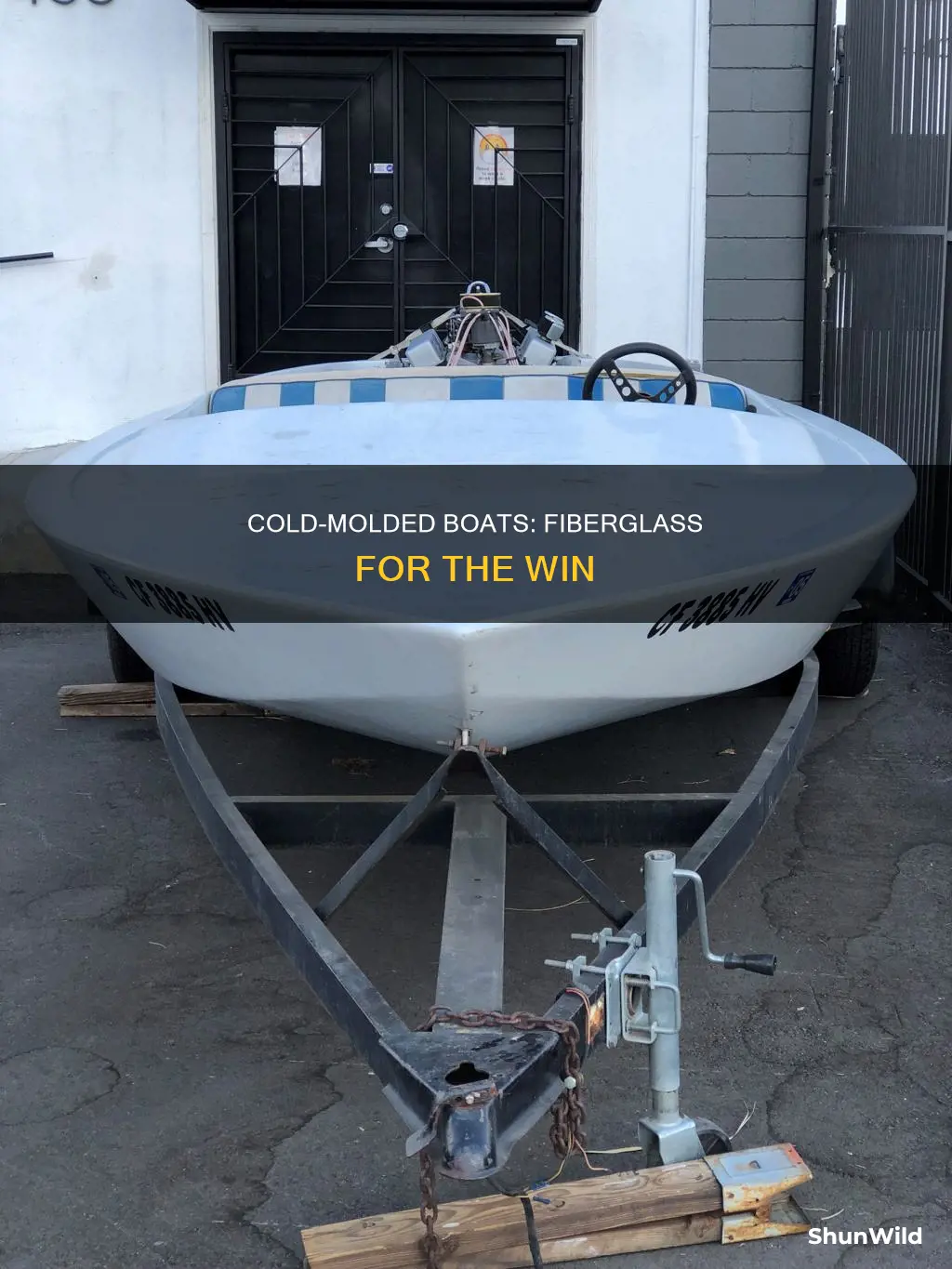
Cold-molded boats are constructed by laminating layers of wood or wood planks over a jig, with the stringers usually made of fir and the planking of Okoume plywood. This method can also be used with other materials, such as composites. Cold-molded boats are known for their strength, lightweight, and watertight qualities. They have excellent strength-to-weight ratios, flexibility in design, and considerable weight savings over solid glass boats. However, they may require more maintenance and have higher insurance costs compared to fiberglass boats. The choice between cold-molded and fiberglass boats depends on various factors, including performance, cost, and the level of customization desired.
