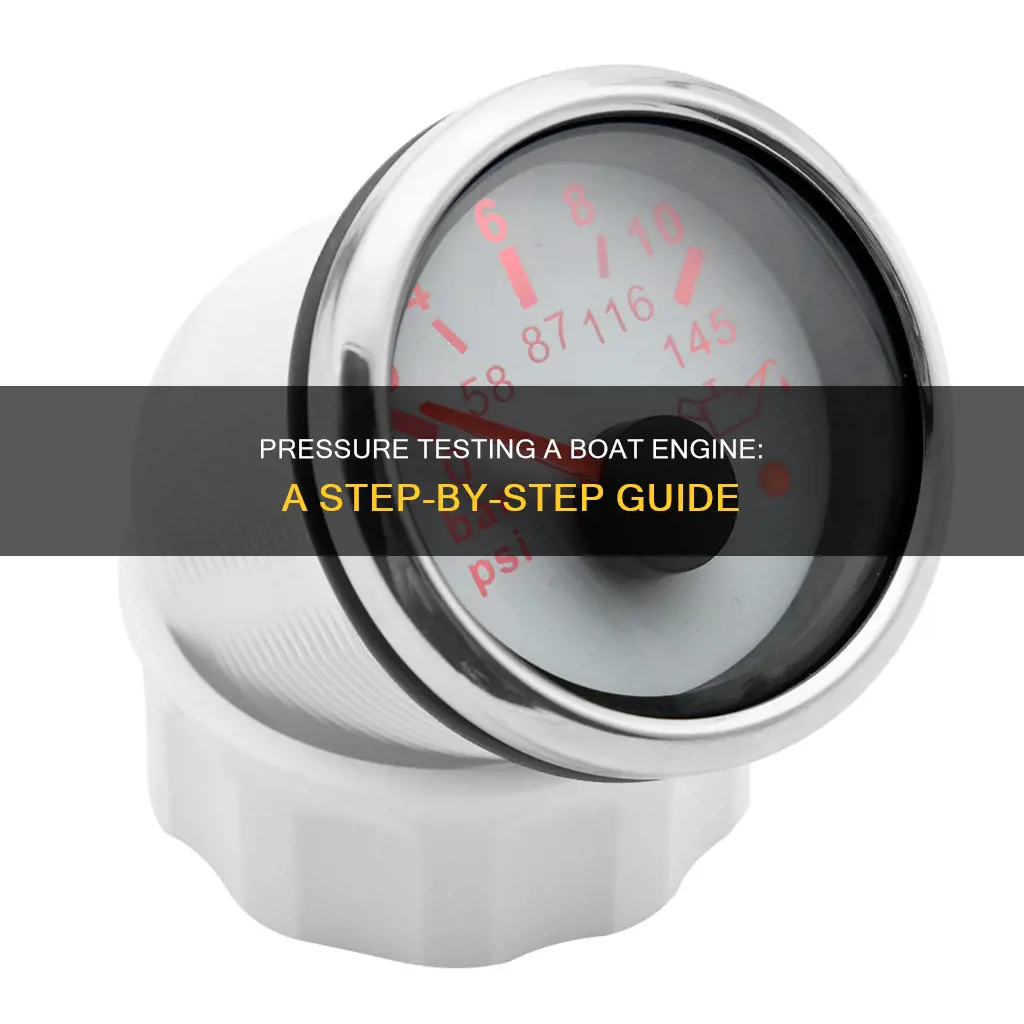
Pressure testing a boat engine is a crucial aspect of boat maintenance, as it helps identify leaks and prevent potential damage. The process involves applying pressure to different components, such as the fuel tank, engine block, or gearcase, and checking for any pressure loss or leaks. By understanding the specifics of the testing procedure, boat owners can ensure the reliability and longevity of their vessels. This introduction will provide an overview of the importance, tools, and steps involved in pressure testing a boat engine, with a focus on safety and effectiveness.
