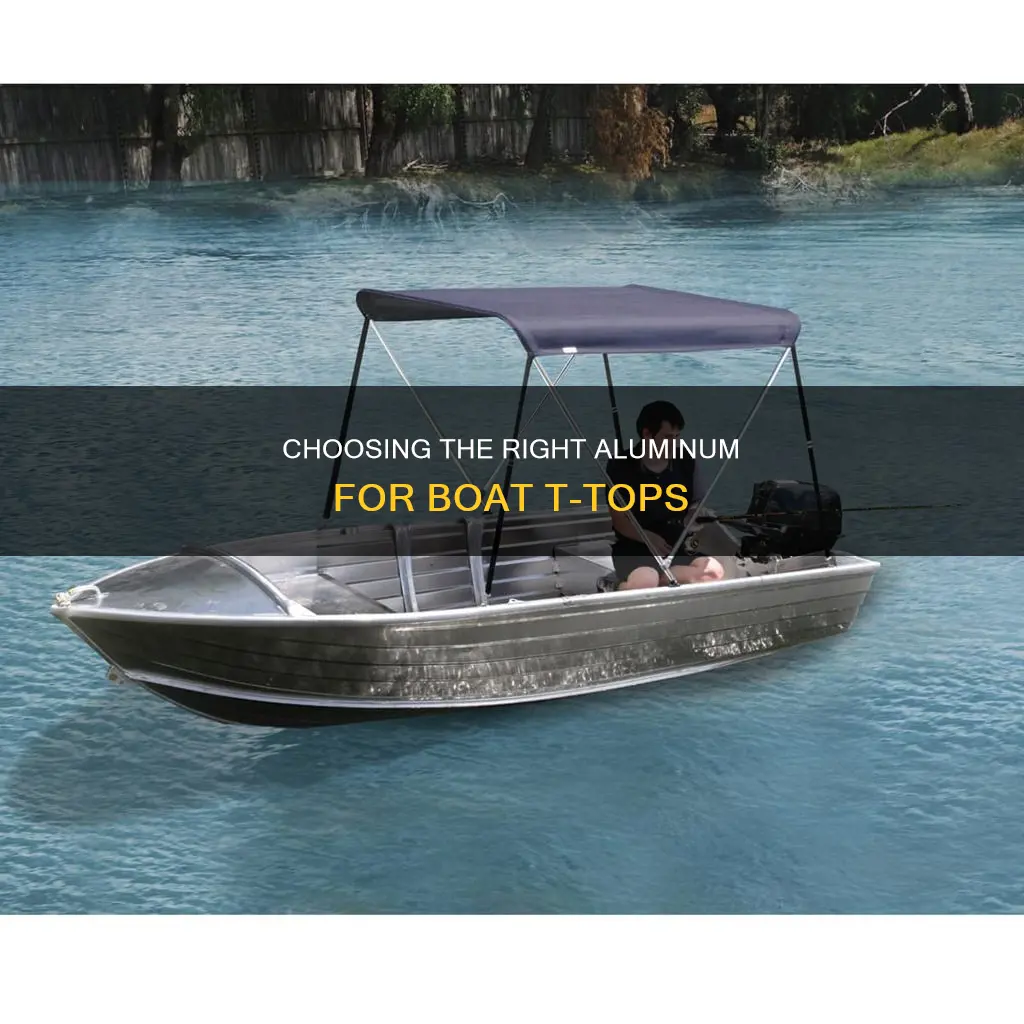
Boat T-tops are a great investment for boat owners, providing shade, functionality for fishing, and increasing the boat's resale value. When selecting a T-top, it is important to consider the type of metal used, as this will impact the T-top's durability, weight, and resistance to corrosion. The most common types of aluminum used for boat T-tops are 6061-T6 and 6063 aluminum. 6061-T6 aluminum is a durable alloy with excellent corrosion resistance and is commonly used in airplanes, race cars, and bicycles. On the other hand, 6063 aluminum is weaker and has lower tensile strength and yield strength but is more malleable and commonly used in architectural applications. Another option for T-tops is stainless steel, which is strong but heavy and not used by many manufacturers. When choosing a T-top, it is crucial to consider the material's durability, weight, and resistance to corrosion to ensure the T-top can withstand water, wind, and sun exposure.
