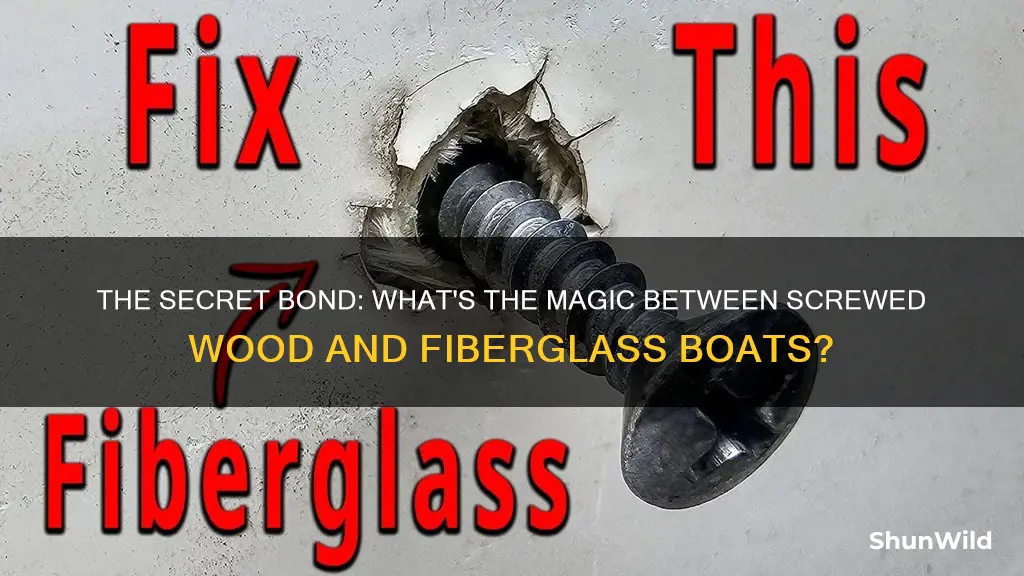
When it comes to the construction of a fiberglass boat, there are several key components that come together to create a sturdy and durable vessel. One crucial element that often goes unnoticed is the material that acts as a bridge between the screwed-on wood and the fiberglass. This intermediate layer plays a vital role in ensuring the structural integrity of the boat, providing a seamless transition between the two materials and enhancing the overall performance and longevity of the vessel. Understanding the specific requirements and properties of this material is essential for boat builders and enthusiasts alike.
What You'll Learn
- Fasteners: Screws, bolts, and rivets secure wood and fiberglass
- Adhesives: Epoxy and wood glue bond wood and fiberglass
- Sealing: Caulking and tape prevent water infiltration
- Reinforcement: Carbon fiber and Kevlar strengthen boat structure
- Finishing: Sanding and painting enhance aesthetics and durability
Fasteners: Screws, bolts, and rivets secure wood and fiberglass
When it comes to joining wood and fiberglass in a boat construction, the choice of fasteners is crucial for ensuring a strong and durable bond. Screws, bolts, and rivets are the primary fasteners used in this context, each offering unique advantages and considerations.
Screws are a popular choice for securing wood to fiberglass. They provide a strong mechanical grip due to their self-tapping threads, which create a tight fit in the wood. Wood screws are typically made with a sharp point and a coarse thread pattern, allowing them to cut into the wood and create a secure anchor. When using screws, it's essential to pre-drill holes to prevent the wood from splitting. The screw's head should be countersunk to ensure a flush surface, which is especially important in boat construction where aesthetics and water resistance are key.
Bolts, on the other hand, offer a more permanent solution. They are often used in conjunction with nuts and washers to create a tight bond. Bolts provide excellent shear strength and can be tightened to precise specifications. In boat building, bolts are commonly used for structural joints, especially when a strong, rigid connection is required. The use of washers between the bolt and the fiberglass surface can help distribute the load evenly, preventing damage to the material.
Rivets are another traditional fastener used in marine applications. They are inserted through pre-drilled holes in both the wood and fiberglass, and then the rivet head is typically formed or crushed to create a permanent joint. Rivets provide a strong bond and are resistant to vibration and shock, making them ideal for critical load-bearing areas. However, they require specialized tools for installation and may not be as accessible as screws or bolts.
The choice between screws, bolts, and rivets depends on various factors, including the specific application, load requirements, and aesthetic considerations. For example, in lightweight boat construction, screws might be preferred for their ease of installation and minimal intrusion into the fiberglass surface. In contrast, bolts and rivets could be more suitable for heavy-duty structural connections. Proper preparation of the materials, including cleaning and priming, is essential to ensure optimal adhesion and the longevity of the fastener.