Characteristics | Values |
---|---|
When to pressure test | When you suspect a leak in the fuel tank or when you find water in the gear lube |
What to test | The lower unit or gearcase, the fuel tank, the cooling system |
Tools | Hose pinch pliers, inflatable pipe plug, low-pressure air pressure gauge, short piece of 3/8" fuel hose, brass fitting with 3/8" hose barb and threaded adapter, adapter for Schrader valve, air pump or tank of compressed air, pressure tester, soapy water, utility knife, screwdriver, spark tester, compression gauge, spark plugs |
Fuel tank test procedure | 1. Locate the fuel fill hose, vent hose access ports, and fuel pick-up access. 2. Install the inflatable pipe plug into the fuel fill port and pump to shut off the fuel fill hose. 3. Pinch off the fuel tank vent hose. 4. Remove the fuel hose from the pickup tube fitting and install the low-pressure air pressure gauge and hose. 5. Pump up the tank with air but do not exceed 3 psi. 6. Spray the sender and all fittings and ports on the tank with soapy water and look for air bubbles. |
Gearcase test procedure | 1. Remove the lower drain screw and the top vent screw to drain the gear lube. 2. Reinstall the drain screw with a seal. 3. Install the pressure tester in the top vent screw hole and pump up to 10-12 PSI. 4. Spray soapy water around the seals of the drive, shift, and prop shaft. 5. Inspect for bubbles indicating a leak. |
Cooling system test procedure | 1. Remove the fresh water intake hose and attach a small pressure pump with a gauge to the thermostat housing. 2. Remove the thermostat housing to manifold hose and attach a short hose/PVC cap to plug up the return side. 3. Pressurise the block to 10-20 psi and check for pressure drops. 4. Spray a soapy water solution around the block, spark plug holes, and outside of the engine to look for bubbles indicating a leak. |
What You'll Learn
Locating a leak
Visual Inspection
Start by visually inspecting your boat for any signs of fuel leaks. While this method may not always yield accurate results, it is still worth performing. Gas fumes are typically colorless and challenging to spot with the naked eye. However, you may notice a hissing sound, which could indicate a fuel leak. A keen sense of hearing can help localize the source. Additionally, check the bilge water for a "rainbow effect." This effect occurs when petroleum products, such as gasoline or diesel fuel, create an oily film on the water's surface, dispersing light and resulting in a rainbow-like appearance.
The "Sniff Test"
The "sniff test" is a reliable and traditional method for detecting fuel leaks. As the name suggests, this test involves using your sense of smell to detect the presence of gasoline fumes. Before starting the engine, activate the boat's engine compartment ventilation blower for about five minutes. This helps spread any gasoline fumes throughout the cavity if there is a leak. After fueling, open the engine compartment and take a whiff. The scent of gasoline fumes should be more distinct, making it easier to pinpoint the source of the leak.
Dye Testing
Dye testing is a variation of visual inspection, adding color to gasoline to make it more visible. You can add a hydrocarbon-based dye (gasoline-friendly) to your marine fuel and then check the boat's fuel lines after refueling. If you don't spot the color in the fuel lines, it indicates that there is no leak.
Pressure Drop and Soap Test
The pressure drop and soap test is a more thorough approach to detecting leaks and checking the integrity of your fuel tank. It involves building a DIY pressure testing tool and applying approximately 1 to 3 PSI of pressure. You will also need to remove the original fuel line, so it is recommended to leave this method to a technician. However, if you choose to proceed with a DIY approach, ensure you have the right tools and apply the correct amount of pressure. After pressurizing the system, check for pressure drops and visually inspect for leaks using soap or soapy water. Apply soapy water to hose connections, vent ports, and other components to identify the leak's location.
Ultrasonic Testing
Ultrasonic testing utilizes a pressure tester or a custom-built device to detect fuel leaks by listening for high-frequency sounds. When a fuel leak occurs, gas fumes or liquid move from a high-pressure area to a low-pressure area, creating a whistling sound. The pressure tester helps identify the location of the leak by applying 3 PSI to the fuel tank and checking for pressure drops.
Thermal Imaging
Thermal imaging is another advanced method that employs thermal cameras to capture images of the boat's fuel system. Gas fumes emit energy invisible to the human eye, but a thermal camera can reveal "hotspots," indicating potential leaks.
