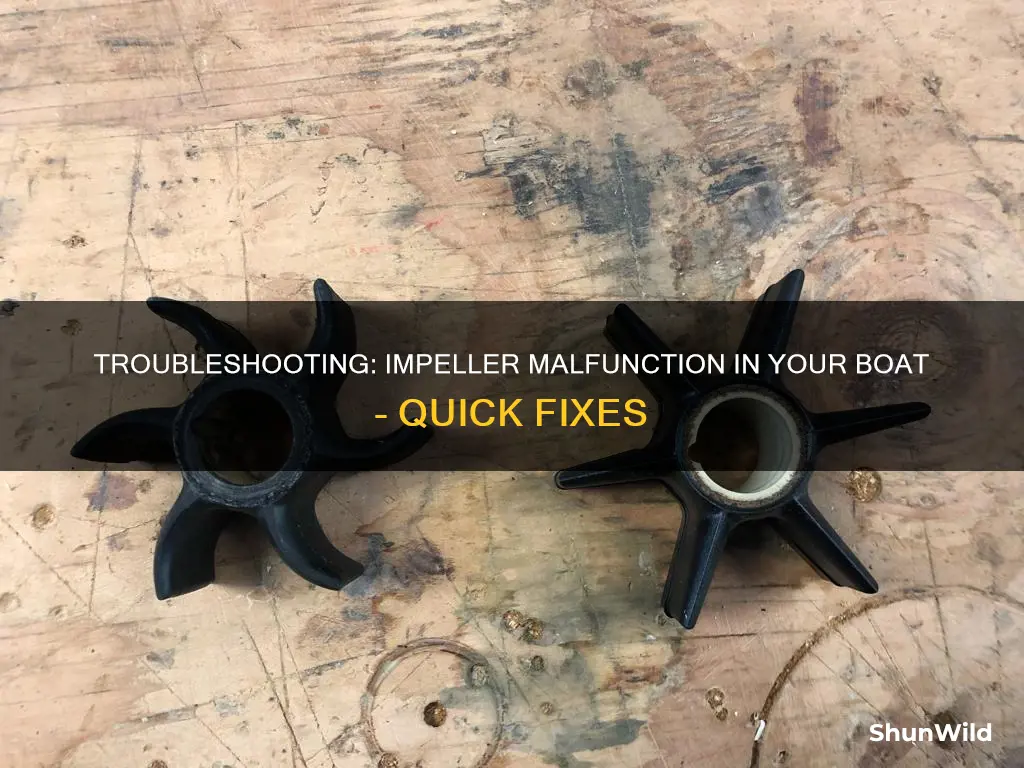
If you're experiencing issues with your boat's impeller regularly going out, it's important to understand the potential causes and solutions. Impellers are crucial components of a boat's cooling system, and their failure can lead to overheating and potential engine damage. Common reasons for impeller failure include blockages from debris or sediment, wear and tear due to age or improper maintenance, and improper installation or alignment. Identifying the root cause will help you determine the appropriate repairs or replacements needed to ensure your boat's cooling system functions optimally and prevent further issues.
What You'll Learn
- Impeller Material: Choose durable materials to withstand water pressure
- Impeller Size: Ensure the impeller size matches the pump's requirements
- Impeller Alignment: Proper alignment prevents impeller damage and ensures efficient operation
- Water Quality: Impeller wear can be caused by contaminants in the water
- Maintenance Schedule: Regular maintenance and inspections can prevent impeller failure
Impeller Material: Choose durable materials to withstand water pressure
When it comes to maintaining a boat's performance, the impeller is a critical component that often requires attention. The impeller is responsible for circulating water through the cooling system, ensuring optimal engine operation. However, many boat owners encounter a common issue: the impeller frequently going out of alignment or failing. One of the primary reasons for this problem is the choice of material, which can significantly impact the impeller's durability and longevity.
The impeller's primary function is to direct water flow, creating a pressure differential that enables the engine to operate efficiently. This process involves handling high-pressure water, which can be extremely demanding on the impeller's structural integrity. Therefore, selecting the right material is crucial to ensure it can withstand the rigorous conditions it encounters.
Durable materials such as stainless steel or specialized alloys are ideal for impellers. These materials offer excellent resistance to corrosion and wear, ensuring that the impeller can handle the constant exposure to water and its associated pressures. For instance, stainless steel impellers are known for their strength and ability to maintain their structural integrity even in harsh marine environments. This material's resistance to rust and corrosion makes it an excellent choice, especially for boats operating in saltwater conditions.
In addition to stainless steel, some manufacturers use advanced composites or ceramic materials. These modern materials provide exceptional strength and heat resistance, making them suitable for high-performance engines. Composite impellers, for example, offer a lightweight yet robust solution, ensuring efficient water flow without compromising on durability.
