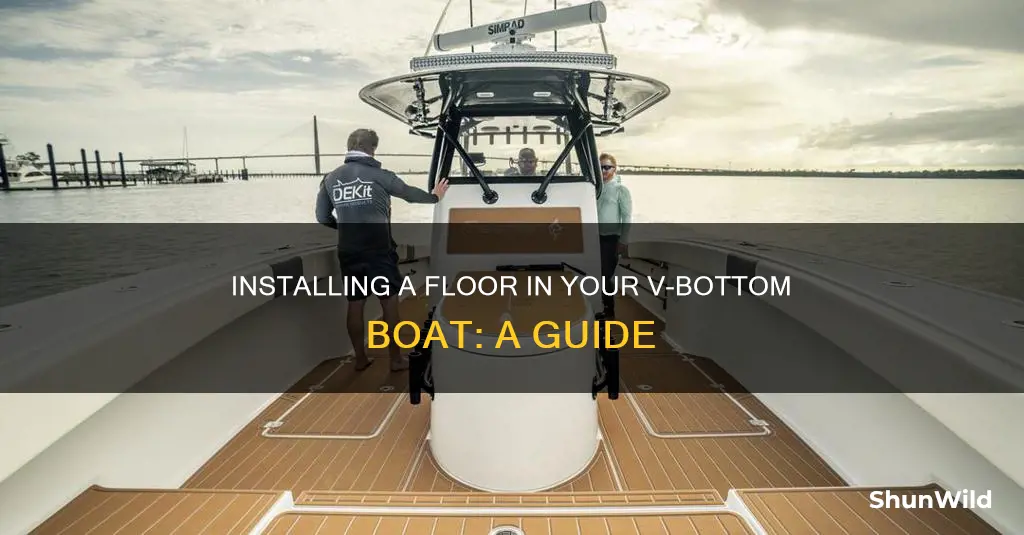
Installing a floor in a V-bottom boat can be a challenging task, but it is doable with the right tools and knowledge. The process involves reinforcing the boat's hull, adding stiffness and support, and creating a comfortable and functional space for occupants. The type of flooring material, such as plywood or aluminium tubing, and the method of installation, such as welding or screwing, are important considerations. Safety precautions must be taken when using power tools and working with chemicals. The floor's design should also take into account the weight, stability, and structural integrity of the boat.
What You'll Learn
Using treated or marine plywood for flooring
Marine-grade plywood is made of thin layers of high-quality hardwood held together with waterproof glue. It is not entirely waterproof but it is water-resistant, lightweight, strong, and durable. It can last 15 to 25 years, especially when coated with a protective finish.
Marine-grade plywood is used for wooden boat floors exposed to a lot of water. It is made with at least five thin layers or plies of 100% hardwood veneer, which is generally stronger and harder and has a finer grain than softwood. The plies are arranged in sheets or perpendicular layers to strengthen the plywood. Cross-lamination gives marine plywood even more strength. The plies may have knots but no knotholes.
The waterproof glue between the wood layers will not delaminate or fall apart when the plywood is exposed to moisture, very high humidity, or boiling temperatures. It is also resistant to termites and ants.
If you are using marine-grade plywood for your boat floor, it is important to protect it with a water-resistant finish. To preserve marine plywood, use a clear penetrating epoxy. This type of sealant takes more time to apply than a polyurethane sealer but requires less maintenance in the long term.
Alternatively, you can use treated plywood for your boat floor. However, it is important to note that the chemicals used in pressure-treated wood can cause corrosion in aluminum boats. If you choose to use treated plywood, be sure to seal it with a protective finish such as epoxy resin or Thompson water seal.
The Mysterious Sinking of Paul Allen's Luxury Yacht
You may want to see also
Reinforcing the boat's hull and transom
Reinforcing the hull and transom of a boat is a crucial step in ensuring its longevity, safety, and performance. Here is a comprehensive guide on how to reinforce the hull and transom of your V-bottom boat:
Planning and Materials
Before beginning the reinforcement process, it's important to plan the design of your boat's flooring and gather the necessary materials. For the flooring itself, you will need 3/4-inch treated or marine plywood. Additionally, you will require stainless steel screws, a screw gun or drill motor with a screw tip, and adhesive polyurethane caulk.
Hull Reinforcement
To reinforce the hull, you will create a supporting framework using cleats and deckbeams. First, determine the desired height of the floor and subtract 1 1/2 inches. Mark the inside of the hull at the bow and stern at this adjusted height, then connect these marks with a straightedge. This line will be the top of your support cleats. Measure and cut the support cleats with a bevel angle that matches the angle of the hull. Drill pilot holes along the cleats about every 8 inches. Apply a liberal amount of adhesive caulk to the backside of the cleats and attach them to the inside of the hull, screwing them in place.
