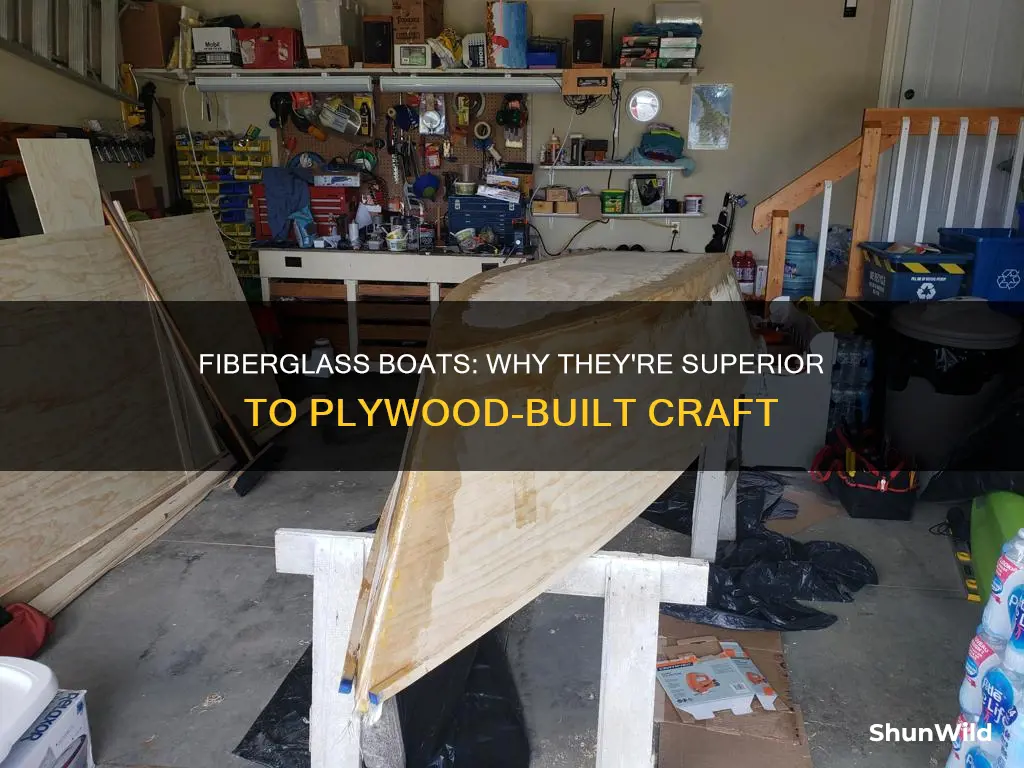
Fiberglass is a popular choice for boat construction due to its superior strength-to-weight ratio compared to plywood. It offers a more durable and lightweight alternative, making it ideal for boats that require strength and rigidity without adding excessive weight. Fiberglass can be molded into various shapes and forms, allowing for intricate designs and smooth, seamless surfaces that enhance the boat's aesthetics and performance. Additionally, fiberglass is resistant to rot, corrosion, and UV damage, ensuring a longer lifespan and reduced maintenance compared to traditional materials like plywood. This makes fiberglass an excellent option for boat builders seeking a reliable and versatile material that can withstand the rigors of marine environments.
Characteristics | Values |
---|---|
Strength | Fiberglass is generally stronger and more durable than plywood, providing better structural integrity for boats. |
Corrosion Resistance | It offers excellent resistance to corrosion, making it ideal for marine environments where saltwater and chemicals are present. |
Lightweight | The material is lightweight, reducing the overall weight of the boat, which can improve fuel efficiency and handling. |
Impact Resistance | Fiberglass is more impact-resistant compared to plywood, making it less prone to damage from waves, anchors, and other marine hazards. |
Smooth Surface | The finished surface of fiberglass is typically smoother, providing a more comfortable and aesthetically pleasing interior for the boat. |
Customization | It can be easily molded and shaped, allowing for more design flexibility and customization options for boat builders. |
Cost-Effectiveness | In the long run, fiberglass can be more cost-effective due to its durability and ease of maintenance. |
Maintenance | Requires less maintenance over time, as it is less susceptible to rot, insect damage, and water absorption. |
Longevity | Fiberglass boats often have a longer lifespan compared to those made with plywood due to its superior material properties. |
Insulation | Provides better insulation, helping to maintain a comfortable temperature inside the boat. |
What You'll Learn
- Cost-Effectiveness: Fiberglass is cheaper than high-quality plywood for boat construction
- Durability: Fiberglass boats are more durable and less prone to damage from water and UV light
- Lightweight: Fiberglass is lighter, making boats easier to handle and faster
- Customizability: Fiberglass can be easily shaped and molded, offering more design flexibility
- Maintenance: Fiberglass requires less maintenance and is easier to clean and repair
Cost-Effectiveness: Fiberglass is cheaper than high-quality plywood for boat construction
Fiberglass is often the preferred material for boat construction due to its cost-effectiveness compared to high-quality plywood. While plywood offers strength and durability, it is significantly more expensive, especially when considering the large surface areas typically required for boat hulls and decks. Fiberglass, on the other hand, provides a lightweight yet robust alternative that is easier and more economical to work with.
