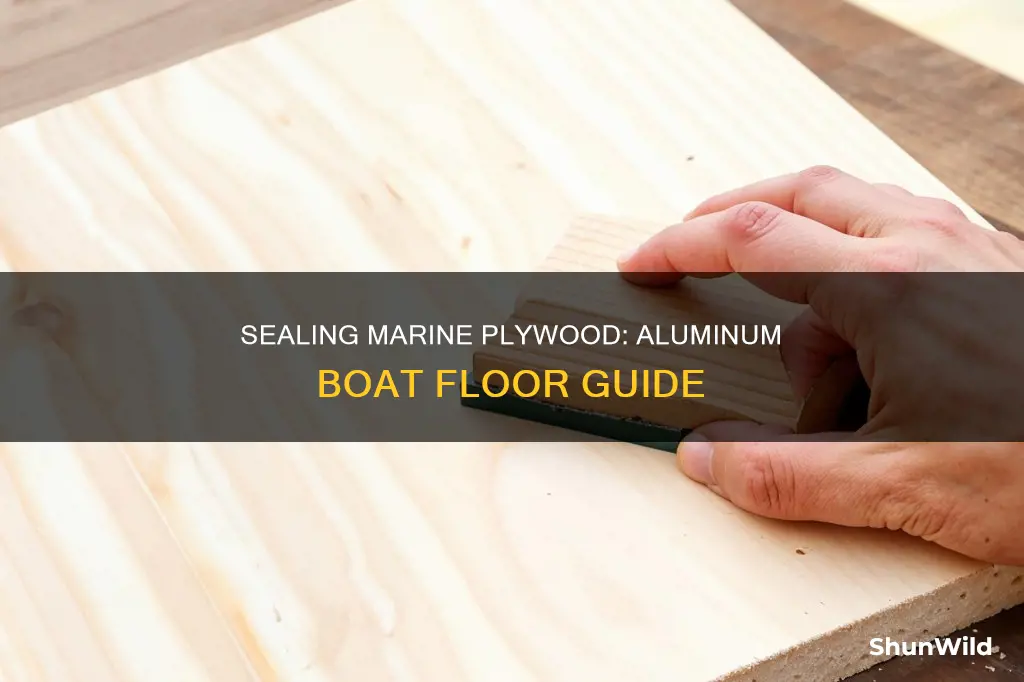
Sealing marine plywood in an aluminum boat floor is a meticulous process that requires careful preparation and treatment to ensure maximum durability and protection. The process involves several steps, starting with the selection of suitable materials and ending with the application of a topcoat. The specific steps include preparing the substrate, priming, patching, and profiling, broadcasting rubber granules, applying a liquid rubber base, and finally, applying a topcoat. The choice of sealant is crucial, with options such as clear, penetrating epoxy, marine-grade sealer, and bed liner material. Proper sealing of marine plywood can increase its lifespan and ensure it withstands moisture and water exposure.
What You'll Learn
- Prepare the surface by removing loose material and cleaning with acetone
- Sand the plywood and surrounding aluminium for better adhesion
- Prime the plywood and aluminium with a waterproof adhesive
- Seal with a clear, penetrating epoxy or marine-grade sealer
- Apply multiple coats, scuffing with sandpaper between each layer
Prepare the surface by removing loose material and cleaning with acetone
Preparing the surface of your marine plywood for sealing is a crucial step in ensuring the effectiveness and longevity of the seal. Here's a detailed guide on how to prepare the surface by removing loose material and cleaning with acetone:
Removing Loose Material
Start by removing any loose or crumbly material from the surface of the plywood. This includes debris, dirt, or any previously applied products. It is essential to ensure that the plywood surface is completely clean and dry. If there are any holes or cracks in the plywood, fill them with an appropriate wood filler or putty before proceeding.
Sandblasting or Sanding
For best results, if your boat floor is made of aluminum, consider sandblasting the surface. Sandblasting provides an ideal texture that promotes strong adhesion for the sealant. If sandblasting is not feasible, you can use coarse sandpaper (80-grit) to replicate this effect. Sand the surface evenly, creating a rough texture that will help the primer and sealant adhere more effectively. Make sure to sand both sides of the plywood, including the edges.
Cleaning with Acetone
Once the surface is prepared, it's time to clean it with acetone. Dip a paper towel or a soft cloth into acetone and wipe down the entire surface of the plywood. This will help remove grease, stains, and any remaining dirt or dust. Ensure you cover all areas, including the edges and any hard-to-reach corners. Allow the acetone to dry completely for at least 1-2 hours before proceeding to the next step.
By following these steps, you will ensure that the surface of your marine plywood is properly prepared for sealing. A clean and roughened surface will provide a strong foundation for the subsequent layers of primer and sealant, ensuring maximum protection for your aluminum boat floor.
