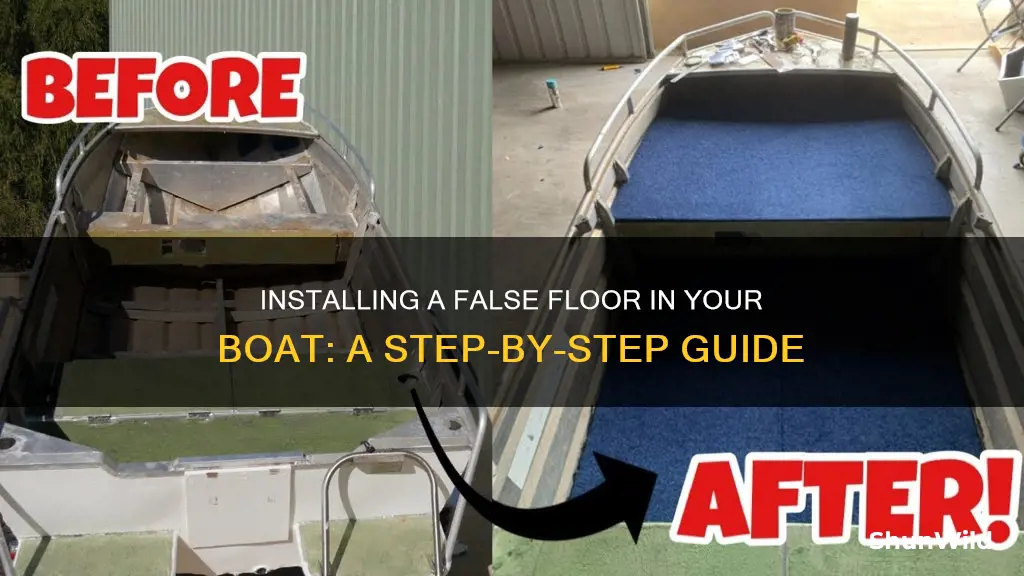
Boat floors are prone to wear and tear, and sometimes need to be replaced. One option for boat owners is to install a false floor. A false floor can be made using treated pine and exterior ply sheets. The frame can be made from timber, and the gaps between the floor and the boat's sides can be covered with carpet. One builder used 12mm exterior ply sheets, which were sealed and screwed down, and then covered with marine carpet. Another boat owner reinforced the interior floor of their boat with 1708 and added a false floor made from 1/2 coosa.
Characteristics | Values |
---|---|
Materials for boat false floor | Treated pine, CCA-treated timber, KD treated pine, H3-rated timber, H4-rated timber, H5-6-rated timber, Marine ply, Luan/Meranti, Epoxy sealer, Marine paint, Marine carpet, Coosa, Divinycell, Nidacore, CSM cloth, Biax tape, PVC, Aluminium, Plywood, Conventional wood, Vinyl, Marine carpet, Aluminium, PVC flooring tiles, Rubber |
Boat false floor construction tips | Seal the timber framing with epoxy sealer and marine paint, seal all edges of the plywood floor, use stainless steel screws, use construction adhesive, use marine epoxy, seal the timber with varnish, use PVA or alphalactic resins, use epoxy for bonding, use epoxy thickened with filler, use 5200 for bonding, use biax over divinycell, use epoxy and biax tape/CSM cloth for lighter option, use stringers for support, use PVC for cable management, use epoxy resin, use vacuum bag |
What You'll Learn
Treating the wood to prevent rot
Wood rot is a common problem that can cause serious damage to boats if left untreated. To treat wood and prevent rot, you must first understand the conditions that cause rot. There are two main types of rot that infect wooden boats: wet rot and dry rot. Wet rot occurs when unprotected timber is in constant contact with moisture, while dry rot occurs when unprotected timber is repeatedly wetted and dried out.
To prevent rot, it is important to keep your boat dry and well-ventilated. Fix any leaks promptly and ensure good airflow throughout the boat to prevent moisture accumulation. Seal all wood surfaces with an appropriate sealant such as epoxy, polyurethane, or varnish, following the manufacturer's instructions.
If wood rot does occur, remove the affected wood and replace it with a new piece. Treat the surrounding wood with a fungicide to kill any remaining spores and prevent further spread. One inexpensive remedy is ethylene glycol, which is found in car antifreeze and is toxic to most wood rot organisms. Alternatively, you can use a borate solution, such as Sodium Octaborate Tetrahydrate, which can be bought as a solution or solid that is mixed with water.
For long-term preservation of softwoods, a glycol borate ester solution is recommended. This solution is made by heating ethylene glycol with borax and can be used to treat teak decks and swim platforms. However, it is time-consuming to work with and requires a long drying time before coating.
Another option is to use a commercial product such as System Three EndRot, which includes a borate-based anti-rot powder, sealers, and fillers to repair damage. For smaller projects, a DIY formula using ethylene glycol or propylene glycol can be effective. Both are biodegradable and classified as non-toxic by the US Fish and Wildlife Service.
