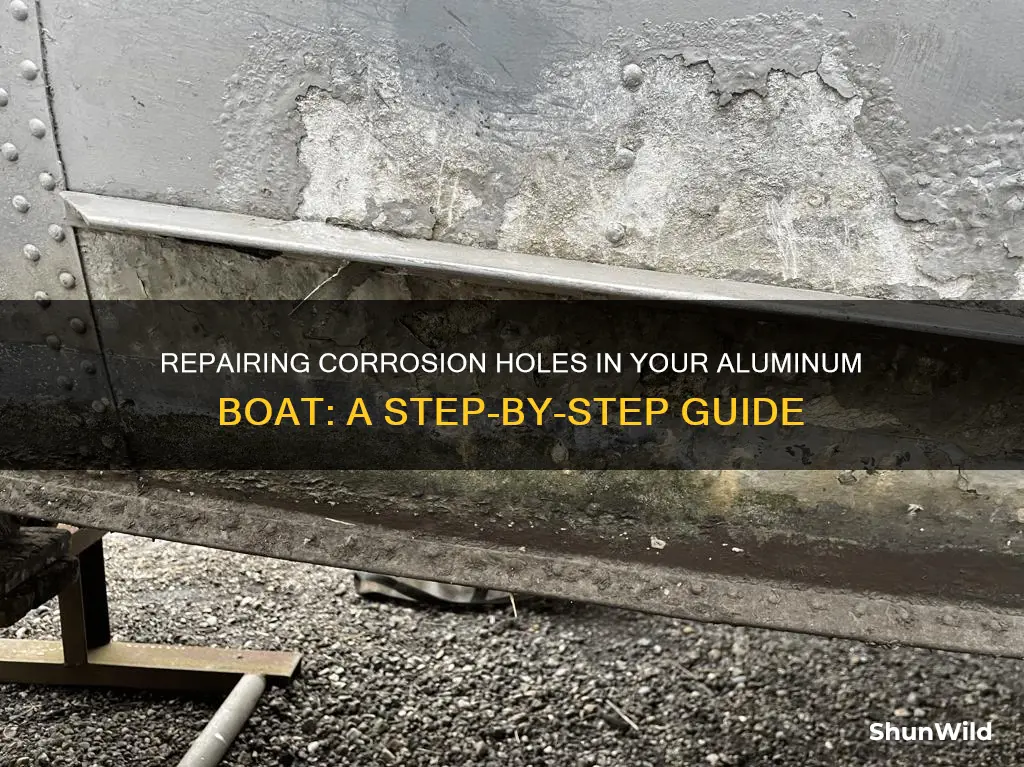
Corrosion holes in an aluminium boat can be repaired by welding, using epoxy, or patching with a rivet and sealant. However, welding is not always an option, as some aluminium boats are made with un-weldable alloys. Before repairing the corrosion holes, the area must be cleaned with a wire brush, sandblasting, or soda blasting.
Characteristics | Values |
---|---|
Corrosion type | Pitting, galvanic corrosion, stray current corrosion |
Corrosion cause | Salt water, battery acid, copper, galvanised bolts |
Corrosion repair | Sandblasting, welding, epoxy paste, acid etching, soldering, patching, coating |
Corrosion prevention | Removing corrosion source, rinsing, coating with protective layer |
What You'll Learn
Clean the corroded area with a wire brush
To repair corrosion holes in an aluminium boat, it is important to clean the corroded area with a wire brush. This process is crucial to ensure that the repair work will be effective and long-lasting. Here are some detailed instructions to guide you through the process:
First, put on the appropriate safety gear, including gloves, eye protection, and a respirator. Corrosion and rust can be hazardous to your health, so it is important to protect yourself during the cleaning process.
Next, use a wire brush to scrub the corroded area vigorously. The goal is to remove as much of the corrosion and any loose paint or debris as possible. Pay close attention to the edges of the corrosion holes, as these areas need to be clean and smooth for the repair to be effective. You can use a wire brush attachment on a power drill to make the process easier and faster. Make sure to get into any crevices or tight spaces affected by corrosion.
After brushing, inspect the area closely. If there is still corrosion present or if the metal is uneven, you may need to use a stronger tool, such as a carbide burr or a die grinder, to remove the remaining corrosion and create a smooth surface. Be careful not to damage the surrounding metal.
Once you are satisfied with the cleaning, it is important to neutralise any remaining corrosive agents and prepare the surface for repair. You can do this by rinsing the area with water and then using a solution of diluted acid, such as hydrofluoric, sulfuric, or hydrochloric acid, to etch the surface. Alternatively, you can use a specialised aluminium cleaner or a product like Alumabrite to neutralise and protect the aluminium. Make sure to follow the instructions on your chosen product carefully.
