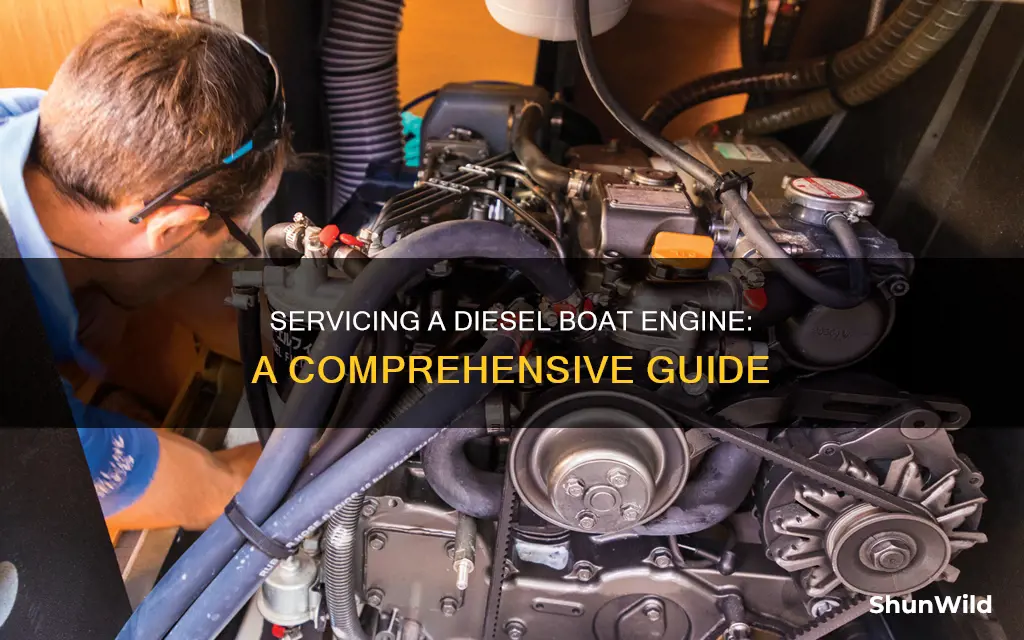
Servicing a diesel boat engine can be a daunting task, but with the right tools, knowledge, and regular maintenance, it becomes much more manageable. Here are some essential tips to help you get started:
- Familiarise yourself with the engine: Know the different components and their functions. Understand that the diesel engine is a system, and all parts need to work together in harmony.
- Preventative maintenance is key: Regularly check for problems and address them promptly. Listen to your engine and spot trends, such as unusual sounds or performance issues.
- Keep a maintenance log: Record engine details such as oil changes, filter replacements, and any unusual findings. This log will help you identify potential issues and ensure your engine's longevity.
- Change your oil and filters: Engine oil and filters should be changed seasonally or after a certain number of engine hours. This is crucial to remove contaminants and prevent corrosion.
- Check the coolant and antifreeze: Drain and replace the coolant and antifreeze periodically to prevent overheating and corrosion.
- Inspect the raw water pump and impeller: Remove and clean the impeller regularly, coating it with provided glycerin or olive oil before reinstallation.
- Maintain the air intake and exhaust: Ensure the free flow of air into the engine by regularly replacing air filters or cleaning synthetic wadding filters.
- Keep an eye on the alternator belt: Check the alternator belt for wear and cracking. Ensure it is properly tensioned, and consider replacing it annually.
- Fuel system care: Use the correct fuel filter for your engine and check the inspection bowl before each trip. Bleed the fuel system if air gets into it.
- Seek professional help when needed: Some tasks, such as valve adjustments, cylinder head retorquing, and turbocharger maintenance, are best left to trained technicians.
Characteristics | Values |
---|---|
Tools required | Spanners or wrenches, wire brushes, Vaseline, Marine 16 fuel additive, gloves |
Engine parts | Fuel tank, filters, oil, anodes, impellers, alternator drive belt, etc. |
Maintenance tasks | Check engine oil level, coolant/antifreeze, transmission fluid, belts, pulleys, etc. |
Fuel | Diesel |
Engine type | Marine diesel engine |
What You'll Learn
Fuel filters: how to check, clean and replace them
Checking and replacing the primary fuel filter
The primary fuel filter is placed in the fuel lines between the tank and engine. It is usually a filter element with a glass or metal bowl underneath to catch water and heavy sediment. Check regularly throughout the season for water collection. It will be clearly visible at the bottom of a glass bowl; metal bowls will require occasional draining to check.
To drain the filter bowl, there will be a cock or plug at the bottom. Hold a container underneath and open the cock or loosen the plug. Once any water has passed through, you should see a stream of clear fuel. Close the cock or screw the plug shut.
Replacing the filter is recommended at intervals of around 200 hours, although you should check the engine manual. First, remember to close the fuel stopcock to stop fuel draining from the tank. Some systems have stopcocks on both sides of the filter, which minimises loss from fuel pipes and reduces the amount of air a new filter introduces to the system.
