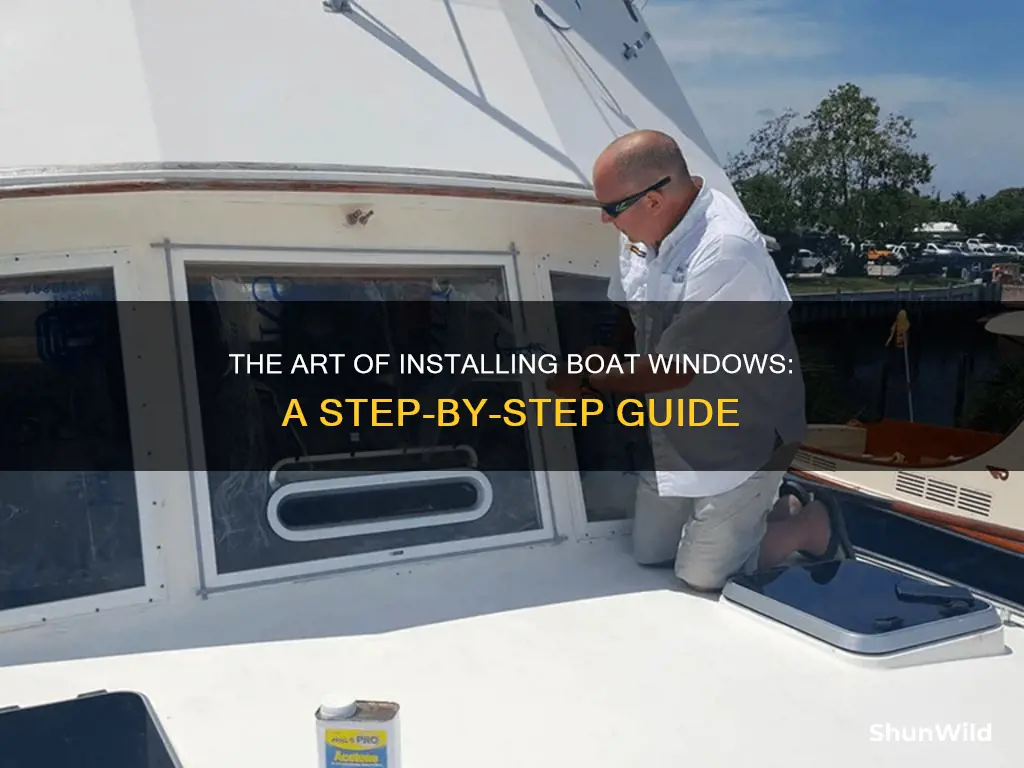
Installing boat windows is a complex process that requires careful planning and execution. The first step is to determine the type of window you want to install, such as acrylic, polycarbonate, or tempered glass, each with its advantages and disadvantages. The next step is to remove the old window, which is usually done by unscrewing the trim ring and pushing the window out. It's important to clean any leftover sealant to ensure a smooth installation process. When installing the new window, it's crucial to select the right window compound, such as a marine compound, and pay attention to the glazing materials. The process can be time-consuming and challenging, but with the right tools, knowledge, and patience, it can be a rewarding project.
What You'll Learn
- Removing the old window: Take out screws on the trim ring, then push the window out
- Clean the window frame: Remove any sealant residue with paint thinner and alcohol, then sand
- Choose the right window type: Acrylic, polycarbonate, or tempered glass
- Select the right window compound: Use a marine compound, not an adhesive
- Reassemble the window: Drill holes, apply sealant, and insert the window
Removing the old window: Take out screws on the trim ring, then push the window out
Removing the old window can be a challenging task, but with careful planning and execution, it can be done successfully. Here is a detailed guide on how to remove the old window of your boat:
Tools and Materials:
Before you begin, ensure you have the right tools and materials for the job. You will need a screwdriver or drill to remove the screws, a putty knife, and a soft surface such as a cloth or foam to place the window on. It is also recommended to have good quality, sharp tools of the correct size for the job.
Remove Screws on the Trim Ring:
Locate the trim ring on the inside of the boat. Using your screwdriver or drill, remove the screws that secure the trim ring in place. Be careful not to strip the screws or damage the surrounding area. If the screws are difficult to remove due to years of fixation, consider using a heat gun or releasing fluids to help loosen them.
Push Out the Window:
Once all the screws have been removed, it's time to apply force to push the window out of the opening. Work carefully and avoid using excessive force, as this may damage the surrounding structure. It is recommended to have someone assist you, especially when working with larger windows.
Release Sealant:
After removing the window, you will need to release the sealant from under the window flange. Use a very thin putty knife to work around the outside flange, selecting a corner of the window to start. Work the flange loose, and then push the corner of the window out of the hole. Be careful not to damage the flange or the surrounding area.
