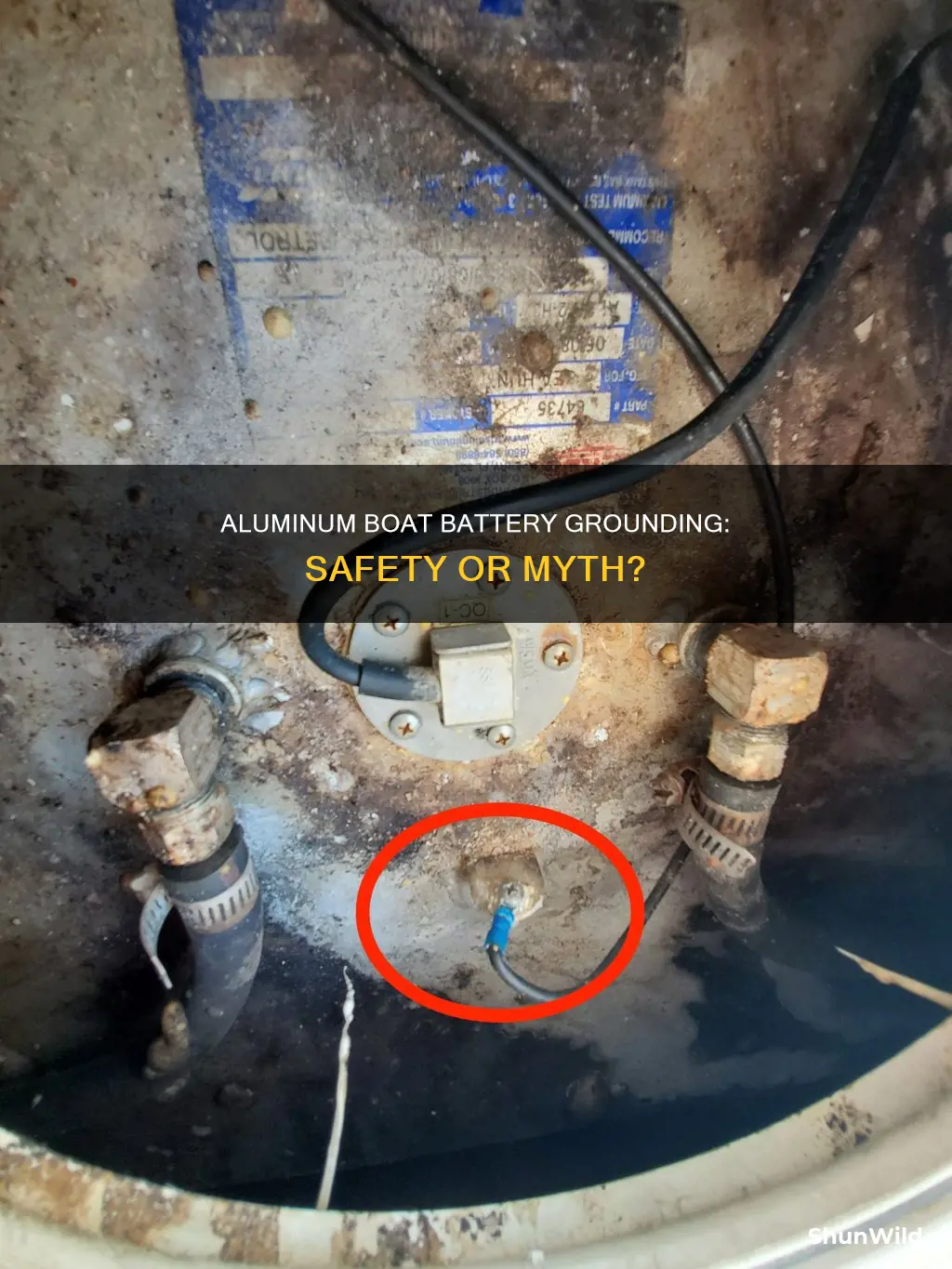
There are conflicting opinions on whether an aluminium boat should be grounded to a battery. Some people argue that grounding the battery to the aluminium hull of a boat can increase corrosion, especially in saltwater, and cause galvanic corrosion. However, others claim that grounding the battery can help reduce galvanic corrosion by providing a clear path for electrons to flow. Ultimately, it is important to consult a reliable technician or a boat dealer to ensure that the electrical system of the boat is properly grounded to prevent any potential issues or dangers.