Before touching the filter, make sure you have measures in place to catch the fuel that will drain from the filter. A bowl below allows easy access when working, or if there isn’t space, try hanging a plastic bag around the filter. Unscrew the central bolt, allowing the filter and bowl to separate from the bracket and the fuel to drain into the bowl or bag.
To fit the new filter, simply reverse the process. It’s best to assemble the base plate, bowl and filter as a single stack before offering it up and inserting the bolt. Finally, tighten the bolt firmly with a spanner.
Replacing the secondary fuel filter
The secondary filter is generally one of two types: a spin-on filter similar to a car oil filter, or a type similar to the primary filter, without the separator bowl.
To replace a spin-on filter, unscrew the filter with a filter wrench until you can just move it by hand. Place a plastic bag around the filter and continue to unscrew it, allowing the fuel to drain into the bag.
Check the area where the new seals will sit for grime and wipe if necessary. Having first applied a smear of diesel to the sealing ring, screw the new filter in place: hand-tight is sufficient if access is good enough to apply your full force, otherwise, use a filter wrench – but only gently!
Bleeding the fuel system
Changing the fuel filters allows air into the pipes. For the engine to run properly, this must be ‘bled’ by driving it out under slight pressure from high points in the fuel system. Some engines are self-bleeding and can vent air without assistance, but most require you to carry out a few simple steps.
Firstly, make sure you have plenty of fuel and that all the valves in the fuel lines are fully open. Try to operate the lift pump lever – if it won’t move or is reluctant, hand-turn the engine half a revolution to move the drive cam, and try again.
If your primary filter is below the level of the fuel in the tank, and your fuel is drawn directly from the bottom of the tank rather than via a dip pipe, you can fill the primary filter simply by cracking open the bleed screw on the top. You should see the bowl fill with fuel, and once clean, bubble-free fuel starts to flow from around the bleed screw, close it. There may still be air on the downstream side of the filter which will need to be vented using the method described below, but having already filled the primary filter accelerates the bleeding process.
In either case, the next stage is the secondary filter. Open the bleed screw and operate the lift pump. This may take several minutes, especially if you have to fill the primary filter this way. Fuel should start appearing around the bleed screw; once this is free of bubbles, you can close the screw.
Checking for water in the fuel
Water in the fuel can promote the growth of bacteria that can block fuel filters. Take a fuel sample and pump half a litre or so of liquid from the very bottom of the tank into a clear container. If only clear diesel comes out, you’re lucky. If you get a mix of fuel and water, keep pumping until you get only clean diesel. Bacteria tend to live at the boundary between the water and fuel layers, so if any was present in the tank, you can expect to have extracted at least some of it. If there are none in your sample, then you know you now have a tank of clean, water-free fuel.
Repairing Your Plywood Boat: A Comprehensive Guide
You may want to see also
Bleeding the fuel system
Firstly, ensure that you have enough fuel and that all valves in the fuel lines are fully open. Try operating the lift pump lever. If it is stiff or does not move, turn the engine half a revolution by hand to move the drive cam, then try again.
If your primary fuel filter is below the fuel level in the tank and the fuel is drawn directly from the bottom of the tank, you can fill the primary filter by opening the bleed screw. You will see the bowl fill with fuel, and once clean, bubble-free fuel starts to flow from around the bleed screw, close it.
Next, move on to the secondary filter. Open the bleed screw and operate the lift pump. This may take several minutes, especially if the primary filter also needed filling. Fuel should start appearing around the bleed screw; once this is free of bubbles, close the screw.
For certain engine types, such as Yanmar GM, Perkins, Thornycroft and Kubota-based units, you will also need to prime the injection pump. To do this, open the injection pump bleed screw and operate the lift pump until clear fuel emerges. Older pumps may have two screws, which should be bled one after the other, starting with the bottom one.
Now try starting the engine. If it runs smoothly, you are done. If not, switch it off and bleed the high-pressure part of the system. Loosen the injection pipe nuts by a few turns, open the throttle fully in neutral, and crank the engine. Use short bursts to avoid damaging the starter motor.
Once you see spurts of clean fuel coming from around the injection pipes, tighten the nuts and start the engine. Keep a safe distance from the injection pipe nuts while cranking the engine, as the fuel pressure is high enough to pierce your skin.
And that's it! You have successfully bled the fuel system, an important step in servicing your diesel boat engine.
Moomba Boats: Are They Worth the Hype?
You may want to see also
Changing the oil and oil filter
The oil and oil filter should be changed at the end of the season, as engine oil can become contaminated with sulphur from diesel combustion, forming sulphuric acid which can accelerate corrosion.
First, run the engine up to its normal operating temperature. This will thin the oil and stir up any sludge from the bottom of the sump so that it can be removed with the oil. Warming the engine normally takes about 15 minutes.
To change the oil, use the sump plug, a cock or pump to drain it. If your engine has a pump fitted, or you can buy a pump to extract the oil through the dipstick hole.
Next, use a filter wrench to loosen the oil filter until it is just hand-tight. Place a plastic bag or absorbent pad around the filter to catch any spills, then unscrew it.
