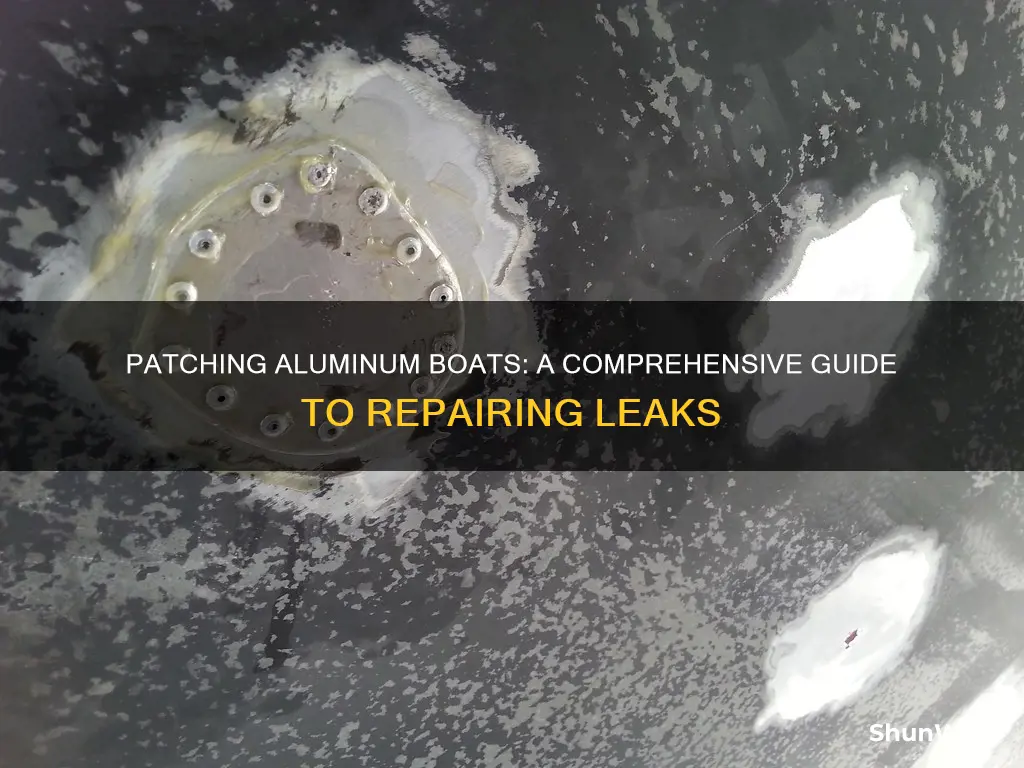
Owning a boat is a dream for many, but it can quickly turn into a nightmare if you don't know how to maintain it. One of the most common issues boat owners face is dealing with leaks, which can range from tiny pinhole leaks to larger holes. While it may seem daunting to fix a leak in an aluminium boat, it is possible to do so with relative ease and affordability. In this guide, we will explore the different methods for patching an aluminium boat, from welding to epoxy putty, and provide step-by-step instructions on how to properly seal those leaks and get your boat back in the water where it belongs.
Characteristics | Values |
---|---|
Hole size | From pinhole leaks to 1/3 inch in diameter |
Hole location | On the hull, transom, keel, or bottom of the boat |
Repair methods | Welding, epoxy putty, Flex Seal, Flex Paste, JB Weld, 3M 5200, silicone, radiator repair sticks, riveting, screws, bolts, aluminium patches, caulking tube of epoxy, acetone, sandpaper, Flex Seal spray, glue, Lexel caulk, aluminium weld, or a new hull |
Tools | Propane catalytic heater, putty knife, acetone, sandpaper, heat gun, caulking tube, mixing nozzle, wire brush, drill, blind rivet, bolts, washers, screws, angle grinder, steel brush |
Materials | Epoxy, JB Weld, Flex Seal, Flex Paste, acetone, sandpaper, aluminium, 3M 5200, silicone, radiator repair sticks, aluminium rivets, aluminium bolts, aluminium washers, aluminium patches, caulking epoxy, Flex Seal spray, glue, Lexel caulk, aluminium weld |
What You'll Learn
Clean the area with acetone and sandpaper
To clean the area with acetone and sandpaper, follow these steps:
Firstly, wipe the surface of the boat with acetone. This will remove any dirt, grease, or oil that may be present. Next, use sandpaper or a wire brush to roughen the area around the hole. You can do this by hand, or with an angle grinder if you prefer. This process will create a rough surface for the patch to adhere to. Once you have finished sanding, use acetone to wipe down the area again, ensuring that it is clean and free of any debris. It is important to note that you should wear gloves during this process to protect your hands from the acetone and to avoid getting oil from your fingers on the surface, which could affect how well the patch adheres.
Finding Boat Owners in Ontario: A Quick Guide
You may want to see also
Use an epoxy putty, like JB Weld
Epoxy putty is a great option for patching small holes in an aluminium boat. It is a spot repair, so it is best for isolated holes rather than widespread damage. It is also a good option if you cannot afford to get a professional weld.
To patch your boat with epoxy putty, first, flatten the area around the hole as much as possible with a hammer. Next, use sandpaper or a grinder to rough up the area around the hole, and clean it with a solvent such as acetone. This will help the epoxy stick to the surface. Wear gloves during this process to avoid getting oil from your fingers on the surface, which could affect how well the epoxy seals.
Once the area is prepared, you can apply the epoxy putty. Epoxy putty comes in two parts which need to be mixed together. Take equal parts of each and roll them together until the colour is uniform. Then, press and smooth the putty into the hole and surrounding area, from both sides if possible. If the hole is a crack, drill a small hole at each end to stop the crack from spreading.
