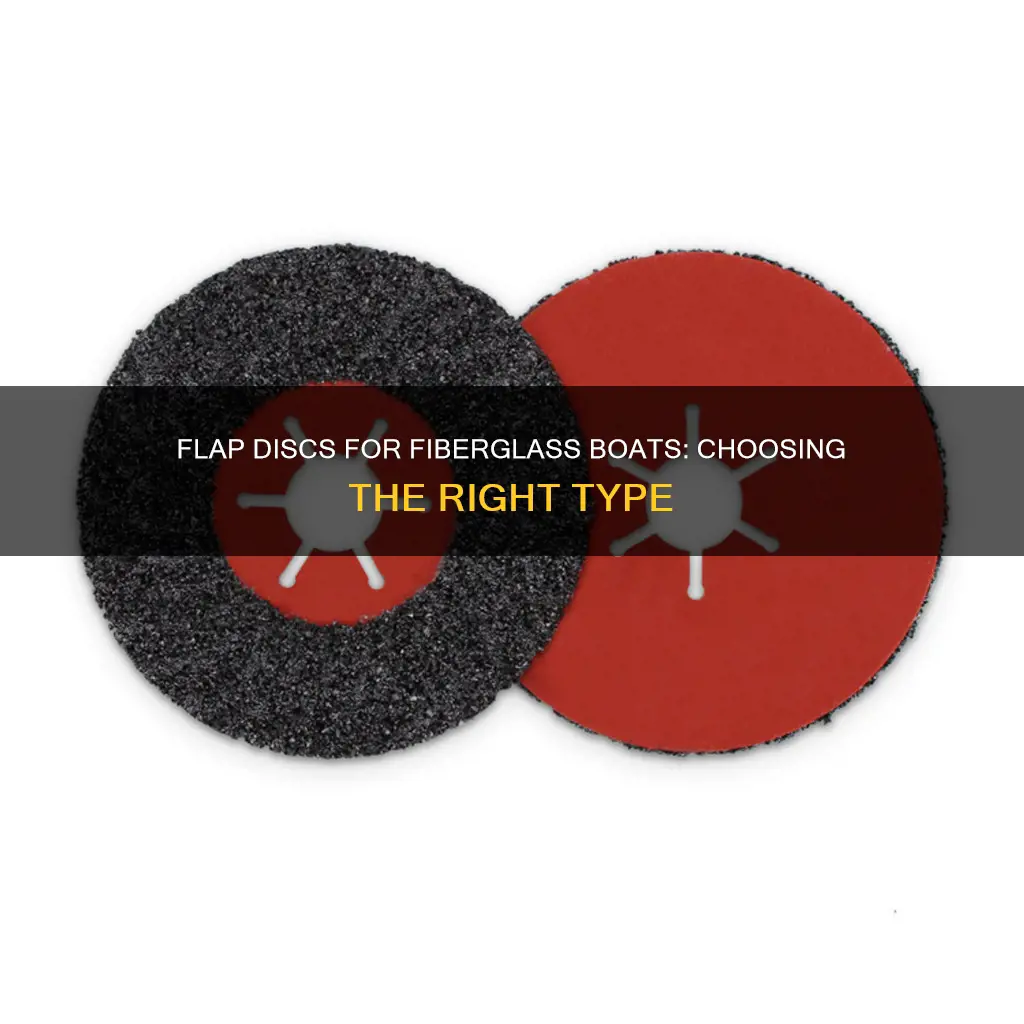
When it comes to maintaining a fiberglass boat, choosing the right flap discs is crucial for effective sanding and restoration. Flap discs are versatile tools that can help remove old paint, repair minor damage, and smooth surfaces. For fiberglass boats, it's essential to select flap discs that are specifically designed for composite materials. These discs should offer a balance of durability and flexibility to handle the unique characteristics of fiberglass. The right flap discs will ensure a smooth finish and help preserve the boat's structural integrity.
What You'll Learn
- Material: Choose from aluminum oxide, silicon carbide, or zirconia for specific applications
- Thickness: Select a thickness based on the desired cut rate and material hardness
- Hole Size: Ensure compatibility with your power tool's spindle hole
- Backing Material: Opt for a durable backing material like fiber or resin-bonded paper
- Coating: Consider a protective coating to enhance durability and prevent fiber wear
Material: Choose from aluminum oxide, silicon carbide, or zirconia for specific applications
When it comes to choosing the right flap disc for your fiberglass boat, the material is a critical factor that can significantly impact performance and longevity. The three primary materials to consider are aluminum oxide, silicon carbide, and zirconia, each with unique properties suited to specific applications.
Aluminum oxide is a versatile and cost-effective option, making it a popular choice for general-purpose flap discs. It offers a balanced combination of hardness, durability, and heat resistance, making it suitable for a wide range of applications. This material is ideal for smoothing and finishing fiberglass surfaces, as it provides a smooth cut and a consistent finish. However, it may not be the best choice for aggressive cutting or heavy-duty applications due to its relatively lower hardness compared to other materials.