Characteristics | Values |
---|---|
Most durable alloy | 6061-T6 aluminum |
Corrosion-resistance | 6061-T6 aluminum |
"Architectural grade" | 6063 aluminum |
Heavy | Stainless steel |
Cheaper | 6063 aluminum |
Bends easily | 6063 aluminum |
High level of temper | T6 |
Good corrosion-resistance | Anodized aluminum |
What You'll Learn
6061-T6 aluminum alloy is the best option
The "T6" in 6061-T6 indicates that the alloy has been solution heat-treated and artificially aged, resulting in increased hardness and strength. This tempering process enhances the alloy's durability, making it less prone to cracking and breakage.
Compared to other metals used for boat T-tops, such as 6063 aluminum and stainless steel, 6061-T6 aluminum alloy offers superior strength and corrosion resistance. It is commonly used in applications that require high strength, including airplanes, race cars, and bicycles.
Additionally, 6061-T6 aluminum alloy is easy to work with. It can be cut, drilled, and formed into various shapes, making it a versatile choice for boat T-tops. Its lightweight nature also makes it easier to install, and its corrosion resistance ensures that it will stand up to exposure to water, wind, and sun.
In summary, 6061-T6 aluminum alloy is the best option for boat T-tops due to its strength, durability, corrosion resistance, and ease of fabrication. It is a safe and reliable choice for boat owners, ensuring that their T-tops will withstand the rigors of marine environments.
Unfastening Your Boat Battery: A Step-by-Step Guide
You may want to see also
6063 aluminum is weaker but more malleable
6063 aluminium alloy is a popular choice for boat t-tops, but it is weaker than other alloys. It has roughly half the strength of 6061-T6 aluminium, which is the most durable option. 6063 aluminium is considered an "architectural grade" alloy, making it more suitable for applications where strength is not the main requirement.
The 6063 alloy is often referred to as "architectural aluminium" due to its common use in architectural applications such as window and door frames, roofs, and sign frames. It is also used for pipe and tubing, furniture, and decorative materials. This alloy is well-suited for these applications because it can be formed into complex shapes with very smooth surfaces.
While 6063 aluminium is weaker than other alloys, it does offer some advantages. It has good corrosion resistance, weldability, and workability. It can be tempered to achieve greater strength, and it is highly weldable using tungsten inert gas welding. Additionally, 6063 aluminium is easier to form into complex shapes compared to other alloys like 6061-T6.
When choosing a boat t-top, it is important to consider the balance between strength and malleability. 6063 aluminium may be a suitable option if you prioritise the ability to form complex shapes and smooth surfaces over maximum strength. However, if durability and strength are your primary concerns, then 6061-T6 aluminium would be the better choice.
Transferring Boat Ownership: Signing Over a Title in Wisconsin
You may want to see also
Stainless steel is strong but heavy
While stainless steel is a strong material, it is also very heavy. This makes it less than ideal for boat t-tops, as it can negatively impact a boat's performance and stability.
Stainless steel is about three times heavier than aluminum, which is the most common material used for t-tops. Aluminum is preferred because it is strong, lightweight, corrosion-resistant, and easy to clean.
Stainless steel is also more expensive than aluminum, and it is more difficult to work with. It is harder to cut and form, and it requires special tube benders. It is also challenging to prepare stainless steel for welding joints, and the joints must be perfectly tight before welding to avoid weakening the area surrounding the weld.
For these reasons, most boat t-tops are made from aluminum, specifically the 6061-T6 aluminum alloy. This alloy is commonly used in applications that require high strength, such as airplanes, race cars, and bicycles. It has excellent corrosion resistance and is known for its durability.
While stainless steel may be stronger than aluminum, its weight and cost make it a less practical choice for boat t-tops.
Being a Boat Captain: Essential Skills and Traits
You may want to see also
Anodized aluminum is easy to maintain
Anodized aluminum is a popular choice for boat t-tops, and for good reason. It offers a durable, long-lasting, protective, and lustrous finish that is perfect for the marine industry. Anodized aluminum is also easy to maintain, ensuring that your boat t-top stays in top condition for years to come. Here are some tips to help you keep your anodized aluminum boat t-top in tip-top shape:
Cleaning and Maintenance:
- Determine the Condition: Before cleaning, assess the condition of the surface and how long it has been since the last cleaning. If your t-top is regularly maintained, a simple wash-down with a mild soapy solution or warm water with a wetting agent will suffice.
- Mild Abrasives: Anodizing creates a hard finish, so mild abrasives or an abrasive cleaning sponge can be used to tackle more stubborn grime. However, always consult a professional before using any abrasive cleaning products, and be sure to test any cleaning solutions on a small, inconspicuous area first.
