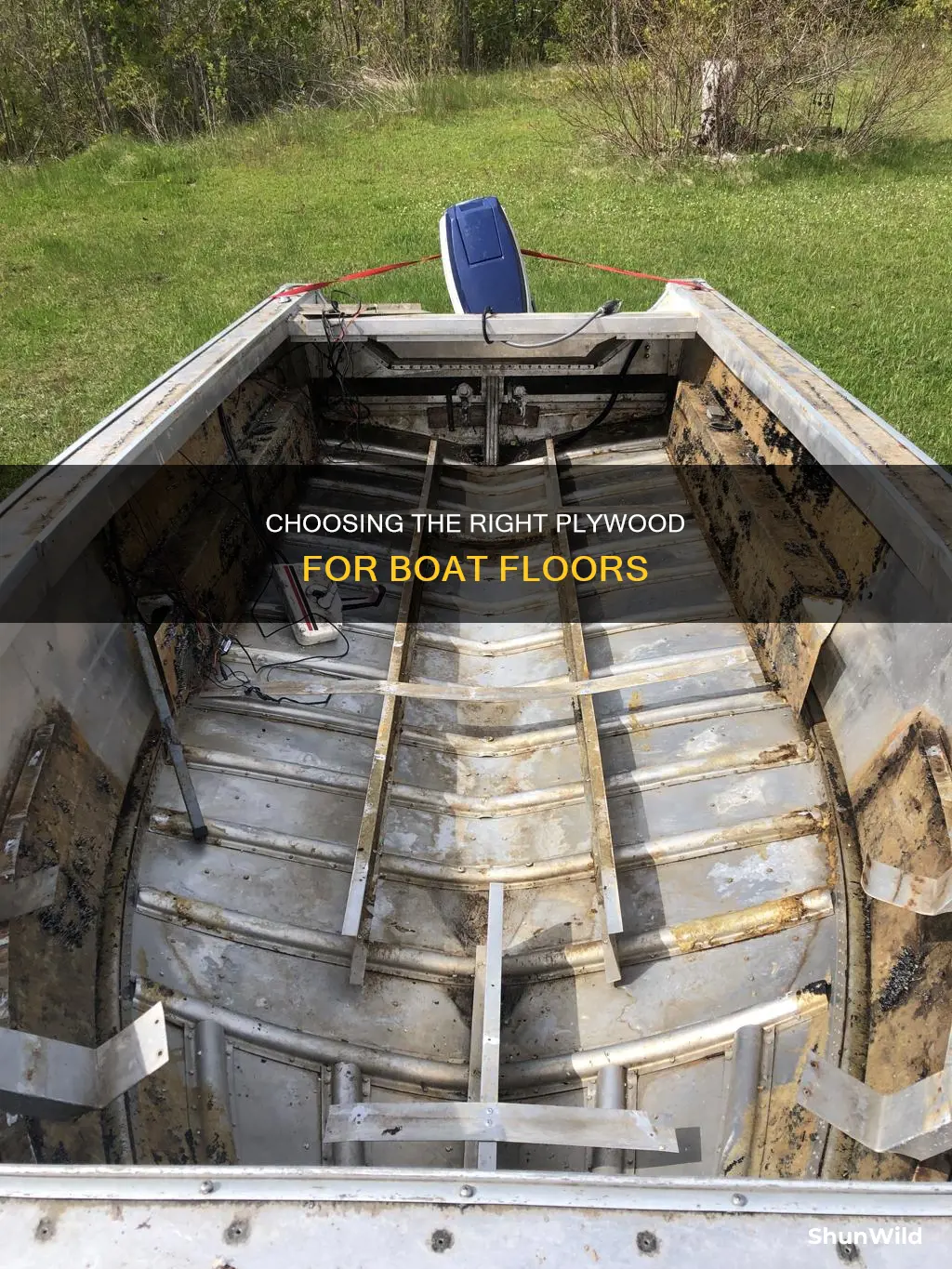
Plywood is a popular material for boat floors thanks to its high strength and relative affordability. However, not all plywood is created equal, and there are several factors to consider when choosing the right plywood for your boat floor. The most important factor is the type of plywood, as certain types are better suited for boat floors than others. For example, marine-grade plywood is designed for strength and durability in water, while exterior-grade plywood is a more affordable option that can be sealed with resin to prevent rot. In addition to the type of plywood, the thickness and number of plies are also important considerations, as they will affect the stiffness and load-bearing capacity of the floor. Proper treatment and installation are also key to ensuring the longevity of your boat floor.
