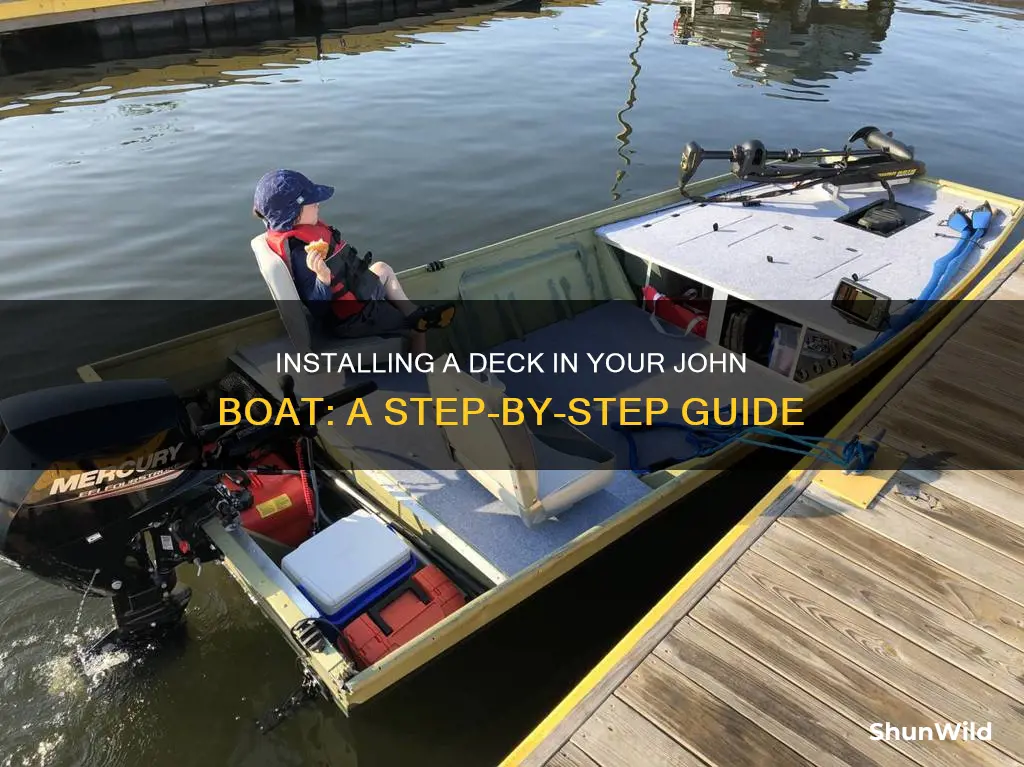
Jon boats are usually sold as a basic aluminium shell, which means they can be easily customised for specific uses. A front casting deck is a quick and easy way to improve the functionality of a Jon boat, providing the angler with a raised platform for better visibility, casting accuracy, and quietness. This can be achieved using an old aluminium step ladder or by using 3/4 treated plywood, a saber saw for notching around support ribs, and a circular saw for long cuts.
What You'll Learn
Enhancing fishability with a front casting deck
A front casting deck can significantly enhance the fishability of a Jon boat, providing several advantages for anglers. Firstly, it offers a raised platform, improving visibility and casting accuracy. This is especially beneficial when fishing in areas with low clearance or when accuracy is crucial for success. The height provided by the deck can also reduce noise, allowing for a quieter approach that improves the chances of catching more fish.
To build a front casting deck, you'll need to start with a sturdy and durable material such as 3/4" treated plywood, which can be customised to fit the boat. Using a saber saw, carefully notch around the support ribs of the boat to ensure a perfect fit. A circular saw will also be useful for making long cuts and shaping the plywood to the desired size and shape.
When designing the deck, consider the overall layout of your Jon boat and how you plan to use it. The deck should complement your fishing style and techniques, providing ample space for casting and manoeuvring. You may also want to incorporate storage solutions into your deck design to keep your gear organised and easily accessible.
Additionally, think about the aesthetics and comfort of your front casting deck. You can stain or paint the plywood to match the style of your boat and add non-slip coatings or mats to improve safety and comfort when standing for extended periods. Finally, ensure that all your measurements are precise and that the deck is securely fitted to the boat to ensure stability and safety while fishing.
Waterproofing Painted Wood for Boats: Expert Tips and Tricks
You may want to see also
Using plywood to fit the front deck
Fitting a front deck to your John boat with plywood is a great way to customise your vessel. The first step is to measure the width of your boat at the point where you want the deck to begin. This will give you the width of the plywood sheet you need to cut. You can then cut the plywood to size, ensuring it fits snugly within the boat.
The next step is to create a template for the curved section of the deck. You can do this by using a large piece of cardboard or paper and a razor knife to trace the curve of the bow. Cut the template to shape and then transfer this onto the plywood. Carefully cut the plywood along the template line, creating a smooth curve that follows the contour of the bow.
