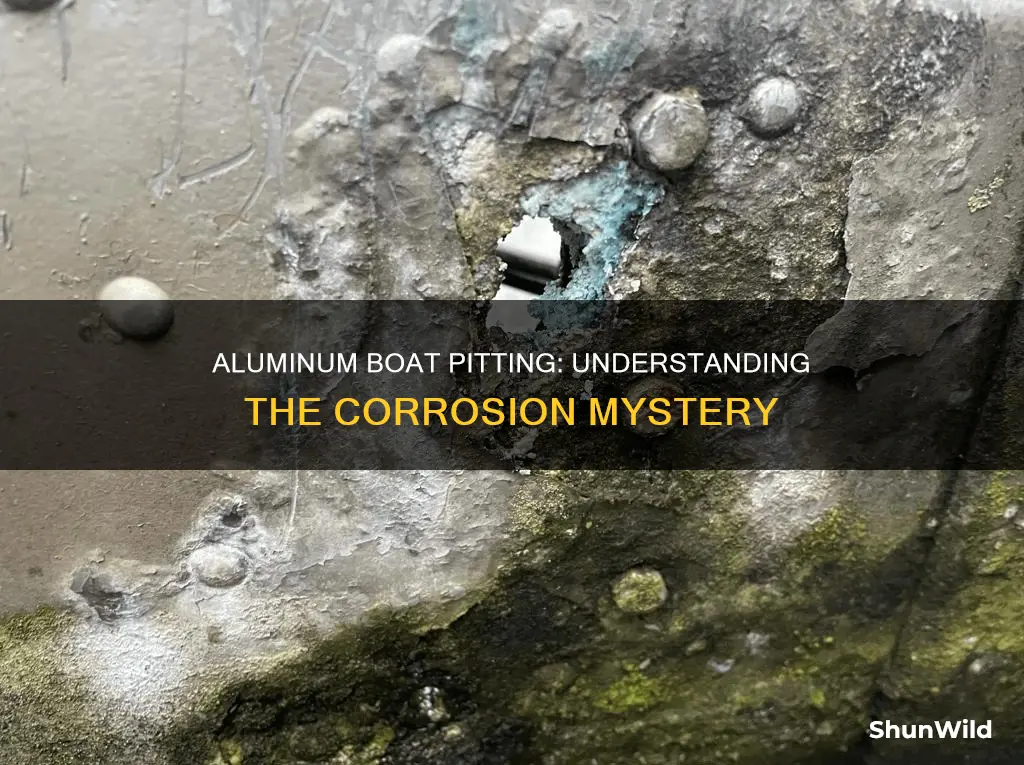
Pitting is a type of corrosion that occurs on aluminum boats, causing small holes to form in the metal. This is often caused by the deterioration of protective coatings around the metal due to contact with a chloride, with saltwater being the main culprit. To repair pitting on an aluminum boat, it is essential to first identify and address the source of the corrosion. This may involve removing any treated wood or other materials that are causing a chemical reaction with the aluminum. Next, the affected areas should be cleaned and dried thoroughly. Once the surface is prepared, various methods can be used to fill in the pits, including dry or wet sanding, using a razor blade, or applying an aluminum filler or putty. After the pits are filled, the area should be buffed until smooth, and a polish and sealer can be applied to protect the aluminum from further oxidation and pitting. Additionally, sacrificial anodes, such as zinc or magnesium, can be attached to the boat to help prevent future corrosion.
Characteristics | Values |
---|---|
Reason for pitting | Saltwater, galvanic corrosion, depassivation, chloride contact, treated wood, stray current, electrolysis, crevice corrosion, copper-rich chemicals, pressure-treated wood, battery on aluminum, etc. |
Repair methods | Dry/wet sanding, razor blade, polishing, waxing, welding, soldering, epoxy, acid wash, sandblasting, acid etching, etc. |
What You'll Learn
- Pitting is a type of corrosion caused by a process called depassivation
- Salt water is the main culprit for pitting in aluminium boats
- Pitting can be fixed by sanding, acid etching, and then applying a coat of polish and sealant
- Sacrificial anodes can be used to protect aluminium boats from corrosion
- Pitting can be caused by electrolysis
Pitting is a type of corrosion caused by a process called depassivation
Pitting is a type of corrosion that creates small holes in metal. It is caused by a process called depassivation, which involves the deterioration of protective coatings around a metal due to contact with a chloride. In the case of aluminum boats, the main culprit for pitting is saltwater.
