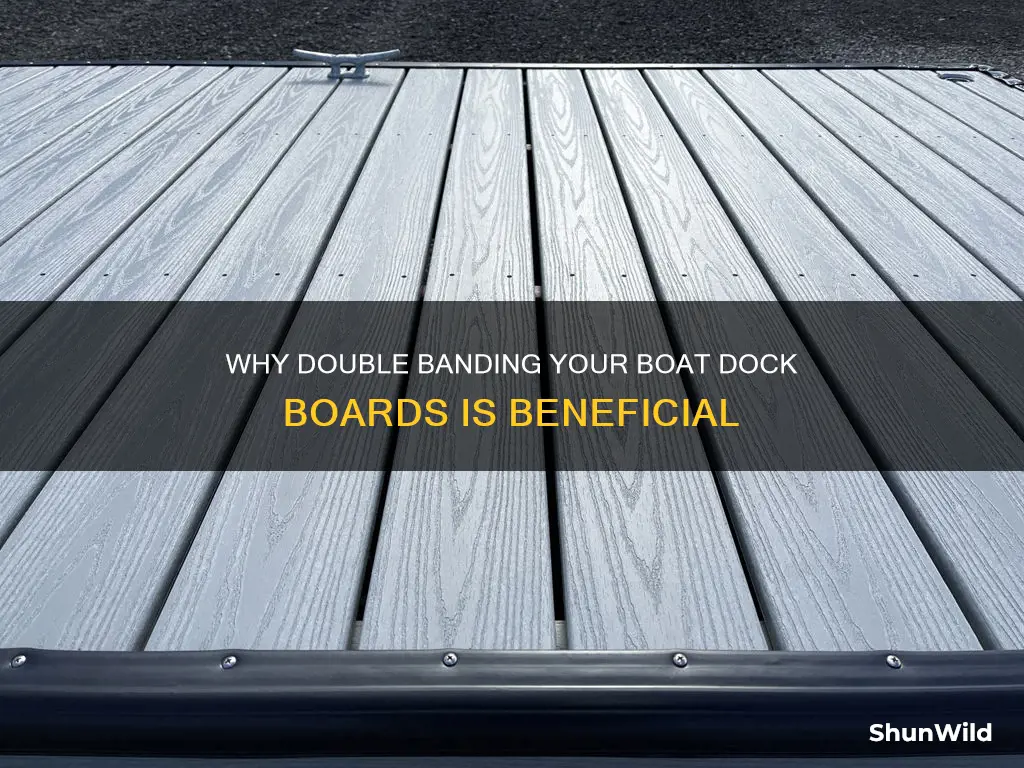
Boat dock boards should be fastened securely to withstand the test of time and the elements. When it comes to choosing between screws and nails as fasteners, there are several factors to consider. While nails are a traditional choice, stainless steel screws are highly recommended for their durability and resistance to rust, especially in marine environments. Screws also offer the advantage of being easier to remove if needed. However, some people prefer nails as they believe that if the boards can be easily removed, then the issue lies with the wood underneath rather than the fasteners. Ultimately, the decision between screws and nails depends on personal preference and the specific requirements of the boat dock.
What You'll Learn
Screws vs nails for fastening
When it comes to fastening boat dock boards, there are several factors to consider when choosing between screws and nails. Firstly, the type of stresses the fasteners will be subjected to is crucial. Shear strength refers to the ability of the fastener to withstand lateral pressure, such as wind blowing against a house, and this is where nails excel. They are more flexible under lateral pressure and can bend without snapping. On the other hand, screws have greater tensile strength, which is the ability to resist breaking under pressure or pulling apart. This makes them more suitable for projects where joined pieces are under tension or bearing weight.
Another consideration is the scale of the project and the speed of installation. Nails are generally faster and easier to install, especially with the use of nail guns. They are also less expensive than screws. However, screws have better holding power and can be adjusted or removed easily for repairs. Electric power tools like cordless drills and impact wrenches have made the installation of screws much quicker and easier.