LPG Leak Down Test
If you suspect a leak in your LPG system, a leak down test is recommended. LPG systems typically have a pressure gauge installed on the cylinder side of the pressure regulator. To perform the test, close all stove valves, then open the LPG tank manual supply valve and the electronic solenoid valve to pressurize the system. Afterward, close the tank supply valve, leaving the solenoid valve open, and observe the pressure gauge. If the pressure drops, it indicates a leak, and the entire system should be checked with a non-corrosive and non-toxic leak detection fluid or detergent solution to pinpoint the exact location.
Engine/Generator Exhaust System Leaks
Exhaust system leaks can be serious, potentially leading to catastrophic engine failure and the introduction of carbon monoxide into the vessel, which can be deadly. To detect dry exhaust leaks (between the manifold and block), feel for escaping exhaust or hold tissue paper near the suspected area to observe movement. Wet leaks in manifolds, exhaust risers, or mufflers are usually accompanied by corrosion, stains, or "running rust" near the leak. Cleaning the area with a non-flammable aerosol disc brake cleaner and then spraying on deodorant can also help identify leaks. The deodorant leaves a uniform coating of white powder that makes leaks easy to spot and can be easily removed.
Fuel System Leaks
For suspected fuel leaks at the engine, clean and dry the area beneath, then cover it with paper towels or oil pads. If the engine needs to be running to generate the leak, do so and check for wet areas. If you suspect fuel fitting leaks, clean the connections with alcohol and tie a small wad of toilet paper or paper towel to each fitting. Wait a while, then check for signs of leakage.
Sanitation System Leaks
Start by inspecting the hose connections, toilet bowl outlet, Y-valves, and fittings for stains, rusty hose clamps, or similar issues. Check each hose clamp with a screwdriver to ensure tightness, and replace any damaged or inoperative clamps. Inspect the toilet itself, especially around the base, for leaks. If there are no apparent leaks, the sanitation hose itself could be the issue due to permeation, especially if it is older. Wipe a section of the hose with a clean, damp cloth (warm water works best), place it in a Ziplock bag, and take it above deck to smell it. If the hose needs replacement, you'll likely notice an obvious odor.
Bilge Leaks
To locate a non-obvious bilge leak, start by pumping or vacuuming the section of the bilge where the leak seems to be coming from, drying it as much as possible. Then, place folded paper towels in the bilge fore and aft of the suspected area. Wait and check if either towel is damp. If one of the end towels is wet, move to that area and repeat the process until you've narrowed down the leak to a specific section of the bilge. Once you've identified the section, dry the bilge and cover it with paper towels, observing which ones get wet first. Alternatively, you can draw lines along both sides of the bilge with a water-soluble felt pen or sidewalk chalk and check back later for runs, working your way up the hull until you find the source of the leak.
Remember, when dealing with leaks, patience and careful observation are key. Some leaks may require professional assistance, especially when dealing with pressurized systems or advanced testing equipment.
Removing Seats from Your Ranger Boat: A Step-by-Step Guide
You may want to see also
Removing the fuel delivery hose
Once the hose is off, stick on your pressure testing tool and put a hose clamp on the end of it, tightening it onto the hose barb. Now you are ready to start testing!
Another method for removing the fuel hose is to use a heat gun. Apply moderate heat to the hose end to expand and soften it, and it should come off easily without damaging the hose or barb. It takes a little practice to learn to apply heat slowly and evenly so as not to damage the outer shell of the hose.
If you are still unable to remove the fuel hose, try using a small flat blade screwdriver. Bend the end of the screwdriver at 90 degrees, slide that end under the hose and "work" it around while pulling the hose. The blade will break the suction and also help the hose as it works over the individual barbs until it is released.
