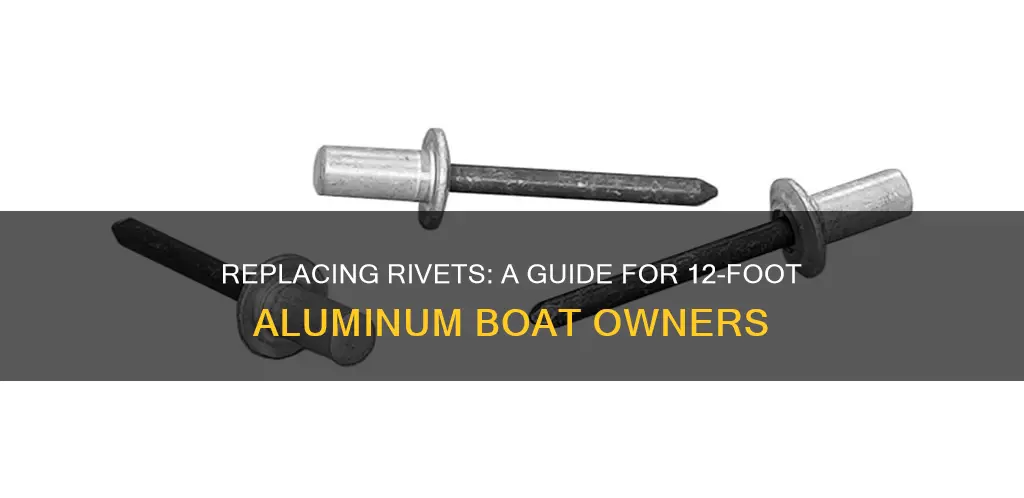
Owning a boat is a dream for many, but it's also a lot of work. One common issue with aluminium boats is leaking rivets. While some people choose to repair these with products like JB Weld, a more permanent solution is to replace the rivets. This can be done with a rivet gun or by hand with a hammer and mallet. It's important to use aluminium rivets to avoid a chemical reaction that could lead to rapid corrosion. Drilling out the old rivets and replacing them one at a time is also recommended to avoid alignment issues. With the right tools and some time, you can have your aluminium boat back in the water in no time!
Characteristics | Values |
---|---|
Tools required | Rivet gun, air hammer, 2 hammers, 2-pound mallet, heavy hammer, concave bar, chisel, air compressor, pneumatic rivet gun, pneumatic puller, heavy-duty manual puller, automatic center punch, small center punch, sharp chisel, drill, screwdriver, open-end wrench, angle grinder, wire brush, air riveter |
Materials required | Zinc-based soldering rods, Aluma-Fix, filler, aluminium rivets, sealant, epoxy, aluminium putty repair kit, closed-end pop rivets, solid rivets, blind rivets, stainless steel bolts, washers, nuts, 5200 sealant, 520, 3M 5200, aluminium screws, aluminium truss head Phillips screws, flat washers, nylon locking nuts, lacquer thinner, alodine, epoxy, aluminium primer, aluminium paint, aluminium chromate primer spray, aluminium, aluminium weld filler, Duraflex, aluminium weld filler, clecos, aluminium rivets, aluminium bolts, aluminium nuts, aluminium washers |
Techniques | Drilling out old rivets, vigorous wire brushing, re-setting existing rivets, using sealant to keep out moisture and debris, cleaning aluminium, priming with zinc chromate or epoxy primer, stop drilling cracks, bucking rivets, beheading rivets, drilling out rivets, filling holes with JB Weld, using bolts, tapping shank of rivet, hammering rivet, flattening shank, using closed-end pop rivets, using solid rivets, using blind rivets, using stainless steel bolts, filling holes with JB Weld, using bolts, using aluminium rivets, welding, chemically treating aluminium, using alodine, using self-etching primer, using zinc chromate, using aluminium chromate, using aluminium weld filler, using clecos, using aluminium rivets, using aluminium bolts, using aluminium nuts, using aluminium washers |
What You'll Learn
How to identify a leaking rivet
Owning a boat is a lot of fun, but it also comes with maintenance and repair work. If you have a 12-foot aluminum boat, you may eventually need to replace some of the rivets due to leaks. But how do you identify a leaking rivet? Here are some methods to help you locate those troublesome leaks:
The Water Test
One common way to find leaking rivets is to perform a simple water test. This can be done by filling your boat with water while it's on a trailer or beached. Fill it up to the waterline, and then carefully observe and mark any rivets that are leaking. If you don't want to fill the entire boat with water, you can also perform this test in sections by gradually sliding the boat into the water, foot by foot, and marking the leaking rivets as you go. Alternatively, if your boat is off the ground, you can fill it with water and mark the leaking rivets from the inside.
