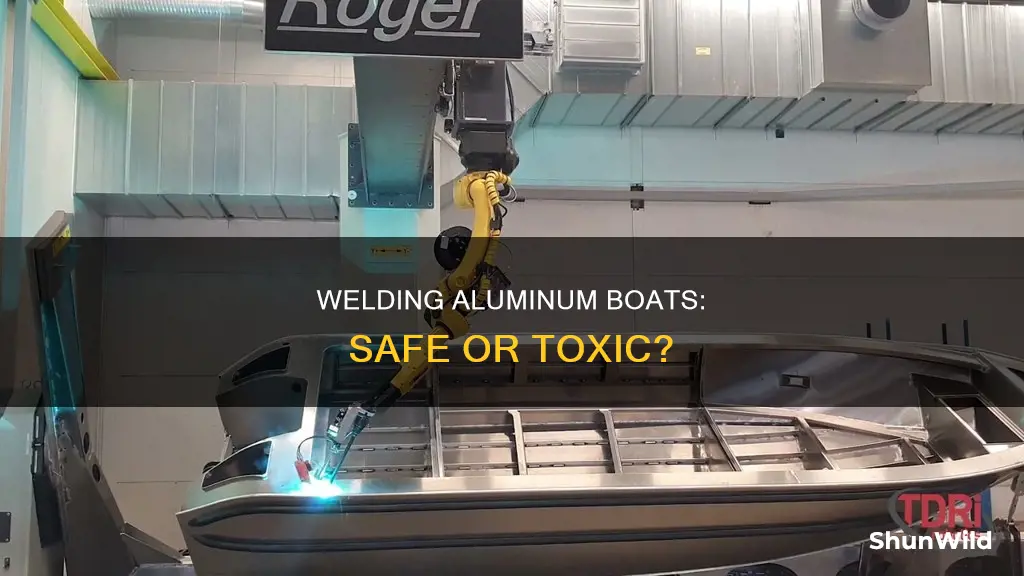
Welding an aluminium boat is a challenging task, especially for beginners. Aluminium boats are usually made with un-weldable alloys, which can crack very easily as the weld cools. Aluminium also dissipates heat quickly, so you will need oxyacetylene, oxy-MAPP gas, or oxy-propane to weld it. In addition, aluminium boats flex a lot, so a welded area may not be as flexible and could crack. However, with the right tools and preparation, it is possible to successfully weld an aluminium boat.
What You'll Learn
TIG welding is a suitable method for repairing an aluminium boat leak
TIG welding is a suitable method for repairing a leak in an aluminium boat, but it can be challenging and there are other methods that may be more appropriate.
Advantages of TIG Welding
TIG welding is a good method for repairing aluminium boats because it offers greater control than MIG welding, allowing for smaller beads and more precise welds. This is especially useful for thin aluminium sheets, which are commonly used for aluminium boats. TIG welding can also be scaled down for the small beads implied by thin aluminium sheets.
Disadvantages of TIG Welding
TIG welding can be challenging for boat repairs due to the amount of crud that accumulates in the weld pool. It is also a slow process that puts a lot of heat into the metal, which can cause warping. Additionally, TIG welding equipment can be expensive.
Alternative Methods
Other methods for repairing leaks in aluminium boats include:
- Using epoxy or sealant
- Riveting on an aluminium patch
- Soldering with a propane torch and zinc alloy filler
- Brazing with an acetylene torch and aluminium brazing rod
- MIG welding with a spool gun
Considerations for TIG Welding Aluminium Boats
If you decide to use TIG welding to repair a leak in an aluminium boat, there are a few things to keep in mind:
- Cleanliness and surface preparation are crucial. Both the filler material and the base should be free of any foreign objects or materials.
- Cut the aluminium pieces right before welding to minimise oxidation.
- Use a clean stainless steel brush to remove aluminium oxide from welding surfaces.
- Avoid using compressed air to clean aluminium, as it can contain moisture that will react during the weld.
- Do not lubricate metal pieces that will be welded.
Troubleshooting Boat Engine Cut-Out Issues During Acceleration
You may want to see also
Aluminium boats are prone to corrosion
Galvanic corrosion occurs when two dissimilar metals come into contact with each other in an electrolyte solution, such as saltwater or freshwater. In most cases, the corrosion of the aluminium hull will be visible around the fitting or the cause of the corrosion. Stainless steel bolts and fittings are usually isolated from the aluminium hull using plastic washers and sleeves to prevent galvanic corrosion. Sacrificial anodes, typically made of zinc, can also be used to protect the aluminium hull from corrosion.
Electrolysis is caused by potential current (AC or DC) between two different objects, often due to stray electrical current travelling through the water. A well-maintained bonding system that meets American Boat and Yacht Council (ABYC) standards can help safeguard against electrolysis.
Crevice corrosion occurs when contaminated water is trapped against the aluminium, such as under paint edges that were not properly prepared. To reduce the risk of crevice corrosion, aluminium boats should be designed without crevices or joints that could collect and trap water. Paint systems should also be approved for aluminium use, and both paint and vinyl wrap applications should minimise sharp edges that allow water penetration.
To prevent corrosion in aluminium boats, it is important to use only paint and coatings designed for aluminium. After using the boat in saltwater, it is crucial to rinse the boat thoroughly. Additionally, cracks and scratches that expose the bare aluminium should be repaired, and impressed voltage should not exceed 1,300 millivolts when protecting the aluminium.