When treating wood, it is important to consider the type of wood and its intended use. Teak, for example, is highly resistant but not light or economical. Pressure-treated lumber may seem like a solution but it is not recommended for interior use as it is ugly, warps, and does not take coatings well. Western red cedar is a good alternative as it is light, rot-resistant, and has a reputation for durability.
In summary, preventing and treating wood rot is crucial for boat maintenance. By keeping your boat dry, sealing wood surfaces, and promptly addressing any rot, you can maintain the quality of your boat for years to come.
Wooden Boat Show Dates and Times Revealed
You may want to see also
Sealing the wood to prevent water intrusion
Wood is a traditional boat floor material that can serve you well with regular maintenance. However, wood is not naturally waterproof, so sealing is necessary to prevent water intrusion and the damage that comes with it. Here is a step-by-step guide to sealing wood for a false floor in a boat:
Step 1: Prepare the Wood
Before applying any kind of sealant, it's important to prepare the wood surface. Start by removing any paint or other coatings from the wood using strippers or sandpaper. This will ensure that the sealant adheres properly to the wood. After removing any coatings, clean the wood with a vacuum, tack cloth, or a cloth soaked in mineral spirits to remove any residue or grease. If the wood is new, you can skip the cleaning process.
Step 2: Choose the Right Sealant
There are several types of sealants available, including synthetic sealants, natural oils, and stain/sealer combinations. Synthetic sealants form an impermeable barrier on the wood, preventing water from penetrating. Natural oils, on the other hand, penetrate and harden within the wood's cells, maintaining its natural look and feel. Stain/sealer combinations are designed for outdoor use and provide protection against harsh conditions, including UV rays, mould, and mildew. Choose the type of sealant that best suits your needs and preferences.
Step 3: Apply the Sealant
Once you have chosen the right sealant, it's time to apply it to the wood. Stir the sealant gently with a paint-stirring stick, being careful not to create bubbles. Then, use a brush, foam brush, or applicator pad to apply the sealant to the wood. Allow the sealant to dry completely before applying additional coats, following the instructions on the product label. Sand the surface lightly between coats to improve adhesion.
Step 4: Cure the Wood
After applying the final coat of sealant, allow the wood to cure for several days before using it or placing any objects on top of it. This will ensure that the sealant has fully hardened and will provide the best protection against water intrusion.
Maintenance:
Depending on the type of sealant used, you may need to reapply it periodically to maintain the waterproofing. Natural oils, for example, may need to be reapplied up to twice a year. Always follow the manufacturer's instructions and recommendations for the specific sealant you have chosen.
Boat Show Shoes: Picking the Right Pair for the Deck
You may want to see also
Using stainless steel screws to fix the timber together
When fixing timber together to create a false floor in a boat, it is important to use the right type of screws. Stainless steel screws are ideal for this purpose, as they are highly corrosion-resistant, especially in exterior settings.
There are several types of stainless steel screws available, including self-drilling fasteners and wood screws. Self-drilling fasteners are designed to drill into both timber and steel, ensuring a strong and secure connection. They feature a countersunk head and are available in carbon or stainless steel. When fixing timber into steel, it is crucial to use a self-drilling fastener designed for this specific application. Some of these fasteners have special wings that create a wider hole in the timber than in the metal, ensuring a proper fit for the screw.
Wood screws, on the other hand, are commonly used for timber-to-timber joints, but they are especially suitable for steel-to-timber and panel-to-timber connections. It is important to insert wood screws by turning them and not by driving them with a hammer, as this will reduce their load-carrying capacity. The diameter of a wood screw typically ranges from 6mm to 20mm for coach screws and 4mm to 8mm for countersunk screws. To prevent the wood from splitting, it is recommended to pre-drill holes for screws with a diameter greater than 5mm.
When selecting screws, consider the length and diameter required for your specific application. For example, timber screws are available in various lengths, such as 75mm, 100mm, 150mm, and more. Additionally, the type of timber and its moisture content can influence the choice of screws. For timber with a moisture content above 16%, concealed clips are not recommended due to the natural movement of the wood.
By following these guidelines and selecting the appropriate stainless steel screws, you can effectively fix timber together to create a sturdy and durable false floor in your boat.
Who Manages the Road to Cahookie Creek's Boat Launch?
You may want to see also
Using construction adhesive to join timbers together
Construction adhesive is a versatile product used in building, renovating, and finishing homes. It is available in cans, squeeze tubes, and caulking tubes, and has a thick, pasty consistency that can be applied with a putty knife or notched trowel. When using construction adhesive to join timbers together for a false floor in a boat, there are several factors and techniques to consider.
