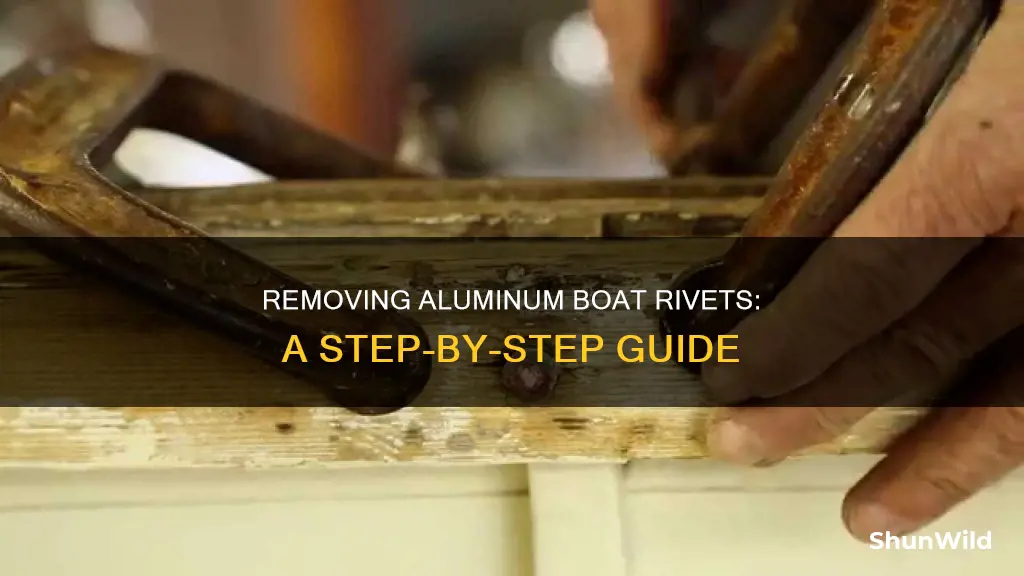
Removing rivets from an aluminium boat can be a challenging task. The process may involve grinding, drilling, or punching out the rivets, and it is important to take precautions to avoid damaging the boat or enlarging the holes. Before removing rivets, it is essential to identify the type of rivets used, as this will determine the appropriate removal technique. Blind rivets, for example, have a core that needs to be knocked out before drilling, while solid rivets can be removed by grinding off the head and then punching out the core. When drilling, it is crucial to use the correct drill bit size and maintain a slow and steady pace to avoid tempering the rivet. Additionally, filling the boat with water can help identify leaking rivets, which can then be repaired with an epoxy-based sealer.
What You'll Learn
Drilling out rivets
Step 1: Choose the Right Drill Bits
Select high-quality drill bits that are designed for drilling through metal. Avoid cheap, low-quality bits as they are more likely to break during the process. It is also recommended to use Titanium or Milwaukee bits for this task.
Step 2: Prepare the Rivets
Before you start drilling, it is important to determine what type of rivets you are dealing with. If they are blind rivets (installed with a puller), you will need to knock out the core and remove the locking ring before drilling. For solid driven rivets, you can start by center-punching the head.
Step 3: Set Up Your Drill
Ensure that your drill is set to a slow speed. High speeds can temper the rivet, making it stronger and more difficult to drill through. Position the drill straight up and down, perpendicular to the surface of the rivet.
Step 4: Start Drilling
Begin drilling slowly and carefully. It is important not to apply too much pressure, as this can cause the drill bit to grab and spin the rivet. Use a sharp, normal bit and a steady hand to drill through the center of the rivet.
Step 5: Remove the Rivet
Once you have drilled through the head of the rivet, you can knock out the rest of the rivet with a punch or a small drift. Be careful not to enlarge the original hole, as this will require re-drilling to fit a replacement rivet.
Tips:
- If the rivet starts to spin, you can use duct tape to hold it in place or grip it with pliers.
- You can also use a grinder to remove the head of the rivet before punching it out.
- Always wear appropriate safety gear, including eye protection, when drilling.
Best Bayliner Boat Model Years: An Overview
You may want to see also
Using a grinder
Step 1: Put on Safety Gear
Before you begin, it is important to prioritise your safety. Make sure to wear strong safety glasses to protect your eyes from sparks and metal shards. Additionally, wear gloves to shield your hands from metal pieces and the grinder's vibrations.
Step 2: Prepare the Grinder
Select a metal grinding wheel that is specifically designed for use with aluminium. Ensure the grinder is in good working condition and the wheel is securely attached. Adjust the grinder's settings to a speed suitable for aluminium; a slower speed is generally recommended to prevent the metal from overheating.
Step 3: Position the Grinder
Hold the grinder with both hands, positioning it parallel to the surface of the boat. The grinder wheel should be held close to the rivet, specifically where the head of the rivet connects with the boat's surface. Be cautious not to wedge the grinder wheel beneath the rivet's head before starting the device, as this can cause damage.