Next, measure from stem to stern along the cleats and mark 16-inch intervals for the deckbeam locations. Cut deckbeams to fit between the cleats, drilling pilot holes and applying adhesive caulk before screwing them down. Cut additional cleat material to fill the spaces between the beams, ensuring full support for the edges of the flooring.
Transom Reinforcement
The transom, or the rear of the boat, is an essential structural component that transfers the power of the motor to the hull. Over time, the transom may weaken due to water damage, rot, or other factors, compromising the safety and performance of the boat. To reinforce a fiberglass transom, follow these steps:
- Remove any hardware, such as cleats, brackets, and lights, attached to the transom.
- If the transom is damaged, remove any rotten wood.
- Thoroughly clean the transom to remove any dirt or debris.
- Sand the transom to create a rough surface that will help new materials adhere.
- Cover the surrounding area with plastic sheeting to protect it from spilled resin or epoxy.
- Cut a piece of marine plywood to the exact size of the transom.
- Coat the plywood with resin to seal it and prevent moisture penetration.
- Apply layers of fiberglass cloth to the plywood and transom, wetting them with resin to saturate them thoroughly. Three layers of fiberglass cloth are recommended.
- Allow the fiberglass to cure for 24-48 hours, or according to the manufacturer's instructions.
- Fill any gaps or holes with epoxy filler and sand the transom to create a smooth surface.
- Apply a coat of marine paint to protect the transom from the elements.
- Reattach any hardware that was removed.
Final Steps
Once the hull and transom reinforcement is complete, you can continue with the flooring installation. Measure and cut the plywood flooring to fit, then mix a batch of fiberglass resin and acetone to thin it to a watery consistency. Apply this mixture to the plywood and the supporting framework to provide additional waterproofing and stability.
Apply adhesive caulk to the top edge of the cleats, beams, and filler pieces, then place the plywood pieces in position and screw them down. Allow the adhesive to dry, trimming off any excess. Finally, caulk the edges of the flooring to the sides of the hull to create a watertight seal. Mix another batch of fiberglass resin and roll it onto the flooring for further waterproofing and impact resistance.
Always exercise caution when using power tools and avoid contact with resin. It is also recommended to work in small batches and avoid high-air temperatures or direct sunlight, as these conditions can accelerate the hardening process.
Wax Sources for Paper Boat Crafts: Creative Options
You may want to see also
Adding buoyancy with dead-air space
The floor of a V-hull boat can add stiffness and support to the hull. It creates a dead-air space just above the hull's bottom, which can add buoyancy to a boat made from materials with no inherent buoyancy, such as fiberglass, steel, or aluminium.
To install a floor in a V-hull boat, you will need the following:
- Screw gun or drill motor with a screw tip
- Adhesive polyurethane caulk
- 3/4-inch treated or marine plywood
- Stainless steel screws
- 1/8-inch plywood
First, cut a strip of 1/8-inch plywood 4 inches wide. Cut the factory edge from the sheet to ensure that at least one edge is straight for use as a straightedge. Next, determine the desired height of the floor and subtract 1 1/2 inches from the height. Mark the inside of the hull at the bow and stern at this adjusted height. Connect these marks with the straightedge. This will be the top of the support cleats. Mark out both sides of the hull.
Hold a short straightedge from side to side (athwartships) between these marks on opposite sides. Lay the bevel square vertically onto the hull and the straightedge and tighten the nut on the square. Set up the table saw bevel angle as indicated by the square. Cut the support cleats on this angle. This will allow the cleats to project from the sides of the hull on a horizontal plane. Cleating should measure one and a half by one and a half minus the bevel. Drill pilot holes about every 8 inches along the cleats. Apply a liberal bead of adhesive caulk onto the backside of the cleats. Immediately apply the cleats to the inside of the hull, dressing the top of the cleat to the line. Screw the cleats into the hull and allow the adhesive to cure fully for 12 to 24 hours.
Measure from stem to stern along the cleats and mark out 16-inch intervals. This will indicate the deck beam locations. Measure athwartships between these marks and cut 1 1/2 by 1 1/2 deck beam material from the treated lumber. Crosscut the deck beams at the athwartship measurements. Drill a pilot hole near the ends of the deck beams where it laps over the cleats. Apply a dab of adhesive caulk at the lap and screw the beams down to the cleats. Cut additional cleat material and crosscut to act as a filler to fit between the beams to fully support the edges of the flooring.
Measure the areas to be decked and cut the plywood to fit. Mix a batch of fiberglass resin with acetone to thin the resin to an almost watery consistency. Add the catalyst to the resin and immediately roll on a coat to both sides of the plywood and on all surfaces of the supporting framework. Allow the resin to soak into the wood and harden to provide additional waterproofing and stability to the materials.
Apply a heavy bead of adhesive caulk to the top edge of the cleats, beams, and filler pieces. Immediately place the plywood pieces in position on the framing and screw the plywood down to the framing. Allow the adhesive to dry and trim off any adhesive squeeze-out present above the flooring.
