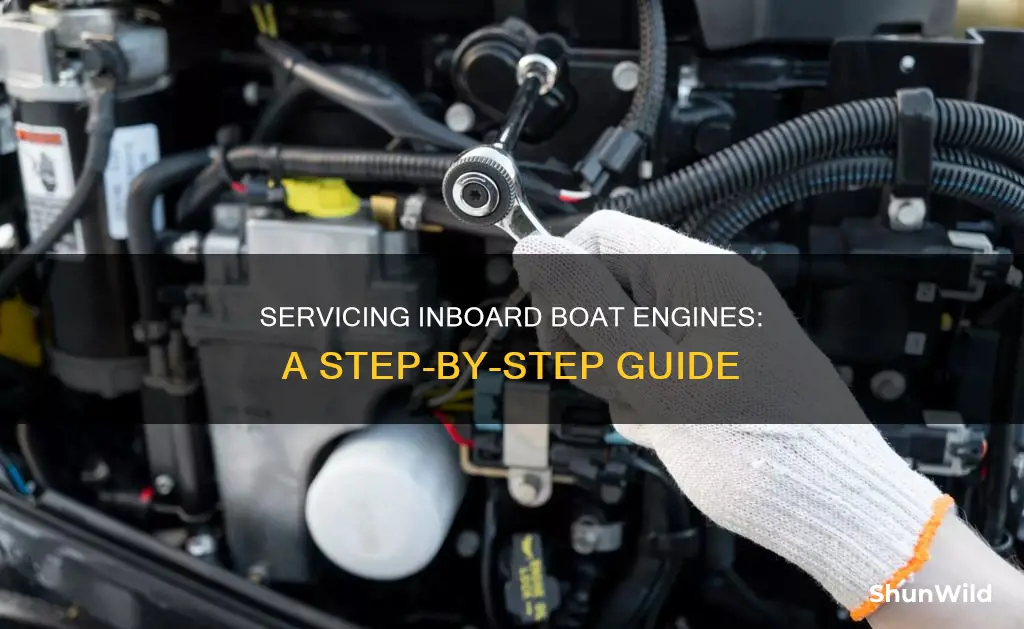
Servicing your inboard boat engine is essential to ensure it runs smoothly and efficiently. Inboard engines are vulnerable to the marine environment, with unique challenges such as water and salt corrosion, making regular servicing critical to prevent engine failure. The frequency of servicing depends on usage, with servicing recommended at either 12 months or 100 hours, whichever comes first. This guide will explore the key areas that need attention during servicing and provide an overview of the steps involved in maintaining your inboard boat engine.
What You'll Learn
Check for water on spark plug electrodes
Checking for Water on Spark Plug Electrodes
When servicing an inboard boat engine, it is important to check for water on the spark plug electrodes. This is because water in the spark plugs can indicate a larger problem with the engine, such as a bad head gasket, water in the fuel, or a bad exhaust manifold. Checking for water on the spark plug electrodes is a simple process, but it can help diagnose problems and save future repair costs.
To check for water on the spark plug electrodes, first remove the spark plugs from the engine. Look for water droplets or rust on the spark plugs, as this could indicate that water is getting into the cylinder. If water is present, it is important to address the issue and ensure that the spark plugs are dry before continuing.
Next, examine the tip of the spark plug, also known as the firing nose. A healthy spark plug will have a gray or light beige colour, indicating that it is operating at the right temperature. If the tip is dry and covered in soft, sooty black deposits, it indicates that the engine is running an excessively rich fuel mixture. A wet, oily coating on the tip may be a sign of a breached head gasket or engine oil leaking past worn valve guides or piston rings, allowing oil into the combustion chamber.
Finally, check the electrodes for signs of excessive wear. Rapid wear often indicates that the spark plugs are overheating. Other signs of overheating include misfiring while accelerating and difficulty starting the engine. If the spark plugs show signs of water damage or excessive wear, they should be replaced.
It is important to consult the engine manual for specific recommendations on spark plug maintenance and replacement. Additionally, if you are unsure about any aspect of the process, it is best to seek advice from a qualified mechanic.
Balancing Your V-Hull Boat: Weight Distribution Tips
You may want to see also
Inspect the coolant pump
Servicing your inboard boat engine's coolant pump is a critical aspect of ensuring optimal performance and prolonging the engine's lifespan. Here are some detailed instructions to guide you through the process:
Understand the Cooling System:
Before inspecting the coolant pump, it's essential to grasp the fundamentals of your boat's cooling system. Inboard boat engines typically employ one of two cooling systems: a freshwater-dependent system or an "enclosed" system. The former relies solely on a constant supply of fresh seawater to cool the engine, while the latter uses a mix of antifreeze and a heat exchanger to regulate engine temperature. Understanding which system your boat employs will help you locate the coolant pump and identify its key components.
