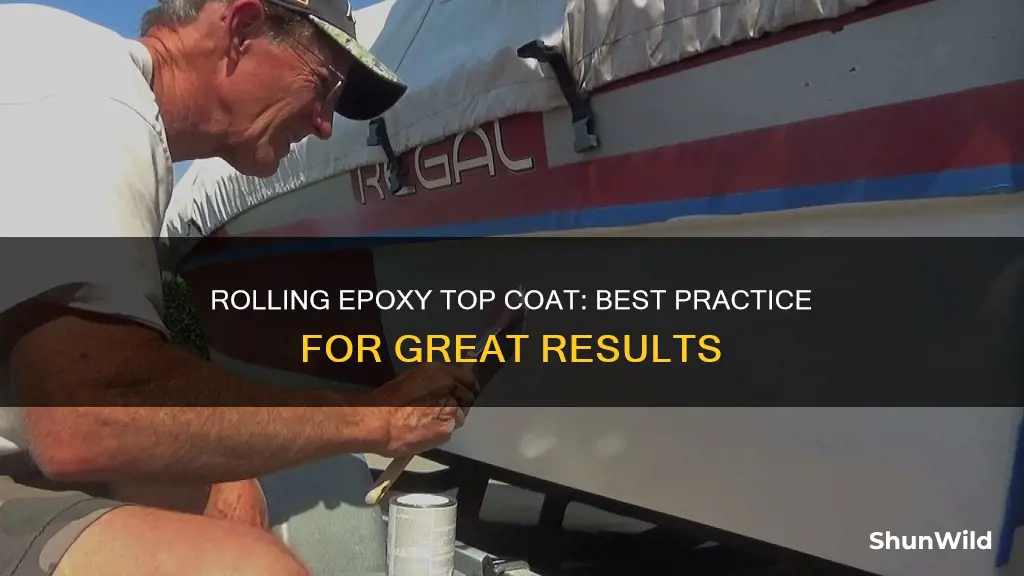
Applying an epoxy top coat to your boat is a delicate process that requires careful preparation and execution. The first step is to ensure that your boat's surface is properly prepared, filling in any scratches, dings, or dents with an epoxy fairing compound and sanding the surface smooth. The next step is to mix your epoxy, following the manufacturer's instructions for the correct ratio of base to curing agent. Once your epoxy is mixed, you can apply it to your boat using a roller, brush, or spray. It is important to work quickly as the epoxy will begin to cure shortly after mixing. For best results, apply multiple thin coats of epoxy, allowing each coat to dry thoroughly before applying the next. Finally, after the final coat has dried, sand the surface with fine-grit sandpaper to ensure a smooth finish.
Characteristics | Values |
---|---|
Application Methods | Brush, roll, or spray |
Nap Size | 3/16" to 3/8" |
Roller Type | Solvent-safe |
Number of Coats | 2-5 |
Film Thickness | 2.5-4 mils dry per coat |
Dry Time to Recoat | 2-6 hours at 90ºF |
Dry Time to Overcoat | 3-10 hours at 90ºF |
Dry Time to Launch | 12 hours at 90ºF |
Thinner | TotalBoat Epoxy Primer Thinner 200 |
What You'll Learn
Ensure your epoxy is fully cured to avoid amine bleed-through problems
When applying an epoxy top coat to your boat, it is crucial to ensure that the epoxy is fully cured to prevent amine bleed-through issues. Amine blush is a waxy film that can form during the curing process, and if not removed, it can cause adhesion problems and a cloudy finish.
To ensure your epoxy is fully cured, follow these steps:
- Allow sufficient curing time: For DIY projects, it is recommended to allow a full seven-day curing period before applying any additional coats or finishes. This will prevent the epoxy from reacting when other products, such as a polyester gel coat, are applied on top.
- Measure and mix accurately: Carefully measure and thoroughly mix the epoxy resin and hardener according to the manufacturer's instructions. An accurate ratio of resin to hardener is essential for the epoxy to cure properly.
- Control the temperature: The curing process is affected by temperature. In warm temperatures, epoxy cures faster, while in cool temperatures, it cures slower. Maintain an ideal temperature of around 15°C (59°F) for the best results.
- Post-curing: Even after the epoxy appears cured, there may still be small amounts of uncured epoxy and unreacted groups present. Therefore, consider post-curing the surface by exposing it to elevated temperatures to ensure a thorough cure.
- Remove amine blush: After the initial curing phase, wash the surface with clean water and an abrasive pad to remove any amine blush. Dry the surface with paper towels and sand any remaining glossy areas to ensure a dull finish.