What You'll Learn
Cold-moulded boats are stronger, lighter and stiffer than traditional fibreglass boats
Cold-moulded boats are superior to traditional fibreglass boats in several ways. Firstly, they are stronger and more flexible. The cold-moulding process involves laminating layers of wood or wood planks, typically using fir stringers and Okoume plywood, to create a sturdy and durable hull. This construction method results in a boat that is not only stronger but also lighter than a traditional fibreglass boat. The lightweight nature of cold-moulded boats is due to the use of wood, which has a higher strength-to-weight ratio than fibreglass.
Additionally, cold-moulded boats offer improved performance and customisation options. The reduced weight of cold-moulded boats leads to better performance on the water, as less fuel is required to propel a lighter boat. This makes cold-moulded boats more fuel-efficient and cost-effective in the long run. Furthermore, the absence of a mould in the construction process allows for greater flexibility in design. Builders can easily adapt to customer requests for changes in size or appearance without the constraints of a mould.
Another advantage of cold-moulded boats is their quietness and comfort. Fibreglass is a stiff material that readily transfers noise and vibration. In contrast, the wood used in cold-moulded boats acts as an insulator, reducing the amount of noise and vibration experienced by passengers. This makes for a more pleasant and comfortable boating experience, especially over extended periods.
Lastly, cold-moulded boats are known for their excellent craftsmanship and attention to detail. Many custom Carolina sportfishing yachts and high-end cruisers are built using the cold-moulding technique. Despite the time-consuming and expensive nature of this construction method, the resulting boats are of exceptional quality and are often considered superior to those built using more modern techniques.
In summary, cold-moulded boats offer several advantages over traditional fibreglass boats. They are stronger, lighter, and more flexible, resulting in improved performance and customisation options. The use of wood provides insulation from noise and vibration, enhancing the overall boating experience. Additionally, the craftsmanship and attention to detail inherent in the cold-moulding process result in boats of exceptional quality.
Malibu Boat Company: Ownership and Leadership
You may want to see also
Cold-moulded boats are quieter and feel better
Cold-moulded boats are constructed by laminating and encapsulating layers of wood or wood planks in epoxy resin, and then reinforcing the outer hull with layers of fibreglass. This construction method results in boats that are quieter and have a better "feel" compared to traditional fibreglass boats.
The insulating quality of wood means that cold-moulded boats do not transfer noise or vibration as much as boats made from stiffer, denser materials like fibreglass. John Bayliss, a boatbuilder from North Carolina, asserts that cold-moulded boats are "quieter and feel better". He adds that they are also very strong, lightweight and watertight.
Ritchie Howell, another boatbuilder, agrees that cold-moulded boats are superior to fibreglass boats in terms of sound and vibration. He notes that fibreglass boats resonate a different sound and have a buzz to them. In contrast, cold-moulded boats are quieter because they use wood, which is not as stiff or dense as fibreglass, and thus has insulating qualities.
The use of wood in cold-moulded boats also contributes to their strength and lightweight nature. Boatbuilder Sunny Briggs claims that a cold-moulded boat is "stronger than plank-on-frame". Additionally, cold-moulded boats have an excellent strength-to-weight ratio, which is a crucial factor in boat performance.
The construction process of cold-moulded boats also offers advantages over traditional fibreglass boats. Unlike fibreglass boats, cold-moulded boats do not require a mould, which provides flexibility in the building process and allows for easier customisation to meet customer demands.
Boat Mechanics: Skills, Challenges, and a Life at Sea
You may want to see also
Cold-moulded boats have excellent strength-to-weight ratios
Cold-moulded boats are known for their excellent strength-to-weight ratios. This is achieved through the use of composite materials and a plywood hull, which results in a lightweight yet sturdy vessel. The strength-to-weight ratio is a crucial factor in boat building, as it directly impacts the performance and efficiency of the boat.
The cold-moulded construction process involves laminating layers of wood or wood planks over a pre-fabricated jig to create the boat's hull. The wood is typically encapsulated in fibreglass and epoxy resin for added strength and protection. This method allows boat builders to create a structure that is both strong and lightweight, outperforming traditional fibreglass boats in terms of performance.
