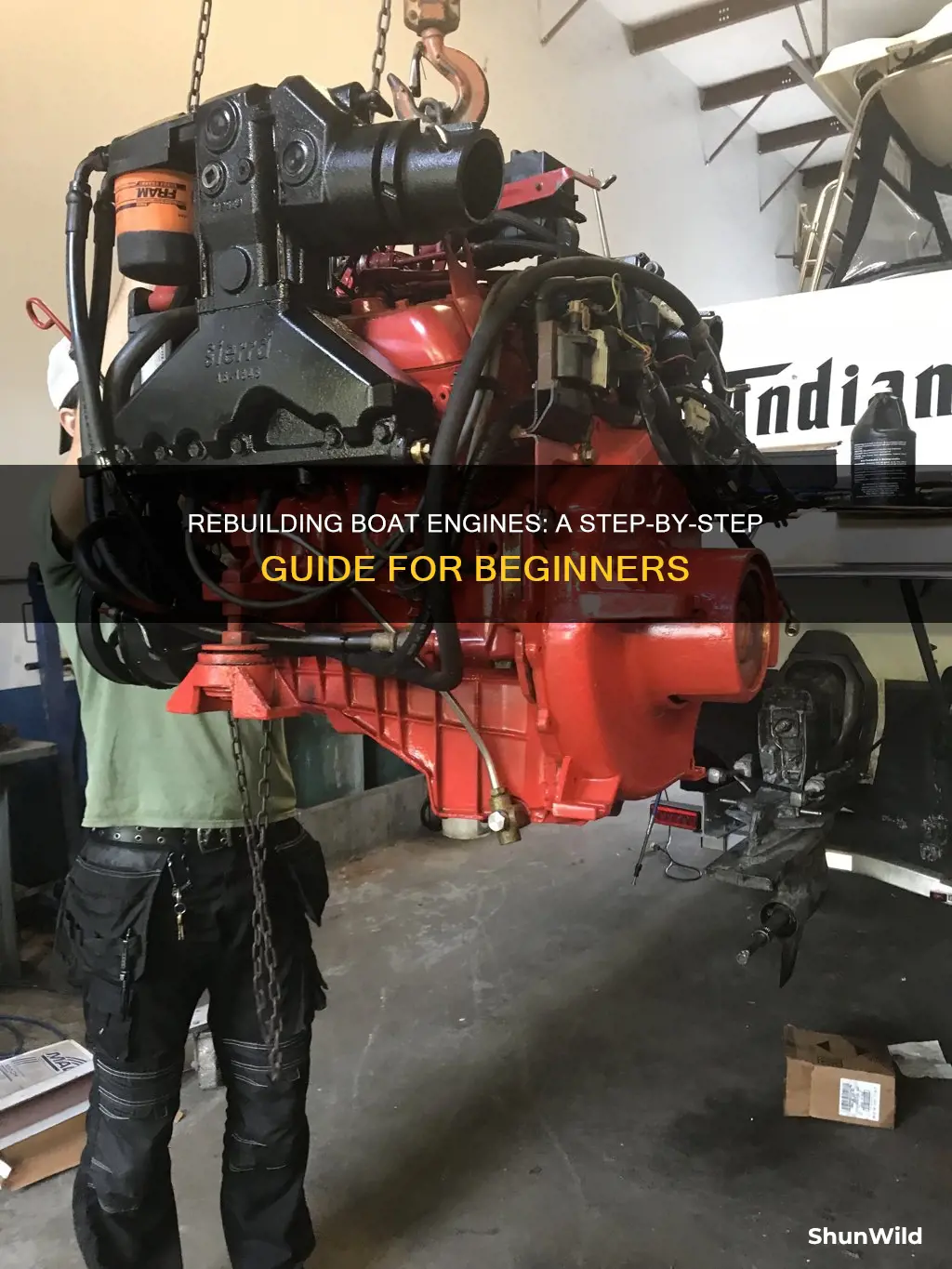
Rebuilding a boat engine is a complex task that requires careful consideration and planning. It involves disassembling the engine, inspecting and replacing worn-out parts, and reassembling it with precision. While it can be a rewarding project for experienced mechanics or boat enthusiasts, it is essential to weigh the pros and cons before embarking on this endeavour. One key factor is the age of the engine, as older engines may have scarce parts and dated technology, making them unsuitable for rebuilding. Additionally, the cost of rebuilding should be compared with the price of purchasing a rebuilt engine or a newer model, taking into account factors such as budget, service options, and turnaround time.