The cost advantage of fiberglass becomes evident when you consider the manufacturing process. Fiberglass can be produced in large sheets, which are then cut and shaped to fit the specific requirements of a boat's design. This manufacturing method allows for efficient use of materials, reducing waste and keeping costs down. In contrast, high-quality plywood must be carefully selected and cut to size, which can be a time-consuming and costly process, especially for custom-built boats.
Another factor contributing to the cost-effectiveness of fiberglass is its ability to be reinforced with various materials. It can be strengthened with glass fibers, which are relatively inexpensive, or even cheaper materials like plastic or carbon fiber, depending on the desired performance and budget. This versatility allows boat builders to tailor the material to their specific needs without breaking the bank.
Furthermore, the ease of installation is a significant cost-saving factor. Fiberglass can be applied using a spray-on or hand-lay technique, which is generally faster and requires less specialized equipment compared to the precision and skill needed for plywood construction. This simplicity in installation translates to lower labor costs, making fiberglass an attractive option for both amateur and professional boat builders.
In summary, fiberglass offers a cost-effective solution for boat construction, especially when compared to high-quality plywood. Its efficient manufacturing process, versatility in reinforcement, and ease of installation contribute to its affordability without compromising on strength and durability. These factors make fiberglass an excellent choice for those seeking a balance between performance and budget.
Dispose of a Boat Without Title: A Step-by-Step Guide
You may want to see also
Durability: Fiberglass boats are more durable and less prone to damage from water and UV light
Fiberglass boats offer a significant advantage in terms of durability compared to boats constructed with plywood. This is primarily due to the inherent properties of the materials used. Fiberglass, a composite material made from glass fibers and a resin matrix, is renowned for its strength and resistance to various environmental factors. When used in boat construction, fiberglass provides a robust and long-lasting structure.
One of the key advantages of fiberglass is its ability to withstand the corrosive effects of water. Unlike plywood, which is susceptible to water absorption and can become damaged over time, fiberglass forms a protective barrier around the boat's structure. This barrier prevents water from seeping into the boat's core, reducing the risk of rot, mold, and structural degradation. As a result, fiberglass boats often have a longer lifespan and require less maintenance in terms of repairs due to water-related damage.
UV light is another environmental factor that can take a toll on boat materials. Prolonged exposure to sunlight can cause deterioration and fading in materials like plywood. However, fiberglass boats are designed to be more resistant to UV radiation. The resin used in fiberglass construction acts as a protective shield, minimizing the harmful effects of UV light and preventing premature aging and degradation of the boat's structure. This durability ensures that fiberglass boats maintain their structural integrity and appearance over a more extended period.
In addition, the manufacturing process of fiberglass boats involves a meticulous layering of glass fibers and resin, creating a highly reinforced structure. This construction technique provides excellent impact resistance, making fiberglass boats less susceptible to damage from collisions with objects in the water or even from rough handling during maintenance. The result is a boat that can withstand the rigors of marine environments and provide a reliable and safe vessel for its owner.
Furthermore, the durability of fiberglass boats extends to their ability to retain structural shape and form. Fiberglass's flexibility and ability to conform to design specifications allow for the creation of sleek and aerodynamic hulls. This design feature not only enhances the boat's aesthetics but also contributes to its overall performance and stability on the water. The combination of strength, resistance to environmental damage, and structural integrity makes fiberglass an excellent choice for boat construction, offering a more durable and reliable vessel compared to traditional plywood-based designs.