Pitting corrosion occurs when the protective coating on a metal is damaged, allowing water or corrosive solutions to attack the underlying substrate. This creates a weak point that can lead to rapid and devastating penetration and attack. The adjacent materials may appear unaffected, and pitting corrosion can be difficult to detect as it often occurs in small, localized areas. However, it can have severe consequences if left unchecked, particularly for metal structures such as boats.
The process of pit formation can be understood as a two-step process: nucleation followed by growth. Nucleation occurs when the protective oxide layer isolating the metal substrate from the aggressive solution is disrupted. This can be due to mechanical or physical damage, crystalline defects, or impurity inclusions in the base metal material. The subsequent growth of pits can occur through various chemical reactions, with anions such as chloride and thiosulfate playing a significant role in the local dissolution of the protective oxide layer.
To prevent pitting corrosion, it is essential to minimize exposure to environmental factors such as humidity, temperature, chloride, and pH levels. Additionally, using corrosion-resistant materials, regular washing of fluids in contact with the material, and maintaining protective films can help mitigate the risk of pitting.
Strategic Placement of Reflective Tape on Boat Trailers
You may want to see also
Salt water is the main culprit for pitting in aluminium boats
Saltwater is the main culprit for pitting in aluminium boats. Pitting is a type of corrosion caused by a process called depassivation, which involves the deterioration of protective coatings around a metal due to contact with a chloride. In the case of aluminium boats, saltwater is the primary source of chloride that leads to pitting.
When aluminium comes into contact with saltwater, it triggers a chemical reaction that results in the formation of small holes in the metal, known as pitting. This occurs because saltwater contains high levels of chloride ions, which can break down the protective oxide layer on the surface of aluminium, making it more susceptible to corrosion. Over time, this corrosion can cause extensive damage to the boat, potentially leading to leaks and even structural failure.
To prevent pitting in aluminium boats, it is crucial to minimise exposure to saltwater. This includes rinsing the boat with freshwater after each use and regularly inspecting for any signs of corrosion. Additionally, using non-carpeted bunks and installing sacrificial anodes made of zinc can help reduce the risk of pitting.
If pitting does occur, it is important to address it promptly. Repairs can range from simple filling of small pits to more extensive welding or patching of larger holes. Proper surface preparation is essential, including cleaning, sanding, and treating the affected areas with acid or a conversion coating. Fillers such as epoxy or specialised aluminium repair putty can be used to fill small pits, followed by priming and painting to protect the repaired areas. For more severe cases, welding or patching with new aluminium plates may be necessary.
While it is challenging to completely prevent pitting in aluminium boats, especially in saltwater environments, proper maintenance and prompt repair can help extend the life of the boat and ensure safe operation.
How to Know It's Time to Replace Your Boat Prop
You may want to see also
Pitting can be fixed by sanding, acid etching, and then applying a coat of polish and sealant
Pitting is a type of corrosion that occurs on aluminium boats due to a process called depassivation, which is caused by the deterioration of protective coatings around the metal when it comes into contact with a chloride. Saltwater is the main culprit for pitting on aluminium boats. To remove pitting, start by rinsing off all the dirt and grime from the aluminium surface using a power washer or a hose. Next, wash the surface with a mild alkaline soap, as common dish soap may have high alkaline levels that can strip the wax. Once you're finished washing, dry the surface thoroughly with a microfiber towel.
There are several methods to remove the corrosion:
- Dry Sanding: Start with a higher grit (200-400) sandpaper and work your way to a finer grit (600-800). Use the more abrasive sandpaper to remove deep pits, and then switch to the finer paper. Do two or three rounds of sanding, using a finer grit than the last round.
- Wet Sanding: This method is preferred by some as it does not produce as much dust and does not clog the sandpaper as often as dry sanding. For this method, use sandpaper specifically for wet sanding and start with a grit of around 200-400. Mix a bowl of water with a few drops of dishwashing liquid, wet the paper, and sand off the pitting. Finish by using a fine grit of around 600-800.
- Razor Blade: Use a straight razor blade to lightly scratch off the damaged areas.
After removing the corrosion, use a rotating buffer or fine steel wool to buff the sanded area until it appears smooth and free of all pitting. Finish by wiping off all debris with a clean microfiber towel.
Once the aluminium surface is smooth, you can apply an aluminium polish and sealer using a clean cloth. This will not only brighten the surface but also protect it from further oxidation and pitting.