The Suction Cup Method
If filling your boat with water is not an option, there's another clever way to identify leaking rivets. You can use a small suction cup-type dent puller for this test. Place the suction cup over a rivet and pull a vacuum. If the rivet holds the vacuum seal, it's intact. However, if it fails to hold the seal, that particular rivet will leak. Mark any rivets that don't hold the seal, and you'll know which ones need attention.
Visual Inspection
In some cases, you may be able to spot leaking rivets simply by looking at them. Over time, wear and tear can loosen rivets, creating gaps that allow water to seep through. These gaps or spaces around the rivets can be a clear indication that they are not sealing properly and need to be replaced or repaired.
Once you've identified the leaking rivets, it's important to clean and prepare the area before repairing or replacing them. You can use a wire brush to clean the surface and expose bright metal around the rivet. This will help create a better bond when you apply an epoxy sealer or install new rivets.
By following these methods, you can efficiently identify leaking rivets on your 12-foot aluminum boat and take the necessary steps to fix them, ensuring your boat remains seaworthy and safe for your adventures on the water.
Exploring Hayden: Boat Launching on McKenzie River
You may want to see also
Tools and equipment needed to replace rivets
To replace rivets on a 12-foot aluminum boat, you will need a variety of tools and equipment. Here is a list of the essential items:
- Rivets: Ensure you have the correct type and size of rivets for your boat. Solid rivets are ideal for areas where you can access both sides. Closed-end, blind rivets are suitable for areas where you can only access one side. Brazier head rivets are commonly used for boat hulls and are typically made of aluminum with a steel mandrel.
- Rivet Tools: You will need tools to set the rivets. For solid rivets, you can use two ball-peen hammers or an air hammer with a bucking bar. For blind rivets, a hand riveter or pneumatic/hydraulic riveter may be required, especially for larger diameters.
- Drills and Drill Bits: Drills and appropriate drill bits are necessary for drilling out old rivets and creating new holes. Center punches can help mark the center of the rivets for accurate drilling.
- Cutting Tools: Sharp wood chisels or cutting wheels can be used to cut off rivet heads before punching out the remaining shaft.
- Measuring Tools: Calipers or measuring tapes can help determine the size and length of the rivets needed.
- Cleaning and Prepping Supplies: Clean and prepare the surfaces before riveting. This may include wire brushes, sandpaper, solvents, and primers like zinc chromate or epoxy primer.
- Safety Equipment: Wear appropriate safety gear such as ear protection and eye protection when working with power tools. Gloves can also protect your hands during the riveting process.
Additionally, you may need a helper for certain tasks, especially when bucking rivets, as it often requires coordination between two people.
Repairing Aluminum Boat Corrosion: A Comprehensive Guide
You may want to see also
The process of replacing rivets
Firstly, you will need to identify which rivets need to be replaced. Fill the boat with water and use a knife to pop the heads off the leaking rivets. You can then punch out the remainder of the rivet. It is important to not distort the hole when doing this.
Next, you will need to source replacement rivets. Make sure to use aluminium rivets to prevent rapid corrosion. The rivets should be total thickness + 125% of the rivet diameter long. You will also need various tools, including a rivet gun, air hammer, and a concave or flat hammer.
Now, you are ready to begin the process of riveting. This will require two people. One person will need to be inside the boat, holding a piece of steel or a bucking bar against the shank of the rivet. The other person will be outside the boat, using the hammer to hit or 'buck' the head of the rivet. This process will need to be repeated for each rivet.
It is important to note that riveting should be done with care. Do not overdrive or over-hammer the rivets, as this can cause the metal between the rivets to upset and buckle. Additionally, make sure to use the correct size of drill bit when drilling out the old rivets to avoid enlarging the holes.
Bass Boat Restoration: Reviving the Shine
You may want to see also
The importance of sealant for water tightness
When it comes to replacing rivets on a 12-foot aluminum boat, water tightness is crucial. Ensuring that the boat is sealed properly will not only protect it from water ingress but also prevent corrosion and ensure the safety of the boat.