- Avoid Harsh Cleaners: Stay away from harsh acidic or alkaline cleaners, as these can damage the anodized finish. Solvents should also be used with care, as they may stain the finish.
- Rinse Thoroughly: After cleaning, be sure to rinse thoroughly with water, especially in crevices, to ensure the removal of all residues. Improper rinsing can lead to etching or discoloration.
- Avoid Abrasive Materials: Do not use emery paper, sandpaper, steel wool, or other highly abrasive materials to remove grime, as these can damage the anodized coating.
- Frequency of Cleaning: The frequency of cleaning will depend on various factors, such as your location, local climate, exposure to saltwater, and direct sunlight. Typically, cleaning should be done every month to every six months, with a focus on regular mild cleaning rather than less frequent harsh cleaning.
Benefits of Anodized Aluminum:
Anodized aluminum is a great choice for boat t-tops due to its durability and ease of maintenance. It is chemically stable, non-toxic, and heat-resistant, making it a safe and long-lasting option. Additionally, its corrosion resistance makes it ideal for the marine environment.
Anodized vs. Polished Aluminum:
While anodized aluminum is low-maintenance and protective, polished aluminum requires frequent and diligent cleaning, polishing, and protection. Polished aluminum is raw aluminum with a mirror finish, which is susceptible to damage from saltwater and atmospheric contaminants.
By choosing anodized aluminum for your boat t-top and following the recommended cleaning and maintenance tips, you can enjoy a durable, protective, and low-maintenance finish that will enhance the functionality and aesthetics of your boat for years to come.
Boys in the Boat: Rated PG-13 for Intense Rowing Scenes
You may want to see also
Polished aluminum is high-maintenance
Polished aluminum is raw aluminum that has been buffed and polished to a mirror finish. This process is typically done by hand and can be time-consuming and expensive. While polished aluminum has a vibrant and bright silver color, it has zero protection. This means that it requires frequent and diligent cleaning, polishing, and protection.
Maintenance
Polished aluminum is commonly used in owner-operated or small to midsize fleets, as well as brand-new fleet vehicles. To maintain the mirrored finish, it is recommended to wash the aluminum at least once a week or more, depending on usage. The wash process should include a pre-treatment, such as applying a polish-safe bug remover or degreaser, followed by the application of specialty detergents. After washing, it is important to dry the aluminum with a fine cloth or chamois to avoid causing abrasions.
Protection
To protect the finish of polished aluminum, it is essential to seal the surface to prevent oxidation and corrosion. This can be done by using a clear powder coat, lacquer finish, or polyurethane finish. These coatings will distort the light reflection and reduce the sharpness of the finish by a small amount. Alternatively, Shark Mouth, a marine coating, can be applied with a soft cloth to protect the finish. For an even more brilliant shine, a two-part clear coat like POR15 Glisten PC can be applied after neutralizing the aluminum with a prep solution.
Comparison to Other Metals
Polished aluminum is brighter and more reflective than non-polished aluminum, which has a satin-silver appearance. It is also more prone to scratches and corrosion than stainless steel, which has a denser, more corrosion-resistant, and naturally satin-silver finish. Stainless steel is commonly used for food-grade and hazardous material transport due to its higher resistance to corrosion.
While polished aluminum can provide a vibrant and mirror-like finish, it requires regular maintenance and protection to prevent oxidation and corrosion. This involves frequent washing, drying, and the possible application of specialty coatings.
Painting Pup on a Row Boat: A Creative Guide
You may want to see also
Frequently asked questions
6061-T6 aluminum alloy is considered the best type of metal for boat T-tops due to its high strength, corrosion resistance, and durability. It is also lightweight, easy to clean, and commonly used in applications such as airplanes, race cars, and bicycles.
6061-T6 aluminum is a high-grade, aircraft-grade alloy with greater tensile strength, yield strength, and durability compared to 6063 aluminum. 6063 aluminum is primarily used for architectural applications and is easier to extrude, bend, and finish, but it is not as strong.
While it is possible to weld aluminum with a MIG welder, it is not recommended for boat T-tops. MIG welding can result in filler buildup and pinhole welds, which can lead to corrosion issues. TIG welding is a better option for aluminum boat T-tops as it provides more control and precision.
Anodizing creates a hard, corrosion-resistant finish that protects the aluminum from saltwater and atmospheric contaminants. It is easy to maintain and provides long-lasting protection for the T-top. However, it requires specific cleaning products and regimens for proper care.