Why Aluminum Boats Float: Science Explained
You may want to see also
Sand the plywood and surrounding aluminium for better adhesion
Sanding the plywood and surrounding aluminium in your boat is a crucial step to ensure better adhesion of the sealant. Here's a detailed guide to help you through the process:
Before you begin, it's important to understand why sanding is necessary. The process of sanding creates a rough texture on the surface of the plywood and aluminium, which helps the primer and sealant adhere more effectively. This is especially important for aluminium surfaces, as they can be smooth and need some texture to help the sealant grip.
First, let's talk about the tools you'll need. You can use coarse sandpaper or opt for power tools like an orbital sander or a belt sander, depending on the size of the area you need to cover. If using sandpaper, choose a suitable grit size. Start with a coarser grit to remove any imperfections, and then switch to a finer grit for a smooth finish. For aluminium, you can use silicon carbide sandpaper, which is great for sanding metal surfaces.
Now, let's get into the process:
- Clean the surface: Start by removing any dust, debris, or grease from the plywood and aluminium surface. You can use a soft brush or a damp cloth to wipe away loose particles. Ensure the surface is completely dry before moving on to the next step.
- Sand the plywood and aluminium: Using your chosen sandpaper or power tool, begin sanding the plywood and surrounding aluminium. If using sandpaper, hold it firmly with one hand and use the other hand to apply even pressure as you move the sandpaper in long, straight strokes. Always follow the direction of the wood grain to avoid scratches. For aluminium, you can sand in a back-and-forth motion, following the grain of the metal. Remember to wear protective gear, including a dust mask, safety glasses, and gloves.
- Check for smoothness: After sanding a section, run your hand over it to feel for any rough spots or imperfections. If you find any, continue sanding until the entire surface is uniformly smooth.
- Repeat as needed: Depending on the condition of the plywood and aluminium, you may need to repeat the sanding process with progressively finer grit sandpaper to achieve the desired smoothness.
- Remove dust: Once you're satisfied with the smoothness, use a soft brush or a vacuum to remove any remaining dust or debris from the sanded surfaces. It is crucial to ensure that the surface is entirely free of dust before applying any sealant or primer.
Remember to take your time during the sanding process and work systematically. Avoid applying too much pressure when sanding, as it can cause uneven results. Additionally, be cautious not to sand against the grain, as this can lead to scratches and an uneven finish.
By following these steps, you will effectively prepare the plywood and aluminium surface for better adhesion of the sealant, ensuring a long-lasting and protective finish for your boat floor.
Boat Registration: Understanding the Rules for Smaller Vessels
You may want to see also
Prime the plywood and aluminium with a waterproof adhesive
To seal marine plywood in an aluminium boat floor, one of the key steps is priming the plywood and aluminium with a waterproof adhesive. This step is crucial for ensuring the effectiveness and longevity of the seal, as well as creating a strong bond between the materials. Here is a detailed guide on how to do it:
Firstly, it is important to prepare the surface by removing any loose or crumbly material. Ensure that the aluminium and plywood are clean, dry, and free from any previously applied products or foreign substances. This step is crucial for the adhesion of the primer and will ensure that your boat floor remains waterproof. For aluminium surfaces, it is recommended to use sandblasting as it provides an ideal texture that promotes strong adhesion. If sandblasting is not feasible, you can use coarse sandpaper to create a rough texture on the surface.
Once the surface is prepared, it's time to prime the plywood and aluminium. Select a high-quality waterproof adhesive suitable for both materials. Apply a coat of the adhesive to the aluminium surface, following the manufacturer's instructions for proper application. Ensure that the adhesive is applied evenly and thoroughly to create a strong bond.
After applying the adhesive to the aluminium, it's important to allow it to dry or cure according to the manufacturer's instructions. This step is crucial, as it will ensure that the adhesive is set correctly and will provide a strong base for the next steps.
Next, apply the same waterproof adhesive to the plywood surface, ensuring that it is applied evenly and thoroughly. Again, follow the manufacturer's instructions for proper application and allow the adhesive to dry or cure completely.
Once both the aluminium and plywood surfaces are primed and the adhesive is fully cured, you can proceed to the next step of your sealing process. Remember that proper priming is essential for creating a strong and long-lasting seal between the plywood and aluminium in your boat floor.
Dragon Boat Paddle Shopping Guide in the Philippines
You may want to see also
Seal with a clear, penetrating epoxy or marine-grade sealer
Sealing marine plywood in an aluminium boat floor with a clear, penetrating epoxy or a marine-grade sealer is a detailed process that requires careful preparation and treatment. Here is a step-by-step guide:
Step 1: Prepare the Surface
Start by cleaning the surface of the marine plywood to remove any grease or stains. Use a soft cloth or paper towel dipped in acetone and wipe down the wood. Allow the acetone to dry completely for 1-2 hours. Next, sand both sides of the wood, including the edges, using 80-grit sandpaper. This step is crucial to ensure the surface is ready for the sealant. Finally, wipe away all dust and particles with a soft, clean cloth.