For those who decide to rebuild, it is crucial to have the necessary tools, a detailed service manual, and a methodical approach to disassembly and reassembly. It is also important to assess the nature of the damage and address the root cause to prevent reoccurrence. This may involve tasks such as boring cylinders, replacing pistons and rings, resurfacing heads, and checking bearings and crankshafts for damage. While rebuilding a boat engine can be challenging, with the right knowledge, skills, and patience, it is possible to restore an engine to its former glory and enjoy the satisfaction of a job well done.
Characteristics | Values |
---|---|
Engine type | Outboard |
Engine age | 1980s to early 2000s |
Engine features | Power trim and tilt, oil injection, primer starting, sound-deadened cowl exhaust, electronic fuel injection |
Rebuild cost | $2,500 |
Rebuilt engine cost | $3,500 - $4,500 |
New engine cost | $6,000 |
Engine rebuild difficulty | Requires mechanical skills and knowledge of engines |
What You'll Learn
Removing the engine
Before removing the engine, it is important to clean it thoroughly to ensure that the process of disconnecting components is not messy. Position the boat near a hoist and organise your work area by setting up tubs for bolts, clamps, and fasteners, and a table for your tools.
First, remove the hood and then start disconnecting the external engine components. Disconnect the ground cable from the battery, drain the coolant and radiator hoses, and remove the radiator and fan shroud. Loosen the alternator, the tension assembly, cooling fans, and belts, and disconnect the intake air supply and fuel lines.
Next, remove the bolts attaching the transmission's bell housing to the engine. Jack up the boat and put it on jack stands, then support the transmission with additional jack stands. Use the hoist to lift the engine, being careful not to hit the boat, and lower it onto your work surface.
Tips and Warnings
- It is a good idea to take close-up pictures of engine components from different angles as a reference for reassembly.
- Some vehicles have a pressurised fuel system, so be prepared to drain the fuel and relieve the pressure before disconnecting the fuel lines.
- Make drawings and take photos of the hoses and wires, and label them with tape and markers to ease the reassembly process.
- Do not depend on memory when disconnecting wires and hoses. Some may only plug in a certain way, but others are not obvious.
- It is very important to use jack stands or another form of support to hold the transmission before you disconnect the bolts. Once you loosen them, there will be nothing to support the transmission and it will fall unless held up.
- Most transmissions do not need to be removed from the vehicle as long as they are safely supported when the engine is removed.
- Be extremely careful when swinging the engine free of the boat to avoid any damage.
Canceling Fresh Off the Boat: Erasure of Asian-American Stories
You may want to see also
Disassembling the engine
Prepare the Work Area and Engine:
Before starting, ensure your work area is well-lit, spacious, and organised. Have all the necessary tools and safety equipment ready. It is also recommended to clean the engine to remove any dirt, grease, or sludge that could make the process messier.
Disconnect External Components:
Start by disconnecting the ground cable from the battery. Then, drain the coolant and radiator hoses. Remove the radiator and fan shroud if applicable, being gentle with the delicate aluminium cells. Loosen and disconnect components like the alternator, tension assembly, cooling fans, belts, intake air supply, and fuel lines. Label and take photos of hoses and wires to ensure proper reassembly.
Remove Transmission and Engine:
Remove all electric connections to the motor, except spark plug wires, and disconnect the exhaust manifold. Disconnect the bolts attaching the transmission's bell housing to the engine. Jack up the car and support the transmission with jack stands. Use a hoist to lift and remove the engine, being cautious not to hit the car.
Disassemble Engine Block:
Refer to the shop manual for your specific engine model. Perform a visual inspection of the engine, checking for signs of wear, damage, or leaks. Remove the exhaust manifold if not already done. Then, start disassembling the engine by removing the oil pan and valve covers, followed by the cylinder heads. Protect the lifter rods during this process.
Inspect and Measure Cylinder Bores:
Check the cylinder bores for wear using a micrometer. If the wear exceeds 20/10000 of an inch, the engine will likely need to be bored and oversized pistons used. Remove the ridge on the cylinders near the top of the bore with a cylinder reamer.
Remove Piston and Rod Assemblies:
After removing the rod caps, place rod journal protectors on the rod ends to prevent damage. Remove the piston and rod assemblies, keeping them in the correct order for reassembly.
Remove and Inspect the Crankshaft:
Once the crankshaft is removed, store it safely and inspect it for cracks and signs of overheating. Measure various crankshaft dimensions and compare them to the specifications in the shop manual. If the crank is out of spec, you may need to send it to a machine shop for resurfacing.
Remove Camshaft, Balancer Shafts, and Auxiliary Drives:
Pay attention to end play shims and spacers, keeping them organised for reassembly. Remove the cam bearings, noting their position.
