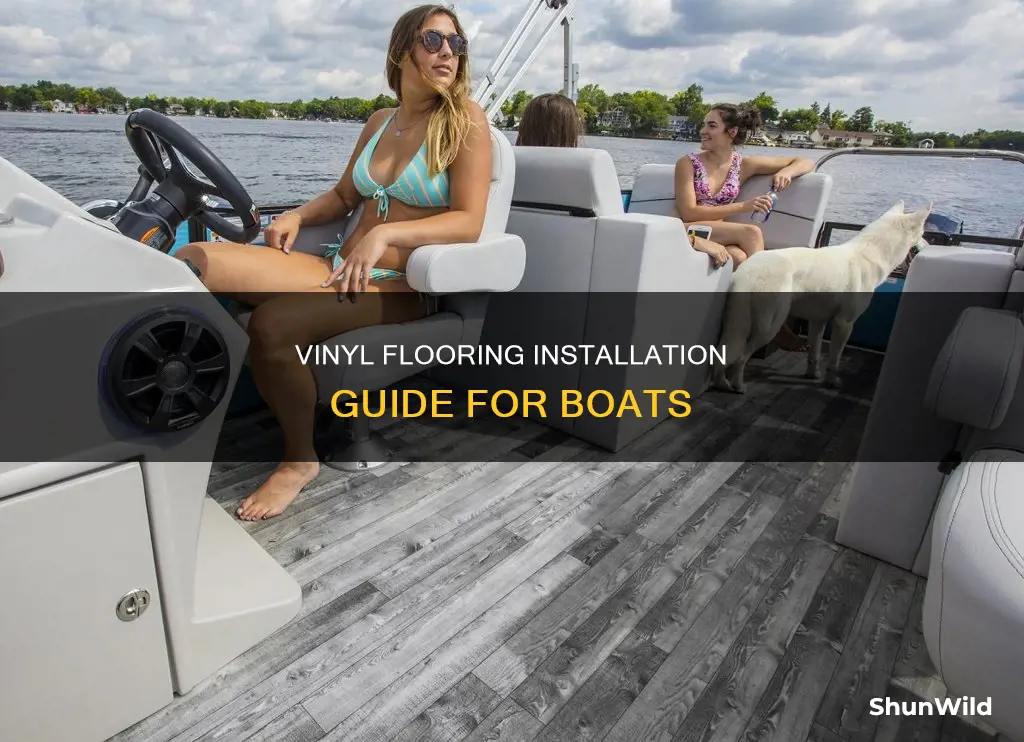
Installing vinyl flooring in a boat is a great way to give it a new look and protect it from damage. Marine vinyl flooring is made from highly durable materials that can resist damage from gasoline, oil, alcohol, sun exposure, abrasion, mildew, heat, and harsh weather conditions. It is also easy to clean and provides skid resistance.
There are a few things to consider when installing vinyl flooring in a boat. Firstly, it is important to choose a vinyl flooring that is durable and has a high wear layer and thickness. Secondly, you need to decide on the installation method – click and lock, glue down, or loose lay. If you want to be able to pull up your vinyl flooring, click and lock or loose lay is the best option. However, if you want a more permanent solution, glue down is the way to go.
In terms of tools and materials, you will need a tape measure to gauge the area, plywood, a marker, spackling paste and tool, fabric, DeckRite Adhesive and Trowel, a manufacturer's cardboard tube, a razor blade, a staple gun and stainless steel staples.
The process of installing vinyl flooring in a boat involves measuring and cutting the plywood to size, filling any holes and sanding it down, applying the adhesive, laying the vinyl, and securing it with staples. It is important to follow the specific instructions for the type of adhesive and vinyl being used, as well as taking into account the material of the boat's surface.
What You'll Learn
Choosing the right vinyl flooring
When choosing the right vinyl flooring for your boat, there are several factors to consider. Firstly, determine your budget and explore options that fit within your spending limit. The cost of the flooring itself and the installation can vary, so it's important to consider both aspects. Installation costs for marine flooring can range from $1,000 to $3,000, but you can save money by installing it yourself if you have the necessary tools and skills.
The next factor to consider is durability. Look for a vinyl flooring with a high wear layer and thickness to ensure it can withstand the harsh environment of a boat. The flooring should be resistant to water, UV rays, and chemicals, and ideally have anti-fatigue properties to provide comfort during long hours on the boat. You should also consider the slip resistance of the flooring, especially if it will be wet. Additionally, check for warranties and lab test results to gauge how long the product may last and how well it performs in terms of mold/mildew resistance, UV ratings, fading, and weathering.