Transferring Boat Ownership: Signing Over a Title in Wisconsin
You may want to see also
Aluminium oxide makes welding more difficult
Aluminium oxide is formed when aluminium materials are welded. This oxide occurs in the form of spherical particles, from a minimum of 10 to 50 or up to 400 nanometres depending on the welding method being used. The oxide particles can put a strain on the respiratory tracts and even the lungs if they are inhaled and deposited there. Respiratory diseases such as bronchitis can occur as a result, and in some cases, the dust deposits can cause irreversible aluminosis, or aluminium lung.
In addition to the health risks posed by the oxide, the combination of aluminium and MIG or TIG welding methods creates another harmful substance: ozone. This is formed as a result of ultraviolet radiation from the oxygen in the air, which is reflected on the bare aluminium surfaces. Ozone is unstable and can spread out easily when there are low levels of fume development. It is also classified as carcinogenic, and protective measures must be taken during welding.
Due to the presence of aluminium oxide and ozone, technical measures are recommended when welding aluminium, such as the suction-removal of welding fumes and gases at their places of origin.
Aluminium oxide is created during the welding process when aluminium materials, including the filler and base materials, react with the atmosphere. This oxide forms spherical particles, which can vary in size depending on the welding method.
The presence of aluminium oxide during welding poses several challenges and risks. Firstly, the oxide particles can be harmful to respiratory health if inhaled, potentially leading to respiratory diseases or even irreversible lung damage, known as aluminosis. Therefore, it is crucial to implement adequate ventilation and protective measures during welding to minimise the risk of inhaling these particles.
Secondly, the formation of aluminium oxide can interfere with the welding process itself. The oxide layer acts as a barrier on the surface of the aluminium, making it more difficult to create a clean and strong weld. This is because the oxide has a higher melting point than the base metal, requiring more heat energy to melt and resulting in a higher risk of weld defects.
To overcome the challenges posed by aluminium oxide, welders often use alternating current (AC) TIG welding. In this process, the constant polarity switch between positive and negative breaks down the oxide layer by bombarding it with particles. The positive side of the AC wave strips away the oxide, allowing for a cleaner weld.
While AC TIG welding is effective for breaking down the oxide layer, it does have some drawbacks. It can result in a slight waste of heat due to the positive side of the wave, and it may not be suitable for all types of aluminium welding, especially for thin aluminium. In such cases, other techniques, such as manual cleaning of the oxide layer or using a larger electrode to handle the heat, may be considered.
In summary, aluminium oxide formation during welding not only poses health risks but also makes the welding process more difficult. Welders need to be aware of these challenges and take appropriate measures to ensure a safe and successful weld.
Boat Engine Types: Outboard, Inboard, and Sterndrive
You may want to see also
TIG welding requires a high level of cleanliness and surface preparation
Untreated aluminium oxidises when exposed to air, making welding more difficult. To combat this, aluminium pieces should be cut immediately before welding, using a plasma arc, laser, or a circular saw. A solvent should then be used to remove any foreign grease and oil from the surfaces of the aluminium pieces.
A stainless steel brush is the best tool to remove aluminium oxide from welding surfaces. This provides a much better, more long-lasting result. Grinders should be avoided, as they leave burrs and other imperfections that make welding more difficult.
Oxy-fuel should not be used to cut or pre-heat parts, as it contains oxygen, which will cause more oxidation. Similarly, shop rags and compressed air should be avoided when cleaning aluminium, as they can contain dirt, grime, debris, and moisture, which will react during the weld.
Finally, metal pieces that will be welded should not be lubricated, as they will be hard to clean thoroughly before welding.
Exploring Boat Back Fees: Understanding the Cost of Boating
You may want to see also
There are alternative methods to repair an aluminium boat leak
TIG welding is a common method for repairing leaks in aluminium boats. However, it can be challenging due to the amount of debris in the weld pool and the thin aluminium sheets used in boat construction. If the boat was originally riveted, welding repairs may not be successful, and the welds may crack beside the repairs.
- Epoxy resin: This method uses epoxy resin, such as WEST SYSTEM G/flex®, to repair leaky rivets and seams in aluminium boats. The process involves identifying the leaks, preparing the surface, mixing the resin and hardener, drying the repair area, applying the epoxy, and curing it.
- Sealants: Various sealants, such as Flex Seal, Marine Adhesive Sealant, and aircraft sealants, can be used to repair small cracks and holes in aluminium boats. These products provide a temporary solution and may not be as durable as welding or epoxy repairs.
- Rivet replacement: If the leak is due to loose or damaged rivets, they can be replaced with closed-in rivets and rivet burrs. This method requires drilling out the old rivets and installing new ones with a marine adhesive sealant.
- Consulting a professional: For complex or challenging repairs, it may be best to consult a professional boat repair service. They have the experience and equipment to properly fix the leak and avoid further issues.
- Other welding techniques: While TIG welding is commonly used for aluminium boat repairs, other welding techniques, such as MIG welding with pulse settings, can also be employed. However, these techniques may require more expensive equipment and specialised skills.
Mafia 3 Boat Mystery: Solving the Missing Vessel
You may want to see also
Frequently asked questions
TIG welding can be harmful to your health if you don't take the right precautions. Make sure to wear protective clothing, including a welding helmet and gloves, and ensure the area is well-ventilated.
Alternatives to TIG welding include using epoxy, riveting on an aluminium patch, or using a propane torch and zinc alloy filler.
It's important to ensure the area is clean and free of foreign objects or materials. Untreated aluminium should be cut immediately before welding, and all grease and oil should be removed with a solvent.
Do use a plasma arc, laser, or circular saw to cut aluminium pieces, and clean the pieces with a solvent to remove grease and oil. Don't use a grinder to cut aluminium pieces, as it leaves burrs and imperfections that make welding more difficult.