Locate the Coolant Pump:
The coolant pump in an inboard boat engine is usually found at the front of the engine and is often driven by a belt. It plays a vital role in circulating the coolant, ensuring efficient heat absorption and preventing engine overheating.
Over time, the coolant pump's components can wear out or become damaged. Carefully examine the pump for any signs of deterioration, such as cracks or leaks. Pay close attention to the impeller, a critical component that can degrade over time due to dry rot or insufficient water supply. It is generally recommended to replace the impeller every two years, regardless of usage. Also, inspect the pump housing for any signs of damage, which may be caused by a lack of winterization or operating the engine with low water levels.
Check the Pump Belt:
The belt that drives the coolant pump is subject to wear and tear. Inspect the belt for any glazing, which appears as a shiny surface on the interior side of the belt. A glazed belt indicates slippage and should be replaced immediately, as it can lead to engine overheating. Ensure that the belt tension is correctly adjusted to prevent glazing and optimize pump performance.
Maintain the Coolant:
The coolant itself requires regular maintenance to function effectively. Check the coolant reservoir to ensure the fluid level is adequate and top it up if necessary. Additionally, the coolant's condition should be assessed using specialized tools like a floating ball gauge, hydrometer, test strips, or a refractometer. These tools help determine the ratio of antifreeze to water, ensuring it adheres to the manufacturer's specifications, typically a 50/50 mixture. Coolant maintenance also involves verifying the pH level to prevent corrosion.
Replace the Coolant Regularly:
Even with proper maintenance, coolant deteriorates over time, and its effectiveness diminishes. Therefore, it is essential to replace the coolant entirely and flush the system every five years or after 1,000 hours of engine use, whichever comes first. This helps eliminate any built-up deposits and ensures the optimal performance of your inboard boat engine's cooling system.
By following these comprehensive steps, you can effectively inspect and maintain the coolant pump, safeguarding your inboard boat engine's performance and longevity.
Troubleshooting RC Boat Performance: Bogging Down Issues Explained
You may want to see also
Replace the primary fuel filter
Most marine systems have two fuel filters: a primary filter and a secondary filter. The primary filter is placed in the fuel lines between the tank and engine. It is essential to keep water and foreign particles out of your engine.
The type of primary filter commonly found on small boat installations comprises a filter element with a glass or metal bowl underneath to catch water and heavy sediment. These are held together with a long bolt running through the centre of the system.
To replace the primary fuel filter, first close the fuel stopcock to prevent fuel from draining from the tank. Some systems have stopcocks on both sides of the filter, which minimises fuel loss and the amount of air introduced to the system.
Before touching the filter, ensure you have measures in place to catch the fuel that will drain from it. Place a bowl underneath or, if there isn't enough space, hang a plastic bag around the filter.
Unscrew the central bolt, allowing the filter and bowl to separate and the fuel to drain. If the canister doesn't come away, you may need to give it a slight tug to separate it from the bracket. Check the sealing rings between the bracket, canister and bowl. They don't need to be replaced every time, but you may choose to do so as new filters usually come supplied with new seals.
To install the new filter, simply reverse the process. Assemble the base plate, bowl and filter as a single stack, insert the bolt, and tighten it firmly with a spanner.
The manufacturer's manual will specify the recommended replacement interval for the primary fuel filter, but it is typically around 200 hours.
Kickstarting an Inboard Outboard Boat with Starting Fluid
You may want to see also
Change the engine oil
Changing the Engine Oil
Changing the engine oil is one of the most important aspects of maintaining your inboard boat engine's health and performance. Engine manufacturers typically recommend an oil change every 100 hours of use, and at least once a year. However, the unique challenges of the marine environment mean that the oil in boat engines can be contaminated with abrasive and chemical impurities, so it is important to change the oil more frequently than you would for a car engine.
Preparation
Before you begin, purchase the correct type and amount of oil, and gather the necessary tools. Place catch pans and oil-absorbent pads beneath the engine and oil filter to add an extra layer of protection and keep accidental spills from reaching the bilge. Remember that even a sheen of oil on the water from your bilge pump discharge can result in costly cleanup fees. You should also temporarily disable automatic bilge pumps to prevent oil from being pumped overboard in the event of a spill.
