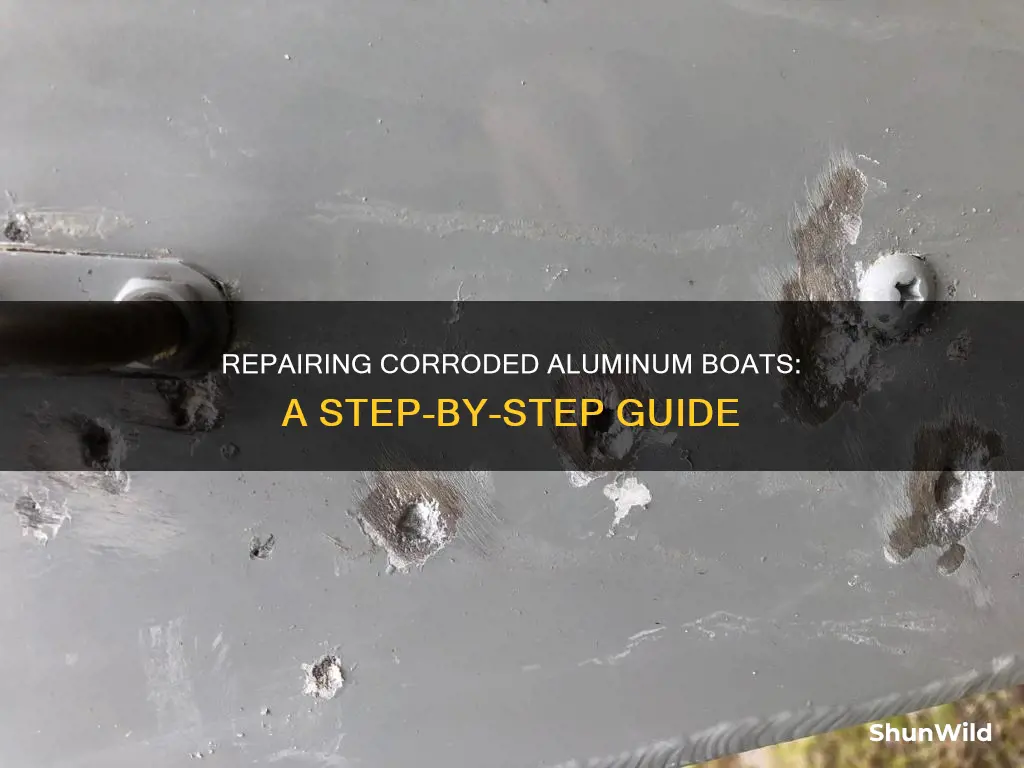
Corrosion is a common issue for aluminium boats, and there are a variety of ways to repair it. The best method depends on the type and extent of the corrosion. For small areas of corrosion, using an epoxy filler or solder can be an effective solution. For larger areas, welding may be necessary, but it is important to ensure that the welder has experience with aluminium boats, as the wrong technique can cause further damage. In some cases, it may be necessary to cut out the corroded section and weld in a new patch. It is also important to address the cause of the corrosion to prevent it from recurring. This may involve treating the wood used in the boat or replacing galvanised bolts with stainless steel ones.
Characteristics | Values |
---|---|
Corrosion type | galvanic corrosion, electrolysis, crevice corrosion |
Cause | saltwater, dissimilar metals, stray electrical current, trapped moisture |
Prevention | floating boat lifts, sacrificial anodes, proper paint and coatings, rinsing after saltwater use |
Repair | spot welding, marine epoxy, chemical treatments, welding patches, brazing |
What You'll Learn
Clean the corroded area with a pressure washer, brush, sandblast, or soda blast
To repair a corroded aluminum boat, you must first clean the corroded area. You can use a pressure washer, brush, sandblast, or soda blast to do this.
Pressure Washer
If you have access to a pressure washer, this can be a quick and effective way to clean your aluminum boat. First, attach a pressure washer soap nozzle to your garden hose. Spray the boat, starting from the bottom, with biodegradable car soap and let it soak for about 5 minutes. Then, rinse off the boat from top to bottom using the pressure washer. Be sure to wash off all the detergent and flush out the motor.