Firstly, it is important to select an appropriate construction adhesive for the task. Some adhesives are specifically designed for certain materials, such as "for ceramic tile only", while others are more versatile and can be used for a wide range of adhesive tasks. For joining timbers, look for an adhesive that is suitable for wood and check if it is intended for exterior use, as this will ensure it can withstand moisture and temperature changes. Additionally, choose an adhesive that is waterproof or water-resistant, especially if your boat will be exposed to water.
When applying the adhesive, there are two main methods: beads and full coverage. The bead method involves applying lines of adhesive to a surface using a caulking gun, and is typically used for gluing large, flat materials to large flat surfaces. On the other hand, full coverage is used when the material to be glued is small or when an absolutely solid surface is required. For joining timbers, the full coverage method is likely to be more suitable, as it provides a stronger bond.
To achieve full coverage, use a notched trowel to apply the adhesive. This technique saves adhesive, ensures consistent thickness, shortens drying time, improves adhesion, and reduces shrinkage. Remember that most construction adhesives tend to remain flexible after drying, so applying too much can cause soft spots and movement in the material. Aim for a thin, consistent layer that will dry quickly and effectively.
When joining the timbers, clamp or press them together firmly and ensure they are aligned correctly. Wipe away any excess adhesive that may squeeze out from between the joints. Allow the adhesive to dry completely before subjecting the joint to any stress. Refer to the manufacturer's instructions for specific drying times, as it can take up to a week for construction adhesives to reach full strength.
By following these instructions and choosing an appropriate construction adhesive, you can effectively join timbers together to create a sturdy and durable false floor for your boat.
Lindbergh's Boat Trip: Mystery of the Missing Plane
You may want to see also
Adding a marine carpet on top
Marine carpet has improved significantly over the years, and it is now a good option for boat flooring. It is water-resistant and durable, but it is important to keep in mind that it will need regular cleaning as it can accumulate dirt and bacteria over time. It is also not UV-stable, so the colour may fade over time.
If you decide to go with marine carpet for your boat's false floor, here is a step-by-step guide on how to install it:
Step 1: Prepare the Area
Remove any seats or fixtures and mark their locations for easy replacement later. Take out the old carpet and clean off any remaining glue residue using a scraper, mineral spirits, and sandpaper. Ensure you clean and dry all areas that will be carpeted. This is also a good opportunity to inspect the deck and underlying areas for any water damage or hidden structural issues.
Step 2: Prepare the Carpet
On a dry day, lay the new carpet out in the sun for several hours (between 65°F-90°F). This will warm and soften the backing, making it more pliable and easier to handle. Then, using oversized measurements, rough-cut the carpet to approximate size.
Step 3: Cut the Carpet to Size
Lay the carpet in place, using weights or clamps to prevent shifting. Custom-cut the carpet for an exact fit using a very sharp utility knife or carpet knife. Ensure that the carpet direction remains the same on each cut piece, as there is a definite grain, and turning a piece sideways will make it appear a different colour. Always allow for extra when measuring and cutting the carpet.
Step 4: Apply Adhesive
Apply carpet glue to the back of the carpet using a trowel in circular motions, moving from front to back. Aim for a thickness equal to a heavy coat of paint. Do not allow the glue to puddle or leave any dry areas. Wait for the glue to become tacky before unfolding the carpet onto the side with glue.
Step 5: Place the Carpet
Carefully place the carpet, ensuring it is straight and wrinkle-free. Once the glue has come into contact with the boat floor, it will not come up again. Remove the clamps and weights from one side of the carpet and fold it over. Repeat the glue application process on the other side.
Step 6: Remove Air Bubbles
Use a roller or stiff broom to go over the carpet from the centre to all edges. This will remove air bubbles and ensure good contact between the carpet and glue. Without this step, bubbles or lines may develop, or areas of the carpet may come up over time.
Step 7: Allow to Cure
The carpet will start to cure between 3-4 hours, but it is best to leave it to dry fully (24 hours) before vacuuming, reinstalling rails and seats, or using the boat. Wait 48 hours before taking the boat out on the water.
And that's it! You now have a new marine carpet installed on your boat's false floor.
Repairing a Hole in Your Boat's Side: Easy Patching Guide
You may want to see also
Frequently asked questions
A false floor in a boat is an additional floor that is installed on top of the boat's existing floor to provide more rigidity and support.
The most common materials used for false floors in boats are wood, such as treated pine or plywood, and foam, such as Coosa or Divinycell.
To install a false floor, you will need to build a frame using timber or plywood and secure it to the boat's ribs or cross members. The floor sheets are then screwed or glued onto the frame, and a marine carpet is usually added on top for comfort and traction.
A false floor can provide additional rigidity, support, and flotation to your boat. It can also be used to create storage compartments or raise the floor level to improve comfort and drainage.
It is important to consider the weight and type of timber or plywood used, as some materials may not be suitable for constant water immersion. Proper sealing and treatment of the timber are crucial to prevent rotting and corrosion. Additionally, the height of the false floor can affect the boat's stability, so it is important to ensure that the center of gravity is not too elevated.