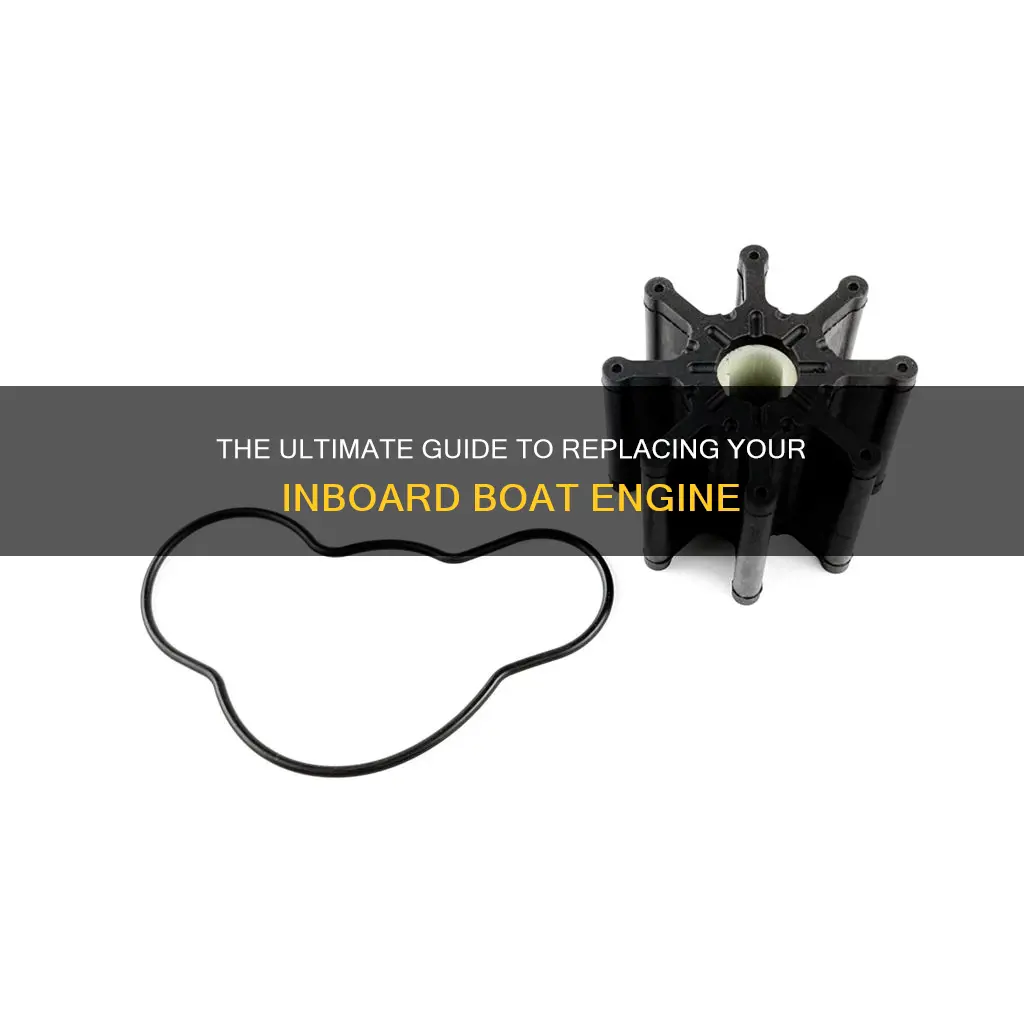
Replacing an inboard boat engine is a complex task that requires careful consideration and planning. Before embarking on this endeavour, it is essential to understand the financial implications and the level of work involved. The cost of a new engine can range from $5,000 to $15,000, and labour costs for installation can vary depending on the complexity of the job. It is also important to determine whether the engine simply needs repairs or a full replacement, as repairs may be a more cost-effective solution.
When replacing an inboard boat engine, it is crucial to have the right tools and equipment. The process involves disconnecting various components that link the motor to the boat's systems and then carefully lifting the motor out. This task may require the use of specialised equipment such as a front loader or a block and tackle. Additionally, it is important to consult manufacturer guidelines or a mechanic to ensure that the new engine is suitable for the boat and to consider the engine size, horsepower, and compatibility with other systems.
For those with reasonable practical skills and a willingness to learn, replacing an inboard boat engine can be a rewarding project that improves the boat's performance and extends its lifespan. However, it is important to thoroughly research and plan the process to ensure a successful outcome.