Silicon carbide, on the other hand, is known for its exceptional hardness and heat resistance. This material is an excellent choice for applications that require a more aggressive cut and high material removal rates. Silicon carbide flap discs are particularly useful for removing thick layers of material or when working with harder substrates. They provide a faster cut and can be more durable, making them suitable for heavy-duty tasks. However, they may not be as gentle on the surface as aluminum oxide, so they should be used with caution to avoid damage to the fiberglass.
Zirconia flap discs offer the highest hardness and heat resistance among the three materials. They are designed for the most demanding applications, providing an extremely aggressive cut and exceptional durability. Zirconia is ideal for heavy-duty tasks, such as removing old paint, heavy material, or even metal. Its hardness and heat resistance make it a powerful tool for professionals who need to work with tough materials. However, due to its hardness, it may require more careful application to avoid scratching or damaging the fiberglass surface.
In summary, the choice of material depends on the specific requirements of your project. Aluminum oxide provides versatility and cost-effectiveness, silicon carbide offers a more aggressive cut, and zirconia delivers the highest performance for heavy-duty tasks. Understanding the properties of each material will help you select the most appropriate flap disc for your fiberglass boat, ensuring efficient and effective results.
Placing a Boat's Engine: Factors for Optimal Positioning
You may want to see also
Thickness: Select a thickness based on the desired cut rate and material hardness
When it comes to choosing the right flap disc for cutting fiberglass boats, thickness is a critical factor that directly impacts the performance and longevity of the disc. The thickness of a flap disc refers to the depth of the cutting layer, which determines how quickly the disc will wear down and how aggressive the cutting action is.
The desired cut rate is a key consideration. A higher cut rate means the disc will wear down faster, resulting in a more aggressive cut. This is beneficial for quickly removing material, especially when dealing with thick fiberglass layers. However, a higher cut rate also means the disc will have a shorter lifespan, requiring more frequent replacements. On the other hand, a lower cut rate provides a longer-lasting disc, which is ideal for more delicate work or when precision is essential.
Material hardness also plays a significant role in determining the appropriate thickness. Harder materials, such as those with higher resin content, require a thicker flap disc to achieve the desired cut rate. Thicker discs provide more cutting power, allowing for faster material removal. Conversely, softer materials may only need a thinner disc to achieve the required cut rate, ensuring a longer-lasting disc and potentially reducing the risk of damage to the workpiece.
Selecting the right thickness involves finding a balance between the desired cut rate and material hardness. For example, if you're working with a hard fiberglass material, a thicker disc with a higher cut rate might be necessary to make significant progress. However, for softer materials or when precision is crucial, a thinner disc with a lower cut rate could be more suitable.
In summary, when choosing flap discs for fiberglass boats, consider the desired cut rate and material hardness to determine the optimal thickness. This ensures efficient material removal while maintaining the disc's durability and longevity, ultimately contributing to a successful and safe cutting process.
Boat Engine Failure: Is Insurance Coverage Available?
You may want to see also
Hole Size: Ensure compatibility with your power tool's spindle hole
When it comes to choosing the right flap disc for your fiberglass boat, one crucial aspect to consider is the hole size. This detail is often overlooked, but it plays a significant role in ensuring compatibility and optimal performance. The spindle hole, also known as the arbor hole, is the central opening in the disc where it attaches to your power tool. It's essential to match this hole size to the spindle of your tool to achieve a secure and efficient connection.
In the world of power tools, various spindle sizes are available, and they can range from 1/4-inch to 1/2-inch in diameter. The hole size in your flap disc should correspond to the spindle size of your tool. For instance, if you have a power tool with a 1/4-inch spindle, you'll need a flap disc with a 1/4-inch hole. This compatibility ensures that the disc is firmly attached, preventing any wobbling or instability during use, which could lead to uneven cuts or damage to the tool.
To determine the correct hole size, start by checking your power tool's manual or specifications. Most manufacturers provide detailed information about the spindle size, often listed in the tool's documentation. Alternatively, you can physically measure the spindle hole on your tool using a caliper for accuracy. This measurement will give you the exact diameter, ensuring you select a flap disc with a matching hole size.
It's worth noting that some power tools may have interchangeable spindles or adapters, allowing for versatility. In such cases, you might need to consider the range of spindle sizes your tool can accommodate. This information will help you choose a flap disc with a hole size that fits within the acceptable range, ensuring compatibility.
In summary, paying attention to the hole size is vital when selecting flap discs for your fiberglass boat. Compatibility with your power tool's spindle hole ensures a secure attachment, leading to precise cuts and a longer tool lifespan. Always refer to your tool's specifications or measure the spindle hole to make an informed decision.
Revamping Boat Seats: Cutting and Upholstering Made Easy
You may want to see also
Backing Material: Opt for a durable backing material like fiber or resin-bonded paper
When it comes to choosing the right flap discs for your fiberglass boat, one crucial aspect to consider is the backing material. This component plays a vital role in determining the durability, performance, and overall quality of the disc. Opting for a durable backing material is essential to ensure that your flap discs can withstand the rigors of marine environments and provide long-lasting results.
