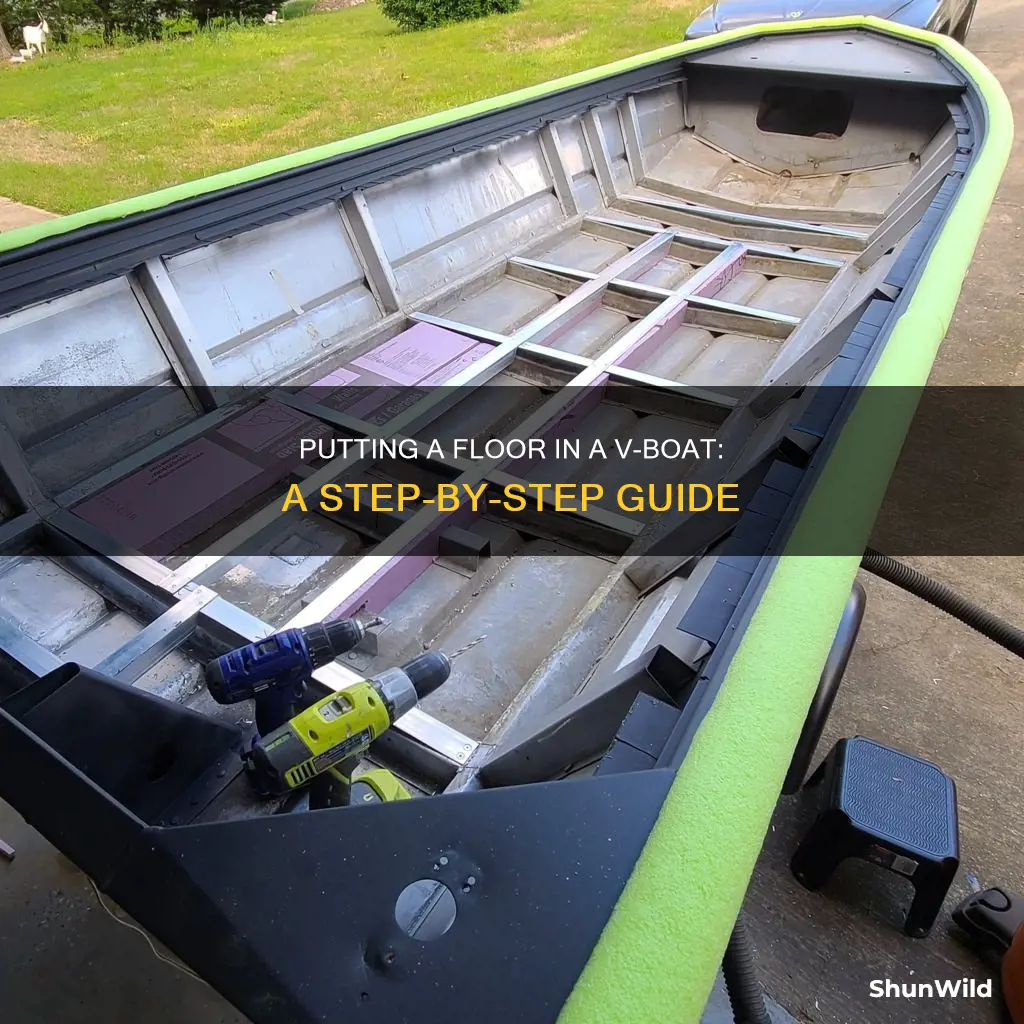
Installing a floor in a V-hull boat can be a challenging task, but with the right tools and knowledge, it is certainly achievable. The process involves several steps, including reinforcing the boat's transom, building a windshield, and carefully measuring and cutting the flooring material. It is important to use the correct type of wood or aluminium and to ensure that the floor is securely attached to the hull to avoid any accidents or damage.
What You'll Learn
Choosing the right material for your boat floor
The right boat flooring material will protect your vessel and add to its style. Choosing the wrong material can lead to expensive cleaning, replacements, and repairs. The best boat flooring material will depend on its durability, cost, aesthetic value, and toughness. Here are some of the most popular boat flooring materials and their pros and cons.
Wood
Wood has been the flooring material of choice for boat and shipbuilders for thousands of years due to its durability and natural ruggedness. Oak is a popular choice for marine flooring because of its strength, flexibility, durability, and water resistance. However, wood can be expensive and it tends to fade and rot over time if not properly maintained. Wood is also slippery and tough on the feet, so it may not be the most comfortable option.
Linoleum or Vinyl
Linoleum or vinyl flooring can be a good option for boat cabins but not decks, especially if it is in an enclosed space with air conditioning. Vinyl flooring is durable, water-resistant, UV-resistant, comfortable to use, and easy to maintain. However, it can be slippery when wet and may not dissipate heat well, which can make it uncomfortable to stand on in hot weather.