The style of the flooring is also important. You can choose from a variety of designs and colors to match your boat's personality. Opt for a timeless look or a modern aesthetic, or go for a coastal theme with a vinyl that looks weather-worn or whitewashed. If you prefer a more classic touch, marine carpeting offers softness and warmth underfoot, although it requires regular cleaning and upkeep to prevent moisture buildup and mold growth.
Finally, consider the maintenance required for the flooring. Some options, like carpeting, can trap sand, odors, and moisture, requiring frequent cleaning. Others, like Flexa woven vinyl, are easy to maintain with regular sweeping and mopping using mild soap and water. Ultimately, the right flooring for your boat depends on your personal preferences, budget, and specific needs.
Boat Hull Registration in Texas: Is It Required?
You may want to see also
Preparing the surface
Firstly, it is important to remove any objects attached to the boat floor, such as seating, tables, trolling motors, and electronic devices. This will allow for a smoother and more efficient application of the vinyl flooring. Make sure to also remove any plastic or metal trim pieces, as these will be reused later in the process to secure the edges of the vinyl.
Next, you will need to remove any existing carpet or vinyl flooring that is currently on the boat. This includes any adhesive residue left on the surface. For wood boat decks (pontoons), it is recommended to completely remove the existing wood surface and replace it with new 3/4" pressure-treated plywood screwed securely into the structure. Consult a professional if you are unsure about the suitability of the surface.
Once the surface is clear, fill any holes in the plywood with spackling paste and smooth it over with sandpaper. This will create an even and level surface for the vinyl to adhere to. Use a broom to remove any dust or debris from the sanding process, ensuring a completely clean surface.
Now, you will need to measure the area where you will be installing the marine vinyl fabric. Use a tape measure to determine the length and width of the area. Mark these dimensions on a piece of plywood and cut the plywood accordingly. This will serve as the base for your vinyl flooring.
Before applying the vinyl, it is important to prepare the plywood base. Mark the lines for the saw cuts on the plywood using a marker. This will ensure that your vinyl flooring aligns correctly with the base.
With the surface prepared, you can now move on to the next step of the process, which involves cutting and adhering the vinyl fabric.
The Basics of Boat Driving: A Beginner's Guide
You may want to see also
Applying adhesive
Before applying the adhesive, ensure the surface of the boat is clean and free of debris, sawdust, screws, or any foreign objects. Use a leaf blower or broom to ensure the surface is completely clean. If you are applying the vinyl flooring to a fiberglass surface, you will need to etch the surface using a coarse grade of sandpaper to allow for better adhesion.
For wood surface applications, use MD-101 adhesive. Prior to opening, shake the glue container for about 60 seconds. The coverage rate for MD-101 is approximately 125 square feet per gallon. Pour the adhesive in a serpentine pattern onto the wood deck, creating ribbons of adhesive that are approximately 1.5 inches wide. Use a medium-nap paint roller to blend the adhesive together and completely cover the wood surface. Ensure the consistency and coverage of the adhesive are even, resembling a heavy coat of paint.
For aluminum or fiberglass surfaces, use MD-102 solvent adhesive. Apply the adhesive to the non-woven polyester backside of the vinyl using a paint roller. Be careful not to get adhesive on the topside of the vinyl as removing spilled or excess adhesive is extremely difficult. Then, apply a coat of MD-102 adhesive onto the surface of the boat. Allow the adhesive to set for 10-15 minutes.
The adhesive is ready when you can touch it and feel only a slight tackiness. If "legs" or "strings" appear between your finger and the adhesive, allow another 5 minutes to dry before proceeding. Carefully lay the vinyl onto the glued surface, ensuring it is straight and wrinkle-free. Use a plastic cutting board to push out any air bubbles or wrinkles.
For both types of surfaces, it is important to work in small sections at a time, especially if you are working alone. The vinyl needs to be applied when the adhesive is wet, and it begins to dry relatively fast.
Boat Length and Permit Requirements: What You Need to Know
You may want to see also
Rolling out the vinyl
Once the surface is ready, carefully unroll the vinyl and centre it on the surface, adjusting for the appropriate overhang on all sides. Pull out any wrinkles or folds in the material. Place some weighted objects, such as a toolbox or a brick, on the vinyl at one end of the boat, within 24 inches of the edge. Starting from the opposite end, roll the vinyl loosely back towards the weighted objects, maintaining a straight and consistent roll.