Fiberglass boats present unique challenges when it comes to sanding and finishing. The material is known for its strength and lightweight nature, but it can be delicate and prone to damage if not handled properly. This is where the backing material comes into play. By selecting a robust backing, you create a sturdy foundation for your flap discs, enabling them to effectively cut and shape the fiberglass surface without compromising their integrity.
One popular choice for backing materials is fiber. Fiber-backed flap discs offer excellent durability and heat resistance, making them ideal for aggressive sanding applications. The fibers provide a strong and flexible support system, allowing the disc to maintain its shape and cutting performance even under heavy pressure. This is particularly beneficial when working with the curved and contoured surfaces often found on boats.
Another excellent option is resin-bonded paper. Resin bonding provides a strong and durable backing that can handle the demands of marine environments. This type of backing is known for its ability to withstand moisture and humidity, ensuring that your flap discs remain effective even in wet conditions. Resin-bonded paper is also flexible, allowing for a smooth and even finish when sanding fiberglass.
In summary, when selecting flap discs for your fiberglass boat, prioritizing a durable backing material is essential. Fiber and resin-bonded paper are excellent choices, offering strength, flexibility, and resistance to the unique challenges posed by marine environments. By investing in high-quality backing materials, you can ensure that your flap discs provide exceptional performance and longevity, making the sanding and finishing process a more efficient and rewarding experience.
Charging Boat Batteries: Alternative Methods to Standard Chargers
You may want to see also
Coating: Consider a protective coating to enhance durability and prevent fiber wear
When it comes to maintaining and repairing a fiberglass boat, the choice of flap discs (also known as flap wheels) is crucial for achieving a smooth and professional finish. One often overlooked but essential aspect is the application of a protective coating. This simple yet effective step can significantly enhance the durability and longevity of your boat's surface.
Fiberglass, being a composite material, can be susceptible to wear and tear, especially when using flap discs for cutting, sanding, or polishing. The abrasive action of the flap discs can gradually wear down the fibers, leading to a rough and uneven surface. To combat this, consider applying a protective coating specifically designed for marine environments. These coatings are typically made from epoxy or polyurethane resins, which create a hard, protective layer over the fiberglass. This layer acts as a barrier, preventing the abrasive particles from directly interacting with the fibers and causing wear.
The benefits of using a protective coating are twofold. Firstly, it increases the durability of the boat's surface, making it more resistant to scratches, chips, and other forms of damage. This is particularly important for high-traffic areas or when performing aggressive sanding or cutting operations. Secondly, the coating helps to maintain the original appearance of the fiberglass, ensuring that the boat retains its sleek and smooth finish. This is especially crucial for aesthetic reasons and can also impact the boat's resale value.
When choosing a protective coating, it is essential to select a product that is compatible with fiberglass and marine conditions. Look for coatings that are specifically formulated for use in saltwater environments, as these will provide the necessary protection against corrosion and UV degradation. Additionally, consider the application process; some coatings may require multiple layers or specific priming to ensure optimal adhesion and protection.
In summary, applying a protective coating to your fiberglass boat is a simple yet powerful way to enhance its durability and appearance. By choosing the right coating and following the manufacturer's instructions, you can ensure that your boat remains in excellent condition, even when using flap discs for various maintenance and repair tasks. This additional step will contribute to the overall longevity and beauty of your vessel.
Installing a Radio on Your Paddle Boat: A Simple Guide
You may want to see also
Frequently asked questions
The choice of flap disc depends on the specific application and the condition of your boat's surface. For general maintenance and light sanding, a medium-grit flap disc (e.g., 80-grit) is often recommended. This grit size is versatile and can handle various materials, including fiberglass. For more aggressive sanding or removing old paint, consider a higher grit (e.g., 120-grit or higher) flap disc, which will provide a smoother finish.
Flap discs come in various sizes, typically ranging from 4 to 12 inches in diameter. The size you need depends on the area you want to work on; larger sizes are efficient for wide panels, while smaller sizes offer more precision. Thickness is also important; for fiberglass, a standard thickness of 0.025 inches is common, but you can opt for a thinner (0.015 inches) or thicker (0.035 inches) disc depending on the depth of the material and the desired sanding effect.
Yes, safety is crucial when working with flap discs. Always wear protective gear, including safety goggles and a dust mask, to guard against debris and fiber inhalation. Ensure your work area is well-ventilated. When sanding, maintain a steady hand and a consistent pressure to avoid damaging the fiberglass. It's also essential to follow the manufacturer's guidelines for your specific flap disc and boat material to ensure optimal results and prevent any accidents.
Yes, flap discs can be used on gelcoat and painted surfaces, but it requires careful consideration. For gelcoat, a finer grit (e.g., 180-grit or higher) is often preferred to avoid scratching the surface. Start with a lower grit if necessary and gradually move to finer grits. When working on painted surfaces, use a flap disc with a very fine grit to avoid removing the paint. Always test in an inconspicuous area first to ensure you're satisfied with the results before proceeding.