Before attaching the new filter, smear a little fresh oil onto the sealing ring. Screw the new filter in and tighten it as much as you can by hand – this is usually enough, but you can nip it up with a filter wrench if you want to be extra safe.
Finally, check your engine manual for the grade and quantity of oil required, then refill the engine. Stop just before the recommended amount and check the level with the dipstick. You may need to top up the level a few times as the oil works its way down into the crankcase.
Tips
- It is a good idea to wear gloves when changing the oil and filter, as it is a dirty job.
- Keep a maintenance log to record the date and details of the work done.
- Be vigilant and take heed of any warnings – a new sound, less water in the exhaust, or a loose nut or washer could be a sign that something is not right.
- It is also important to check the engine oil level before every trip.
The Paddle Boat Invention by Da Vinci: A Historical Perspective
You may want to see also
Checking the engine's cooling system
The marine engine's cooling system is essential to prevent overheating and ensure optimal performance. It consists of two primary components: the raw-water system and the freshwater system. Here are some detailed instructions on checking and maintaining this critical system.
Raw-Water System
The raw-water system draws in seawater through an open seacock and a seawater strainer to prevent debris from entering the engine. The seawater is then pumped through various components, such as the lube oil cooler and the heat exchanger, to cool the engine's freshwater and the exhaust gas.
Maintenance Tips:
- Regularly inspect and clean the seawater strainer to prevent clogging, which is a common cause of engine failure.
- Check the raw-water pump and impeller for wear and tear. The impeller veins should be flexible and free of cracks or breaks. Consider replacing the impeller annually or at least inspecting it before the boating season.
- When removing the raw-water pump, use a socket wrench and an impeller removal tool. Coat the inside of the new pump with glycerin or extra virgin olive oil before installation.
- Ensure all bolts and hose clamps on the pump are tightened to the correct torque specifications and in the proper sequence.
Freshwater System
The freshwater system is a closed loop that circulates freshwater through the engine to absorb heat. It consists of a reservoir tank, cylinder jacket, turbocharger, and cycle head. A thermostat regulates the flow of freshwater, and a heat exchanger cools it using the seawater from the raw-water system.
Maintenance Tips:
- Check the pressure cap on the freshwater system to ensure it is sealed properly. A faulty cap can cause the water to boil and lead to overheating.
- Change the antifreeze in the freshwater system every two years, using extended-life products and mixing with distilled water.
- The heat exchanger should be cleaned every three years. Its removal is a complex process that may require disassembling other components.
- Inspect the mixing elbow, which combines the exhaust and seawater, for scaling and corrosion. It should be replaced every three years to prevent blockages.
- Test the thermostat by removing it and boiling it in water. Measure the water temperature and the length of the opening hole to ensure it functions correctly. Replace it if it doesn't meet specifications.
Finding an Affordable Bowfishing Boat: Tips and Tricks
You may want to see also
Maintaining the engine's electrical system
The electrical system is a critical component of a diesel boat engine, and proper maintenance is essential to ensure the engine's reliability and performance. Here are some detailed instructions and tips to help you maintain the electrical system of your diesel boat engine:
Regular Visual Inspections
Perform regular visual inspections of the engine room, looking for any signs of wear, corrosion, or loose connections. Check the wires to critical components such as the oil pressure switch, cooling water temperature switch, and battery switch. Ensure all connections are tight and free of dirt and grime.
Battery Maintenance
The battery is the heart of the electrical system. Keep it fully charged or trickle-charged to maintain optimal performance. Check the battery terminals for any signs of corrosion and clean them if necessary. Use a multimeter to check the open-circuit voltage of the battery. Additionally, if you have a wet-cell battery, check the electrolyte levels and add distilled water if needed.
Alternator and Belts
The alternator plays a crucial role in charging the boat's batteries. Ensure the alternator is securely mounted, and the bolts are properly torqued. Inspect the belts for any signs of wear, cracking, or looseness. V-type belts should be able to deflect about 12 mm when pressed with your finger, while flat belts should be able to twist through 90 degrees. Tighten belts if necessary, using a belt tension jack.
Fuses and Solenoids
Check all fuses in the electrical system and replace any blown fuses. Inspect the starter motor for any issues, such as a bad solenoid or a faulty Bendix drive, and replace or repair as needed.
Preventative Maintenance
Preventative maintenance is key to avoiding electrical issues. Refer to your engine's service manual for specific maintenance tasks and intervals. Take photos of the engine and its components before and after maintenance work for future reference. Additionally, keep a comprehensive maintenance logbook, recording all work done, any issues encountered, and follow-up actions.
Safety Precautions
Always exercise caution when working on the electrical system. Ensure the battery switch is off before performing any maintenance. Be mindful of high-current electrical connections, as corrosion or loose connections can lead to voltage drop and affect the engine's performance. When tightening bolts, follow the specified torque specs and tightening sequence provided in the engine manual.
A Boy's Harrowing Tale of Survival at Sea
You may want to see also