When choosing an impeller, it is essential to consider the specific requirements of your boat's engine. Consulting with marine experts or referring to the manufacturer's guidelines can help determine the most suitable material. By selecting a durable impeller material, you can significantly reduce the likelihood of frequent replacements and ensure a more reliable and efficient boat operation. This simple yet crucial decision can save boat owners time and money in the long run.
Best Places to Buy Interlux Boat Paint
You may want to see also
Impeller Size: Ensure the impeller size matches the pump's requirements
When it comes to maintaining a boat's propulsion system, one common issue that boat owners often encounter is the frequent failure of the impeller. The impeller is a crucial component of the pump system, responsible for moving water through the engine and driving the propeller. However, if the impeller size is not compatible with the pump's requirements, it can lead to frequent replacements and potential performance issues.
The impeller's size is directly related to its ability to handle the flow rate and pressure generated by the pump. If the impeller is too small, it may struggle to maintain the necessary water flow, resulting in reduced engine performance and potential overheating. On the other hand, an impeller that is too large can create excessive cavitation, which occurs when vapor bubbles form and collapse in the pump, causing damage to the impeller and the overall system.
To ensure optimal performance and longevity of your boat's impeller, it is essential to match the impeller size to the pump's specifications. Manufacturers provide detailed information about the recommended impeller sizes for their pumps. Referring to the manufacturer's guidelines is crucial as it ensures that the impeller can handle the specific flow rate and pressure requirements of your boat's engine. Using the correct size impeller will prevent excessive wear and tear, reduce the risk of failure, and maintain the efficiency of the entire propulsion system.
In some cases, boat owners might consider upgrading to a larger impeller to increase performance. However, this decision should be made carefully, as it may not always be necessary or beneficial. Upgrading to a larger impeller can lead to increased power consumption and potential issues with cavitation. It is advisable to consult with marine mechanics or experts who can assess your boat's specific needs and recommend the appropriate impeller size.
Regular maintenance and inspection of the impeller are also vital. Over time, impellers can become worn out or damaged due to various factors such as cavitation, debris, or improper use. By monitoring the impeller's condition and replacing it when necessary, you can prevent unexpected failures and ensure the overall reliability of your boat's propulsion system.
Charging an Optima Boat Battery: A Step-by-Step Guide
You may want to see also
Impeller Alignment: Proper alignment prevents impeller damage and ensures efficient operation
Impeller alignment is a critical aspect of maintaining the performance and longevity of your boat's water pump system. Proper alignment ensures that the impeller, a crucial component of the pump, operates efficiently and avoids unnecessary wear and tear. When the impeller is misaligned, it can lead to several issues, including reduced performance, increased energy consumption, and frequent failures. Here's a detailed guide on why alignment is essential and how to achieve it.
The impeller is responsible for creating the necessary pressure and flow rate to move water through the system. It is designed to rotate at a specific speed and angle, ensuring optimal performance. Misalignment occurs when the impeller's position or angle deviates from the ideal configuration. This can happen due to various factors, such as improper installation, vibration, or the natural wear and tear of components over time. When the impeller is not aligned correctly, it may rub against other parts, causing damage to the impeller itself and potentially other components of the pump.
To prevent impeller damage and ensure efficient operation, it is essential to check and adjust the alignment regularly. Here are the steps to achieve proper impeller alignment:
- Access the Impeller: Locate the impeller assembly in your boat's water pump system. This is typically found near the engine or the water intake. Carefully remove any access panels or covers to expose the impeller.
- Measure the Impeller's Position: Use a straightedge or a laser alignment tool to measure the distance between the impeller's center and the pump's centerline. Ensure that the impeller is positioned at the correct angle, usually within a small range, to maintain optimal performance. Make detailed notes of the current alignment for future reference.
- Adjust the Impeller: If the impeller is misaligned, you can adjust it by loosening the impeller nut or bolt and gently moving the impeller to the correct position. Tighten the fastener securely but avoid over-tightening, as this can cause additional stress on the impeller. After making adjustments, recheck the alignment to ensure it meets the manufacturer's specifications.
- Secure and Test: Once the impeller is properly aligned, secure it in place and reattach any covers or panels. Start the boat's engine and operate the water pump to ensure the impeller is functioning correctly. Listen for any unusual noises and check for leaks to confirm that the alignment has been successful.
Regular maintenance and alignment checks are vital to keeping your boat's water pump system in top condition. By ensuring proper impeller alignment, you can prevent costly repairs and extend the lifespan of your pump. Remember, if you encounter any issues or are unsure about the alignment process, consulting a professional marine mechanic is always a wise decision.
