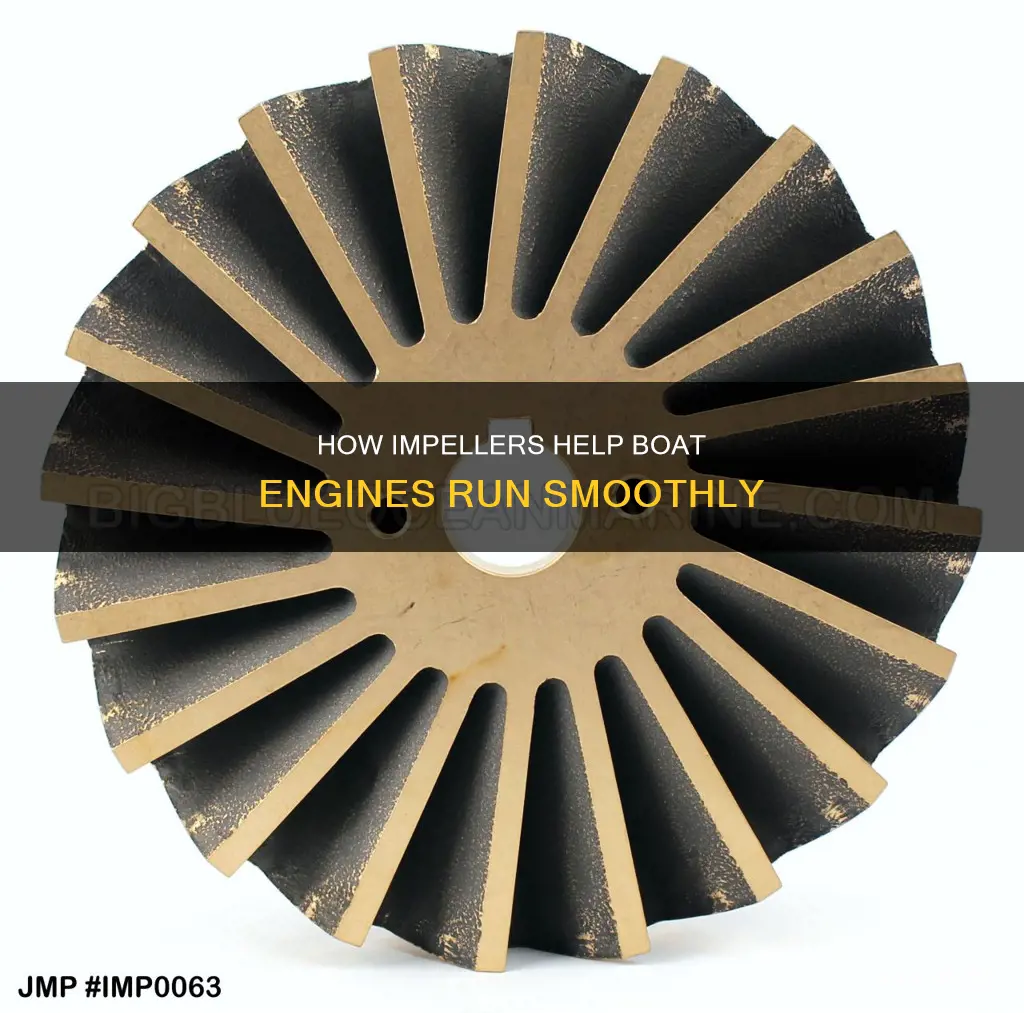
Boat impellers are a crucial component of a boat's engine cooling system. They are flexible rubber components with fins that rotate to pump raw water from outside the boat into the engine's cooling system, ensuring the engine operates at a safe temperature. Impellers are simple yet versatile, handling small debris and various fluids, including water and oil. While durable, they require regular maintenance and replacement as they are prone to wear and can fail catastrophically if neglected, leading to severe engine damage.