Now you have the basic shape of the deck, you can install it in the boat. One option is to use wooden stringers, parallel to the ribs of the boat, to support the plywood. You can then attach the plywood to these stringers, creating a removable deck that can be lifted for cleaning. Alternatively, you can use L-brackets to screw the plywood deck directly to the ribs of the boat.
When installing the deck, be mindful of the height. A deck that is too high can affect the stability of the boat. It is also important to consider the weight capacity of the deck. As this is a casting deck, it will need to support a lot of weight. Most owners of John boats prefer to use 1/2" to 3/4" marine-grade plywood for their decks, which should be able to handle a significant amount of weight.
Finally, you can add a layer of carpet or felt to the deck to provide soundproofing. This will prevent the deck from clacking against the boat ribs while motoring or stepping on the deck.
Bottom Paint for 35-Foot Boats: How Much Gallon is Needed?
You may want to see also
Tools for notching: saber saw
Saber saws, also known as jigsaws or reciprocating saws, are a common electrical tool used in boat building. They are versatile and powerful, offering precision and efficiency for a wide range of cutting tasks. When it comes to notching, a technique used to create precise grooves or indentations in materials like wood or metal, the saber saw is a perfect fit.
The saber saw is capable of making a variety of cuts, including straight cuts, curved cuts, and plunge cuts. For notching, the focus is on making precise cuts at designated points. By selecting the appropriate blade, you can achieve clean and accurate results. For instance, when notching wood, a coarse-toothed blade is ideal, while a fine-toothed blade is more suitable for metal. Additionally, the TPI (teeth per inch) of the blade plays a crucial role, with lower TPI blades suited for wood and higher TPI blades for metal.
To ensure optimal results and safety during the notching process, it's important to follow some key guidelines. Firstly, always wear personal protective equipment, such as safety goggles and gloves, to safeguard against potential hazards. Secondly, secure the workpiece firmly with clamps or other appropriate fixtures to prevent accidental movement. This is crucial for achieving accurate cuts and preventing accidents.
When using a saber saw for notching, it's important to ease the blade into the material at the designated point, rather than forcing it. This allows the blade to establish a smooth pathway for a precise cut. Maintaining a firm grip on the saw and guiding it steadily along the cutting line will help you achieve clean and accurate results. Additionally, the shape of the tooth pattern on the blade contributes to the type of cut. For notching, a blade with a straight tooth pattern will yield better results for straight cuts, while a wavy tooth pattern is ideal for curved cuts.
The versatility and precision of saber saws make them a valuable tool for notching in boat building projects, allowing for the creation of precise grooves and indentations in various materials. With the right blades and techniques, you can achieve clean and accurate results, elevating the overall craftsmanship of your project.
Launching a Food Boat: A Beginner's Guide to Success
You may want to see also
Tools for long cuts: circular saw
When putting a deck in a Jon boat, you may need to cut long boards and plywood. While a table saw is ideal for cutting long pieces of wood, a circular saw can also be used with a couple of techniques, finesse, and practice.
Safety Precautions
Before using a circular saw for long cuts, it is important to take the following safety measures:
- Wear safety gear, including safety glasses and hearing protection, and avoid loose-fitting clothes. Tie back long hair.
- Set the saw blade to cut about a quarter of an inch deeper than the wood's thickness.
- Secure boards less than 6 inches wide with nails and wider boards with clamps.
- Always stand beside the blade, never behind it, and ensure there are no bystanders in the area behind the saw.
- If the board starts to pinch the blade, wedge the saw cut open with a shim.
- Ensure the blade guard is operating freely and never block or wedge it in the raised position.
Sawing Boards Freehand
This method is suitable for cutting a few 2- to 4-inch strips. It results in a board of consistent width and parallel sides, regardless of whether the board you're cutting from is straight or crooked.
- Secure the board for lengthwise cutting by nailing it to sawhorses. Position one finish nail at each end near the board's edge, away from the blade's path. Use 4D finish nails for 3/4-inch thick wood and 8D finish nails for 1-1/2-inch boards.
- Draw a guideline parallel to the edge of the board using a combination square and pencil. Press the fence of the combination square against the board as you slide it along.
- Position your hand on the wide section of the saw shoe, not near the blade, and grip the shoe with your forefinger and thumb. Your forefinger will act as a guide.
- Cut the board, directing pressure straight ahead through the saw's handle and concentrating on the line.
- If the saw starts to wander from the line, back up to about 6 inches behind the deviation and start again. Before restarting the cut, ensure the blade is perfectly aligned in the kerf and maintain a firm grip to prevent the blade from catching and jerking the saw.
- For an accurate finish, guide the saw beyond the end of the board as if the line continued.
Cutting Plywood with a Straightedge Guide
To make cabinet-quality straight cuts in plywood, you need a clamp and a perfectly straight board. The key is to align the straightedge at the right distance from the cutting line and keep the saw shoe tight to the straightedge during the cut.
- Clamp a straightedge to a scrap of lumber to create a circular saw rip guide. Then, hold the saw's shoe tight to the straightedge while you saw a kerf in the scrap.