Brush
If your boat is well-maintained and not frequently taken out on the water, a simple brush and some soapy water may be all you need to clean the corroded area. Start by rinsing the boat off with a garden hose. Then, fill a bucket with water and car soap, dip a gentle scrubber into the mixture, and scrub down the boat's hull. Finally, rinse the soap and dirt off the boat thoroughly. If necessary, repeat the process or move on to a more heavy-duty method.
Sandblast
Sandblasting can be an effective way to clean and restore an aluminum boat hull. It will remove paint and reveal any corrosion or cracks, leaving a totally workable surface for repairs and modifications. However, sandblasting can be costly and may not be the best method for revealing corrosion and pitting. Acid etching may be a better option for revealing these issues. Additionally, sandblasting alone may not leave a clean, weldable surface.
Soda Blast
Soda blasting is another option for cleaning aluminum. It can leave a finer finish than other methods, such as glass bead blasting, and is easier to remove afterward. Simply rinse the soda blasting soda with water and let the aluminum dry, then apply other chemicals to prevent further corrosion.
LLC for Boat Owners: Pros and Cons
You may want to see also
Drill out the corroded holes
To repair a corroded aluminum boat, you will need to drill out the corroded holes. This is a crucial step to ensure that the boat's integrity is restored and prevent further corrosion. Here is a step-by-step guide on how to effectively drill out the corroded holes:
Assess the Damage:
Begin by carefully inspecting the corroded areas of your aluminum boat. Identify the holes that require drilling and assess their size and depth. This will help you determine the appropriate tools and techniques for the drilling process.
Gather the Right Tools:
Make sure you have the necessary tools for the job. You will need a drill with a suitable drill bit for metal. It is recommended to use a metal-cutting hole saw or a step drill bit for drilling out the corroded holes. These tools will help you achieve clean cuts and minimize burrs.
Prepare the Work Area:
Before you start drilling, it is important to create a safe and clean work environment. Place the boat on a stable surface and ensure you have adequate lighting and ventilation. Wear appropriate safety gear, including eye protection, gloves, and a respirator to protect yourself from metal shavings and dust.
Mark the Drilling Spots:
Using a center punch or a nail, carefully mark the center of each corroded hole that you need to drill out. This will help guide your drill bit and ensure accurate drilling.
Drill Pilot Holes:
Start by drilling small pilot holes at the marked spots. Choose a drill bit size that is smaller than the final desired hole size. This will help guide your larger drill bit and prevent wandering. Drill slowly and with moderate pressure to maintain control.
Drill Out the Corroded Holes:
Now, it's time to drill out the corroded holes. Select the appropriate size of the metal-cutting hole saw or step drill bit. Align the drill bit with the pilot hole and start drilling. Apply steady pressure and maintain a moderate speed to avoid melting the aluminum. Go easy on the pressure, and don't force the drill; let the drill bit do the work.
Deburr and Clean the Holes:
Once you've drilled out the corroded holes, use a rat-tail file or a deburring tool to remove any burrs or sharp edges around the newly drilled holes. Clean the area with a soft brush or cloth to remove metal shavings and debris.
Apply Corrosion Protection:
After drilling, it is important to protect the freshly drilled holes from future corrosion. Apply a corrosion-inhibiting primer or coating specifically designed for aluminum. Follow the manufacturer's instructions for proper application.
Final Inspection:
Finally, inspect your work thoroughly. Ensure that the drilled holes are clean, smooth, and free from any signs of corrosion. Check that all burrs have been removed and the surrounding aluminum surface is intact.
Drilling out the corroded holes is a crucial step in repairing your aluminum boat. By following these steps, you can effectively restore the integrity of your boat and prevent further corrosion. Remember to work carefully, maintain a safe environment, and always wear the appropriate safety gear when working with power tools.
Shark-Pulling Stunt: Men Behaving Badly?
You may want to see also
Acid etch the area around the holes
To repair corrosion on an aluminium boat, you can use an acid wash to etch the aluminium surface. This process removes corrosion and oxidation, preparing the metal for coating. Here is a step-by-step guide:
- Prepare the Area: Before applying the acid wash, ensure the area around the holes is clean and free from debris. You may need to sand or scrub the area to remove any remaining corrosion or residue. It is crucial to wear protective gear, including rubber gloves, goggles, and an apron, as you will be working with corrosive materials.