Clean Residual Sealant:
Once the window is completely removed, carefully clean any residual sealant stuck to the outside wall. This step is important to ensure a smooth surface for the new window installation.
By following these steps, you will be able to successfully remove the old window of your boat, preparing you for the next step of installing the new window. Remember to take your time, work carefully, and seek assistance if needed.
Boat Launches in Rhode Island: Free or Fee?
You may want to see also
Clean the window frame: Remove any sealant residue with paint thinner and alcohol, then sand
To clean the window frame and remove any sealant residue, you'll need to use a combination of chemical solvents and manual abrasion. Here's a step-by-step guide:
- Select the Appropriate Solvent: Start with a milder solution like paint thinner and work your way up to stronger chemicals if needed. Lacquer thinner, for instance, is stronger and can break down old paint. Other options include mineral spirits, denatured alcohol, acetone, or commercial paint removers like Goof Off. Choose a solvent that is suitable for the surface you're working on.
- Apply the Solvent: Using a clean cloth, apply the chosen solvent to the sealant residue. Work it into the residue with some elbow grease. You may need to let it sit for a while to soften the sealant.
- Scrape Away the Residue: Once the sealant has softened, use a plastic putty knife or a razor blade held at a 45-degree angle to carefully scrape away the residue. Keep the surface damp during this process to avoid scratches.
- Sand the Frame: After removing the bulk of the residue, use sandpaper or a bobbin sander to smooth out the window frame. This will help create an even surface for the new window installation.
- Clean and Prepare: Finally, clean the window frame thoroughly to remove any remaining solvent or residue. Ensure the frame is completely dry before proceeding with the new window installation.
Remember to work in a well-ventilated area when using chemical solvents, and always wear protective gear, including gloves and eye protection. Additionally, test the chosen solvent on a small, inconspicuous area first to ensure it doesn't damage the window frame material.
When to Watch: Oxford-Cambridge Boat Race
You may want to see also
Choose the right window type: Acrylic, polycarbonate, or tempered glass
When it comes to choosing the right window type for your boat, there are a few options to consider: acrylic, polycarbonate, or tempered glass. All three materials offer distinct advantages and disadvantages that should be considered before making a decision.
Acrylic Windows
Acrylic, also known as polymethyl methacrylate (PMMA), is a popular choice for boat windows due to its strength, durability, and workability. Acrylic sheets can be easily fabricated, machined, and thermoformed to fit a variety of window shapes and sizes. They also offer good dimensional stability, making them resistant to warping or shrinking over time. Additionally, acrylic windows provide excellent visibility and are very difficult to break, making them a great choice for rugged marine use. However, one downside to acrylic windows is that they are more susceptible to scratching compared to other materials. They also tend to be expensive, so it is recommended to use them sparingly.
Polycarbonate Windows
Polycarbonate windows are another excellent option for boat owners. Polycarbonate is a strong, lightweight material with very high UV resistance, making it ideal for tough weather conditions. In fact, polycarbonate is up to 250 times stronger than glass against high-impact forces, and it is what bulletproof glass is made from. This material can also be tinted and coated with scratch and UV-resistant treatments for added protection and versatility. Similar to acrylic, polycarbonate windows are semi-rigid and provide excellent visibility. However, polycarbonate may be initially more expensive than acrylic, but its superior durability may save you money in the long run by reducing the need for frequent replacements.
Tempered Glass Windows
Tempered glass is also an option for boat windows, offering superior clarity and scratch resistance compared to acrylic and polycarbonate. However, glass is more fragile and susceptible to breaking, especially when compared to polycarbonate. Additionally, tempered glass may not be suitable for windows with unique shapes or bends, as it is less flexible than the other two materials.
In summary, when choosing the right window type for your boat, consider the advantages and disadvantages of each material. Acrylic windows offer strength and durability, polycarbonate provides exceptional impact resistance and UV protection, while tempered glass delivers superior clarity and scratch resistance. Ultimately, the decision should be based on your specific needs, budget, and the conditions your boat will be exposed to.
Mastering the Art of Driving a Boat Sideways
You may want to see also
Select the right window compound: Use a marine compound, not an adhesive
Marine compounds are designed to withstand the harsh aquatic environment, including saltwater, UV light, and extreme temperatures. They are essential for bonding and sealing the components of a boat, such as the hull, deck, and hatches. Therefore, it is crucial to select a marine compound instead of an adhesive when installing boat windows.
Marine compounds offer exceptional bonding, gap-filling, and sealing properties, ensuring the safety and longevity of the boat. They are specifically formulated to be compatible with the materials commonly used in boat construction, such as metal, plastic, and fiberglass.