Step 2: Apply the First Coat
For the sealant, you can choose between clear, penetrating epoxy or a marine-grade sealer. The clear epoxy works its way deep into the wood, dries transparent, and requires less maintenance. On the other hand, the marine-grade sealer will require more coats and needs to be reapplied every 3 to 4 years. Regardless of your choice, dip your foam brush or roller into the sealant and start applying it to the wood. Begin with the top and side edges, and then move on to the front face. Allow the sealant to dry completely before flipping the plywood over and applying it to the bottom edge and back.
Step 3: Add Additional Coats
Marine plywood is thicker than standard plywood, so it's essential to add more coats to maximise its lifespan. A good rule of thumb is to apply as many coats of sealant as there are layers of plywood. For example, if your plywood has 7 layers of wood, add 7 layers of sealant. Gently scuff the wood with sandpaper between each coat to enhance adhesion, and remember to wipe off any dust before adding the next layer.
Step 4: Finalise the Process
Once you've applied all the necessary coats of sealant, let it cure completely. This process may vary depending on the product you've chosen, so refer to the manufacturer's instructions. After curing, your marine plywood should now be properly sealed and protected. This process will extend the lifespan of the wood and ensure it withstands moisture and water exposure.
Repairing a Leaking Boat: A Step-by-Step Guide
You may want to see also
Apply multiple coats, scuffing with sandpaper between each layer
When sealing marine plywood in an aluminium boat floor, the application of multiple coats is essential to maximise the plywood's lifespan and ensure adequate protection against moisture and water exposure. Here is a detailed guide on how to achieve this:
Before you begin, gather the necessary materials: soft cloths or paper towels, clear penetrating epoxy, and a foam brush or roller. It is also important to ensure that the aluminium surface is clean, dry, and free from any foreign substances.
Start by applying the first coat of sealant to the plywood. Dip your foam brush or roller into the clear penetrating epoxy and apply it evenly to the wood, covering all surfaces, including the edges. Allow the epoxy to dry completely before turning the plywood over and applying the sealant to the other side. This initial coat serves as a foundation for subsequent layers.
Once the first coat is dry, gently scuff the surface of the plywood with fine-grit sandpaper (around 80-grit). This process helps create a rough texture that enhances the adhesion of the next coat. Be sure to wipe away any dust or particles with a soft cloth before proceeding.
Apply the second coat of sealant using the same technique as the first. Ensure that you are generous with the epoxy, as you want to work it deep into the wood. Allow this coat to dry completely as well.
Repeat the process of scuffing the plywood with sandpaper and wiping away any dust. This step is crucial for maximum adhesion and helps create a strong bond between the layers of epoxy.
Continue applying additional coats of epoxy, scuffing with sandpaper between each layer, and ensuring that each coat is completely dry before proceeding. A good rule of thumb is to apply as many coats of sealant as there are layers of plywood. For example, if your plywood has seven layers of wood, aim for seven layers of sealant.
By following these steps and applying multiple coats, scuffing with sandpaper between each layer, you will effectively seal the marine plywood in your aluminium boat floor. This process will help extend the lifespan of the plywood, ensuring it withstands moisture and water exposure, and providing a durable finish that can withstand harsh marine conditions.
The Luxury Yacht Kogo: Who Owns It?
You may want to see also
Frequently asked questions
You will need soft cloths or paper towels, clear penetrating epoxy, and a foam brush or roller. Additionally, for maximum adhesion, you may want to use sandpaper and a sealant such as SANI-TRED® marine plywood deck paint, which includes PermaFlex®, LRB (Liquid Rubber Base), TAV (Thickening Activator), and Rubber Granules.
First, clean the surface of the plywood by wiping it down with a soft cloth dipped in acetone to remove any grease or stains. Allow it to dry completely before sanding both sides of the plywood with 80-grit sandpaper. Next, apply a coat of clear penetrating epoxy to all surfaces of the plywood, allowing it to dry before flipping and coating the other side. Repeat this process, adding as many coats of sealant as there are layers of plywood. Finally, gently sand the plywood between each coat for better adhesion and wipe off any dust before applying the next layer.
Start by removing any loose or crumbly material from the surface of the aluminum boat floor. Ensure that the surface is clean, dry, and free from any previously applied products or foreign matter. For the best results, sandblast or use coarse sandpaper to create a rough texture that promotes strong adhesion for the sealant.
Alternative methods include using marine-grade sealer, resin, fiberglass, poly resin, or a combination of resin and fiberglass. You can also use a product like Durabak-18 as a bedliner material for the top surface.