Finally, rinse the area thoroughly with water again to remove any residue from the cleaning and neutralising process. At this point, the corroded area should be clean, smooth, and ready for the next steps in the repair process, such as filling the holes with epoxy or welding.
Boat Insurance: Liability Coverage While Trailered?
You may want to see also
Sandblast the area to remove corrosion
Sandblasting is a great way to remove corrosion from your aluminium boat. However, it is important to remember that aluminium is softer than steel, so you will need to be careful with your choice of sandblast media and pressure.
First, you need to choose the right sandblast media. Do not use steel-based media as this will impregnate the aluminium surface and create corrosion. Instead, use glass beads, baking soda, crushed glass, aluminium oxide, or walnut shells. These options are softer and will not damage the hull.
Next, you need to set the sandblasting pressure. Aluminium panels are usually thinner, so they are susceptible to warping when blasted. Start with a very low pressure and gradually increase it. Typically, you will end up with a blasting pressure of around 50-60 PSI.
Before you begin, it is a good idea to do a small spot test. This will show you the end result of a given blast media and pressure, as well as how long the process will take.
Now, you are ready to sandblast the area. Remember to wear protective gear, especially a respirator to avoid inhaling any dust or silica. Start with the sandblaster at a low pressure and gradually increase it as you work. Move the nozzle in a consistent manner to ensure an even finish. Work in small sections until you have removed all the corrosion from the area.
Once you have finished sandblasting, use a microfiber towel to wipe down the area and remove any remaining dust or debris.
Choosing the Right Boat for Extended Voyages
You may want to see also
Fill the holes with an epoxy paste
Filling corrosion holes in an aluminium boat with an epoxy paste is a straightforward process, but it requires careful preparation to ensure an effective repair. Here is a step-by-step guide:
Step 1: Clean the Corroded Area
Before applying the epoxy paste, it is essential to clean the corroded area thoroughly. Use a wire brush or a wire wheel attached to a drill to remove any corrosion, paint, or debris from the aluminium surface. This step is crucial to ensure that the epoxy paste adheres properly to the aluminium. It is also recommended to wear safety gear, such as gloves and eye protection, during this process to avoid injury.
Step 2: Sand or Soda Blast the Area (Optional)
While not always necessary, some people recommend sandblasting or soda blasting the corroded area to create a clean and rough surface for better adhesion. However, this step should be approached with caution, as sandblasting can be too harsh on soft aluminium, and soda blasting may not have enough power to clean out deep corrosion pits effectively. If you choose to sand or soda blast, be sure to wear appropriate safety gear and follow the manufacturer's instructions for proper usage.
Step 3: Acid Etching (Optional)
Acid etching is another optional step that can be performed to clean the aluminium surface and prepare it for the epoxy paste application. Use a mixture of hydrofluoric, sulfuric, and hydrochloric acids to etch the aluminium, which will help remove any remaining corrosion and create a clean surface for the epoxy to adhere to. Be sure to follow safety precautions when handling these acids and rinse the area thoroughly with water after etching.
Step 4: Apply the Epoxy Paste
With the corroded area clean and prepared, you can now apply the epoxy paste. Choose a marine-grade epoxy paste that is suitable for use with aluminium and follow the manufacturer's instructions for proper mixing and application. Fill the corrosion holes and any pitted areas with the epoxy paste, making sure to work it into all crevices and cracks. Use a putty knife or similar tool to smooth out the epoxy and ensure a flush finish with the surrounding aluminium surface.
Step 5: Allow the Epoxy to Cure
Once the epoxy paste has been applied, allow it to cure completely according to the manufacturer's instructions. This typically involves leaving the epoxy undisturbed for a specified amount of time, often several hours or more, depending on the product. Do not disturb the boat or subject it to any stress during the curing process to ensure the epoxy sets properly.
Step 6: Sand and Paint (Optional)
After the epoxy has cured, you may choose to sand the repaired area to smooth out any rough spots and create a uniform surface. This step is especially important if you plan to paint the boat. Finally, if desired, apply a coat of marine-grade paint compatible with aluminium to the repaired area, following the paint manufacturer's instructions. Allow the paint to dry completely before using the boat.
Where to Buy Boat Paint: Top Retailers and Brands
You may want to see also
Acid wash the area to remove corrosive residue
To repair corrosion holes in an aluminum boat, you must first clean the area. One way to do this is by using an acid wash. Acid washing your boat will remove the mill scale and any other residue or contaminants.