Characteristics | Values |
---|---|
When to replace the engine | When the engine has become costly to maintain, is not as powerful as it used to be, stutters or makes unusual noises, or keeps overheating. |
Things to consider when replacing the engine | Cost of the new engine, manufacturer guidelines, choosing the right accessories, and considering the size and dimensions of the engine. |
Cost of replacement | $5,000 to $15,000, depending on the type of engine and excluding labour costs. |
Cost of removal | $150 to $250. |
When to replace the engine | When the engine shows signs of damage or no longer performs at the required level. |
Engine type | Inboard boat engines are more expensive to replace compared to other types of engines. |
What You'll Learn
Engine removal
Before starting the process of removing your inboard boat engine, it is important to understand the complexity of the task at hand. Removing an inboard engine requires careful attention to various components and connections, and it is crucial to follow the manufacturer's instructions closely. Here is a step-by-step guide to help you through the engine removal process:
Step 1: Prepare the Boat
Position the boat's gear shift lever in forward gear. This is an important initial step to ensure the safety of the procedure.
Step 2: Access the Engine
Remove the engine cover inside the boat. This will grant you access to the engine and its surrounding components. It is advisable to remove any built-in furnishings, such as seats or sun platforms, to allow for better access to the engine from multiple angles.
Step 3: Disconnect Electrical Components
Disconnect the ground cable leading from the battery to the engine block. This is a crucial step to ensure the electrical safety of the procedure. Next, disconnect the main wiring harness connection. Once this is done, your engine should be completely disconnected from the electrical system.
Step 4: Shut Off Fuel Supply
Turn the fuel shut-off valve between the fuel tank and the motor to the off position. This will prevent any accidental fuel discharge during the engine removal process.
Step 5: Remove Fuel and Exhaust Lines
Remove the gasoline line from the inlet side of the fuel/water separating filter. You can do this by loosening the hose clamp with a flat screwdriver and then carefully working the hose free. Additionally, disconnect any rubber hoses from the exhaust manifold in a similar manner.
Step 6: Disconnect Throttle and Shift Mechanism
Remove the throttle/shift mechanism by detaching the bolts and nuts that secure it to the motor. Also, disconnect the linkage between the throttle/shift mechanism and the carburetor or throttle body.
Step 7: Disconnect Water Intake Hoses
Disconnect the water intake hoses that lead from the rear of the boat to the water pump. You can disconnect these either at the water pump itself or where they attach at the rear of the boat, whichever is more accessible.
Step 8: Remove Motor Mount Nuts
Remove the outer motor mount nuts from the motor mounts that hold the motor to the bottom of the boat and the transom. Do not change the position of the nuts under the motor's mounting brackets, as these are the engine alignment nuts.
Step 9: Prepare for Engine Lift-Out
At this point, your engine should be completely disconnected from the boat. Connect a chain to the engine lifting bracket on top of the motor and to a front loader or tractor. Alternatively, if you are in a shop, you can use an overhead chain hoist.
Step 10: Lift Out the Engine
Slowly lift the engine out of the boat, being cautious of any remaining wires or hoses that may still be connected. Ensure that none of the hoses or wires removed get caught during this process.
Once the engine is removed, take the opportunity to clean and inspect the bottom of the boat, the motor mounts, and other parts that are usually difficult to access. Also, check the bottom of the motor, the starter, oil pan, and related components.
Fixing a Boat Drive Shaft: Repairing a Broken Coupling
You may want to see also
Disconnecting components
Disconnecting the components of an inboard boat engine can be a challenging task, but with the right tools and careful planning, it can be accomplished successfully. Here is a step-by-step guide on how to disconnect the components of an inboard boat engine:
Step 1: Position the Boat's Gear Shift Lever
Place the boat's gear shift lever in forward gear. This will ensure that the propeller is locked and will not rotate during the disassembly process.
Step 2: Disconnect the Outdrive Unit
Remove the outdrive unit from the rear of the boat. Disconnect the tilt/trim cylinders and remove the nuts securing the outdrive to the gimbal. Carefully pull out the outdrive and driveshaft from the rear of the boat.
Step 3: Access the Engine
Remove the engine cover inside the boat. Take out any seats, sun platforms, or built-in furnishings that may obstruct access to the engine. It is important to have clear access to the engine from all sides to facilitate the disconnection process.
Step 4: Disconnect the Ground Cable
Locate the ground cable that connects the battery to the engine block. Carefully disconnect this cable, ensuring that the connection is completely severed.
Step 5: Disconnect the Main Wiring Harness
Disconnect the main wiring harness connection. This step is crucial as it ensures that the motor is completely electrically disconnected from the boat.
Step 6: Shut Off the Fuel Supply
Turn the fuel shut-off valve between the fuel tank and the engine to the "off" position. This will prevent any accidental fuel discharge during the disassembly process.