Repairing a Wooden Boat's Transom: A Step-by-Step Guide
You may want to see also
Lightweight: Fiberglass is lighter, making boats easier to handle and faster
Fiberglass is a popular choice for boat construction due to its exceptional lightweight properties, which offer numerous advantages over traditional materials like plywood. This lightweight nature is a key factor in enhancing the overall performance and handling of boats.
One of the primary benefits of using fiberglass in boat construction is its significantly lower weight compared to plywood. Fiberglass is composed of a matrix of glass fibers and a polymer resin, resulting in a material that is both strong and lightweight. This reduced weight translates to a more manageable boat, making it easier for sailors and boaters to handle and maneuver. Lighter boats require less power to propel, leading to improved fuel efficiency and reduced operating costs. Additionally, the lightweight nature of fiberglass contributes to a faster boat, as less weight means quicker acceleration and higher top speeds.
The lightweight advantage of fiberglass becomes particularly evident when considering the structural integrity of the boat. Plywood, while sturdy, can be heavy and bulky, making it challenging to work with and increasing the overall weight of the vessel. Fiberglass, on the other hand, offers a more efficient and lightweight solution for boat construction. It can be molded into various shapes and forms, allowing for innovative and streamlined designs that minimize drag and maximize speed. This is especially crucial for racing boats or high-performance vessels where every ounce of weight matters.
Furthermore, the lightweight nature of fiberglass contributes to better fuel efficiency. Lighter boats require less fuel to achieve the same speed as heavier vessels, resulting in cost savings for boaters. The reduced weight also means that the boat's engine doesn't have to work as hard to move the vessel, further enhancing fuel efficiency. This is a significant advantage, especially for long-distance cruising or fishing trips where fuel consumption is a critical factor.
In summary, the lightweight property of fiberglass is a compelling reason for its preference in boat construction. It not only makes boats easier to handle and maneuver but also contributes to improved speed, fuel efficiency, and overall performance. The combination of strength and low weight makes fiberglass an ideal material for building boats that are both fast and efficient, providing an enjoyable and practical boating experience.
Who Owns the Renowned Lund Boat Company?
You may want to see also
Customizability: Fiberglass can be easily shaped and molded, offering more design flexibility
Fiberglass is a versatile material that has revolutionized boat construction, offering a level of customizability that plywood simply cannot match. One of the most significant advantages of using fiberglass in boat building is its ability to be easily shaped and molded, which provides designers and builders with unparalleled design flexibility. This flexibility allows for the creation of unique and innovative boat designs that cater to specific needs and preferences.
The process of shaping and molding fiberglass is relatively straightforward and accessible. It involves a combination of techniques such as hand lay-up, spray-up, and vacuum bag molding. With hand lay-up, the fiberglass cloth is manually laid over a mold, and resin is applied to create a solid structure. Spray-up is a faster method where resin is sprayed onto the mold and the fiberglass cloth is laid over it, ensuring an even distribution. Vacuum bag molding utilizes a vacuum to draw the resin and fiberglass into the mold, creating a precise and consistent shape. These methods enable builders to customize the boat's hull, deck, and other components to achieve the desired aesthetics and performance.
The customizability of fiberglass extends beyond the basic shaping process. It can be easily reinforced with various materials to enhance strength and durability. For instance, carbon fiber can be incorporated into the fiberglass to create a lightweight yet robust structure, ideal for high-performance boats. Additionally, fiberglass can be layered and compounded to achieve specific thicknesses and textures, allowing for the creation of intricate designs and detailing. This level of customization ensures that each boat can be tailored to the owner's vision, whether it's a sleek and modern yacht or a classic, timeless vessel.
Furthermore, the flexibility of fiberglass construction enables boat builders to experiment with different hull shapes and designs. They can create sharp, streamlined hulls for racing boats or more rounded and displacement-oriented shapes for cruising vessels. The ability to mold fiberglass around complex contours and curves allows for improved hydrodynamics, reducing drag and enhancing fuel efficiency. This level of design freedom is crucial in the marine industry, where boats are often customized for specific water conditions, passenger capacity, and intended use.
In summary, fiberglass offers an unparalleled level of customizability in boat construction. Its ease of shaping and molding, combined with the ability to reinforce and layer the material, provides designers and builders with the freedom to create unique and tailored boat designs. Whether it's achieving a specific aesthetic, enhancing performance, or catering to individual preferences, fiberglass enables the creation of boats that are not only functional but also truly one-of-a-kind. This customizability is a significant factor in the popularity of fiberglass over plywood in the marine industry.