For boat dock boards, the choice between screws and nails may depend on the specific requirements of the project. If the boards need to withstand significant lateral pressure or tension, screws would be more suitable due to their tensile strength. If speed and cost are important factors, nails might be preferred. Additionally, the type of wood and the presence of water could influence the decision. For example, nails may be preferred for hardwood flooring to prevent splitting, while screws are often used for composite decking. In the case of boat docks, stainless steel screws are recommended to prevent rust in the brackish river water.
In summary, both screws and nails have their advantages and are suitable for different situations. Screws offer superior tensile strength, holding power, and removability, making them ideal for projects with tension or weight-bearing requirements. Nails provide excellent shear strength, flexibility, and speed of installation, and they are more cost-effective. For boat dock boards, the decision between screws and nails should consider the specific project requirements, type of wood, presence of water, and cost.
Boat Battery Electricity: AC or DC?
You may want to see also
Stainless steel vs galvanised nails
When it comes to fastening down boards for a boat dock, there are a few options to consider. The existing nails may show rust, so it is important to choose a material that is durable and corrosion-resistant. Two options that are commonly used are stainless steel and galvanised nails.
Stainless steel is an excellent choice for boat dock boards due to its superior corrosion resistance. Type 316 stainless steel, in particular, is well-suited for marine environments and offers excellent durability. Stainless steel screws are available with different types of drives, including Torx and square drives. Torx drives are known for their ease of removal, while square drives offer consistent performance and ease of cleaning.
On the other hand, galvanised nails are a more economical option. They are made by dipping steel nails in molten zinc, which creates a protective coating that delays the onset of rust. Galvanised nails are commonly used for boat docks and are available in various sizes, such as 10d, 12d, 16d, 20d, 40d, and 60d common nails.
While both options have their advantages, the choice between stainless steel and galvanised nails ultimately depends on specific requirements and budget. Stainless steel offers superior corrosion resistance and is ideal for marine applications, but it may be more expensive. Galvanised nails provide adequate protection against rust at a more affordable cost but may require more frequent maintenance in marine environments.
When deciding between stainless steel and galvanised nails for boat dock boards, it is important to consider the specific needs of the project, the level of corrosion resistance required, and the available budget. By taking these factors into account, you can make an informed decision that best suits your needs.
Firming Up: Tightening Loose Boat Cleats
You may want to see also
Wood treatment
Wood is a popular choice for docks due to its natural and aesthetically pleasing finish. However, not all wood is created equal when it comes to weather resistance. To ensure the durability and safety of your dock, it is crucial to select wood with natural weather-resistant properties or treat it to withstand the elements.
Teak
Teak is a traditional choice for maritime use due to its exceptional weather resistance. Its natural oils effectively repel water, and it exhibits high resistance to decay, insects, and UV radiation. Teak also possesses the strength to withstand heavy use, making it a premium option for boat docks.
Cedar
Cedar is a lightweight and naturally rot-resistant alternative to teak. It is easier to work with during construction and possesses natural compounds that make it resistant to rot, decay, and insect attacks. Cedar has a distinct warm, reddish hue that many find appealing. However, cedar requires annual maintenance with a waterproofing sealer and is prone to developing knots and splinters over time.
Ipe
Ipe is a dense, tropical hardwood renowned for its incredible strength and durability. It is often referred to as "ironwood" due to its density, which contributes to its weather resistance. Ipe can last for decades with proper maintenance and is an excellent choice for a long-lasting boat dock.
Pressure-Treated Douglas Fir
While fir wood is not typically known for its weather resistance, certain types like Douglas fir can be treated to improve their durability. Pressure-treated Douglas fir is a more affordable option that can withstand moisture and decay when properly maintained.