Step 7: Remove the Gasoline Line
Using a flat screwdriver, loosen the hose clamp connecting the gasoline line to the fuel/water separating filter. Carefully work the hose free from the hose barb.
Step 8: Disconnect the Throttle/Shift Mechanism
Remove the bolts and nuts securing the throttle/shift mechanism to the engine. Also, disconnect the linkage between the mechanism and the carburetor or throttle body.
Step 9: Disconnect the Exhaust Hose(s)
If your boat has a V-6 or V-8 engine, it will have multiple rubber hoses connected to the exhaust manifold. Use a flat screwdriver to loosen the hose clamp and carefully work the hose free from the nipple.
Step 10: Disconnect the Water Intake Hoses
Disconnect the water intake hoses that lead from the rear of the boat to the water pump. You can disconnect them either at the water pump itself or where they attach at the rear of the boat, whichever is more accessible.
Step 11: Remove the Motor Mount Nuts
Remove the outer motor mount nuts from the motor mounts that hold the motor to the bottom of the boat and the transom. Do not change the position of the nuts under the motor's mounting brackets, as these are crucial for engine alignment.
At this point, the motor should be completely disconnected from the boat and ready to be lifted out. Ensure that all wires and hoses have been disconnected before proceeding with the removal of the engine.
Football Star's Extravagant Vessel: Sunday Money
You may want to see also
Engine installation
Before you begin the installation process, it is important to understand the basic differences between inboard and outboard engines. Inboard engines are installed within the hull of the boat, while outboard engines are attached to the outside of the boat, typically at the stern. Outboard engines are generally easier to maintain, offer better fuel efficiency, and provide improved manoeuvrability. However, the conversion process can be intricate and time-consuming, so carefully consider the advantages and disadvantages before deciding to switch.
When installing an inboard engine, the first step is to measure and prepare. Determine the installation dimensions, paying close attention to the propeller shaft height, the rotation direction of the propeller, and the propeller shaft and bearing. Ensure that the engine matches the propeller shaft height by checking if the reverse clutch output and the crankshaft are at the same height.
Next, consider the tilt of the engine when sailing. Check the maximum tilt specified in the manual and ensure the engine can handle it. Be cautious when dealing with a 'Z-drive' and carefully review the specifications. If you are maintaining the same power direction, you can typically use the existing supply and return connections, such as the exhaust gas outlet and cold water inlet.
When it comes to the propeller shaft and bearing, think about how you will connect the propeller to the reverse gear. Some brands are interchangeable, but you may need an adapter flange if they are not. Consider using a thrust bearing with a homokinetic drive to reduce vibration and simplify the connection process.
The next step is to remove the existing inboard engine. Follow the manufacturer's instructions and take your time with this complex task. Disconnect the engine from the propeller shaft, remove any attached components, and carefully lift the engine out of the boat. Seal any holes or openings in the hull with a marine sealant to prevent water ingress and potential damage.
Now you are ready to install the new inboard engine. Mount the engine to the hull of the boat, following the manufacturer's instructions and ensuring a secure fit. Connect the engine to the boat's controls, including the throttle and steering cables. Test these connections before proceeding to the next step.
Finally, start the engine and check for any unusual noises or vibrations. Test the boat's performance on the water, monitoring the engine's performance and making any necessary adjustments to optimise fuel efficiency and overall performance. Remember to always prioritise safety when working on your boat, wearing the appropriate gear and ensuring the boat is out of the water.
Pursuit 21 Center Console: A Good Boat?
You may want to see also
Engine alignment
Understanding Shaft Droop
The weight of the shaft and couplings, typically made from iron alloys, can cause them to sag. This shaft droop or sag can be significant, depending on the distance between the forward-most bearing and the coupling. It is crucial to account for this droop during the alignment process.
Optical or Laser Alignment
Optical or laser alignment gear can be used to "sight through" the bearings supporting the shaft, up to the transmission output coupling. This method ensures that the shaft droop is eliminated and the couplings are centred relative to each other.
Shaft-to-Bearing Alignment
This type of alignment requires more specialised skills, tools, and experience. It involves assessing the relationship between the shaft and the bearing(s) supporting it, as well as the relationship between the shaft and the engine.
- Inspect Motor Mounts: Check the motor mounts or "isolators" for any signs of deterioration, such as rusty adjustment stud threads or cracked, oil-soaked, or collapsed rubber material. If the mounts are compromised, replace them before proceeding.
- Separate the Couplings: Remove the coupling bolts and separate the engine coupling from the shaft coupling. Inspect the fasteners for any damage and replace if necessary.
