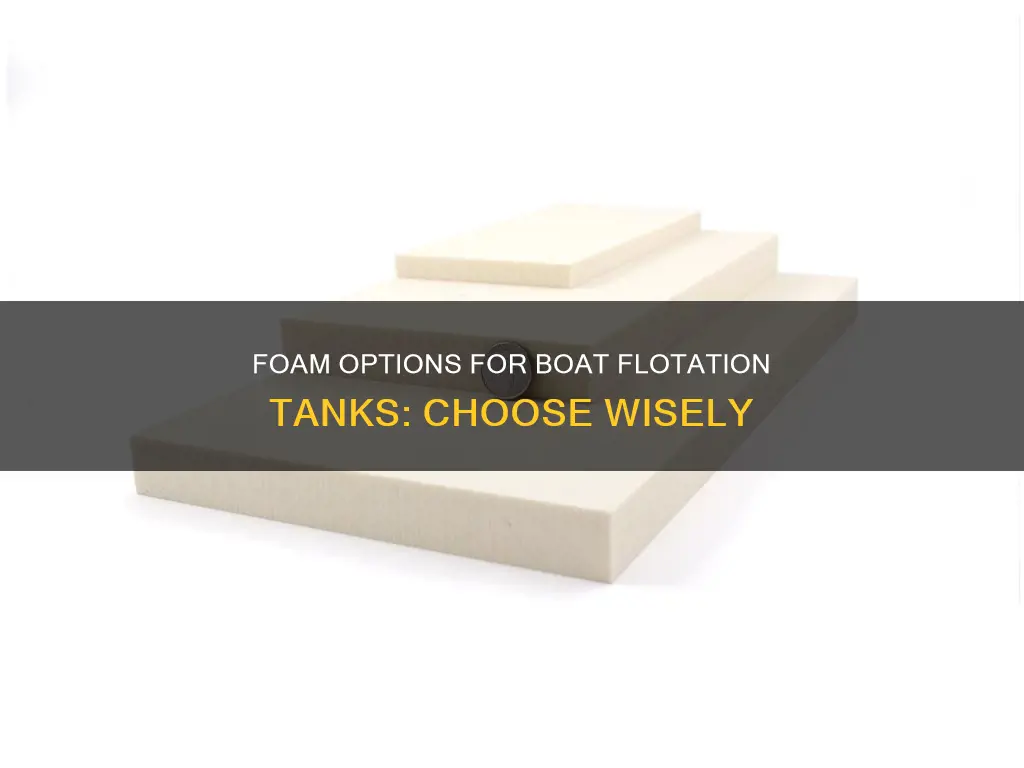
Boat flotation tanks are a crucial safety feature, ensuring that a boat can stay afloat even if it is flooded, swamped, or capsized. When it comes to choosing the right foam for your boat's flotation tank, there are several factors to consider. Firstly, it is important to select a foam that is specifically designed for marine use, as this will ensure that it can withstand the unique challenges of the marine environment, such as water absorption, resistance to fuel, and buoyancy. Closed-cell foam, for example, is a popular choice due to its ability to resist moisture intrusion and absorb less water in the event of a leak. Polyurethane foams are also a common choice for boat flotation tanks, as they are resistant to polyester resins used in the fiberglass process and are approved by organizations such as the US Coast Guard. Other factors to consider when choosing a foam include density, cost, and flammability, as you will want to select a foam that is safe, durable, and within your budget.
Characteristics | Values |
---|---|
Type | Closed-cell foam |
Material | Polyurethane |
Density | 2 lb or 6 lb |
Volume | 2-quart or 2-gallon kits |
Expansion Rate | Expands to 20-25 times its original volume |
Buoyancy | 60 pounds of "dead weight" per cubic foot of polyurethane |
Resistance | Resistant to polyester resins, fuel, oil, and solvents |
Flammability | Self-extinguishing |
What You'll Learn
Coast Guard-approved foam
When selecting foam for a boat flotation tank, it is important to ensure that the foam is Coast Guard-approved. Coast Guard-approved foams undergo rigorous testing to guarantee buoyancy in water. These foams are specifically tested for water absorption, resistance to fuel, fuel vapour, bilge cleaner, and oil.
One Coast Guard-approved foam option is the Versi-Foam® standard foam, which is found in System I, System 15, and System 50. This foam meets the requirements set by the Code of Federal Regulations and is resistant to polyester resins used in the fibreglass process. Versi-Foam® is a popular choice for the manufacture and repair of boats and other marine vessels. It is credited for keeping boats afloat during accidents and providing added strength to the vessel.
Another option for Coast Guard-approved foam is the Bio-Renew Flotation Foam 2.2 pcf, developed and manufactured by Empire Foam Solutions. This foam is self-extinguishing, meaning it will smoke and burn but will not catch fire. It also has excellent buoyancy and a solid structure, making it a lightweight foam solution for marine applications.
When choosing a Coast Guard-approved foam, it is important to consider factors such as buoyancy, density, cost, and flammability. These foams are designed to meet strict safety standards and provide reliable flotation for boats and other marine vessels.