Repair Boat Shoe Soles: A Step-by-Step Guide
You may want to see also
Adhesives: Epoxy and wood glue bond wood and fiberglass
When it comes to bonding wood and fiberglass in a boat construction, the choice of adhesive is crucial for ensuring a strong and durable bond. Two popular options that are commonly used in this application are epoxy and wood glue.
Epoxy is a versatile and powerful adhesive known for its exceptional bonding strength. It creates a strong, flexible bond between materials, making it ideal for bonding wood to fiberglass. The process typically involves mixing a two-part epoxy resin and hardener, which then sets to form a tough, durable bond. This type of adhesive is highly resistant to water and chemicals, making it suitable for marine environments. When using epoxy, it's important to follow the manufacturer's instructions for mixing ratios and application techniques to ensure optimal results.
Wood glue, on the other hand, is a type of adhesive specifically designed for bonding wood. While it may not provide the same level of strength as epoxy, wood glue is easy to use and can create a strong bond when applied correctly. It is particularly useful for smaller boat components or when a more flexible bond is required. Wood glue is water-based and dries quickly, making it convenient for various bonding tasks. However, it is important to note that wood glue may not be as resistant to water and chemicals as epoxy, so it is generally recommended for non-structural applications or when bonding wood to other wood materials.
In the context of a boat, where structural integrity is essential, epoxy is often the preferred choice. It provides a robust and long-lasting bond, ensuring that the wood and fiberglass components remain securely attached. The use of epoxy can be especially critical in areas exposed to moisture and potential impact, such as the hull or deck. By carefully applying epoxy, boat builders can create a seamless and strong connection between wood and fiberglass, contributing to the overall safety and performance of the vessel.
Additionally, when bonding wood to fiberglass, it is crucial to prepare the surfaces properly. This includes cleaning the surfaces to remove any dirt or contaminants and ensuring that the wood is smooth and free of any protruding fibers. Proper surface preparation enhances the adhesion of the adhesive and promotes a stronger bond.
In summary, epoxy and wood glue are both viable options for bonding wood and fiberglass in boat construction. Epoxy offers superior strength and durability, making it ideal for structural applications, while wood glue is convenient for smaller tasks or when a more flexible bond is desired. Understanding the properties and limitations of each adhesive is key to making an informed decision and ensuring a successful bond in marine environments.
Selling a Boat Without a Title: What You Need to Know
You may want to see also
Sealing: Caulking and tape prevent water infiltration
When it comes to sealing the gap between screwed-on wood and fiberglass components on a boat, the primary goal is to prevent water infiltration, which can lead to structural damage and compromise the boat's integrity. This is a critical step in boat maintenance, especially for those with older vessels or those that are frequently exposed to harsh marine environments.
Caulking: One of the most traditional and effective methods of sealing this gap is by using caulking. Caulking is a process where a special sealing compound, typically a putty-like material, is applied to the gap. This compound is designed to be flexible, allowing it to expand and contract with the movement of the boat, while also providing a strong, waterproof barrier. The process involves cleaning the surfaces, applying a primer to ensure better adhesion, and then carefully inserting the caulking material into the gap. Once set, it forms a durable seal that can withstand the elements. It's important to choose the right type of caulking for the specific application; marine-grade caulking is ideal for this purpose due to its resistance to water and UV degradation.
Sealing Tape: Another effective method is the use of specialized sealing tapes. These tapes are designed to provide a quick and easy solution for sealing gaps. They are typically made from a combination of adhesive-backed materials and are engineered to be flexible and durable. The process involves cleaning the surfaces, applying the tape directly to the gap, and ensuring a firm press to create a tight seal. Sealing tapes are particularly useful for smaller gaps and can be a convenient option for DIY boat owners. Modern sealing tapes often include additional features like UV resistance and flexibility to accommodate the unique challenges of boat construction.
Both caulking and sealing tape offer effective solutions for preventing water infiltration. Caulking provides a more traditional, long-lasting seal, while sealing tape offers a quick and convenient alternative. The choice between the two often depends on the specific requirements of the boat, the size and location of the gap, and the level of DIY expertise available. It is always recommended to use materials specifically designed for marine environments to ensure the longevity and safety of the boat.
Repairing Vinyl Boat Tears: A Comprehensive Guide
You may want to see also
Reinforcement: Carbon fiber and Kevlar strengthen boat structure
Carbon fiber and Kevlar are two advanced materials that play a crucial role in reinforcing the structural integrity of boats, particularly when it comes to combining wood and fiberglass components. These materials are renowned for their exceptional strength-to-weight ratio, making them ideal for enhancing the performance and durability of marine vessels.