- Apply the Acid Wash: Using a brush or spray equipment, apply a thin, even coat of the acid wash to the area around the holes. Keep the surface wet with the acid wash solution and do not allow it to dry. For areas with heavy oxidation, use a Scotch-Brite pad to lightly abrade the surface while it is wet with the acid wash.
- Rinse the Area: After allowing the acid wash to sit for approximately five minutes, thoroughly rinse the area with fresh or deionized water. Ensure that you remove all traces of the acid wash, as well as any oils or contaminants. Dry the surface completely after rinsing.
- Apply Primer and Paint: Once the surface is clean and dry, apply a primer designed for use on aluminium, such as an etch primer or a vinyl wash primer. Choose a primer that is compatible with the type of paint you will be using. After priming, follow up with the appropriate paint, such as a marine-grade paint designed for aluminium boats. Make sure to work quickly, as oxidation can set in rapidly on bare aluminium.
Remember to always work in a well-ventilated area when using corrosive chemicals, and carefully follow the safety instructions provided by the manufacturer.
The Mystery of EOS: Who Owns the Boat?
You may want to see also
Tape the outside of the holes and fill with sealant
To repair corrosion damage on an aluminium boat, you will need to clean the corroded area, fill the holes with a sealant, and then coat the area to prevent further corrosion.
First, clean the area with a wire brush, sandpaper, or sandblasting. You want to remove all corrosion and contaminants from the area to ensure that the sealant will adhere properly. If there is any remaining wood in the boat, remove it, as this can be a source of corrosion.
Once the area is clean, it's time to fill the holes. Tape the outside of the holes to catch any excess sealant, and then fill the holes with a marine-grade sealant such as epoxy or marine caulk. Make sure to follow the instructions for your chosen sealant carefully, as improper mixing or application can result in a weak bond.
After the sealant has cured, you may need to sand or shape the patched area to match the surrounding hull. Once you're happy with the shape, coat the patched area with a protective coating such as zinc chromate primer or epoxy to prevent further corrosion.
Easy Guide to Changing Batteries in a Boat Cover Remote
You may want to see also
Coat the entire bilge with epoxy
To repair corrosion on an aluminium boat, you can coat the entire bilge with epoxy. This will prevent corrosion and provide superior adhesion for antifouling and other 1- and 2-part paints.
Firstly, you need to ensure that the aluminium surface is clean, bright, shiny, and completely free of oxidation and surface contamination. You can use a wire brush, sandpaper, or soda blasting to clean the corrosion and pitting. It is important to note that sandblasting may be too harsh on aluminium, so proceed with caution. Once the surface is clean, you can apply the epoxy primer.
When applying the epoxy, make sure to follow the manufacturer's instructions for mixing and application. The recommended mix ratio is 3:1 (three parts base to one part curing agent), and you can apply it by brush, roller, or spray. You will need to apply at least two coats of epoxy, with a dry film thickness of 8-12 mils. Allow the epoxy to dry completely between coats.
After the final coat of epoxy has been applied, you will need to apply a finish coat, such as a polyurethane finish or antifouling paint. This will provide protection and a smooth finish to the repaired area.
It is important to work quickly when applying the epoxy, as it has a relatively short pot life, and any delays can result in reduced adhesion or other issues. Additionally, make sure the area is well-ventilated during application and drying to avoid inhaling toxic fumes.
The Open Boat: Conflict and Survival at Sea
You may want to see also
Frequently asked questions
First, clean the corroded area with a brush, sandblasting or soda blasting. Then, fill the holes with an epoxy paste or marine glue. Finally, coat the area with a protective layer, such as zinc chromate primer, to prevent further corrosion.
Welding over corroded areas is not recommended as it can create a bigger hole and cause further corrosion. If you do choose to weld, make sure the area is thoroughly cleaned and use a copper plate covered with aluminium foil to prevent air infiltration.
One alternative method is to use a propane torch and a zinc soldering rod, such as Aluma-weld. This method requires constantly wire-brushing the area to remove any surface oxide.
Some recommended products include JB Weld, Marine-Tex, Gluvit, and Flex Seal.
Corrosion on aluminium boats can be caused by several factors, including galvanic corrosion, electrolysis, and the use of treated wood or copper in the boat's construction.