What You'll Learn
Marine-grade plywood is designed for strength
Marine plywood is not waterproof or rot-proof, contrary to popular belief. It is essential to treat it with CCA (Chromated Copper Arsenate) to protect against rot. CCA treatment involves applying chemicals under pressure to the wood, altering its chemical composition and making it insoluble. This process ensures that wood-destroying organisms cannot survive on the plywood panels as they cannot use the treated wood as a food source.
When selecting plywood for boat flooring, it is crucial to consider the thickness. While thinner plywood like 3/8" can be used, it may not provide sufficient stiffness, depending on the supporting structure. Thicker plywood, such as 3/4", offers greater stiffness and strength due to its higher number of wood veneers.
In addition to the type of plywood, the glass fibre coating plays a vital role in the overall strength and durability of the boat floor. It is recommended to use glass fibre cloth, such as 18oz woven roving, to provide strength and control checking. The underside of the plywood should also be coated with a layer of glass fibre to seal it from moisture.
By combining marine-grade plywood with the right thickness and a well-applied glass fibre coating, you can achieve a strong and durable boat floor.
Finding Lobster Boats: Exploring Maine's Coastal Culture
You may want to see also
Epoxy resin is the best coating for plywood
Epoxy resin is a good choice for plywood boat floors as it will seal the wood, preventing water ingress and rot. It can also repair and preserve old boats made from plywood. When applying epoxy resin, it is important to prepare the plywood properly. This includes removing any fittings and decorative coatings, washing the surface, and abrading it with paper to create a texture that the epoxy resin can adhere to.
When coating plywood with epoxy resin, it is best to apply several thin coats, allowing each coat to become tacky before applying the next. This is known as the "wet-on-tacky" method and helps create a strong, watertight seal. It is also important to work on cool, overcast days as the epoxy resin can create air bubbles when applied in direct sunlight.
In addition to its waterproofing qualities, epoxy resin can also be used to fill and stabilise areas of rot in plywood. After removing the soft wood and drying the area, epoxy resin can be mixed with additives to create a filler to patch the voids. This not only repairs the plywood but also helps to prevent further deterioration.
Overall, epoxy resin is an ideal coating for plywood boat floors due to its strong adhesive properties, flexibility, and waterproofing capabilities. With proper preparation and application, it can help create a durable, watertight surface that will protect the plywood from deterioration for many years.
Don's Fate: Surviving the Boys in the Boat
You may want to see also
Polyester resin is not as waterproof as epoxy
When it comes to waterproofing plywood for boat floors, there are a few key considerations to keep in mind. Firstly, it's important to select the appropriate type of plywood, such as marine-grade plywood or exterior-grade plywood. Additionally, treating the plywood with a suitable resin is crucial to ensure its durability and longevity. While both polyester resin and epoxy resin can be used for this purpose, it's important to understand their differences.
Polyester resin is widely used and accounts for approximately 75% of the resin market in the UK. One of its primary advantages is its excellent mechanical and chemical stability, coupled with a low cost. Polyester resin is often favoured for large projects due to its ease of use and the fact that it cures with a surface tack, eliminating the need for sanding between layers. Additionally, the cure time of polyester resin can be adjusted by varying the amount of MEKP catalyst added. However, one of its drawbacks is that it has a strong odour due to the presence of styrene, necessitating proper ventilation and safety precautions when working with this resin.
On the other hand, epoxy resin stands out for its superior bonding strength and moisture resistance. It is highly adhesive and durable, making it a preferred choice for high-performance and lightweight parts. Epoxy resin is commonly used in aircraft components, boat building, and industrial and commercial flooring. When paired with carbon fibre, it creates exceptionally strong, rigid, and lightweight structures. Additionally, epoxy resin has a longer shelf life than polyester resin and typically lasts at least a year when stored properly.
While polyester resin is a popular and cost-effective choice for many applications, it is important to recognise that it is not as waterproof as epoxy resin. Polyester resin is more water-permeable, allowing more water to pass through over time. This makes epoxy resin a better choice for applications where moisture resistance is a critical factor, such as boat floors.
When deciding between polyester and epoxy resin for waterproofing plywood boat floors, it is essential to consider the specific requirements of your project. While polyester resin offers ease of use and cost-effectiveness, epoxy resin provides superior waterproofing capabilities and bonding strength. Therefore, if you are seeking a long-lasting and highly durable solution for your boat floor, epoxy resin is the more suitable option.