JB Weld is a popular brand of epoxy putty, and their product MarineWeld is specifically designed for marine repairs. It is like putty, rather than runny, so it is easy to apply. You can buy it from auto parts stores or home improvement stores.
Measuring Boat Sails: A Comprehensive Guide to Success
You may want to see also
Seal with Flex Seal spray
To seal an aluminium boat using Flex Seal spray, you should first identify the source of the leak. If the problem is leaky rivets, one option is to reset them by flipping the boat over and having someone underneath the boat push on the rivet with a hammer. You can then give the rivet a tap with a hammer from the outside of the boat.
If you decide to seal the boat with Flex Seal spray, it is important to prepare the area. Clean the area you intend to apply the spray to and allow it to dry. It is also a good idea to check the weather forecast and ensure it won't rain for at least 24 hours after application.
When applying the Flex Seal spray, ensure you follow the directions on the product. Apply one coat at a time, letting each coat dry before applying the next one. Flex Seal spray dries to the touch in about 2-3 hours and will fully cure in 24-48 hours. When patching, make sure that you extend the product well past the hole. If the gash is 2 inches wide, add another inch on either end for complete coverage.
You can also use Flex Seal Liquid to seal an aluminium boat. This can be brushed, poured, or rolled on. Multiple coats can be applied for more protection, but each coat should be allowed to dry before the next one is added.
Testing Boat Hulls: Methods to Assess Structural Integrity
You may want to see also
Welding with a TIG welder
Preparation:
Before you begin welding, it is important to prepare your equipment and work area. Put on protective gear, including thick leather welding gloves, a welding helmet, and closed-toe shoes. Ensure your welding helmet is clean, providing you with a clear view of your work. Check that your work area is well-lit, with lighting from the side as well as overhead. This will help you see the tungsten position before starting the weld.
Setting up the TIG Welder:
For welding aluminum, choose a pure tungsten rod as your electrode. Grind the tungsten rod to a point, especially if it is a new cylinder without a pointed or rounded tip. Lincoln recommends a balled tip for AC welding and a pointed tip for DC welding. A pointed tip will give you a more directed arc. Insert the electrode into its collet, ensuring the tip is about 1/4" away from the protective sheath.
Choosing Settings and Gas:
Set your TIG welder to the appropriate settings. For aluminum, choose "AC" from the electricity options. Set the "Cleaning/Penetrating" setting to around 7 on a scale from 1 to 10, and the "Air on" to about 5 seconds if available. Set the "Max Amps" high, around 250. Turn on the gas, using pure argon for aluminum.
Preparing the Metal:
Clean the surfaces of the metal with a wire brush. Use a dedicated aluminum brush to avoid contamination. You can also wipe down the welding rods with acetone for a nicer finish. Clamp your metals to ensure they stay in place during the welding process.
Welding Technique:
Hold the electrode in your dominant hand, ensuring it can move freely without any tangles. Position the electrode about an inch away from the metal, never touching it. If you do, stop immediately, turn off the welder, and grind down the tungsten rod. To start the weld, quickly heat the metal by pressing down on the foot pedal. You will know the weld pool has formed when the metal becomes fluid. Start on an edge, and once the pool has formed, touch the rod in. Ease off the pedal to control the amount of heat and current.
Drawing a Bead:
After tacking, remove any clamps and start a weld pool by pressing down on the pedal. Then, lighten up on the pedal to regulate the current. If the metal starts to burn or melt, reduce the current. If the metal looks flaky, increase the power. To weld aluminum, move the electrode towards the rod while feeding the rod into the pool. The rod should be to the side that the weld will grow towards, known as "leading" the electrode.
Types of Welds:
The easiest type of weld is the "fillet," where two metals are joined at right angles. The next is the "lap" weld, with two metals resting flat against each other. More challenging is the "butt" weld, where two metals touch along the edges, requiring a straight line and consistent weld pool.
Remember to always follow safety precautions when working with welding equipment, and if you are a beginner, consider practicing on thicker steel to develop your technique before moving on to thinner materials.
Repairing Your Boat's Livewell: A Step-by-Step Guide
You may want to see also
Use a patch riveted over the hole with a permanent sealer
To repair a hole in an aluminium boat, you can use a patch riveted over the hole with a permanent sealer. This method is a proper way to repair the hole and will ensure the fix is long-lasting.
First, you need to source a quarter or half-dollar-sized piece of aluminium. Clean the area around the hole with acetone to remove any oil or grease. Then, sand or grind the area to ensure the surface is smooth and free of paint. Drill a small hole at each end of the crack to prevent it from spreading. Next, apply a permanent sealer, such as 5200, to the patch. Place the patch over the hole and rivet it in place.
This method will create a strong, permanent repair that will last for several years. However, it is important to note that this is not a quick fix, and proper preparation is key to ensuring a successful repair.
If you are unsure about riveting a patch, you may want to consider other methods, such as welding, epoxy putty, or marine sealant. These methods can also provide effective repairs but may require more specialised skills or equipment.
Understanding Porpoising in Bass Tracker Boats
You may want to see also
Frequently asked questions
The best way to patch a hole in an aluminium boat is to take it to a weld shop and let them weld it with a TIG welder. If you can't afford to do that, small holes can be fixed with epoxy putty.
The area should be hammered flat to shut the hole as much as possible. Then sand or grind the area and clean it with an acetone solvent.
A two-part, marine-grade epoxy putty. Mix the two parts, rolling equal amounts of A and B together until the colour is uniform.
Drill a small hole at each end of the crack to stop it from spreading.