What You'll Learn
The pros and cons of grounding an aluminium boat to the battery
There are differing opinions on whether it is a good idea to ground an aluminium boat to the battery. Some people say that grounding the battery to the hull of an aluminium boat will increase corrosion and could even cause the boat to sink. However, others say that this is not the case and that it is normal to ground the battery to the hull.
Pros
One advantage of grounding the battery to the hull is that it makes wiring much easier. It is also argued that grounding the battery can reduce the chances of electrolysis, particularly in saltwater. Additionally, it is claimed that grounding the battery can help to deal with stray currents and electrolysis.
Cons
The main concern with grounding an aluminium boat to the battery is the potential for increased corrosion. This is due to the creation of a battery when two dissimilar metals (in this case, the aluminium boat and the battery) are introduced into water, which acts as an electrolyte. This can lead to galvanic corrosion, where the aluminium boat becomes the anode and is slowly eaten away.
Another potential issue with grounding the boat to the battery is the risk of electrical shorts. If a wire chafes on the hull, it could create a short circuit, which could be dangerous.
It is worth noting that some people argue that grounding the battery to the hull of an aluminium boat is unnecessary, as the hull will become a negative circuit as soon as the engine is hooked up to the battery terminals anyway. Therefore, it is recommended to keep an eye on the sacrificial anodes and ensure that all electrical devices have their own dedicated ground wire connected directly to the battery.
Tracing Boat Registration Numbers: A Step-by-Step Guide
You may want to see also
The impact of saltwater on a grounded aluminium boat
Saltwater can have a devastating impact on a grounded aluminium boat. Aluminium is susceptible to galvanic corrosion, which occurs when two dissimilar metals are brought together in an electrolyte solution, such as saltwater. In this process, one metal will give up atoms to the other, causing it to fall apart or corrode.
Aluminium boats are particularly vulnerable to galvanic corrosion when in contact with saltwater and other metals. This is because aluminium is a very reactive metal, and when connected to a dissimilar metal in saltwater, it will give up its atoms, leading to corrosion. The presence of saltwater accelerates this process, as it is an effective conductor of electricity.
The damage caused by saltwater to an aluminium boat can be severe and may include pitting, flaking, blistering, and spalling of the aluminium structure. This can result in leaks and even catastrophic failure. To prevent this, it is crucial to take measures such as using sacrificial anodes, isolating dissimilar metals, and regularly cleaning and drying the boat.
Additionally, it is generally not recommended to ground the battery of an aluminium boat directly to the hull, especially in saltwater environments. This is because it can increase the risk of galvanic corrosion and create a safety hazard. Instead, each device should have its own separate ground wire connected directly to the battery.
To protect an aluminium boat from the damaging effects of saltwater, it is essential to follow best practices for wiring, grounding, and corrosion prevention. This includes using dedicated ground wires for each device, avoiding the use of the hull as a common ground, and regularly inspecting and maintaining the boat's electrical systems.
Deluxe Bolster Seats: A Worthy Boat Investment?
You may want to see also
The potential for galvanic corrosion
Aluminum boats are susceptible to galvanic corrosion, which occurs when two dissimilar metals are connected by an electrolyte, enabling the movement of electrical current. In this process, one metal acts as the anode (giving up electrons) and the other as the cathode (gaining electrons). This leads to the breakdown and dissolution of the anode into the electrolyte, while the cathode is also broken down more slowly.
Aluminum boats are particularly vulnerable to galvanic corrosion when in contact with metals that are higher on the anodic index, such as copper. This includes pressure-treated wood, which often contains copper and can lead to rapid oxidation of the aluminum hull. Even in the absence of dissimilar metals, aluminum boats can experience galvanic corrosion if they come into contact with conductive solutions like saltwater, which can cause the boat to corrode and fall apart.
