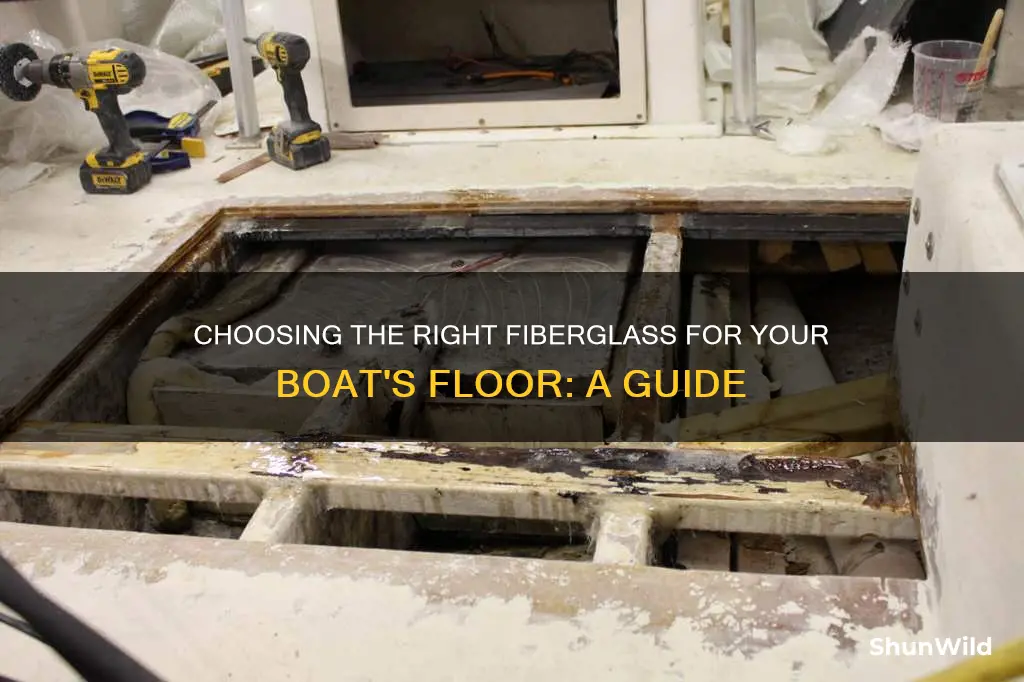
Fiberglass is a popular material for boat floors due to its durability, lightweight nature, and resistance to water damage. When choosing fiberglass for a boat floor, it's important to consider the specific requirements of your boat, such as the size, weight capacity, and intended use. There are several types of fiberglass available, including woven, chopped, and random fiber, each with its own unique properties and benefits. In this article, we'll explore the different types of fiberglass and their applications in boat flooring, as well as provide tips on how to select the right fiberglass for your boat.
What You'll Learn
- Fiberglass Types: Choose the right type for boat floor, considering strength, weight, and cost
- Reinforcement Techniques: Learn how to reinforce fiberglass for a sturdy boat floor
- Bonding Methods: Explore various bonding techniques for a strong and durable fiberglass floor
- Surface Preparation: Proper surface prep ensures a strong bond and a smooth finish
- Finishing Touches: Tips for finishing the fiberglass floor, including sealing and painting
Fiberglass Types: Choose the right type for boat floor, considering strength, weight, and cost
When it comes to choosing the right type of fiberglass for a boat floor, there are several factors to consider, including strength, weight, and cost. Fiberglass is a popular choice for boat construction due to its durability, lightweight nature, and ability to be molded into various shapes. Here's a breakdown of the different types of fiberglass and their suitability for boat floors:
- E-Glass (E-Glass Fiberglass): This is the most common and cost-effective type of fiberglass used in boat construction. E-Glass is known for its excellent balance of strength and affordability. It is composed of a blend of glass fibers and a resin system, providing structural integrity without adding excessive weight. E-Glass is ideal for boat floors as it offers a good level of impact resistance and can withstand the rigors of marine environments. Its low cost makes it a popular choice for recreational boats and smaller vessels.