Step 4: Start Grinding
Turn on the grinder and gently move it towards the rivet. Maintain a steady and slow speed as you cut through the metal. If you encounter resistance, hold the grinder in place until it finishes cutting through that section before continuing. Continue grinding until you have removed as much of the rivet's head as possible.
Step 5: Create a Pilot Hole
Once the majority of the rivet's head has been removed, use a pin, prick, or centre punch to create a small dent in the centre of the remaining rivet material. This will serve as a pilot hole to guide your drill bit. Strike the punch with a hammer a few times to create a noticeable divot.
Step 6: Drill the Rivet
Lubricate your drill bit with cutting fluid or lubricant to prevent overheating and damage. Choose a drill bit that fits the size of the divot created by the punch and is long enough to penetrate the rivet completely. Drill through the rivet at a steady speed, applying firm pressure. Continue drilling until the rivet is pushed all the way through and removed from the surface.
Sea-Doo Challenger Boat: Worth the Investment?
You may want to see also
Finding leaking rivets
Once you have identified the leaking rivets, you can begin the process of repairing them.
Firstly, ensure the boat is dry and clean. You can then repair the leaking rivets with an epoxy-based sealer. For example, West System G/Flex 650-K, TotalBoat FlexEpox, or TotalBoat Aluminum Boat Leak Sealer. According to user reviews, Gluvit, JB Weld, and 3M5200 are also popular products for repairing leaking rivets.
Before applying the epoxy, use a wire brush to expose the bright metal around the rivet. You can then mix the resin and hardener components and transfer the mixture to a plastic epoxy syringe. Heat the rivet with a heat gun or propane torch to remove any remaining water. Finally, use the syringe to apply the epoxy around the head of the rivet.
If you are using TotalBoat Aluminum Boat Leak Sealer, it is recommended that you sand within a 1" radius of the rivet head until the metal is bright and shiny. Attach a static mixing tip to the cartridge and insert it into a caulk gun. Apply a bead of the product around the rivet head to form a flexible, waterproof seal.
Exploring Boat Launches: Coral Cove and Flopper Pond
You may want to see also
Rebucking (tightening) a rivet
Rebucking, or tightening, a rivet is a simple process that requires a few tools and some basic knowledge. It is important to understand the different types of rivets and the materials they are used on to ensure a secure and long-lasting connection.
To rebuck a rivet, first identify the loose rivet and remove it from the material. This involves drilling out the center of the rivet and then removing the head. For metal rivets, use a drill bit that is the same size as the rivet. For wood rivets, be careful not to damage the wood while drilling. And for plastic rivets, use a drill bit that is slightly smaller than the rivet. Once the center of the rivet is removed, use pliers to grip the remaining part and twist it out.
Next, choose the right rivet for the job. Consider the material and thickness of the objects being fastened together, as well as the strength and corrosion resistance required. The diameter of the rivet should be slightly larger than the diameter of the hole.
Now, install the new rivet. Place the rivet into the hole and use a hammer to drive it into place. A ball-peen hammer is ideal as it has a rounded end that is perfect for shaping the rivet head. You can also use an anvil, which is a flat metal surface, to support the rivet during installation and prevent bending or warping.
Finally, secure the rivet. Place a washer over the stem of the rivet and apply pressure using a rivet gun. Pull the stem of the rivet gun until the rivet is tight, then release the handle and remove the stem. Ensure that the pressure applied is enough to secure the rivet without damaging the objects being fastened.
By following these steps, you can effectively rebuck or tighten a rivet, ensuring a strong and secure fastening for your projects.
Boat Shoes and Socks: The Perfect Color Combination
You may want to see also
Removing old rivets
There are several ways to remove old rivets from an aluminium boat. One method is to use a drill to drill out the rivets. It is important to go slowly and use a sharp bit to avoid snapping the bit or tempering the rivet. The drill should be held perfectly straight up and down. The size of the drill should match the size of the shank. If the size of the shank is unknown, start with a drill that is about 1/3 the size of the head and work up to a size that removes the head.
Another method is to use a grinder. A grinder will cut through the aluminium quickly, so it is important to go lightly. A metal grinding wheel can be used to grind off the head of the rivet, and the rest can be punched out with a punch or small drift.
If you are removing blind rivets, the core and locking ring will need to be removed first. This can be done by centre-punching the head of the rivet and drilling it out. The core can then be forced out from the opposite side with a straight punch. The retaining ring can be pried out with the same punch.
Alternatively, an air chisel can be used to pop off the head of the rivet, and then a punch can be used to knock out the body.
Repairing Boat Seat Foam: A Step-by-Step Guide
You may want to see also
Frequently asked questions
You can use a drill, grinder, blowtorch, or angle grinder.
Go slow and ensure your drill is straight up and down. Start with a sharp bit and a low speed.
Use a center punch to mark the center of the rivet head, then drill a hole in the head of the rivet. Hit the side of the rivet head with a chisel and hammer, then use a punch to remove the body of the rivet.
Use a fine flame tip with Ox control.
Use a wire wheel or wire brush to remove any residual silicon.