Boat Slip Ownership: Is It Worth the Cost?
You may want to see also
Sacrificial anodes can be used to protect aluminium boats from corrosion
Aluminium boats are susceptible to pitting, which is a type of corrosion caused by a process called depassivation. This involves the deterioration of protective coatings around the metal due to contact with a chloride. In the case of aluminium boats, the main culprit for pitting is saltwater.
There are two types of corrosion that we need to be wary of as boat owners: galvanic corrosion and electrolytic corrosion.
Galvanic corrosion is caused when parts made from different metals are joined or connected to each other while in water. When dissimilar metals are put into water, a voltage is produced, effectively creating a battery causing one of the components to corrode. The part of the boat lower down in the galvanic series will form the cathode, and the one higher up in the series will be the anode. The anode is the part that will corrode.
For example, when a brass propeller is connected to a stainless steel prop shaft, the brass propeller is the anode and the prop shaft is the cathode. This means that the brass propeller would be the component to suffer corrosion.
Electrolytic corrosion occurs when stray currents from your boat's electrical system or from a shore power system find their way through your hull or hull fitting into the water. The currents in this situation can be much greater and cause more damage than those from galvanic corrosion.
Sacrificial anodes are made from three commonly used materials: aluminium, zinc and magnesium. Selecting which material is best for your sacrificial anode depends on the type of water that the boat is mainly used in.
Aluminium anodes are suited to brackish water or saltwater. They are not suited to freshwater as prolonged exposure can lead to the build-up of an oxide layer, which prevents the anode from working effectively.
Zinc anodes are suited to saltwater, but not recommended for freshwater as prolonged exposure can lead to the build-up of an oxide layer, which prevents the anode from working once the boat is back in saltwater.
Magnesium anodes are suited to freshwater. Magnesium is not suited to saltwater as they are too active in this situation and will corrode too quickly.
Sacrificial anodes should be fitted to each propeller shaft assembly, and additional anodes are often advisable to protect trim tabs and rudders, as well as the hull and keel areas.
When an anode is approaching 50% of its original size, it should be replaced. If in doubt, it is recommended to err on the side of caution. Anodes should be inspected at least every season.
Sacrificial anodes work on a principle similar to electrolysis. In the case of a ship, seawater acts as an electrolyte and transfers the electrons from the anode by oxidising it over the steel plate and making a protecting layer. If the metal is more active, it will be easily oxidised and will protect the metallic compound by making it act as a cathode. The anode will corrode first, sacrificing itself for the other compound.
Sacrificial anodes are used to protect the main hull, ballast tanks and heat exchangers of a ship from corrosion. They are also used to protect sea chests, which are storage chests provided to cater to storage requirements by the sailor.
Sacrificial anodes work without any external power source and are easy to install with the help of bolts, brackets or welds. They also increase the durability or service life of the ship by reducing corrosion attacks.
However, sometimes the material used as an anode is unable to work effectively due to a lack of continuous electrical conductivity. This ineffective working of the anode results in the continuous corrosion of the parent material.
Wiring Boat Batteries: Charging from a Wall Outlet
You may want to see also
Pitting can be caused by electrolysis
Aluminum boats are particularly susceptible to electrolysis because the current will flow through the water, stripping electrons from the metal components, eating away at them as a result. This can happen very quickly and is almost unavoidable with an aluminum boat unless steps are taken to prevent or reduce the damage.
Electrolysis can be prevented by using sacrificial anodes, which are often made of zinc. These anodes are used in saltwater and are located on trim tabs, shafts, and other places. They give up electrons and weaken over time to protect the other, more important parts of the boat.
Other ways to prevent electrolysis include:
- Paint: A good coat of protective paint over metal surfaces will reduce the risk of a reaction.
- Corrosion inhibitors: These make metal resistant to corrosion.
- Check wiring: Electrolysis will only occur in the presence of a current, so if you're in freshwater, there's no need to worry.
- Maintain anodes: Keep them clean and free of any grime or buildup so they can do their job effectively.
- Don't mix metals: Use the same type of metal for fittings, fasteners, etc.
- Keep the power off: When the boat is not in use, shut down magnetic fields to prevent the reaction from occurring.
- Do a test: Hull reference tests can measure the ambient voltage near the boat, helping to determine how many anodes are needed.
By taking these steps, boat owners can effectively prevent electrolysis and protect their aluminum boats from corrosion and pitting.
Boat Starting Guide: Neutral Gear or Not?
You may want to see also