- Test for curing: If you are unsure whether the epoxy is fully cured, you can perform a simple test. Try to dent the surface with your thumbnail. If it leaves an indentation, the epoxy is not fully cured. If it returns to its original shape without any marks, the epoxy is fully cured.
By following these steps and allowing adequate curing time, you can ensure that your epoxy boat top coat is fully cured and ready for further finishing or painting. A properly cured epoxy surface will provide a strong, durable, and water-resistant foundation for your boat.
Bass Boat Weight: How Much Do They Weigh?
You may want to see also
Use a roller designed for epoxy for best results
When applying an epoxy top coat to your boat, it is important to use a roller designed for this specific task. Using the correct roller will ensure a smooth and even finish, without leaving any streaks or brush tracks.
There are a variety of rollers available that are specifically designed for use with epoxy. These rollers are typically made from materials such as foam, polyester, or microfiber, and have a nap length between 1/4" and 3/8". It is important to choose a roller with the appropriate nap length for the surface you are coating. For example, if you are coating a smooth surface, a roller with a shorter nap length, such as 1/4", would be a better choice. On the other hand, if you are coating a textured surface, a longer nap length of 3/8" would be more suitable.
Additionally, it is recommended to use a roller with a hard texture for applying epoxy to smooth surfaces. This will help ensure an even and consistent finish. You can find epoxy rollers in a variety of sizes, typically ranging from 4 inches to 18 inches in width. Make sure to choose a roller that is compatible with the size of your boat and the surface area you need to cover.
When using an epoxy roller, it is important to roll out the epoxy sufficiently to avoid applying too thick of a coating. A thin coat of epoxy will result in a smoother finish and will be easier to sand down if needed. It is also a good idea to sand between coats of epoxy to create an even smoother surface for the final top coat.
By following these instructions and using a roller designed for epoxy, you will achieve the best results when applying an epoxy top coat to your boat.
Catching Sea Bass: Boat Fishing Techniques for UK Anglers
You may want to see also
Use a plastic spreader to move epoxy across the work
When applying epoxy, it's important to use the right tools to get the best results. In this case, a plastic spreader is a great option to move the epoxy across the workpiece and ensure a smooth, even finish. Here's a step-by-step guide on how to use a plastic spreader effectively:
Prepare the Workpiece
Before you begin, ensure that your workpiece is clean, dry, and level. This is crucial for achieving the best results. Any dirt, dust, or uneven surfaces can affect the final finish of your project. Take the time to thoroughly clean and prepare the surface, as this will pay off in the long run.
Mix the Epoxy and Hardener
The next step is to carefully measure and mix your resin and hardener. It's important to follow the manufacturer's instructions and mix the two components in the correct ratio. Epoxy and hardener are usually mixed in equal parts, but always double-check the product instructions to be sure. Thorough mixing is essential to ensure a consistent finish.
Pour the Epoxy
Once your epoxy is mixed, carefully pour it onto the centre of your workpiece. Start by pouring in the middle and work your way outwards. This will help you achieve an even coating. Don't be afraid to pour on the epoxy; you can always spread it out to your desired thickness.
Use a Plastic Spreader to Move the Epoxy
Now it's time to grab your plastic spreader. A plastic spreader is an ideal tool for moving epoxy across your workpiece and creating an even coating. Gently guide the epoxy with the spreader, using smooth, even strokes. Work the epoxy towards the edges of your workpiece, ensuring that it is distributed evenly. Remember, you have a limited time to work with the epoxy before it starts to cure, so work efficiently.
Tips for Using a Plastic Spreader
- Choose a flat, smooth plastic spreader that is specifically designed for epoxy. Reusable spreaders are available, which can be a cost-effective and eco-friendly option.
- Hold the spreader at a slight angle to the workpiece to ensure a smooth, even finish.
- Work quickly but carefully. Epoxy has a limited working time, so you'll need to move it across the surface before it starts to cure and becomes too thick.
- If you need to coat a large area, consider using a longer spreader or a roller designed for epoxy to speed up the process.
- Always clean your spreader immediately after use. Epoxy hardens quickly, and you don't want it to cure on your tools.
By following these steps and using a plastic spreader effectively, you'll be able to achieve a beautiful, smooth finish on your boat top coat. Remember to take your time, work in a well-ventilated area, and always follow safety precautions when working with epoxy.