In addition to Coast Guard-approved foams, there are also throwable flotation cushions available that are approved by the US Coast Guard. These cushions are designed to be easily thrown during emergency situations and can provide crucial rescue flotation. They are typically made of durable nylon fabric with flotation foam, ensuring they stay afloat during emergencies.
Essential Equipment Requirements for Coast Guard-Inspected Boats
You may want to see also
Buoyancy
Coast Guard-approved foams undergo rigorous testing to guarantee they stay buoyant in water and resist water absorption. For example, the Coast Guard tests foam to ensure it doesn't absorb water over a certain period, while some closed-cell foams are engineered to be submerged indefinitely without absorbing water. This is an important consideration, as continuous water submersion can eventually lead to a loss of buoyancy over time.
Density is another key factor, referring to the weight of the foam per cubic foot of material. High-density foam has a higher compressive strength, making it better for structural rigidity and supporting heavy loads. The higher the density, the stronger your vessel will be. For instance, a 2-pound density foam may be suitable for filling non-structural voids and providing buoyancy, while a 6-pound density foam is ideal for filling cavities to support heavy loads.
When selecting a flotation foam, longevity is also important. Some foams may become waterlogged over time, requiring replacement. However, some foams are formulated to last indefinitely and not become waterlogged, saving you the hassle of future replacements.
Cost is also a significant consideration when choosing a flotation foam. Prices can vary depending on the type of foam and the amount required for your project. It is essential to get quotes from different suppliers and compare them to find the most cost-effective option. Additionally, consider the long-term savings by investing in high-quality flotation foam that reduces the overall cost of repairs in the future.
Understanding Boat Sides: Bow and Stern Nomenclature
You may want to see also
Density
High-density foam has a higher compressive strength, which is ideal for structural rigidity and supporting heavy loads. This means that a higher density foam will make for a stronger boat. For example, a 6 lb density foam can support heavy loads in cavities, while a 2 lb density foam is perfect for filling non-structural voids to provide buoyancy.
The density of the foam you choose will depend on the specific requirements of your boat. If you require extreme structural strength, some flotation foams can be formulated to much higher densities than the standard 2 lb and 6 lb options.
It's worth noting that the density of the foam also affects its expansion rate and volume. A 2 lb density foam will typically expand to 20-25 times its original volume, while a 6 lb density foam will expand less. Therefore, you will need a larger volume of 6 lb density foam to fill the same space as a 2 lb density foam.
When selecting a flotation foam, it is essential to consider not only the density but also other factors such as buoyancy, cost, flammability, and longevity. However, density plays a key role in the overall performance and strength of your boat's flotation system.
Launching Large Vessels: A Comprehensive Guide to Success
You may want to see also
Cost
The cost of foam for a boat flotation tank varies depending on the type, quantity, and supplier of the foam. Here is a breakdown of the costs mentioned in different sources:
AeroMarine Products:
- 2-pound density polyurethane pour foam, which is suitable for boats, kayaks, and canoes, is available in various kit sizes:
- 1/2-gallon kit
- 2-gallon kit priced at $124.99
- 10-gallon kit
- 110-gallon kit priced at $5,717.00
Amazon:
TotalBoat 2-part polyurethane 2-pound density flotation foam, 2-gallon kit priced at $124.99
Empire Foam Solutions:
Coast Guard-approved, fire-resistant, closed-cell 2.2-pound per cubic foot (pcf) Bio-Renew flotation foam is priced per cubic foot of your project.
It is important to note that the prices mentioned may not be the most recent, and they can vary based on different factors, such as the quantity purchased, market demand, and supplier. It is always recommended to contact the suppliers directly or visit their websites for the most accurate and up-to-date pricing information.
How to Prepare Your Boat for Dragon Slaying
You may want to see also
Installation
To install flotation foam in your boat, you will first need to calculate how much foam you require. This will depend on the size of your boat and the weight of the materials used in its construction. For example, a 16-foot fiberglass skiff with a 50-horsepower outboard motor will need about six cubic feet of flotation foam to keep it afloat.
Once you have calculated the volume of foam required, you can purchase it in kit form. There are various suppliers of marine-grade flotation foam, such as AeroMarine, TotalBoat, and VersiFoam Systems. These kits are typically available in different volumes, such as half-gallon, two-gallon, or ten-gallon kits, and in different densities, such as two-pound or six-pound density foam. The density of the foam you choose will depend on the weight of the boat you need to support.
When you are ready to install the foam, you will need to follow the instructions provided with your kit. Typically, this will involve mixing the resin and activator in a specific ratio, usually 1:1, and then pouring the mixture into the cavities in your boat. The foam will then expand to fill the cavities, providing buoyancy and added strength to the vessel. It is important to work at an optimal temperature, usually around 75-80°F, to ensure the best yield and cure/working times.
After pouring the foam, you will need to allow it to cure fully. This typically takes about five minutes, but it is important to refer to the specific instructions provided with your kit, as different products may have different curing times. Once cured, the foam can be levelled and trimmed if necessary. Finally, you should paint or fibreglass over the foam to seal it and prevent any water absorption.
Removing Mildew from Boat Lift Covers: Effective Strategies
You may want to see also