In the context of a boat's construction, carbon fiber and Kevlar are often utilized as composite materials. These composites are created by combining these high-performance fibers with a resin, typically an epoxy, to form a lightweight yet robust structure. When a boat's wooden frame is combined with a fiberglass hull, the carbon fiber and Kevlar reinforcement becomes essential. The wooden frame provides a sturdy foundation, while the fiberglass offers a smooth, durable exterior. However, the interface between these two materials can be susceptible to structural weaknesses.
Here's where carbon fiber and Kevlar come into play. These materials are strategically placed between the wooden frame and the fiberglass hull during the manufacturing process. Carbon fiber, known for its exceptional tensile strength, is an excellent choice for load-bearing applications. It can be woven into a fabric or formed into sheets, providing a strong and lightweight layer that reinforces the boat's structure. Kevlar, on the other hand, offers excellent impact resistance and is often used in combination with carbon fiber. Its high tensile strength and low weight make it ideal for creating a robust bond between the wood and fiberglass.
The process of integrating these materials involves careful design and application. Carbon fiber and Kevlar composites are often used to create structural panels that are then bonded to the wooden frame. These panels provide additional strength and stability, ensuring that the boat can withstand various stresses and loads. The composites are designed to complement the natural properties of wood and fiberglass, creating a harmonious and reinforced structure.
By utilizing carbon fiber and Kevlar, boat manufacturers can significantly improve the overall performance and longevity of their vessels. These materials contribute to a stronger, lighter, and more durable boat, ensuring a safer and more enjoyable marine experience. The reinforcement provided by these advanced composites is a testament to the continuous innovation in marine technology, allowing boats to push the boundaries of what is possible in terms of design and functionality.
Life on the Waves: A Day in the Life of a Crab Boat Deckhand
You may want to see also
Finishing: Sanding and painting enhance aesthetics and durability
The process of finishing a boat, especially one with a wooden and fiberglass construction, involves several steps to ensure a smooth and professional appearance. One of the critical aspects of this process is sanding and painting, which significantly enhances both the aesthetics and durability of the boat's surface.
Sanding is an essential step to achieve a smooth and even finish. It involves using various grits of sandpaper to remove any roughness, imperfections, or old paint. Start with a higher grit (e.g., 120-grit) to remove any visible scratches and imperfections. Gradually move to lower grits (e.g., 220-grit and 360-grit) to create a smooth surface. Pay close attention to curves and contours, as these areas require careful sanding to avoid creating a bumpy texture. After sanding, wipe away any dust with a tack cloth to ensure a clean surface for the next step.
Preparing the surface for painting is crucial. Begin by cleaning the sanded surface to remove any dust or debris. You can use a mild detergent mixed with water and a soft brush to ensure a thorough clean. Once dry, apply a suitable primer designed for marine environments. Primers help create an even base for the paint and improve adhesion. Follow the manufacturer's instructions for application and drying times.
Painting the boat requires careful selection of marine-grade paints and coatings. These specialized paints are designed to withstand the harsh marine environment, including UV rays, salt, and moisture. Choose a color that complements the boat's overall design and consider using a base coat and clear coat system for added protection and a high-gloss finish. Apply the paint in thin, even coats, allowing sufficient drying time between layers. Ensure proper ventilation during the painting process.
After painting, allow ample time for the paint to cure and harden. This process may take several days, depending on the type of paint used. Once cured, the boat's surface will be protected, and its appearance will be enhanced, creating a seamless transition between the wooden and fiberglass components. Regular maintenance and touch-ups will further ensure the boat's longevity and keep it looking its best.
Gronk's Boat: A Luxurious Seafaring Vessel
You may want to see also
Frequently asked questions
The most common material is a specialized epoxy-based adhesive. This type of adhesive is designed to bond wood and fiberglass effectively, providing a strong and durable connection. It is essential to use a high-quality epoxy that is specifically formulated for marine environments to ensure longevity and resistance to water and chemicals.
Proper surface preparation is crucial for a successful bond. Start by cleaning the surfaces to remove any dirt, grease, or old adhesive residue. Sand the wood and fiberglass gently to create a rough surface, which will provide better adhesion. Ensure that the surfaces are dry and free of any debris before applying the adhesive.
Yes, after applying the adhesive, it is essential to follow the manufacturer's instructions for curing time and post-application care. Typically, you will need to clamp the surfaces together to ensure proper bonding and then allow sufficient time for the adhesive to cure. Avoid any stress or pressure on the bonded area during the curing process to ensure a strong and long-lasting connection.