Characteristics | Values |
---|---|
Definition | An internal component of a water pump in boat engines |
Function | Pumps raw water from a lake or sea into the engine or heat exchanger for cooling purposes |
Composition | Rubber or nitrile |
Shape | Fan-shaped |
Speed | Proportional to the engine's RPM |
Location | In outboard engines or stern drives, or in sea water pumps |
Maintenance | Requires regular replacement (every 3-5 years) |
Importance | Vital for engine cooling and preventing engine damage |
Failure Consequences | Engine overheating, steam emission, engine seizure, or complete engine failure |
What You'll Learn
Impeller pumps are simple, versatile and self-priming
Impeller pumps are simple, versatile, and self-priming. They are used in a wide range of applications on boats, from outboard engines to pressure water systems. With only one moving part, the impeller itself, these pumps are easy to operate and maintain.
The impeller is a fan-shaped object, usually made of rubber or nitrile, that rotates within a concentric housing. As it spins, its vanes open to draw in water and then close to push it out, facilitating the cooling process of the engine. This simple mechanism allows impeller pumps to handle a variety of fluids, including water, oil, and other substances. They can even handle small debris without issue.
The versatility of impeller pumps is further demonstrated by their ability to be scaled up or down, depending on the application. A well-sealed impeller pump can push fluids to a significant height, making it suitable for a range of uses. Additionally, the pump's self-priming capability means it uses the fluid being pumped to lubricate the rubber impeller, ensuring smooth and efficient operation.
Despite their durability, impellers do require regular maintenance and replacement. This is because they play a crucial role in engine cooling, and a failed impeller can lead to catastrophic engine failure. By replacing the impeller regularly and following manufacturer recommendations, boat owners can ensure optimal performance and avoid costly repairs.
Creating Boat Paddles: Cardboard DIY Project
You may want to see also
Impeller maintenance and replacement
The impeller is a small but essential part of a boat engine. It is a component of the water pump, which is used to cool the engine. The impeller draws water into the water pump to increase the pressure in the motor, and it must be well-lubricated.
Maintenance
Impellers should be replaced regularly to prevent engine damage. They have a limited lifespan and are prone to cracking or breaking over time. Experts recommend replacing the impeller every three to five years, or every 200 hours of use. It is also a good idea to keep a spare impeller on board in case of sudden failure.
Replacement
To replace the impeller, first disconnect the shift rod and remove the two remaining bolts to drop the lower unit. Then, remove the four bolts around the water pump housing and take out the gasket to inspect the water pump. The impeller is located beneath the gasket. Remove and inspect the impeller, and if it is damaged, replace it with a new one. Grease the impeller key and place it back into position, then slide the new impeller down the drive shaft until it fits securely. Slide the impeller and water pump housing on top of the impeller, using soapy water as a lubricant. Finally, reinstall the lower unit onto the motor.
Launching a Pedal Boat: Easy Steps to Get Started
You may want to see also
Impeller failure and causes
Impellers are a crucial component of a boat's engine, and their failure can lead to significant issues. The impeller is responsible for pumping water into the engine for cooling purposes, and its malfunction can result in engine overheating, steam emission, seizure, or even complete engine failure. Therefore, it is essential to understand the causes of impeller failure to prevent these costly and potentially dangerous consequences.
One of the primary causes of impeller failure is the operating environment. If a boat is frequently used in sandy or muddy waters, the abrasive nature of sand particles can accelerate the wear and tear on the impeller's rubber veins. This can lead to reduced performance and, eventually, failure. Additionally, the age of the impeller plays a role in its durability. Over time, rubber can become brittle and dry rotted, making it more susceptible to failure, especially if the boat has been sitting idle for extended periods.
Another critical factor contributing to impeller failure is improper lubrication. Impellers rely on water to keep them lubricated and prevent damage. Running a boat without water flowing through the impeller, even for a short period, can cause the impeller to shred and require immediate replacement. Therefore, it is essential to ensure that the impeller is properly lubricated before operation and that water is always present during use.