- Inspect Flange Surfaces: Ensure that all flange surfaces, including the pilot bushing and pilot receiver, are free from dents, dings, scoring, or corrosion. These surfaces must be capable of engaging each other snugly. If there is any doubt, have the shaft coupling analysed and repaired by a propeller shaft machine shop.
- Lubricate the Couplings: Spray the faces and pilot bushing with a light lubricant to aid in engagement and rotation during alignment.
- Pre-Position the Engine Coupling: Use optical or laser alignment to position the engine coupling relative to the shaft centreline. Alternatively, apply upward force to the shaft to account for shaft sag.
- Press Couplings Together: Press the two coupling faces together tightly and rotate the shaft coupling against the transmission coupling by hand several times to ensure a good fit.
- Insert Feeler Gauge: Insert the thickest feeler gauge that fits into the gap between the two coupling faces. A maximum misalignment of approximately 0.001" per inch of coupling face diameter is acceptable, with an overall maximum of 0.004". If the gap exceeds this value, adjust the engine mounts.
- Rotate Coupling and Recheck: Rotate the shaft coupling 180° and recheck the gap. If any change occurs, it indicates that the coupling, shaft, or fit is not true, and they will need to be removed and inspected by a shaft shop.
- Install Coupling Bolts: Once the gap is minimised and acceptable, install the coupling bolts. Sequentially and cross-torque the bolts up to their maximum torque rating. Use grade 8 mild steel fasteners and lock washers or locking nuts. Ensure that at least two threads protrude past the nut to ensure full load-bearing ability.
- Paint or Corrosion Inhibit: After installing and torquing the fasteners, paint or apply corrosion inhibition to the mild steel couplings and fasteners to prevent rapid rusting.
- Adjust Motor Mounts: Ideally, the adjustable screw studs on the motor mounts should not be at the full extent of their travel. Leave some room for future fine-tuning. If necessary, install shims or modify brackets or stringers to adjust the mount position.
- Dial Indicator Check (Optional): As an optional final check, use a dial indicator to measure shaft irregularity or "run out" at the shaft coupling. This will confirm that the shaft is centred on the transmission coupling centreline.
Compasses on Boats: Essential or Obsolete?
You may want to see also
Testing and inspection
Initial Inspection
Before removing the old engine, it is important to identify the problem by performing a thorough inspection. This includes checking for leaks, worn or damaged parts, and other signs of malfunction. This step helps pinpoint the specific issues that need to be addressed and ensures that all necessary repairs or replacements are identified.
Testing After Reinstallation
Once the new engine is installed, it is critical to test it to ensure proper functioning and performance. This includes checking the engine alignment to ensure it lines up perfectly with the gimbal bearing and drive shaft coupler. Running the engine will provide valuable insights into its condition; excessive smoke, unusual noises, or performance issues may indicate problems that require further attention.
Maintenance and Regular Checks
Regular maintenance and inspections are essential to keep your new engine in optimal condition. This includes routine tasks such as:
- Checking and changing engine oil and filters according to the manufacturer's recommendations.
- Inspecting and maintaining the cooling system, including checking coolant levels and hoses for cracks or leaks.
- Examining and replacing fuel filters and fuel lines as needed to ensure a clean fuel supply.
- Testing the electrical system, including the battery, ignition system, and connections.
- Keeping the engine clean and free of debris, paying attention to parts prone to build-up like the air filter and spark plugs.
- Inspecting belts and hoses for wear and tear, replacing them as necessary.
- Ensuring proper winterization and storage when the engine is not in use for extended periods.
Professional Assistance
While some testing and maintenance can be performed by boat owners, it is often advisable to consult a professional mechanic for certain tasks. Their expertise can help identify complex issues, ensure proper installation, and provide guidance on specific maintenance requirements for your engine.
By following these testing and inspection procedures, you can ensure the safe and efficient operation of your new inboard boat engine, maximising its performance, longevity, and reliability.
The Evolution of Speed Boat Hulls: Materials Used
You may want to see also
Frequently asked questions
If your engine is breaking down regularly, not starting properly, or is costly to maintain, it may be time to replace it. Other signs include reduced speed, slow acceleration, unusual noises, and overheating.
The cost of a new engine can range from $5,000 to $15,000, depending on the type of engine and the labour costs of installation. Inboard engines are generally more expensive to replace than outboard engines.
It's important to consult the manufacturer's guidelines and choose an engine that is suitable for your boat's size and weight. You should also consider the cost, the engine's horsepower, and any necessary accessories.
Replacing an inboard boat engine typically involves disconnecting various components that link the motor to the boat's systems, and then lifting the motor out. This may require specialised tools and equipment.