- S-Glass (Stratum Glass): S-Glass is a high-strength variant of fiberglass, offering superior performance in terms of tensile strength and stiffness. It is composed of long, thin glass fibers, which provide exceptional structural integrity. While S-Glass is stronger, it is also heavier and more expensive than E-Glass. This type of fiberglass is often used in high-performance boats and racing vessels where weight reduction and maximum strength are crucial. However, for most recreational boats, the additional cost and weight may not be justified.
- FRP (Fiberglass Reinforced Plastic): FRP is a composite material made by combining fiberglass with a plastic resin. It offers excellent strength-to-weight ratios and is highly resistant to corrosion and impact. FRP boat floors are known for their smooth and seamless finish, providing a comfortable and safe walking surface. This material is often used in high-end boats and those requiring precise structural requirements. While FRP can be more expensive, its durability and low maintenance make it a popular choice for luxury yachts and specialized vessels.
- Carbon Fiber: Carbon fiber is an advanced composite material known for its exceptional strength and lightweight properties. It is significantly stronger and stiffer than both E-Glass and S-Glass but is also the most expensive option. Carbon fiber boat floors offer unparalleled strength-to-weight ratios, making them ideal for high-performance racing boats or specialized applications where weight reduction is critical. However, the high cost and limited availability of carbon fiber may make it less practical for most recreational boat owners.
When selecting the appropriate fiberglass type for your boat floor, consider the specific requirements of your vessel. E-Glass provides a cost-effective solution with good strength, while S-Glass offers enhanced performance for those seeking maximum strength. FRP delivers a smooth finish and excellent durability, and carbon fiber is reserved for applications demanding the highest level of performance. Ultimately, the choice depends on your budget, desired performance, and the specific needs of your boat.
The SV Esper: A Boat's Unique Identity
You may want to see also
Reinforcement Techniques: Learn how to reinforce fiberglass for a sturdy boat floor
When it comes to reinforcing fiberglass for a boat floor, there are several techniques that can ensure a sturdy and durable structure. One of the primary methods is to use a combination of fiberglass cloth and resin to create a strong, lightweight layer. Start by laying a layer of fiberglass cloth, ensuring it is cut to fit the dimensions of your boat floor. This cloth should be carefully positioned to cover the entire area, paying attention to any curves or contours. Once the cloth is in place, apply a generous amount of epoxy resin, allowing it to penetrate the fibers. This initial layer of resin acts as a bonding agent, creating a strong foundation for further reinforcement.
After the first layer of resin has cured, it's time to add additional strength. Consider using a technique called 'strand mat' or 'glass mat' reinforcement. This involves laying a layer of fiberglass mat, which is a woven or non-woven fabric made of glass fibers, over the previously applied resin. The mat should be cut to size and positioned to cover the entire floor area, ensuring it overlaps the edges of the initial cloth layer. This additional layer adds tensile strength and makes the fiberglass more resistant to tearing or puncturing.
Another effective reinforcement technique is to incorporate carbon fiber or Kevlar cloth. These high-strength materials can be layered on top of the initial fiberglass cloth to provide exceptional structural integrity. Carbon fiber, in particular, offers excellent strength-to-weight ratios, making it ideal for areas that require maximum reinforcement. When using these advanced materials, ensure that they are properly secured and bonded to the existing fiberglass using additional layers of resin.
To further enhance the sturdiness of the boat floor, consider using a process called 'bidding' or 'lamination'. This technique involves creating a multi-layer structure by applying multiple coats of resin and fiberglass cloth. By building up the layers, you increase the overall thickness and strength of the floor. Bidding can be particularly useful for repairing or reinforcing existing fiberglass structures, as it provides a strong bond between layers.
Lastly, don't underestimate the power of proper preparation and surface treatment. Before applying any reinforcement, ensure that the fiberglass surface is clean, smooth, and free from any contaminants. Use a primer or a suitable surface preparation product to create a uniform base for the resin to adhere to. This step is crucial for the long-term success and durability of the reinforced fiberglass boat floor.