To mitigate the risks associated with impeller failure, regular maintenance and replacement are essential. Boat owners should inspect and replace impellers seasonally or every few years, depending on usage. Additionally, when replacing an impeller, it is crucial to use suitable lubricants and follow the manufacturer's recommendations to ensure optimal performance and longevity.
By understanding the causes of impeller failure and implementing preventive measures, boat owners can avoid the costly repairs and potential safety hazards associated with impeller malfunction. Regular maintenance and timely replacements are crucial to ensuring the longevity and reliability of a boat's engine.
Breaking in a Boat Engine: Step-by-Step Guide
You may want to see also
Impeller pump applications
Flexible Impeller Pumps
Flexible impeller pumps are commonly used in outboard engines to pump cooling water through the engine. They are also found in many outdrive units and inboard engines of all sizes, where they drive coolant through the cooling system. These pumps are versatile and can handle anything from water to oil or waste. They are self-priming, using the pumped fluid for lubrication, and can push fluids 15 to 25 feet.
Engine Cooling
A key application of impeller pumps in boat engines is for engine cooling. Impellers pump raw water from outside the boat, through the engine's cooling system, and then expel it through the hull or exhaust. This process maintains the engine's temperature within safe limits, preventing overheating and potential engine seizure or failure.
Other Applications
Impeller pumps are also used in various other applications on a boat. These include macerator pumps, engine oil change systems, washdown pumps, live well aerators, ballast pumps for wake board boats, and pressure water systems.
Maintenance
Impeller pumps require periodic maintenance and replacement. It is recommended to replace the boat engine impeller every three to five years, as they wear out over time. It is crucial never to run the pump dry, as this can lead to disintegration. Lubrication with waterproof grease or manufacturer-approved lubricants is essential during replacement to ensure smooth operation and removability.
Sailing Adventures of Jennifer Connelly: A Boat Trip
You may want to see also
Impeller pump theory
The impeller's function is to convert mechanical energy from the motor to kinetic energy. This energy increase is what raises the fluid's pressure and flow rate. The motor rotates the impeller at high speeds, generating a centrifugal force that moves the fluid outwards. This creates a low-pressure area in the centre of the impeller, drawing in more fluid from the suction line. The continuous rotation of the impeller provides a smooth, even flow.
The impeller pump's simplicity is one of the reasons for its wide usage. It has only one moving part, making it versatile and able to handle small debris. It is self-priming, using the pumped fluid to lubricate the rubber impeller. The pump's housing, which surrounds the impeller, is usually made of plastic or cast bronze and plays a key role in creating the pumping action.
The impeller itself comes in several materials, with neoprene rubber being the most common for water-based fluids and nitrile rubber used for petroleum-based fluids. The choice of impeller type depends on the specific application, with various types suited to different fluid viscosities, desired flow rates, and the presence of solids.
The diameter of the impeller also affects pump performance, with larger diameters handling more fluid but requiring more energy to rotate. Overall, the impeller pump's performance, efficiency, and durability are heavily influenced by factors such as flow rate, head, specific gravity, viscosity, and solids content.
How Fresh Off the Boat Navigated ABC's Waters
You may want to see also
Frequently asked questions
An impeller is an internal component of a water pump in boat engines. It pumps water from outside the boat into the engine for cooling purposes.
The impeller is a fan-shaped object with flexible rubber fins. It rotates at a speed proportional to the engine's RPM, opening its vanes to draw water in and then closing them to push it out.
Impellers are generally found in two locations: in outboard engines or stern drives, and in sea water pumps. In outboard engines, the impeller is located just above the lower unit, near the cavitation plate. In sea water pumps, they are remotely mounted on the front of the engine.
Impellers should be replaced regularly to prevent engine damage. Some sources recommend replacement every year, while others suggest every two to three years.