Boat Towing: Am I Covered by My Car Insurance?
You may want to see also
Plywood should be sealed before fibreglassing
When building a boat floor, it is important to consider the type of plywood and treatment that will be used. While some recommend using marine-grade plywood for boat floors, others suggest that any type of plywood can be used as long as it is properly coated and installed. One key consideration is to use epoxy resin to seal the plywood before fibreglassing, as it soaks into and adheres to the wood better than polyester resin, creating a stronger bond. Polyester resin is also not as waterproof as epoxy and can cause delamination when dry.
Before fibreglassing, it is essential to seal the plywood with epoxy resin to ensure a strong and long-lasting bond. This process involves coating the wood with a layer of epoxy resin, allowing it to soak in and cure, and then scuff sanding before applying the fibreglass. The epoxy resin acts as a barrier, protecting the wood from moisture and rot. It also improves the adhesion of the fibreglass to the plywood, creating a stronger and more durable boat floor.
There are a few methods for sealing plywood with epoxy resin. One suggestion is to apply a coat of epoxy resin to the wood, followed by a layer of fibreglass cloth, and then another coat of epoxy resin. Sanding between coats can also improve the smoothness of the final surface. Another method is to soft pad the plywood with 80-grit sandpaper, coat it with resin, let it cure, and then sand again before fibreglassing. This process ensures that the wood soaks up the resin, creating a strong chemical bond.
The type of fibreglass cloth used can also vary depending on the application. For boat floors, it is essential to use a cloth that provides puncture resistance and controls checking, such as 6 oz or 18 oz woven roving. The cloth should be applied to both the top and bottom sides of the plywood to protect against moisture and provide abrasion resistance. After the final layer of epoxy has cured, the surface can be sanded smooth and painted with a polyurethane paint for added protection.
Overall, sealing plywood with epoxy resin before fibreglassing is a crucial step in ensuring the durability and longevity of a boat floor. By following the proper procedures and allowing adequate curing time, a strong and watertight bond can be achieved, resulting in a high-quality boat construction.
The Nehru Trophy: A Boat Race Like No Other
You may want to see also
Marine plywood is not waterproof or rot-proof
Marine plywood should be CCA treated to protect against rot. CCA-treated plywood is designed to deprive wood-destroying organisms of the four components needed for them to survive. The CCA-treating process robs the organisms of the plywood panels as a food source. The CCA process chemically alters the wood, making it insoluble.
Even if you completely encapsulate the plywood, all wood products have an inherent moisture content. Thicker plywood will be stiffer, with more veneers providing more stiffness. 3/8" is typically 3-ply, 1/2" is typically 4 or 5-ply, and 3/4" is typically 5 or 7-ply.
If you are looking for strength, 8 or 10oz fiberglass is not going to provide much. If you use 3/8" marine-grade plywood, use 18oz woven roving over 3/4oz mat. The mat gives stiffness, and the roving provides strength.
For a stronger bond between the fiberglass and the plywood, a 'wet on wet' chemical bond is better than a sanded bond. You can achieve this by first coating the wood with resin and allowing it to cure, then scuff sanding and applying the glass. This process allows the wood to soak up resin and creates a better bond surface for the glass.
If you are going to seal the plywood with resin, epoxy resin is the only thing you should use. Polyester resin is not waterproof and will jump off the plywood as soon as it freezes in the winter. A slow-setting epoxy resin will take 8-12 hours to set, giving it time to soak in.
Hell's Canyon Jet Boat Ride: Packing Essentials
You may want to see also
Frequently asked questions
Marine-grade plywood is the best option for boat flooring as it is specifically designed for this purpose. However, if you are on a budget, exterior-grade plywood such as CDX or pressure-treated plywood can also be used.
Yes, it is important to seal the plywood with a waterproof coating such as epoxy resin or fiberglass resin to prevent rot and ensure a long-lasting floor.
The thickness of the plywood will depend on the size and structure of your boat. For smaller boats, 1/2-inch or 3/8-inch plywood may be sufficient, while larger boats may require 3/4-inch or thicker plywood.
Epoxy resin is generally recommended over polyester fiberglass resin as it soaks into the wood better and provides a stronger bond. However, fiberglass resin is also a common choice and can be effective if applied correctly.
This is a matter of personal preference. Carpet can provide a non-slip surface and improve the aesthetics of your boat, but it may also retain moisture and require more maintenance. Other options include paint with sand grit or specialized boat flooring products.