Mounting Transducers: Bass Boat Edition
You may want to see also
Bonding Methods: Explore various bonding techniques for a strong and durable fiberglass floor
When it comes to installing a fiberglass floor in your boat, ensuring a strong and durable bond is crucial for the long-term performance and safety of the vessel. The bonding process involves several key steps and techniques to achieve a seamless and robust connection between the fiberglass material and the underlying structure. Here's an exploration of various bonding methods to consider:
Resin-Based Adhesives: One of the most common and effective bonding techniques for fiberglass is the use of resin-based adhesives. These adhesives typically consist of a two-part system, with a resin and a hardener. The resin acts as a binder, while the hardener initiates the curing process, creating a strong chemical bond. Before application, ensure the surface is clean and free of any contaminants. Mix the resin and hardener according to the manufacturer's instructions, and apply it generously to the fiberglass floor and the underlying structure. Allow the adhesive to cure fully, following the recommended time before handling or applying additional layers. This method provides excellent strength and flexibility, making it ideal for boat floors that require movement and impact resistance.
Epoxy Resins: Epoxy resins are another popular choice for bonding fiberglass due to their exceptional bonding strength and resistance to chemicals and abrasion. Similar to resin-based adhesives, epoxy systems come in two parts, which need to be mixed and applied carefully. Prepare the surface by sanding and ensuring a rough texture for better adhesion. Apply the epoxy resin and hardener, following the manufacturer's guidelines for mixing ratios. Allow sufficient curing time, and consider using a primer to enhance bonding, especially if the fiberglass is new or has a smooth surface. Epoxy-bonded fiberglass floors offer excellent durability and can withstand the harsh marine environment.
Structural Bonding: For a more permanent and robust bond, structural bonding techniques can be employed. This method involves using specialized adhesives designed for structural applications. These adhesives are typically applied in layers, creating a sandwich effect between the fiberglass and the underlying structure. The bonding process may require heating or pressure to initiate curing. Structural bonding is ideal for heavy-duty applications and provides a strong, rigid connection. It is commonly used in boat manufacturing to attach floors to the hull, ensuring a solid foundation for the entire vessel.
Reinforcement with Fibers: To enhance the bonding process and overall strength, consider incorporating fiber reinforcements. Glass fiber mats or weaves can be applied over the adhesive layer before or after the bonding process. These fibers provide additional structural support and improve the load-bearing capacity of the fiberglass floor. Ensure proper alignment and coverage of the fiber reinforcement, and allow adequate curing time. This technique is particularly useful for repairing existing fiberglass floors or creating a more robust bond in high-stress areas.
When working with fiberglass bonding, it is essential to consider the specific requirements of your boat project. Factors such as load-bearing capacity, environmental conditions, and maintenance needs will influence the choice of bonding method. Proper surface preparation, accurate mixing of adhesives, and adherence to curing times are critical to achieving a successful and long-lasting bond.
Time to Retire Your Boat: Signs to Watch For
You may want to see also
Surface Preparation: Proper surface prep ensures a strong bond and a smooth finish
When preparing the boat floor for fiberglass installation, surface preparation is a critical step that cannot be overlooked. It ensures a strong bond between the fiberglass and the existing substrate, creating a durable and long-lasting finish. Here's a detailed guide on how to approach this essential process:
Cleaning and Degreasing: Begin by thoroughly cleaning the boat floor surface. Use a high-pressure washer or a powerful detergent to remove any dirt, grime, or old coatings. Pay extra attention to areas around the bilge, as these spots tend to accumulate more contaminants. Ensure that the surface is completely dry before proceeding.
Sanding and Abrazive Blasting: After cleaning, the surface needs to be roughened to provide a better bonding surface for the fiberglass. Use a power sander or an abrasive blaster to create a consistent texture. Start with a lower grit (e.g., 40-60) and gradually move to higher grits (80-120) for a smoother finish. Focus on the entire floor, ensuring an even application. This process helps to create a mechanical bond between the fiberglass and the substrate, enhancing the overall strength of the repair.
Filling and Repair: Inspect the boat floor for any holes, cracks, or imperfections. Fill these areas with a suitable marine-grade filler or putty. Allow it to cure according to the manufacturer's instructions. Once cured, sand the filled areas to create a seamless surface. This step is crucial to ensure that the final fiberglass layer adheres properly and provides a smooth, professional finish.