Pressure-Treated Pine
Pressure-treated pine is the most common and affordable type of wood used for boat docks. It offers low initial installation costs, and with proper maintenance, it can last for more than 20 years. However, this wood type requires annual maintenance, including sealing with a water sealer to prevent water saturation. Without proper care, pressure-treated pine is susceptible to decay, rot, insect attacks, and the growth of mold, fungi, and algae.
Understanding Boat Engine Misalignment: Causes and Solutions
You may want to see also
Board spacing
The spacing between dock boards is critical for several reasons. Firstly, it allows for water drainage from the deck and prevents water from collecting and causing rot. Secondly, it facilitates ventilation and enhances cleaning by allowing debris to fall through the gaps. The size of the gap can vary depending on the type of decking material used and the presence of wave action or flooding.
For traditional wood decking, the gap between boards should be wide enough to accommodate the expansion and contraction of the wood due to changes in moisture content and temperature fluctuations. A gap of at least 1/8 inch is generally recommended for wood decking, with some sources suggesting a larger gap of up to 1/4 inch to allow for better water drainage and debris fall-through.
When using composite decking, which is made with a significant amount of plastic, the expansion and contraction are primarily due to temperature changes rather than moisture variations. Therefore, it is crucial to follow the manufacturer's installation instructions for composite decking to ensure proper board spacing.
In areas with wave action or flooding, it is recommended to leave a larger space between the dock boards. This allows for water flow and prevents the boards from acting as one large piece, which could be easily torn up by waves.
The use of spacers, such as a 16-penny nail or a professional deck spacing tool, can help achieve consistent spacing during installation. However, it is important to note that the fasteners used to attach the deck boards can also impact the spacing, and it is crucial to use fasteners that are long enough to penetrate the deck floor joists adequately.
Overall, the key to successful board spacing for boat dock boards is to strike a balance between allowing for drainage, ventilation, and debris fall-through, while also considering the expansion and contraction of the decking material and the presence of environmental factors such as waves or flooding.
Repairing Your Aluminum Boat: A Comprehensive Guide
You may want to see also
Board drying and shrinking
Wood is a hygroscopic material, meaning it can absorb and lose moisture. This is due to the way in which it grows—trees use water as part of their growth medium, taking it in at the root and leaf areas. During the primary growing seasons of spring and summer, trees have the most amount of moisture. In the fall and winter, moisture is stored in the roots as little to no growth is occurring.
Wood has an incredible capacity to hold moisture and is capable of holding twice its weight in water. As a log is converted (or sawn) into boards, water leaves the wood by surface evaporation. As water is evaporated at the surface, interior moisture migrates to the surface and is also evaporated. This is the natural drying process.
Gradually, the moisture content drops to the 30% level, which means 30% by weight compared to the dry weight of the wood. At this point, there is still fibre saturation in the wood, and there is no physical change in the size and shape of the board. Once the percentage of water content drops below 30%, the cell walls start to shrink and distortion of the piece of lumber starts to occur.
Generally, wood shrinks more around its circumference than it does across its radius. If you think of the annual growth rings, the shrinkage 'along the rings' is about twice as much as the shrinkage 'between the rings'. Therefore, shrinkage is not equal in both directions. It is this unequal shrinkage that causes distortion in wood as it dries.
The amount of shrinking and warping of wood depends on its moisture content, the wood species, and the orientation of growth rings. For example, some species such as Oak, Beech, and Hickory shrink more than Teak, Mesquite, and Cedar.
To minimize shrinking and warping in finished wood products, use only dry lumber between 6 to 9% and maintain an environment of 35-50% relative humidity. If you live in a very moist or very dry climate, measure the moisture in well-acclimated wood and match that moisture content when selecting lumber for your project.
Outboard Bass Boat Thermostat: Maintenance and Replacement Guide
You may want to see also
Frequently asked questions
It is recommended to use stainless steel screws or galvanised nails.
For screws, 316SS and square drive or torx head are recommended. For nails, 4-inch galvanised nails are suggested.
It is not recommended to seal, stain, or paint the wood near a marine environment, especially saltwater, as this will require more maintenance.