Caulk the edges of the flooring to the sides of the hull to provide a watertight seal and trap the air beneath to create the dead-air space. Allow the caulk to dry. Mix another thin batch of fiberglass resin and roll it onto the flooring to provide additional waterproofing and some impact resistance.
When installing a floor in a V-bottom boat, it is important to consider the weight and height of the floor. You may want to run stringers across the boat to screw down the floor or use foam to secure the floor. Additionally, consider the need for cross support and structural integrity, especially when removing seats or making other modifications.
Boat Hull Waxing: A Guide to Frequency and Maintenance
You may want to see also
Using fiberglass resin for waterproofing
When installing a floor in a V-hull boat, it is important to consider the benefits of the supporting framing and flooring. The floor can add stiffness and support to the hull, as well as provide additional buoyancy to boats made from materials with no inherent buoyancy, such as fiberglass. The flooring also provides support for deck equipment and added comfort by insulating occupants from cold water temperatures.
To install a floor in a V-hull boat, one must follow a series of steps, including measuring, cutting, and drilling, as well as applying adhesive and screws to secure the flooring in place. One crucial step in this process is waterproofing the plywood subfloor with fiberglass resin.
Fiberglass resin is a crucial component in creating a durable and waterproof finish for the boat's floor. The process of using fiberglass resin for waterproofing involves the following steps:
Step 1: Prepare the Surface
Before applying the fiberglass resin, ensure that the plywood surface is clean, dry, and free of any contaminants such as dust, paint, grease, or oil. Sand the surface with coarse sandpaper and power sanders to achieve a smooth finish. Clean the surface with acetone to remove any remaining dust or grease. This step is essential for ensuring the resin adheres properly to the surface.
Step 2: Mix the Fiberglass Resin
The fiberglass resin needs to be mixed with acetone to achieve a watery consistency. This will allow it to penetrate the plywood more effectively. Add the catalyst to the resin and mix thoroughly. It is important to work in small batches as the resin has a short shelf life and can cure quickly, especially in high temperatures.
Step 3: Apply the First Coat of Resin
Once the resin is mixed, apply a coat to both sides of the plywood and all surfaces of the supporting framework. Allow the resin to soak into the wood and harden, providing additional waterproofing and stability. This step ensures that the plywood is thoroughly sealed and protected from moisture.
Step 4: Apply the Second Coat of Resin
After the first coat has cured, mix another batch of fiberglass resin and roll it onto the flooring. This second coat provides additional waterproofing and impact resistance. It creates a strong, durable seal that protects the floor from water intrusion.
It is important to work cautiously when using power tools and avoid contact between the resin and your skin. Always follow safety guidelines and wear proper protective gear, including gloves, eye protection, and a respirator mask.
Angelina's Identity in Romancing the Stone: Unveiling the Mystery
You may want to see also
Installing a flat floor with square aluminium tubing
Installing a flat floor in a V-bottom boat can be done in several ways. One method is to use square aluminium tubing, which can be laid on top of each rib to support marine plywood. However, it is important to note that removing the seats can affect the structural integrity of lightweight boats, so additional bracing may be required.
To secure the aluminium tubing to the ribs, one suggestion is to weld the bottom lip of the tubing to the end of the rib. Another option is to use rivets and brackets, or L-shaped pieces that are riveted to the tubing and the rib. It is also recommended to include vertical supports attached to the ribs for additional stability.
Before installing the floor, it is important to determine the desired height and mark the inside of the hull at the bow and stern accordingly. This will be the guide for the support cleats. After marking, hold a straightedge from side to side between these marks and lay the bevel square vertically onto the hull, tightening the nut. Set the tablesaw bevel angle as indicated by the square. Cut the support cleats at this angle, allowing them to project horizontally from the sides of the hull. Drill pilot holes along the cleats and apply adhesive caulk before attaching them to the inside of the hull.
Measure the distance from stem to stern along the cleats and mark 16-inch intervals for the deckbeam locations. Cut the deckbeams to size and drill pilot holes before attaching them to the cleats with adhesive caulk. To support the edges of the flooring, cut additional cleat material to fit between the beams.
Measure and cut the plywood to fit the areas to be decked. Mix a batch of fiberglass resin with acetone to thin it and add the catalyst to the resin. Apply a coat to both sides of the plywood and all surfaces of the supporting framework. Allow the resin to soak in and harden, providing additional waterproofing and stability.
Apply adhesive caulk to the top edge of the cleats, beams, and filler pieces. Place the plywood in position and screw it down to the framing. Let the adhesive dry, then trim off any excess. Caulk the edges of the flooring to the sides of the hull to create a watertight seal and trap air beneath, adding buoyancy. Apply another thin batch of fiberglass resin to the flooring for further waterproofing and impact resistance.
This process will result in a flat floor installed with square aluminium tubing in a V-bottom boat, ensuring stiffness, support, and buoyancy.
Repairing Yamaha Tach: A Step-by-Step Guide for Boat Owners
You may want to see also