When selecting a marine compound, it is important to consider the type of material being bonded or sealed. For example, an adhesive that can adhere to a wide range of materials may be preferable for bonding metal or plastic. Additionally, if you are sealing a window, choose a compound with waterproofing properties to prevent leaks.
The marine environment in which the boat will operate should also be considered when selecting a compound. For instance, if the boat will be exposed to UV rays, it is essential to choose a compound that is UV resistant to protect against sun damage.
The surface or substrate where the compound will be applied is another crucial factor. If the surface is irregular or porous, a compound that can fill gaps effectively is necessary to ensure a strong bond.
Finally, consider the amount of movement or vibration in the area where the compound will be applied. If the boat component is subject to significant movement or vibration, it is essential to choose a flexible compound that can withstand these conditions without compromising the bond.
By selecting the right marine compound and taking into account the specific application requirements, you can ensure a successful and durable installation of your boat windows.
Cracking Boat Engine Blocks: Cold Temperatures and Their Impact
You may want to see also
Reassemble the window: Drill holes, apply sealant, and insert the window
To reassemble the window, you will need to drill holes, apply sealant, and insert the window. Here is a detailed guide on how to do this:
Drilling Holes:
- Determine the ideal location for the window, ensuring sufficient clearance on both the inside and outside of the hull.
- Apply masking tape to the exterior of the hull, extending at least six inches from the intended drilling location. This will protect the gel coat and prevent splintering. If your boat has a finished bilge liner, mask off the interior as well.
- Drill a pilot hole using a drill bit that matches the size of the pilot bit on your hole saw. Drill from the exterior of the hull, through the gel coat and fiberglass.
- Insert the hole saw bit into the pilot hole from the inside of the bilge. Lightly score the fiberglass by applying pressure and rotating the hole saw bit. This will help prevent chipping when the hole saw finishes the cut.
- Finish drilling the hole from the outside of the boat. Start with the drill in reverse to wear through the gel coat, then switch to forward once you've worn through it.
- Chamfer the gel coat around the perimeter of the hole to prevent superficial cracks. Use sandpaper to create a 45-degree angle between the gel coat and the fiberglass underneath.
Applying Sealant:
- Clean the surface around the hole with adhesive remover or acetone.
- Choose the appropriate sealant for your application. For below the waterline or for additional bonding strength, use a urethane-based sealant such as Sikaflex 291 or 3M 5200. For above the waterline, a silicone sealant is often acceptable.
- Apply a generous bead of sealant around the flange of the window frame. When you push the window into place, the sealant should evenly ooze out around the perimeter of the hole.
- If additional screws are required to secure the window, apply a bead of sealant into each screw hole before installing them.
- Inside the hull, run a bead of sealant around the interior of the hole and snugly tighten the collar or nut.
- If desired, you can overcoat the urethane sealant with silicone to maintain a clean, white appearance.
- Use a plastic scraper or a scrap of Formica to remove excess sealant. Avoid using razor blades as they can damage the surface.
- Wipe away any remaining filmy excess sealant with a scrap of foam rubber and soapy water.
Inserting the Window:
- With the sealant applied, you are now ready to insert the window into the opening. This is typically a two-person task. One person should hold the window in place while the other centers the clamp ring on the inside of the window and installs the screws.
- Use a radius measurement tool to double-check the window's alignment within the opening.
- Install the window screen by inserting it into the screen track and pushing it up and pivoting it into place.
Boat Registration in Illinois: Where to Pay?
You may want to see also
Frequently asked questions
The most common installation method is a clamp-in style window. Remove the screws on the trim ring from inside the vehicle, then push the window out of the opening by applying force from the inside. You may also need to release the sealant from under the window flange outside of the vehicle using a thin putty knife.
You have a few options, each with their own pros and cons. Acrylic is easy to handle, thermoform, and polish. Polycarbonate is extremely tough and durable but can be more expensive and is vulnerable to UV light. Tempered glass is strong, easy to seal, and shatters into small pieces instead of large shards when broken, but it can't be used for curved windows.
You should use a marine compound, not a general adhesive. Avoid products like 3M's 5200.
You can choose from polycarbonate (Lexan), acrylic (Plexiglas), or tempered glass. Polycarbonate is strong but easily scratched and vulnerable to UV light. Acrylic is strong enough for most marine applications, more resistant to scratching and UV light, and is more affordable. Tempered glass is the best material for marine windows as it is strong, scratch-resistant, and impervious to UV light, but it can break under severe impact and can't be used for curved windows.
When drilling into polycarbonate or acrylic, make sure the holes are oversized. Don't countersink the screws, instead, let the screw heads rest flush on the surface. Clean the areas to be sealed with paint thinner and use a generous amount of sealant. If using different types of metal for frames and fasteners, coat your fasteners in a corrosion inhibitor.