Finish Disassembly:
Remove all remaining components attached to the outside of the engine block, including core plugs, brackets, and guide pins. Perform a final visual inspection of the engine block for any cracks. You may also want to Magnaflux the engine block to check for leaks.
Disassembling a boat engine is a detailed and intricate process. Always refer to the specific instructions and manuals for your engine model, and ensure you have the necessary tools and expertise before proceeding. Safety should be a top priority throughout the entire process.
Washington St Boat Launch: Accessibility and Disability Access
You may want to see also
Replacing parts
When rebuilding a boat engine, there are many parts that you may need to replace. The specific parts you will need to replace will depend on the type of engine you have and the extent of the damage. Here is a list of some of the most commonly replaced parts when rebuilding a boat engine:
- Pistons and piston rings: These are crucial components in an engine and are responsible for the engine's compression and power. Over time, pistons can become worn or damaged, leading to reduced engine performance or even engine failure. Replacing pistons and piston rings is a common part of engine rebuilding and can help restore the engine's performance and efficiency.
- Cylinder sleeves: Cylinder sleeves are metal tubes that line the engine's cylinders and provide a smooth surface for the pistons to move up and down. In some cases, the cylinder sleeves may become worn or damaged, requiring replacement. This is particularly common in older engines or engines that have been subjected to excessive wear and tear.
- Gaskets and seals: Gaskets and seals are used throughout an engine to prevent leaks and maintain proper pressure. Over time, these gaskets and seals can deteriorate, leading to leaks and reduced engine performance. Replacing gaskets and seals is an important part of engine maintenance and can help prevent further damage to the engine.
- Bearings: Bearings are used to support and guide rotating parts in an engine, such as the crankshaft and camshaft. Over time, bearings can become worn or damaged, leading to increased friction and heat in the engine. Replacing bearings can help improve the engine's performance and prolong its lifespan.
- Crankshaft and camshaft: The crankshaft and camshaft are critical components in an engine, responsible for converting the linear motion of the pistons into rotational motion. If these components become damaged or worn, they may need to be replaced. However, this is usually a more involved and expensive repair, as it requires disassembling a significant portion of the engine.
- Oil injection pump: This component is responsible for injecting oil into the engine to lubricate and cool the moving parts. If the oil injection pump fails, it can lead to catastrophic engine failure, as the engine will essentially be running without lubrication. Replacing the oil injection pump can help prevent this issue and ensure the engine's longevity.
When rebuilding a boat engine, it is important to consult a qualified technician or mechanic and follow a factory service manual specific to your engine. This will help ensure that the job is done correctly and that all necessary parts are replaced or repaired. Additionally, it is important to consider the cost of rebuilding versus the cost of simply replacing the engine, as in some cases, it may be more cost-effective to opt for a new or rebuilt engine.
Black Gold's Owner: Unveiling the Mystery of the Luxurious Boat
You may want to see also
Reassembling the engine
Clean and Dry the Engine Components:
Before starting the reassembly, ensure that all the engine components are thoroughly cleaned and dried. Use warm water and a water-soluble detergent to wash away any dirt, grease, or residue. Then, blow-dry the parts with compressed air to remove any moisture. This step is crucial to prevent any contaminants from interfering with the engine's performance.
Lubricate and Install the Crankshaft:
Grease the camshaft bearings with high-pressure grease. Then, carefully install the camshaft, ensuring that the caps are positioned and torqued correctly. The caps should be snug first, and then torqued from the center outwards. Once the camshaft is in place, rotate the crankshaft to check for any binding issues.
Install the Timing Chain or Belt:
Refer to your engine's manual to identify the correct timing marks. Align these marks correctly and set the degree wheel at Top Dead Center. This ensures that the crankshaft and piston timing is accurate and that the valves are timed correctly for the intake, compression, power, and exhaust strokes.
Install New Pistons, Rings, Gaskets, and Seals:
Check the piston ring end gaps to ensure they meet the original equipment manufacturer (OEM) clearances. Install the pistons, staggering the ring end gaps by 180 degrees to reduce "blow-by." Additionally, install new gaskets and seals, ensuring they are positioned correctly.
Install the Piston and Rod Assemblies:
Lubricate the rod inserts and install the piston and rod assemblies. Torque the rod caps gradually in stages to ensure even seating. Continue rotating the crankshaft as you install each piston to ensure smooth rotation.
Install the Head Gasket:
The head gasket is crucial, so ensure it is installed correctly. Check if the gasket is directional and install it in the right direction. Lubricate the bolt threads and washers with OEM lubricant or sealer. Then, torque the bolts down in a specified pattern and in stages.