Using the correct sealant is vital to achieving water tightness. A proper marine sealant must be waterproof, flexible, UV resistant, and chemically resistant. It should be able to withstand exposure to fuel and other solvents commonly found in boating materials.
There are three main types of marine sealants: polyurethane-based, polysulfide-based, and silicone-based. Polyurethane-based sealants are known for their strong and permanent adhesion. They can be used both above and below the waterline and are extremely durable due to their long molecular chains. Polysulfide-based sealants are considered the best general-purpose marine sealants. They are flexible, elastic, and can also be used above and below the waterline. Additionally, they adhere well to teak and are excellent for sealing hardware and bedding wooden items. Silicone-based sealants create strong bonds when used correctly but should only be used for above-waterline purposes.
When choosing a sealant, it is important to consider the specific requirements of the boat and the areas that need sealing. Some sealants may not be compatible with certain materials, such as plastics or acrylic perspex, and could cause damage. It is also essential to consider the strength of the mechanical bond, flexibility, serviceability, and service life of the sealant.
By selecting the appropriate sealant and ensuring proper application, you can maintain water tightness in your 12-foot aluminum boat, protecting it from water damage and ensuring its longevity.
The Intricacies of a Ferry Dock
You may want to see also
The pros and cons of welding vs riveting
Welding and riveting are two of the most common methods of metal joinery. While both techniques can be used to repair a 12-foot aluminum boat, they have distinct advantages and disadvantages that should be considered before deciding on a method.
Welding
Welding is a process that uses extreme heat to melt metal and create a fused joint. It is a highly durable, strong, and permanent method that can be used on various materials, including aluminum. Welding is ideal for projects that require a sealed joint, as it does not allow liquids, solids, or gases to pass through. It is also flexible and can be used on both thin and thick materials.
Pros of Welding
- Stronger joints compared to riveting.
- Highly durable and can withstand extreme loads.
- Flexible and can be used on a variety of materials and projects.
- Seals the joint tightly, preventing leaks.
Cons of Welding
- Requires skilled labor, which can be expensive.
- Defects may be difficult to inspect and require special attention.
- Can be dangerous if proper safety procedures are not followed.
- May cause distortion, deformation, or damage to the metal due to heat and pressure.
- Initial equipment cost can be high.
Riveting
Riveting, on the other hand, is a mechanical process that uses a rivet, a metal pin with a head on one end and a cylinder on the other, to join pieces of metal. It is a semi-permanent and straightforward process that requires less skill and equipment than welding. Riveting is ideal for thinner metals and joining different metals with varying melting points.
Pros of Riveting
- Significantly lower cost than welding.
- Requires less skill and preparation.
- Suitable for joining thin or different metals.
- No post-welding cleanup is necessary.
- Semi-permanent, allowing for future disassembly.
Cons of Riveting
- More time-consuming and labor-intensive.
- Requires overlapping of pieces or the addition of extra material for butt joints.
- Weaker and less durable joints that may fail or loosen under stress.
- May create a rough and bulky joint with gaps or protrusions.
- May increase weight and noise due to the extra mass and friction of the rivet.
Both welding and riveting have their advantages and disadvantages, and the best method for repairing a 12-foot aluminum boat will depend on the specific requirements of the project. If a strong, permanent, and sealed joint is required, welding may be the better choice. However, if cost and ease of assembly are more important, then riveting could be the preferred option.
Boat Interior Lighting: Choosing the Best Color Lights
You may want to see also
Frequently asked questions
You will need a rivet gun or an air hammer, a helper, a bucking bar, and a drill. You can also use a chisel, a hammer, and a concave bar to manually replace the rivets.
It is recommended to use aluminum rivets to avoid a chemical reaction between different metals, which can lead to rapid corrosion. Solid rivets are also suggested for a stronger hold.
Leaking rivets or water ingress around the rivets are signs that they need to be replaced. It is also recommended to check for spider cracks extending from the rivet holes, as these can weaken the structure.
While products like JB Weld or epoxy can be used as a temporary fix, replacing the rivets is a more permanent and effective solution. Using a sealant like 5200 in conjunction with new rivets can provide extra insurance against leaks.
The rivets should match the diameter of the existing rivet holes. If you are drilling out the old rivets, ensure you use the correct drill bit size to avoid making the holes bigger.