Marine Carpet
Marine carpet has improved over the years and can be a durable and comfortable option. Some marine carpets are also water-resistant. However, marine carpet is prone to accumulating dirt and bacteria, which can lead to rot and an unkempt appearance. Marine carpet is also not UV-stable, so it may fade over time.
Aluminum
Aluminum is a unique material that can last for 35+ years, but it can be hard on the feet and expensive. Additionally, aluminum can only be used in freshwater as saltwater will cause it to corrode.
Foam
Foam boat flooring is anti-slip, antibacterial, and antifungal, making it a comfortable and reliable option. It is also UV-stable and can be used in both freshwater and saltwater. Foam boat flooring is easy to maintain and can last up to 7 years with proper care.
PVC Tiles
PVC flooring tiles are affordable, durable, and resistant to fading, scratches, and staining. They are also slip-resistant, making them a good choice for boats that will be used outdoors or in areas with a lot of traffic. However, PVC tiles are not UV-stable, so they will need to be installed in a covered area or with a UV-protective coating.
Drainage Tiles
Drainage tiles are a good option if you want to protect your boat from water damage, as they allow water to drain away from the surface of your boat. They also provide an anti-slip surface, which is ideal for boats used in wet or muddy conditions.
Marine Vinyl
Marine vinyl flooring is designed to withstand harsh conditions and is often used on yachts and ski boats. It is waterproof and UV-resistant, but it can be slippery when wet.
When choosing a boat flooring material, it is important to consider your budget, the type of use your boat will get, and the specific features and benefits of each material.
Repairing a Leaky Boat Seam: Quick and Easy Fixes
You may want to see also
Preparing the hull for the new floor
Preparing the hull for a new floor is a crucial step in ensuring a sturdy and long-lasting installation. Here is a detailed guide on how to prepare the hull for a new floor in a V-shaped boat:
Firstly, remove all seats, consoles, and fixed items from the old floor. It is important to disconnect any wiring or connections before removing them to avoid damage. Leave a trim of around 3 inches of the old flooring around the edge of the boat. This trim will ensure you don't accidentally puncture the boat's side and will also provide sturdy support for the new floor as it is moulded into the framework.
Next, you will need to determine the desired height of the new floor. Measure and mark the inside of the hull at the bow and stern, subtracting 1.5 inches from the desired height. These marks will be the reference points for the support cleats. Use a straightedge to connect these marks, marking out both sides of the hull.
Now, you will need to cut the support cleats to size. Hold a short straightedge across the marks on opposite sides of the hull. Place the bevel square vertically against the hull and straightedge, tightening the nut. Set the table saw bevel angle according to the indication on the square. Cut the cleats along this angle, allowing them to project horizontally from the hull sides. The cleats should measure 1.5 by 1.5 inches, minus the bevel. Drill pilot holes approximately every 8 inches along the cleats.
Apply a liberal amount of adhesive caulk to the backside of the cleats and immediately attach them to the inside of the hull, aligning the top of the cleat with the reference marks. Screw the cleats into the hull and allow the adhesive to cure for 12 to 24 hours.
Measure the distance from stem to stern along the cleats and mark 16-inch intervals to indicate the deck beam locations. Measure and cut the deck beam material accordingly. Drill pilot holes where the deck beams overlap the cleats and apply adhesive caulk before screwing the beams down. Cut additional cleat material to fit between the beams, ensuring full support for the flooring edges.
With the framework in place, it is now time to prepare the plywood flooring. Measure the areas to be decked and cut the plywood to fit. Create a thin mixture of fiberglass resin and acetone, adding the catalyst to initiate the hardening process. Apply a coat of this mixture to both sides of the plywood and all surfaces of the supporting framework. Allow the resin to soak in and harden, providing additional waterproofing and stability.
Finally, apply a heavy bead of adhesive caulk to the top edge of the cleats, beams, and filler pieces. Place the plywood pieces onto the framework and screw them down. Allow the adhesive to dry before trimming off any excess.
By following these steps, you will have successfully prepared the hull for a new floor in your V-shaped boat, creating a sturdy and watertight installation.
Boat Repair Guide: BDO Essentials You Need to Know
You may want to see also
Cutting the plywood to fit the V-hull
First, you'll need to determine the desired height of your floor. Measure from the front interior "point" of the boat to the stern, marking the side of the boat in increments along the curve. Transfer these measurements to a large piece of cardboard or plywood, connecting the dots to create your cutting line. It's important to cut slightly outside the line to ensure a snug fit, as you can always trim excess material later.
Now, set up your plywood next to the boat at the precise elevation and angle, ensuring it is parallel to the boat. Use a straightedge or a stick to trace the contour of the hull onto the plywood. This will give you a precise line to cut along. When cutting, use a jigsaw and cut at an angle less than 90 degrees to prevent the bottom edge of the plywood from touching the side of the boat before the top edge is in place.
An alternative method is to use the old pieces of the floor as a template. If you have access to these, trace their shape onto your new plywood, allowing for a little extra room if you plan to fold the carpet underneath. This method can save time and ensure an accurate fit.