Install a New Valve Train:
Lubricate all the components as you install them. Adjust the valves as necessary, using minimal up and down motion.
Reinstall the Engine:
Mount the reassembled engine back onto the hoist and then into the boat. Reconnect all hoses, electrical connectors, and harnesses. Refill the engine oil and antifreeze.
Test the Engine:
Before starting the engine, perform final checks to ensure that all components are in their correct places. Refer to your engine manual for specific start-up and break-in procedures to ensure optimum performance and longevity.
Initial Start-up and Break-in:
During the initial start-up, set the emergency brake and block the wheels. Turn the ignition, and if the engine doesn't start, check the fuel delivery system. Monitor the oil pressure and temperature gauges closely. If you notice full oil pressure, cut the engine immediately and check for fluid leaks.
After getting the engine running reliably, it's important to break it in properly. Rev the engine to 2000 rpm to thin out any excess oil on the camshaft. Run the engine at various speeds between 1800 and 2500 rpm for at least 20 minutes.
Finally, change the oil and filter after the first 100 miles, and then regularly every 1000 miles for the first three months to ease the engine into its new life.
Best Inflatable Boats for Flooded Waters
You may want to see also
Testing the engine
Before testing, it is important to ensure that all ancillary systems are properly reconnected. This includes the wiring loom, alternator, exhaust pipes, and the cooling system. It is also crucial to make the engine room watertight to prevent any water ingress.
Once the preparations are complete, the first step is to test the wiring loom by using the control panel. If all the readings on the various meters are as expected and the warning lights for voltage, oil pressure, and the glow plug indicator are functioning, then the test is a success, and you can proceed to the next step.
The next step is to test the engine's cooling system, which typically consists of a raw water and a freshwater system. The raw water system supplies seawater to the engine via a seacock, while the freshwater system circulates within a closed system to remove heat from the engine. To test this system, you will need to fill the header tank with coolant and look for any leaks. Ensure that the coolant water does not come out immediately, as this could indicate a problem with the radiator cap or seal.
After confirming that the cooling system is functioning correctly, the throttle and gear linkages should be checked. These linkages connect the control levers at the helm to the engine and need to be properly adjusted and secured to ensure smooth operation.
Now, it's time for the moment of truth—the first engine test run. Before starting, ensure that the fuel system is bled to remove any trapped air. Turn the key to the start position a few times to pump fuel through the injectors. Once this is done, tighten the injectors and attempt to start the engine.
During the first test run, pay close attention to the engine's behaviour. If the engine starts but revs excessively or does not respond to the throttle controls, something may be tangled or hindering the movement of the throttle linkage. In this case, it is important to stop the engine and investigate the issue before proceeding.
If the engine starts and runs smoothly, allow it to run for a while, monitoring the temperature and other vital signs. Ensure that the cooling system is functioning correctly and that there are no leaks.
Finally, after a successful test run, it is essential to go over the engine again, checking for any loose connections, leaks, or other potential issues. Address any problems that arise and perform another test run if necessary.
Remember to always put safety first and have a plan for potential issues. It is also helpful to have another person assist you during the testing process, allowing for better communication and quicker response to any problems that may arise.
Restore Your Junked Boat: Kentucky Title Guide
You may want to see also
Frequently asked questions
If your outboard motor was built before 1980, it's probably too old. Parts will be hard to come by, and the technology is dated. If it's from the 1980s, it may have features like power trim and tilt, oil injection, primer starting, and electronic fuel injection. These features make the engine more desirable, but also more complicated and expensive to rebuild.
Rebuilding your engine will likely be cheaper than buying a new one, but it's important to consider the time and effort involved. If you're mechanically inclined and have the necessary tools, rebuilding it yourself can be a rewarding experience. On the other hand, buying a new engine will give you peace of mind and may be more cost-effective in the long run, especially if you plan to sell the boat in the future.
The cost of rebuilding an outboard motor can vary depending on the age and type of engine. For example, a typical rebuilt midsize outboard motor from the 1980s to 2000 with 90 to 115 horsepower will cost at least $3,500 if purchased from a discount dealer. Rebuilding your own engine will likely cost around $2,500. You'll also need to factor in the cost of tools and materials, which can add up quickly.
Rebuilding a boat engine can be a challenging task, especially if you don't have previous experience. It requires mechanical skills and knowledge of engine systems. It's important to have a good understanding of the process before starting and to work carefully to avoid damaging the engine further. It's also crucial to have a factory service manual for reference during the rebuild.