need for coatings and antifouling paints, which can contain harmful chemicals and compounds that are released into the water. By using copper floors, boat owners can reduce their environmental impact and avoid the use of toxic substances.
The use of copper floors also provides fuel savings. By reducing corrosion and biofouling, copper floors help to lower frictional drag on the hull, resulting in improved fuel efficiency. This not only saves money but also contributes to a more environmentally friendly operation by reducing fuel consumption.
In addition, copper floors are durable and long-lasting. They can last for a decade or more, providing a cost-effective solution over time. They are also easy to repair if scratched or damaged.
Overall, copper floors offer a hassle-free, environmentally conscious, and low-maintenance option for boat owners. They provide protection against corrosion and biofouling while also improving fuel efficiency and reducing maintenance costs.
Bayliner 185: A Good Boat for Beginners?
You may want to see also
Copper floors can be made by stirring a high concentration of copper powder into an epoxy matrix
Copper floors in boats are used to protect the hull of a wooden vessel from attack by shipworms, barnacles, and other marine growth. In modern times, bottom paint infused with high concentrations of copper is used to keep fouling at bay. An alternative to this is Coppercoat, which is an epoxy-based antifouling option that consists of stirring a high concentration of copper powder into an epoxy matrix at the time of application. It is rolled on in multiple layers to a substantial thickness, usually about 12mm, and forms a shell on the bottom of the boat.
To make copper floors using the Coppercoat method, a high concentration of copper powder is stirred into an epoxy matrix at the time of application. The mixture is then rolled onto the boat's hull in multiple layers, usually to a thickness of about 12mm. This forms a shell on the bottom of the boat, which is then sanded before being put in the water. Abrasion from the sanding exposes a fixed layer of copper to the surrounding water.
The Coppercoat method offers several advantages over traditional copper paint. It does not flake like hard or ablative paint, which can lead to the release of large amounts of copper and other chemicals into the water. It is also more cost-effective and longer-lasting, with a lifespan of up to a decade or more. Additionally, it provides an attractive, old-fashioned copper-verdigris look to the bottom of the boat.
When considering Coppercoat for your boat, it is important to keep in mind that it may not be suitable if you are concerned about the appearance of an old-fashioned copper-verdigris look on the bottom of your boat. Additionally, you should be prepared for occasional swims with a mask and sponge to wipe off slime during the season. Overall, Coppercoat offers a durable, environmentally friendly, and cost-effective solution for protecting the hull of your boat.
Mastering the Art of Piloting a V-Drive Boat
You may want to see also
Frequently asked questions
Copper floors, or sheathing, are used to protect the hull of a wooden boat from shipworm, barnacles, and other marine growth.
-
Copper sheathing is a method of protection for the hull of a wooden boat. Copper plates are affixed to the surface of the hull, below the waterline.
-
Copper produces a poisonous film when it comes into contact with water, which deters marine organisms. This film also gradually washes away, leaving no way for marine life to attach itself to the ship.
-
Yes, there are a few alternatives to copper sheathing. One option is to use wood or lead sheathing. Another option is to use a coating made from a mixture of whale oil, rosin, and brimstone (known as "white stuff"); tar and pitch ("black stuff"); or brimstone added to tar and pitch ("brown stuff").