The flexibility of the cold-moulding technique is another advantage. Without the need for expensive moulds, boat builders can easily adapt to customer requirements, whether it's a different look or a larger size. This adaptability, combined with the superior strength-to-weight ratio, makes cold-moulded boats a popular choice for those seeking high-performance vessels.
Additionally, cold-moulded boats are known for their quietness and overall better feel on the water. The use of wood in the construction contributes to this, as wood is not as stiff or dense as other materials, resulting in improved insulation against noise and vibration.
While cold-moulded boats offer excellent strength-to-weight ratios, it's important to consider the maintenance and durability aspects as well. Wooden boats require proper maintenance to prevent rot and ensure the longevity of the vessel. Modern cold-moulded boats often encapsulate the wood in epoxy to slow down the rot process and protect the structure.
Boat Insurance: Animal Damage Coverage Explained
You may want to see also
Cold-moulded boats are more flexible
The flexibility of cold-moulded boats is a huge benefit, according to Ricky Scarborough Jr., a boatbuilder from North Carolina. He explains that the lack of a mould means that boatbuilders can adapt to the specific needs and wants of their customers, whether that's a different look or a larger size. This adaptability is further emphasised by Randy Ramsey, another boatbuilder, who highlights the financial benefits of not having to invest in expensive moulds.
The process of cold moulding involves laminating layers of wood or wood planks to create the hull of the boat. The wood is usually fir or Okoume plywood, and the hull is built upside down on a jig, which is then removed. The cold-moulded method can also be used with other materials, such as composites. However, some boatbuilders, like John Bayliss, prefer to use wood as it creates a boat that is strong, lightweight, and watertight.
The flexibility of cold-moulded boats extends beyond the building process and into the water. Cold-moulded boats have an excellent strength-to-weight ratio, which means they are lighter and more fuel-efficient than traditional moulded boats. This is because the wood used in cold-moulded construction is less dense and stiff than the materials used in moulded boats, such as fiberglass. As a result, cold-moulded boats have better performance and can be more fuel-efficient.
Repairing Leaks on a Vintage Plywood Boat
You may want to see also
Cold-moulded boats are stronger than plank-on-frame boats
Cold-moulding is a flexible process, allowing boat builders to adapt to customer needs without the need for costly moulds. The process is also highly customisable, with builders able to choose from a range of materials, including wood, composites, and epoxy resins.
The strength of a cold-moulded boat comes from the multiple layers of wood veneers glued and shaped over a jig, forming a one-piece structure. The veneers are often saturated with epoxy, creating a rot-resistant and watertight boat. The epoxy also fills in any gaps between the wood layers, adding to the overall strength of the boat.
Cold-moulded boats are also known for their quietness and lightweight construction. The use of wood in the construction provides insulation against noise, thermal changes, and vibrations. The lightweight nature of cold-moulded boats can also lead to better performance and fuel efficiency.
While cold-moulded boats offer superior strength, it is important to note that they require more maintenance than traditional fiberglass boats. Proper sealing and regular painting are necessary to prevent water damage and rot.
In summary, cold-moulded boats offer exceptional strength, customisability, and performance due to their unique construction process and the materials used. Their lightweight and quiet nature, combined with their strength, makes them a popular choice for custom boat builders and customers seeking a high-quality vessel.
Fresh Off the Boat: Foxtel Schedule and Viewing Options
You may want to see also
Frequently asked questions
Cold mold fiberglass is a boat-building technique where a wood boat is encapsulated in fiberglass. The hull is built by laminating layers of wood or plywood. The wood is then covered in fiberglass and resin to create a stronger monocoque structure.
Cold mold fiberglass boats are strong, lightweight, and watertight. They are also flexible, allowing for changes to be made more easily than with a mold. They have an excellent strength-to-weight ratio.
Cold mold fiberglass boats can be time-consuming and expensive to build. They require more maintenance than fiberglass boats, and insurance can be harder to obtain. Water can get into the wood, leading to rot.
The stringers are usually fir, and the planking is often Okoume plywood. The wood can also be cedar, juniper, or Douglas fir, depending on the desired characteristics of the hull. Epoxy resin is used to glue the veneers together, and fiberglass and resin are applied for added strength.
Cold mold fiberglass boats can last for decades if properly maintained. However, they require more maintenance than fiberglass boats, and water penetration must be avoided to prevent rot.