If you're working with a deep-V hull, you may need to consider clamping, vacuum bagging, or using weights to bend the plywood to the curve of the hull. This can be a challenging process, and it's important to ensure that any method you use is safe and structurally sound.
Once you have cut your plywood to size and shape, you can move on to the next steps of the flooring installation, including waterproofing and fixing the floor in place. Remember to always work carefully when using power tools and always wear the appropriate safety gear.
The Luxury Yachts of Below Deck Mediterranean
You may want to see also
Attaching the floor to the hull
The next step is to measure from stem to stern along the cleats and mark 16-inch intervals for the deck beam locations. Cut the deck beams to size and drill pilot holes near the ends. Apply adhesive caulk and screw the beams down to the cleats. To ensure full support for the flooring edges, cut additional cleat material to act as fillers between the beams. Measure the areas to be decked and cut the plywood to fit.
To provide additional waterproofing and stability, mix a batch of fiberglass resin with acetone to thin it out, then add the catalyst. Apply a coat to both sides of the plywood and all surfaces of the supporting framework. Allow the resin to soak into the wood and harden. Apply a heavy bead of adhesive caulk to the top edge of the cleats, beams, and filler pieces. Place the plywood pieces on the framing and screw them down. Let the adhesive dry, then trim off any excess.
To create a watertight seal, caulk the edges of the flooring to the sides of the hull. This will also trap the air beneath, creating a dead-air space that adds buoyancy to the boat. Allow the caulk to dry and apply another thin batch of fiberglass resin to the flooring for extra waterproofing and impact resistance.
Best Boats for Wakeboarding: Creating the Perfect Wake
You may want to see also
Waterproofing and sealing the new floor
Prepare the Surface:
Before you begin waterproofing, ensure that the plywood surface is thoroughly cleaned and free of any dirt, debris, or residue. This step ensures that the sealant adheres properly to the wood.
Seal the Wood:
Use a high-quality sealant specifically designed for marine use, such as a two-part epoxy sealer or a marine-grade varnish. Apply the sealant generously to all surfaces of the plywood, including the top, sides, and bottom. Pay special attention to the edges and knots, as these areas are more susceptible to moisture infiltration. You can use a brush or roller to apply the sealant, following the manufacturer's instructions for the best results. Allow the sealant to dry completely according to the product's directions.
Protect Screw Holes:
Before screwing the plywood into place, it is essential to protect the screw holes to prevent moisture infiltration. Use marine-grade silicone to seal around each screw hole. This creates a watertight barrier that prevents water from seeping through the screw holes.
Apply Fiberglass Resin:
As mentioned in the previous section, mix a batch of fiberglass resin with acetone to thin it out. Add the catalyst to the resin and immediately apply a coat to both sides of the plywood and all surfaces of the supporting framework. Allow the resin to soak into the wood and harden, providing additional waterproofing and stability.
Caulk the Edges:
Use a high-quality adhesive caulk to seal the edges of the flooring to the sides of the hull. This creates a watertight seal that traps the air beneath, adding buoyancy and ensuring the floor is securely attached to the hull. Allow the caulk to dry completely before proceeding.
Final Waterproofing Layer:
For added protection, mix another thin batch of fiberglass resin and roll it onto the flooring. This provides a final layer of waterproofing and also offers some impact resistance. Ensure you follow the manufacturer's instructions and safety guidelines when working with fiberglass resin.
By following these steps, you can effectively waterproof and seal the new floor of your V-hull boat, ensuring a long-lasting and safe boating experience.
Exploring the World of Yachts: What Makes Them Unique?
You may want to see also
Frequently asked questions
The supporting framing and floor can add stiffness and support to a hull. The flooring creates a dead-air space just above the hull's bottom that can add buoyancy to a boat made from materials with no inherent buoyancy, such as fiberglass, steel, or aluminum. The floor also provides support for additional deck equipment such as winches, consoles, and seats. Flooring can also provide added comfort by separating the occupants' feet from bilge water and insulating them from cold-water temperatures and the pumping action of the hull when the boat is at high speeds.
Marine-grade plywood is a popular option for boat flooring, but some people also use aluminum or vinyl. It's important to consider the weight of the material, as something too heavy will affect the performance of the boat. It's also important to consider whether the material is slip-resistant and waterproof or water-resistant.
First, determine the desired height of the floor and mark the inside of the hull at the bow and stern. Cut support cleats on a bevel so that they project from the sides of the hull on a horizontal plane. Drill pilot holes and apply adhesive caulk to the backside of the cleats before attaching them to the inside of the hull. Measure and cut deckbeams, drilling pilot holes and applying adhesive caulk before screwing them down. Cut plywood to fit the area and apply a coat of fiberglass resin to both sides of the plywood and the supporting framework. Apply adhesive caulk to the top edge of the cleats, beams, and filler pieces, then place the plywood in position and screw it down. Caulk the edges of the flooring to the sides of the hull to create a watertight seal.