Glasstream Boats: Worthy Watercraft or Not?
You may want to see also
Maintenance: Fiberglass requires less maintenance and is easier to clean and repair
Fiberglass boats offer a significant advantage when it comes to maintenance compared to traditional plywood construction. One of the primary reasons is the material's inherent durability and resistance to the elements. Fiberglass is less susceptible to rot, decay, and insect damage, which are common issues with wood-based materials. This durability means that fiberglass boats often require less frequent maintenance and are more likely to retain their structural integrity over time.
The smooth and seamless surface of fiberglass also contributes to its ease of maintenance. Unlike plywood, which has visible joints and seams, fiberglass forms a continuous shell, making it harder for water and debris to penetrate and cause damage. This smooth surface is easier to clean and maintain, as it doesn't provide hiding places for dirt, grime, or marine growth. Regular cleaning with mild soap and water is typically sufficient to keep a fiberglass boat in good condition.
In the event of minor damage, fiberglass boats can be repaired more conveniently. Small holes or scratches can be filled and sanded down, often without the need for extensive structural work. This repair process is generally less time-consuming and costly compared to plywood boats, where damage might require replacing entire panels or sections. The flexibility of fiberglass allows for more straightforward repairs, ensuring that the boat can be restored to its original condition with relative ease.
Furthermore, the use of fiberglass in boat construction often results in a lighter vessel, which can be advantageous for maintenance. Lighter boats are easier to handle and maneuver, making it simpler to perform routine maintenance tasks such as cleaning, painting, or applying antifouling treatments. This aspect of fiberglass construction contributes to the overall convenience and cost-effectiveness of maintaining a boat over its lifespan.
In summary, fiberglass boats excel in maintenance due to their durability, seamless construction, and ease of repair. These factors combine to provide boat owners with a more convenient and cost-efficient ownership experience, ensuring that their vessels remain in optimal condition for years to come. The reduced maintenance requirements of fiberglass make it an attractive choice for those seeking a reliable and low-maintenance boat building material.
Cleaning Aluminum Boat Bases: A Step-by-Step Guide
You may want to see also
Frequently asked questions
Fiberglass offers several benefits over plywood in boat building. Firstly, it is a lightweight material, reducing the overall weight of the vessel, which is crucial for performance and fuel efficiency. Fiberglass is also known for its excellent structural strength, providing a sturdy and durable hull. It has a smooth surface, which is ideal for painting and finishing, and its resistance to corrosion and water absorption makes it a preferred choice for marine environments.
Fiberglass, when used in boat construction, forms a strong and rigid structure due to its composite nature. It consists of a matrix of fibers (usually glass fibers) reinforced with a polymer resin. This composite material is highly resistant to impact, abrasion, and the damaging effects of sunlight and water. The resin system used in fiberglass provides excellent bonding, ensuring that the boat's hull and structure remain intact over time, even in harsh marine conditions.
The construction of a fiberglass boat involves several steps. It starts with designing the hull shape and creating a mold or pattern. The fiberglass cloth or mat is then laid over the mold, and the resin is carefully applied to bond the fibers together. This process is repeated layer by layer, creating a thick and strong hull. After curing, the boat is removed from the mold, and any necessary reinforcements or detailing are added. Finally, the boat undergoes finishing processes like sanding, painting, and interior fitting.
Fiberglass is a versatile material that allows for a wide range of design possibilities. It can be molded into various shapes and forms, making it suitable for both traditional and modern boat designs. The manufacturing process of fiberglass boats is often faster and more cost-effective compared to other materials. Additionally, fiberglass boats are known for their ease of maintenance, as they are less susceptible to rot and insect damage, ensuring a longer lifespan for the vessel.
While fiberglass is a popular choice, it's important to consider the environmental impact of its production and disposal. The manufacturing process involves the use of chemicals and energy-intensive processes. However, modern fiberglass materials are designed to be more environmentally friendly, with some manufacturers using recycled content and low-VOC (Volatile Organic Compound) resins. Proper disposal and recycling of old fiberglass boats are essential to minimize environmental impact, as the material can be challenging to recycle due to its composite nature.