Replacing Your Boat's Battery Switch: A Step-by-Step Guide
You may want to see also
Water Quality: Impeller wear can be caused by contaminants in the water
Impeller wear in boats is a common issue that can be attributed to various factors, and one of the primary culprits is the quality of the water in which the vessel operates. Contaminants present in the water can significantly contribute to the premature failure of the impeller, a critical component responsible for water circulation and cooling systems.
The impeller, often made of durable materials like bronze or stainless steel, is designed to handle the rigors of marine environments. However, when exposed to water containing abrasive particles, rust, or other foreign matter, its performance can be compromised. These contaminants can cause the impeller to wear down faster, leading to reduced efficiency and, eventually, failure. For instance, sand, silt, or other fine particles in the water can act as sandpaper, gradually eroding the impeller's surface over time.
In addition to physical wear, chemical contaminants in the water can also play a role. Rust, for example, is a common issue in marine environments, especially in areas with high salinity. When water containing dissolved iron or other metals comes into contact with the impeller, it can lead to corrosion, weakening the impeller's structure and reducing its lifespan. This is particularly problematic for aluminum or brass impellers, which are more susceptible to corrosion.
To mitigate these issues, boat owners should consider implementing several measures. Firstly, using a water strainer or filter can help capture and remove contaminants before they reach the impeller. Regularly cleaning and maintaining the water intake system can also prevent the accumulation of debris and reduce the risk of impeller damage. Furthermore, keeping the boat's engine and cooling systems properly maintained can help ensure that the impeller operates under optimal conditions, minimizing the impact of water quality.
In summary, the quality of the water in which a boat operates is a critical factor in impeller wear. Contaminants such as abrasive particles, rust, and other foreign matter can accelerate the impeller's deterioration, leading to frequent replacements. By taking proactive measures to improve water quality and protect the impeller, boat owners can ensure the longevity and reliability of their vessel's cooling and circulation systems.
Martin County Boat Ramps: Open or Closed?
You may want to see also
Maintenance Schedule: Regular maintenance and inspections can prevent impeller failure
Regular maintenance and inspections are crucial for preventing impeller failure in boats, ensuring optimal performance and longevity of the vessel's propulsion system. Impeller issues can be costly and inconvenient, often requiring immediate attention and potentially causing significant downtime. By implementing a structured maintenance schedule, boat owners can identify and address potential problems before they escalate.
The first step in creating an effective maintenance routine is to understand the components of the impeller system. This includes the impeller itself, which is a crucial part of the water pump, and the associated gaskets, seals, and bearings. Each of these elements plays a vital role in the system's functionality and longevity. Regular checks should focus on these critical areas to ensure they are in good condition.
A typical maintenance schedule might include monthly inspections, where boat owners or their mechanics visually examine the impeller and its surrounding parts. This process involves checking for any signs of wear, damage, or leaks. Wear and tear on the impeller blades, for instance, can be identified by their shape and condition. Cracks, chips, or excessive corrosion can indicate potential failure. Similarly, inspecting the gaskets and seals for leaks or deterioration is essential, as these components prevent water intrusion and maintain system efficiency.
Beyond visual inspections, regular maintenance should also include performance tests. This can be done by running the boat's engine and monitoring the impeller's performance. Listen for any unusual noises, such as grinding or whining, which could indicate bearing issues or improper alignment. Additionally, measuring the water flow rate and pressure can help identify any deviations from the expected performance, allowing for early detection of potential problems.
For those who prefer a more proactive approach, regular maintenance can also involve the use of specialized lubricants and cleaning agents. Applying the right type of lubricant to the bearings and other moving parts can reduce friction and wear, thus extending the impeller's lifespan. Cleaning the system regularly to remove debris and contaminants can also prevent blockages and ensure smooth operation.
In summary, a well-structured maintenance schedule is essential for preventing impeller failure in boats. By incorporating regular inspections, performance tests, and appropriate maintenance practices, boat owners can ensure their vessels remain reliable and efficient. This proactive approach not only saves costs but also minimizes the risk of unexpected breakdowns, allowing for a safer and more enjoyable boating experience.
Fort Lauderdale Boat Show: Open for Business
You may want to see also
Frequently asked questions
Impeller issues in boats are often caused by improper installation or alignment. Ensure the impeller is securely fitted and aligned with the engine's water pump. Over time, the impeller can become worn out, leading to reduced suction and potential dislodgement. Regular maintenance and inspection can help identify and replace worn-out parts.
Yes, the water intake system plays a crucial role in keeping the impeller in place. If the intake screen or strainer is clogged with debris, it can create excessive pressure on the impeller, causing it to pop out. Regularly clean and maintain the water intake system to prevent this issue.
High-speed operation or excessive water pressure can strain the impeller and potentially cause it to come loose. Ensure that your boat's speed and water flow are within the recommended limits to avoid putting unnecessary stress on the impeller.