Acid washing is a process that involves etching the oxide film off the aluminum surface using an acid. The most common products for this use are Zep-a-Lume or Alum-a-Brite, which are solutions of phosphoric and hydrofluoric acids. These products are not to be trifled with and should be handled with care. You should wear protective gear and dilute the acid with water.
After applying the acid, you must neutralize it to stop the etching process. This can be done with aluminum brightener and lots of water. Once the acid is neutralized, you need to rinse the surface with water and then apply a zinc and chromium solution, such as Allodyne, which will form a protective film on the aluminum surface.
It is important to note that acid washing is not always necessary for repairing corrosion holes in aluminum boats. In some cases, sanding, wire brushing, or soda blasting may be sufficient to clean the area and prepare it for repair. Additionally, welding is not always an option for repairing corrosion holes, as it can create more problems if the surrounding metal is not clean and free of corrosion.
Boat Hull Inspection: A Comprehensive Guide to Success
You may want to see also
Weld the holes shut
Welding corrosion holes in an aluminium boat shut is a challenging task that requires careful preparation and execution. Here is a step-by-step guide to help you through the process:
Step 1: Assess the Damage
Before beginning any repair work, it is essential to thoroughly inspect the boat and identify all areas of corrosion. Pay close attention to the hull, struts, transom, and stringers, as these areas are particularly susceptible to corrosion. Take measurements of the affected areas, including the depth and width of the corrosion pits and holes. This information will help you determine the best repair method.
Step 2: Clean and Prepare the Surface
To ensure a successful weld, the corroded areas must be thoroughly cleaned and prepared. Use a wire brush, sandblasting, or soda blasting to remove any debris, paint, or oxidation from the aluminium surface. It is crucial to create a clean and smooth surface for welding. Be cautious when cleaning, as aggressive techniques can further damage the soft aluminium metal.
Step 3: Choose the Right Filler
Before welding, you may need to fill in deep pits or small holes to create an even surface. Select a suitable filler material that is compatible with aluminium, such as epoxy or marine-grade filler compounds. Avoid using metallic fillers, as they can cause further corrosion due to dissimilar metal contact. Ensure the filler is suitable for saltwater submersion if your boat is exposed to saltwater.
Step 4: Drill and Enlarge Corrosion Holes
For effective welding, it is often necessary to enlarge the corrosion holes slightly. Using a drill bit, carefully drill out the holes to create a clean and consistent bore. This step will help ensure that the weld pool can adequately fill the hole and create a strong bond. Be cautious not to drill too deeply, as you want to maintain as much structural integrity as possible.
Step 5: Welding Technique
When welding aluminium, it is crucial to use the right technique and equipment. Aluminium welding is typically performed using TIG welding with ER4043 filler rod or MIG welding. Ensure you have the appropriate welding machine and that you are familiar with the process. Use a copper backing plate clamped to the inside of the boat to provide additional support and improve weld quality. Start by welding from the outside, creating a blob that fills the hole. Then, weld from the inside to make the surface flush.
Step 6: Post-Weld Grinding and Finishing
After welding, carefully inspect the repaired areas. Use a grinder to smooth out any weld beads and create a flush surface. Be cautious not to grind too deeply, as you want to maintain the strength of the weld. Apply a suitable primer and paint to the repaired areas to protect the aluminium from further corrosion.
Remember, welding aluminium boats requires skill and experience. If you are unsure or uncomfortable with the process, it is best to seek the assistance of a professional welder or boat repair specialist.
Identifying Battery Drain: A Boat Owner's Guide
You may want to see also
Frequently asked questions
The best way to repair corrosion holes in an aluminium boat is to weld the holes shut. If this is not possible, you can fill the holes with an epoxy paste or marine sealant.
Soldering is not recommended for repairing corrosion holes in an aluminium boat, as it is a more gentle option than welding. It is better to use epoxy or marine sealant to fill the holes.
The area around the corrosion holes should be cleaned and treated to prevent further corrosion. This can be done by using a wire brush, sandblasting, or soda blasting to remove any corrosion and create a clean surface for repair.
There are several types of fillers that can be used to repair corrosion holes in an aluminium boat, including epoxy, marine sealant, and aluminium epoxy stick. It is important to use a filler that is designed for adhesion to aluminium and salt water submersion.
Yes, a welder can be used to fill in the corrosion holes in an aluminium boat. However, welding of hull pits rarely goes well, as there is typically more corrosion in the area that is unseen. It is important to clean and treat the area before welding to ensure a strong repair.