Next, apply the adhesive to the wood deck in a serpentine pattern, using a paint roller to blend it together and completely cover the surface. The consistency should resemble a heavy coat of paint, with no puddles or dry spots.
Now, standing on the vinyl near the weighted objects, carefully begin to unroll the vinyl over the adhesive, ensuring it is straight and wrinkle-free. If a wrinkle appears, lift the vinyl slightly and straighten it out before continuing.
Finally, use a clean, stiff-bristle push broom to sweep over the surface, distributing the adhesive evenly and helping to press out any air pockets.
Steering Cable Replacement: Bass Boat Maintenance Guide
You may want to see also
Securing the flooring
Preparing the Surface:
Before you begin, it is essential to prepare the surface of your boat's floor. Remove any existing carpet or vinyl flooring, as well as any adhesive residue. For wood surfaces, ensure the plywood is in good condition and securely attached to the structure. If needed, replace the plywood with new, pressure-treated plywood. Fill any holes in the plywood with spackling paste, and use sandpaper to smooth the surface. Remove dust and debris with a broom or leaf blower to ensure the surface is completely clean.
Measuring and Cutting the Vinyl:
Measure the area of the floor where you will be installing the vinyl flooring. Cut a piece of plywood to size, marking the dimensions with a marker. This will serve as your template. Roll out your vinyl fabric and cut it to size, allowing a few extra inches to hang over the bow and stern areas. Ensure the fabric is laid flat for at least 30 minutes before glue exposure to ensure perfect adhesion.
Applying Adhesive:
Use a suitable adhesive for your surface type. For wood surfaces, use a waterproof adhesive such as MD-101 or 3M rubber cement. For aluminum or fiberglass surfaces, use MD-102 solvent adhesive. Spread the adhesive evenly across the surface using a trowel or a paint roller. Work in small sections to prevent the adhesive from drying too quickly.
Installing the Vinyl:
Once the adhesive is tacky, carefully roll the vinyl fabric onto the surface, starting from one end of the boat. Use a cardboard tube or a rolling pin to smooth out any air bubbles and ensure consistent contact with the surface. Work your way towards the opposite end of the boat, ensuring the vinyl is straight and wrinkle-free.
Securing with Staples:
Although the adhesive should be strong enough to hold the vinyl in place, it is recommended to add an extra layer of security by stapling the edges of the vinyl. Use a staple gun with stainless steel staples to secure the flooring from bow to stern. This will help prevent peeling or curling over time.
Drying and Curing:
After the vinyl is installed, it is important to allow adequate drying time before using the boat or installing seating and equipment. For MD-101 adhesive on wood surfaces, the drying time is typically 2-3 hours in dry weather conditions with temperatures between 60-90 degrees Fahrenheit. For MD-102 adhesive on aluminum or fiberglass surfaces, allow a minimum of 1 hour of drying time.
Paddling a 14-Foot Flat Bottom Boat: Easy or Challenging?
You may want to see also
Frequently asked questions
Marine-grade vinyl flooring is best for boats as it is designed to withstand damage from gasoline, oil, alcohol, sun exposure, abrasion, mildew, heat, and harsh weather conditions.
You will need a tape measure, plywood, a marker, spackling paste, sandpaper, a broom, fabric, a DeckRite Adhesive and Trowel, a manufacturer's cardboard tube, a razor blade, a staple gun, and stainless steel staples.
First, measure the area where you will be installing the vinyl flooring. Cut a piece of plywood to size and mark the dimensions. Fill any holes in the plywood with spackling paste and smooth it over with sandpaper. Roll the fabric over the plywood and cut it to size, leaving a few extra inches hanging off. Apply adhesive to the plywood and wait for it to become tacky. Use the manufacturer's cardboard tube to roll the fabric onto the plywood and smooth out any air bubbles. Trim the excess fabric with a razor blade and secure the flooring with a staple gun and stainless steel staples.
There are several adhesives that can be used for vinyl flooring in boats, including 3M rubber cement, Roberts 6700, MariDeck MD-101, and MariDeck MD-102. The best adhesive for you will depend on the surface you are applying the vinyl to (wood, aluminum, or fiberglass) and personal preference.