Transferring Boat Ownership in Kentucky: A Guide to Titles
You may want to see also
Pumping air into the fuel tank
To pressure test a boat engine, you'll need to get your hands on a few tools and follow a few important steps. The process involves pumping air into the fuel tank and checking for leaks, but it's crucial to do this safely and carefully to avoid any damage to the tank or engine. Here's a detailed guide specifically focused on the "Pumping air into the fuel tank" section of pressure testing a boat engine:
Tools You'll Need:
Firstly, let's talk about the tools you'll require for this job. For pumping air into the fuel tank of your boat, you'll need the following:
- Hose pinch pliers: These pliers are designed to close onto a hose and stay shut, pinching it closed until you release them.
- Inflatable pipe plug: This plumbing tool can be found at your local hardware store. It fits into a pipe, and when pressure is applied, it expands and closes off the pipe.
- Short piece of 3/8" fuel hose: You'll need a short length of this hose to connect various components.
- Brass fitting: Look for a brass fitting with a 3/8" hose barb on one side and a threaded adapter on the other.
- Tee-fitting: You'll use this to adapt the hose barb to accommodate a pressure gauge.
- Schrader valve: This will allow you to put air through the valve and out the fuel hose.
- Air pump or compressed air tank: You'll need a source of air to pump into the fuel tank.
Accessing the Fuel Tank:
Now that you have the necessary tools, it's time to locate the fuel tank. This can be a tricky part, as not all boats provide easy access to the fuel tank components. Most modern boats have access ports that allow you to reach the fill and vent parts, usually located towards the front of the tank. The pick-up tubes and sender section are typically at the back or aft of the tank.
If you're dealing with an older boat, you may find that access is more limited. Boats from the 1990s or earlier might not have dedicated access ports, and you may need to remove certain components to reach the fuel tank. For example, you might have to remove a leaning post with a livewell to access the port.
Installing the Inflatable Pipe Plug:
Let's start by shutting off the fill port. Take your inflatable pipe plug and insert it into the fuel fill hole. Ensure that the plug goes down into the hose without touching anything except the hose itself. This ensures that there are no gaps for air to leak out. Now, use your air pump or compressed air tank to quickly fill up the plug until it completely seals off the fill hose.
Pinching Off the Vent Hose:
Next, we'll deal with the vent hose, which should be located right next to the fill hose. Use your hose pinch pliers to squeeze the vent hose shut. Make sure you apply enough force to completely compress the hose and prevent any air from escaping. Be cautious, though, as older hoses may be prone to splitting if they're brittle or dry-rotted. If the hose is damaged during this process, simply cut out the affected section and use two splice hose barbs to insert a new piece of hose.
Removing the Fuel Delivery Hose:
Here's a pro tip to save you time and frustration: before removing the fuel delivery hose from the pick-up tube, use a utility knife to slice a small section (about 1/2" to 1") of the fuel hose connected to the tube. This will make it much easier to work the hose off the pick-up tube. Over time, the heat and gasoline can cause the hose to shrink and stick onto the hose barb, making it extremely difficult to remove.
Now comes the critical part: pumping air into the fuel tank. It's important to understand that too much air pressure can damage the fuel tank. The maximum amount of air you should ever put into a fuel tank is three psi (pounds per square inch). Ideally, stay around 2-3 psi, or even slightly lower at 2.5 psi. This amount of pressure is sufficient to push fuel out through any holes or splits in the tank.
Connect your air pump or compressed air tank to the Schrader valve on the pressure gauge and begin filling the tank. The amount of air needed will depend on how much fuel is already in the tank. Apply quick blasts of air, keeping a close eye on the air pressure gauge. Slowly work your way up to two psi and then hold it there to observe if the tank loses pressure.
Locating a Leak:
If the pressure gauge starts to drop, it indicates a potential leak. The most common sources of leaks are the fuel sender or the fittings at the pick-up tubes. Take some soapy water and spray it around the pick-ups and the fuel sender. If you notice air bubbles, it confirms the presence of a leak.
If you don't see any air bubbles, double-check that the vent and fill hose are properly plugged off. Also, ensure that your pressure testing tool isn't leaking around the tee-fitting, the gauge, or the Schrader valve. Continue pumping the tank back up to two psi and spraying with soapy water until you're confident that there are no leaks coming from the top of the tank.