Priming (Optional): Depending on the manufacturer's recommendations and the type of fiberglass used, priming the prepared surface can be beneficial. Primers create a uniform base, improve adhesion, and provide a consistent color for the fiberglass. Apply the primer evenly, allowing sufficient drying time between coats. This step is especially useful when working with gelcoat or specialized fiberglass systems.
Final Inspection: Before applying the fiberglass, conduct a final inspection to ensure the surface is clean, dry, and free of any debris. Check for any remaining imperfections and address them accordingly. Proper surface preparation is the foundation for a successful fiberglass repair or installation, ensuring a strong bond, a smooth finish, and a long-lasting result.
Best Fiberglass for Repairing Boat Transoms: Expert Guide
You may want to see also
Finishing Touches: Tips for finishing the fiberglass floor, including sealing and painting
When it comes to finishing the fiberglass floor of your boat, there are several important steps to ensure a durable and aesthetically pleasing result. Here are some tips to guide you through the process:
Sealing the Fiberglass: Before applying any finish, it's crucial to seal the fiberglass to protect it from moisture and prevent damage. Start by cleaning the surface thoroughly to remove any dirt or debris. You can use a mild detergent and a soft brush for this task. Once clean, apply a suitable fiberglass sealer or epoxy resin. Follow the manufacturer's instructions for proper application techniques. This step is essential as it creates a barrier that safeguards the fiberglass from the elements, ensuring its longevity.
Sanding and Preparation: After the sealer has cured, it's time to sand the surface. Use fine-grit sandpaper (around 400-600 grit) to smooth out any imperfections and create a uniform texture. Start with a larger area and gradually work your way inwards to avoid scratching the edges. Ensure you wipe away any dust with a damp cloth to keep the surface clean. Proper sanding will provide a smooth base for the final finish.
Choosing the Right Paint: Selecting the appropriate paint is key to achieving a professional-looking floor. Consider using a marine-grade epoxy paint or a specialized boat floor paint. These paints are designed to withstand the harsh marine environment and provide excellent adhesion to fiberglass. Look for paints with UV resistance to maintain their color over time. Test the paint in a discreet area to ensure it blends well with the overall color scheme of your boat.
Application Techniques: When painting, use a high-quality brush or roller suitable for the chosen paint. Start with a thin coat, allowing it to dry completely before applying subsequent layers. Multiple thin coats will provide better coverage and a smoother finish compared to a single thick layer. Ensure you follow the paint manufacturer's guidelines for drying times and application rates. Proper painting techniques will result in a durable and visually appealing floor.
Final Touches and Maintenance: Once the paint is fully cured, inspect the floor for any touch-ups or additional sealing required. Consider adding non-slip tape or mats to improve traction and safety. Regular maintenance is essential; clean the floor with marine-safe cleaners and avoid harsh chemicals that could damage the finish. With proper care, your fiberglass boat floor will remain in excellent condition for years.
Exploring the Water Sport of Rowing and Its Nuances
You may want to see also
Frequently asked questions
For boat floors, a specialized type of fiberglass called "boat floor epoxy" or "gelcoat" is commonly used. This material is designed to be durable, lightweight, and resistant to water absorption, making it ideal for the demanding environment of a boat interior. It often comes in a smooth finish, providing a sleek and seamless surface.
Proper preparation is crucial for a successful installation. Start by thoroughly cleaning the existing boat floor to remove any dirt, grease, or old materials. Then, use a high-grit sandpaper to roughen the surface, ensuring the new fiberglass has a good adhesion base. Fill any holes or imperfections with a suitable filler and sand it smooth before applying the gelcoat.
While regular fiberglass can be used, it is not the most recommended choice for boat floors. Regular fiberglass is heavier and more prone to water absorption, which can lead to issues like delamination and structural damage over time. Boat floor epoxy, specifically formulated for this purpose, offers better performance and longevity.
Fiberglass boat floors provide several benefits. They are lightweight, reducing the overall weight of the boat, which can improve fuel efficiency. The material is also non-conductive, helping to prevent electrical issues. Additionally, fiberglass floors are easy to clean and maintain, and they can be customized with various colors and textures to match the boat's interior design.