To prevent galvanic corrosion, it is crucial to avoid direct contact between aluminum and dissimilar metals, especially in a marine environment. Sacrificial anodes, such as zinc or magnesium, can be used to protect aluminum boats by providing extra electrons for the corrosion process, thus corroding themselves instead of the aluminum. Additionally, proper maintenance, including regular rinsing and drying of the boat, can help mitigate the risk of galvanic corrosion.
While grounding the battery to the hull of an aluminum boat may provide certain advantages in terms of wiring convenience, it is generally not recommended due to the potential for galvanic corrosion. This is because the battery, hull, and engine form an electrical circuit, and any dissimilar metals in this circuit can lead to corrosion issues. Therefore, it is advisable to avoid using the hull as a common ground and instead use dedicated wiring for each component, reducing the risk of shorts and galvanic corrosion.
Repairing Aluminum Boats: Dents and Dings
You may want to see also
The role of sacrificial anodes
Sacrificial anodes are critical to any boat corrosion protection system. They are small, inexpensive, and highly effective. They are designed to protect other surfaces from corrosion by oxidising more quickly than other parts of the boat. In doing so, they decay faster, sacrificing themselves to benefit the boat.
There are three main types of sacrificial anodes: zinc, aluminium, and magnesium. Zinc anodes are highly effective, especially for boats docked in saltwater. Aluminium anodes are more durable and can be used in saltwater and brackish water. Magnesium anodes are ideal for freshwater environments, as they have a low electrical potential.
Sacrificial anodes are easy to install and maintain. They can be secured to the surface using bolts, welds, or brackets. They must be regularly checked for signs of corrosion and replaced when they have visibly reduced in size.
Sacrificial anodes play an essential role in protecting boats from corrosion, extending the life of the hull, reducing maintenance costs, and improving performance. They are a cheap and effective way to ensure the longevity of a vessel.
Securing Your Ski Boat: Dock Tying Techniques
You may want to see also
Best practices for wiring an aluminium boat
Aluminium boats are prone to galvanic corrosion, particularly in saltwater. This is caused by the introduction of an external power source, such as a generator or alternator, which can lead to galvanic corrosion and damage the battery. Therefore, it is important to minimise the risk of corrosion by following best practices when wiring an aluminium boat.
Firstly, it is recommended to use a wiring schematic when wiring an aluminium boat. This provides a roadmap for troubleshooting any issues that may arise. Making detailed notes of any repairs and using colour-coded wires can also help with problem-solving. High-grade connections, dielectric grease, and shrink tubing should be used on all connections to prevent corrosion and ensure optimal performance. It is also important to tighten battery terminals snugly and hook up the positive lead first.
When pulling wires through chases, it is recommended to use lubrication and avoid pulling too hard to prevent damage to the wires. Zip ties can be used to bundle wires, but only in limited quantities to avoid snagging. To prevent radio frequency interference, ferrite rings or RF coils should be used around electronics.
It is crucial to use the proper wire gauge for the application, taking into account the load requirement and distance from the battery. For example, a trolling motor on a 20-foot boat should use 4 or 6 gauge wire. Additionally, each device should have its own dedicated ground wire directly connected to the battery negative terminal. This reduces the risk of shorts and ensures optimal battery performance.
Finally, it is recommended to use sacrificial anodes to protect the aluminium boat from corrosion. By providing a less noble metal (zinc) for the electrical charge to pass through, the sacrificial anodes degrade over time, preserving the aluminium hull.
Webber Pond Boat Launch Location: A Guide
You may want to see also
Frequently asked questions
Yes, it is normal to ground an aluminium boat to the battery's negative side. However, it is not recommended as it can lead to galvanic corrosion.
No, it is not necessary to rewire your aluminium boat if it is grounded to the battery's negative side. The grounding of the boat to the battery's negative side is common and will not cause any issues.
Grounding an aluminium boat to the battery can affect its performance by increasing galvanic corrosion. It is recommended to use a separate wire for each electrical device and not use the hull as a common ground.
Grounding an aluminium boat to the battery can make wiring easier as you don't have to take wires far to find ground. It can also reduce galvanic corrosion by providing a clear path for electrons to flow.
Yes, grounding an aluminium boat to the battery can increase the risk of galvanic corrosion, especially in saltwater. It can also create a short circuit if a voltage wire chafes on the hull.