Additionally, keep an eye on the bilge to ensure that fuel isn't leaking into that area. If you see fuel in the bilge, it's a clear sign that the boat's fuel tank has failed, and it's time to replace it.
Pelican Raider 8e: Enough Space for Two Fishers?
You may want to see also
Installing an inflatable pipe plug
To install an inflatable pipe plug, follow these steps:
Firstly, locate the fuel fill hose and the vent hose access ports, as well as the fuel pick-up access. This can vary depending on the age and model of the boat. Typically, the fill and vent parts are located towards the front of the tank, while the pick-up tubes and sender section are at the back. Once you've located these components, you can proceed to the next step.
Now, take the inflatable pipe plug and install it into the fuel fill port. Ensure that the plug is inserted down into the hose, sitting snugly against it to prevent any spots where air can leak out. Once the plug is in place, use an air pump or a tank of compressed air to inflate it quickly. The plug should expand and completely seal off the fill hose.
Next, access the vent hose, which should be located next to the fill hose. Use hose pinch pliers to pinch off the vent hose, compressing it completely so that no air can escape. Be careful not to apply too much force, especially if the hose is old, as it may split or get damaged.
Finally, to ensure a proper seal, spray soapy water around the plug and check for any air bubbles. If you notice any leaks, adjust the plug and inflate it further as needed.
Inflatable pipe plugs are designed to fit into pipes and seal them by applying pressure. They are typically made of natural rubber and can be inflated using air or water. These plugs are versatile and can be used for various applications, including sealing round pipes, leak detection, and pressure testing.
A Guide to Identifying Oregon Boat Titles
You may want to see also
Using soapy water to check for leaks
The soapy water test is a common method for detecting leaks in LPG (liquefied petroleum gas) systems. It is a simple and easy way to identify gas leaks or faults in pipes, valves, and fittings. Here's a step-by-step guide on how to use soapy water to check for leaks in a boat engine:
Step 1: Prepare the Soapy Water Solution
Mix water with a small amount of liquid soap or dish soap. You can use a spray bottle or a bucket for this. A ratio of 1:3 soap to water is ideal. This ratio ensures that the solution has enough soap to create bubbles when it comes into contact with a gas leak.
Step 2: Turn Off the Gas Supply
Before you begin the test, it is crucial to turn off the gas supply. This is an important safety precaution as you do not want any gas escaping while performing the test.
Step 3: Apply the Soapy Water Solution
Spray or apply the soapy water solution onto the areas you want to test, such as joints, seals, or fittings. Be generous with the application to ensure complete coverage.
Step 4: Look for Bubbles
If there is a leak, escaping gas will create bubbles in the soapy water solution. Carefully inspect the areas you have applied the solution to and look for any bubbling or frothing.
Step 5: Identify the Leak
If you observe bubbles, you have successfully identified a leak or fault. Take note of the location and proceed to address the issue.
Step 6: Tighten or Replace Parts
Depending on the location of the leak, you may need to tighten a fitting or replace a faulty part, such as a seal or gasket. This will correct the issue and prevent further gas leakage.
Step 7: Rinse the Area
Once you have completed the test and addressed any leaks, remember to rinse the area with clean water to remove any soap residue.
It is important to note that the soapy water test should not be used for oxygen lines or lines carrying flammable or toxic gases. If you suspect a leakage but are unable to identify the source, it is best to call a technician for further assistance.
Exploring the Ruby Rose: A Unique Boat's Identity
You may want to see also
Frequently asked questions
A pressure test checks for leaks in your boat engine by applying pressure to the system and monitoring for any drops. This is important as leaking seals can cause oil to escape and water to enter the engine, leading to corrosion and damage.
It is recommended to pressure test your boat engine every time you change the gear lube, which is approximately every 100 hours or once per year.
You will need a gearcase pressure tester, hose pinch pliers, an inflatable pipe plug, and a low-pressure air pressure gauge.
The process involves draining the old gear lube, installing the pressure tester, and monitoring the pressure to see if it remains stable.
If a leak is detected, you may need to replace seals or gaskets. It is important to address leaks promptly to prevent further damage and corrosion.