Warm Up the Engine
Before changing the oil, run the engine up to its normal operating temperature. This will thin the oil, making it easier to drain, and stir up any sludge from the bottom of the sump so that it can be removed with the oil. Warming the engine normally takes about 15 minutes, so it's worth planning to change the oil at the end of a day on the water when the engine is already hot.
Drain the Oil
Most marine engines have a sump plug that can be used to drain the oil, but there is rarely room to access the plug or place a tray underneath to catch the oil. If your engine has a sump plug, use a socket wrench to remove it. As soon as the plug is loose enough to turn by hand, switch to a short extension to avoid dropping it into the container.
If your engine doesn't have a sump plug, or it is inaccessible, you will need to use an oil evacuation system to pump the oil out through the dipstick tube. You can buy a manual or electric pump designed for this purpose, or you may need to use a pump permanently mounted to an engine-compartment bulkhead.
Change the Oil Filter
Regardless of the manufacturer's recommendations, you should change the oil filter every time you change the oil. Oil filters are usually the "spin-on" variety, which can be removed with a strap wrench. Coat the gasket of the new filter lightly with oil, then screw it in by hand until the gasket makes full contact. Finally, tighten it another 3/4 of a turn.
Some older engines have cartridge-type oil filters. To change the cartridge, first, remove the center bolt and canister. Empty the canister and discard the old cartridge, then clean the housing with diesel fuel or kerosene before inserting the new cartridge.
Refill the Engine
The final step is to pour in the fresh oil. Check your engine manual for the recommended viscosity and API rating, and make sure you buy oil with these ratings. The API rating will begin with C for diesel engines and S for gasoline engines, followed by a letter indicating the complexity of the additive package. The SAE rating indicates the viscosity, or thickness, of the oil.
When refilling the engine, use a funnel to avoid spills, and add a short length of hose to assist with hard-to-reach oil fills. Once you've added the oil, start the engine and look for leaks, particularly around the oil pan and filter. Top up if needed, as the new filter is now filled.
Safety Equipment for Boating in New York
You may want to see also
Flush the freshwater system
Flushing the freshwater system of an inboard boat engine is essential to maintaining optimal performance and longevity. This process involves removing salt, debris, and other foreign substances that can build up in the cooling system over time. Here's a detailed guide on how to effectively flush the freshwater system:
Locate the Cooling System Components:
First, you need to identify the cooling system components, such as the raw water intake and flushing valve. Refer to the owner's manual to find the intake valves, as these vary for each boat. Inboard engines usually have a through-hull cooling-water pickup, often covered by a grate or strainer.
Connect the Hose:
You will need a garden hose that can reach your boat, a freshwater source, and appropriate valve adapters. The hose will connect your engine to the freshwater source, while valve adapters will help establish a secure connection. A hose with a 1-1/4 inch diameter is typically recommended to ensure adequate water flow.
Run Water Through the System:
Once the hose is connected, turn on the water supply and allow fresh water to flow through the engine's cooling system for several minutes. It is standard practice to start with a low water flow and gradually increase it.
Check for Proper Water Outflow:
Observe the water exiting the exhaust port, which is connected to the exhaust manifold. If the flow is steady and clear, it indicates that the flushing process was successful.
Additional Tips:
- It is recommended to flush your engine for 10 minutes after each use.
- Always flush the engine when it is cool to avoid damage from thermal shock. Running cold water through a hot engine can cause cracking.
- If your boat comes into contact with saltwater, flush the cooling system regularly to prevent salt buildup and corrosion.
- If you are storing your boat, especially in sub-zero temperatures, use antifreeze coolant to prevent freeze-related damage.
By following these steps and maintaining a regular flushing schedule, you can effectively flush the freshwater system of your inboard boat engine, ensuring its optimal performance and longevity.
Finding the Right Boat Broker: What to Look For
You may want to see also
Frequently asked questions
It is recommended to service your engine annually or every 100 hours, whichever comes first.
Water on spark plug electrodes and issues with the coolant pump are two of the most common issues that lead to engine failure.
The basic steps include checking and replacing fuel filters, draining and replacing engine oil, checking and replacing the coolant, and servicing the air and oil filters.
Regular maintenance according to the manufacturer's schedule is key. This includes frequent checks of the exhaust system, ensuring a steady flow of cooling water, and keeping the engine and fuel clean and free of contaminants.
Signs of engine trouble include burning excessive oil, increased fuel consumption, and a lack of "get up and go". If you notice any unusual behaviour, it is best to consult a qualified mechanic for a thorough inspection and servicing.