Fresh Off the Boat Filming Locations: UCLA Campus
You may want to see also
Sanding is important for a smooth finish
Sanding is necessary to smooth out the rough surfaces and imperfections that can occur when working with epoxy. It is particularly important when creating a top coat for a boat, as a smooth finish is essential for both aesthetic and functional reasons. By sanding the epoxy, you can create an even and consistent surface that will enhance the overall appearance of the boat.
The sanding process involves using sandpaper or sanding discs of varying grit sizes to gradually smooth out the epoxy surface. It is important to start with a coarse grit, such as 120-grit, and then progress through finer grits, such as 180-grit, 240-grit, and so on. This gradual progression ensures that deeper scratches and imperfections are removed first, and then finer scratches are addressed to create an increasingly smooth surface.
The type of sanding method used is also important. Dry sanding, where the surface is completely dry, can be effective in removing rough surface imperfections. However, it creates a lot of dust that can be dispersed into the air and inhaled, posing health risks. On the other hand, wet sanding involves moistening the surface before sanding, which helps to reduce dust and allows the dust to be "collected" by the water. While wet sanding can clog the sanding material more quickly, it is generally safer and allows for better visibility of the sanding progress.
When sanding epoxy, it is crucial to take the necessary safety precautions. The dust produced during the process can be toxic and harmful to your lungs, so wearing a respirator or mask is essential. Additionally, using power tools that support dust bags or extractors can help minimise the amount of dust released into the air.
By following a systematic and consistent approach to sanding, you can achieve a smooth and polished finish on your epoxy boat top coat. It is important to take the time to complete multiple passes with each grit size, overlapping your movements to ensure even sanding. Regularly cleaning the sanding discs and the epoxy surface is also crucial to prevent clogging and build-up of dust.
In summary, sanding is an indispensable step in achieving a smooth finish on an epoxy boat top coat. By using the appropriate techniques, grit sizes, and safety measures, you can create a high-quality, polished surface that enhances the beauty and functionality of your boat.
Boat Insurance in Virginia: What's the Law?
You may want to see also
Epoxy can be used as a base for a polyurethane top coat
When it comes to boats, protecting the hull from water intrusion is best done with an epoxy barrier coat. This is more effective in sealing out moisture than gel coat and is probably the single most important coating on your boat. A barrier coat seals a fibreglass hull, blocking water entry and inhibiting blister formation in underwater gel coat and fibreglass.
Epoxy is a thermosetting polymer known for its strong adhesion, chemical resistance, and durability. It’s commonly used in flooring, countertops, and furniture. Polyurethane is another versatile polymer, often used as a topcoat for its additional protective qualities. It’s available in both oil-based and water-based forms.
Applying polyurethane over epoxy is a great way to enhance the durability and scratch resistance of your epoxy projects. Polyurethane adds an extra layer of protection and UV resistance to epoxy-coated surfaces, making them last longer and look better. Polyurethane is highly resistant to scratches, making it perfect for high-traffic areas. It also offers UV resistance, preventing yellowing and degradation over time.
To achieve a flawless finish when applying polyurethane over epoxy, proper surface preparation is crucial. Start by thoroughly cleaning the epoxy surface. Any dirt, grease, or debris can interfere with adhesion, leading to a subpar finish. Sand the epoxy surface with fine-grit sandpaper to create a mechanical bond. The surface needs to be slightly rough, providing tiny grooves for the polyurethane to grip onto.
When it comes to polymer floor coatings, unique needs and circumstances dictate the best grouping of primers, basecoats, and topcoats to use to achieve the desired results. There is an extensive list of polymer flooring choices, such as vinyl esters, novalac epoxies, urethane concrete, and more to accommodate any situation.
In the case of boats, a polyurethane topcoat can be applied over an epoxy base for added protection and a flawless finish.
Boat Prop Damage: What Does Insurance Cover?
You may want to see also
Frequently asked questions
You can brush, roll, or spray epoxy onto your boat. If you choose to roll, use a 3/16" nap or foam solvent-safe roller cover.
It is recommended to apply a minimum of 2-3 coats when using a 3/8" roller cover, 3-4 coats with a 1/4" roller, and 4-5 coats with a 3/16" roller.
Ensure the surface is free of dust, wax, grease, amine blush, and water. Sand the surface and remove any residue with an appropriate solvent such as TotalBoat Dewaxer & Surface Prep.
Use a roller designed for epoxy application, such as a Gougeon foam roller or a 3/16" nap or foam solvent-safe roller cover.
After applying the epoxy, use a plastic spreader or a metal cabinet scraper to smooth out any ridges or bumps. Then, sand the surface with fine-grit sandpaper to create a smooth and fair finish.