- Measure and record the exact distance between the straightedge and the inside edge of the saw kerf.
- Clamp the straightedge on the piece of plywood you plan to keep. This way, if the saw deviates from the straightedge, it won't ruin the piece you need.
- Measure and mark the desired width of the cut. Use the previous measurement to make a second set of marks for the straightedge on the "keeper" side of the first marks.
- Align the straightedge with the second set of marks and clamp it tight.
- Slide the saw's shoe against the straightedge to rip the plywood. Press the saw firmly against the straightedge as you push it along to ensure a straight cut.
- At the beginning of the cut, nick the plywood with the blade to ensure it just touches the outside edge of the cutting mark.
- If adjustments are needed, move both ends of the straightedge slightly and reclamp it.
- During the cut, press the front of the saw shoe against the straightedge at the beginning and the back of the shoe tight until the cut is complete.
Building a Circular Saw Rip Guide
If you don't have a table saw, you can build a guide to attach to your circular saw to help you cut narrow strips with precision. This project takes about an hour and may require modifications to fit your saw's shoe.
- Cut the plywood base and pieces carefully to ensure they have parallel sides and square corners.
- Cut the slots and the hole for the blade and blade guard by first drilling 3/8-inch holes in the corners and then cutting between them with a jigsaw.
- Set the base over the fence and align one long edge. Snug the rails up to the sides of the base and screw them to the fence with 7/8-inch screws.
- Connect the fence to the base with carriage bolts and attach the saw shoe to the base with small screws.
- Drill 5/32-inch holes in your saw shoe and attach the guide with 5/8-inch screws.
- Measure between the blade and the fence to set the width of the rip and tighten the wing nuts. Measure at both the front and back edges of the blade to align the fence parallel to the blade.
- Clamp or tack the board to sawhorses and slide the saw with the jig the full length of the board.
The Best Seating Options for a Moving Boat
You may want to see also
Using an old ladder for framing
When installing a deck on a Jon boat, it's important to consider the stability and safety of the boat. Raising the center of gravity can make the boat more prone to capsizing, so it's crucial to keep the deck as low as possible. Additionally, some seats provide structural stability, so removing them can affect the boat's integrity.
Now, let's discuss using an old ladder for framing the deck. An old aluminum step ladder, or even a new, inexpensive one, can be an excellent framing solution for a deck addition on an aluminum Jon boat. The spaces between the rungs can be utilized to create storage areas or provide room for necessary components such as wires.
Here's a step-by-step guide on how to use an old ladder for framing a deck in a Jon boat:
- Plan and measure: Before starting, it's important to have a clear plan and take accurate measurements of your boat. Measure the area where you want the deck to be and decide on the size and placement of the ladder accordingly.
- Prepare the ladder: Cut the legs of the ladder to the appropriate length so that it fits snugly across the width of your boat. You can use a hacksaw to cut the legs, ensuring a clean and precise cut.
- Secure the ladder: Position the modified ladder horizontally across the width of your boat, resting it on the boat's existing seats or supports. Securely bolt the ladder in place, making sure it is firmly attached to the underlying structure.
- Create the deck frame: Using the ladder as the main support beam, build the deck frame around it. You can use additional lumber, such as 2x4s or 2x6s, to create a sturdy frame. Ensure that the frame is securely attached to the ladder and the boat.
- Cut the plywood: Measure and cut the plywood to fit the deck frame. You can use a jigsaw to cut the plywood, allowing for a tapered edge that follows the contour of the boat's sides. This will result in a neat and snug fit.
- Finish the deck: Once the frame is complete, finish the deck by attaching the plywood securely. You can use epoxy or marine-grade adhesive to attach the plywood to the frame and seal any holes or gaps. Finally, consider adding a layer of outdoor carpet or non-slip coating to the deck surface for added comfort and safety.
Remember to always follow best practices for boat modifications and consult with experts or professionals if you have any doubts or concerns.
Who's at the Helm? Boat Racer: Pilot or Driver?
You may want to see also
Frequently asked questions
Test the stability of your Jon boat by standing up in the boat in shallow water with a life jacket on. Lean to either side, testing both slow and quick movements. If the boat tips too much, it may not be stable enough for a deck.
You will need plywood, preferably marine-grade, carpet, self-tapping screws, hinges, and a saw to cut the plywood to size. You may also need 2x4s to create a frame for the deck.
First, measure and cut the plywood to fit your boat. You can use 2x4s to create a frame for the deck, which can be attached to the boat using face-mount joint hangers. Then, lay the plywood over the frame and attach it using galvanized or stainless steel screws. If you want a hinged deck for storage, use a piano hinge to attach the deck to the frame.
You can add a pedestal seat to your deck, but be sure to test the stability of the boat first. You can also cover the plywood with outdoor carpet or turf for added comfort and traction.
Yes, it is important to use caution when drilling into the aluminum boat. Make sure you have measured and marked the drill holes correctly before drilling. Always wear personal protective equipment, such as gloves and eye protection, when operating power tools.