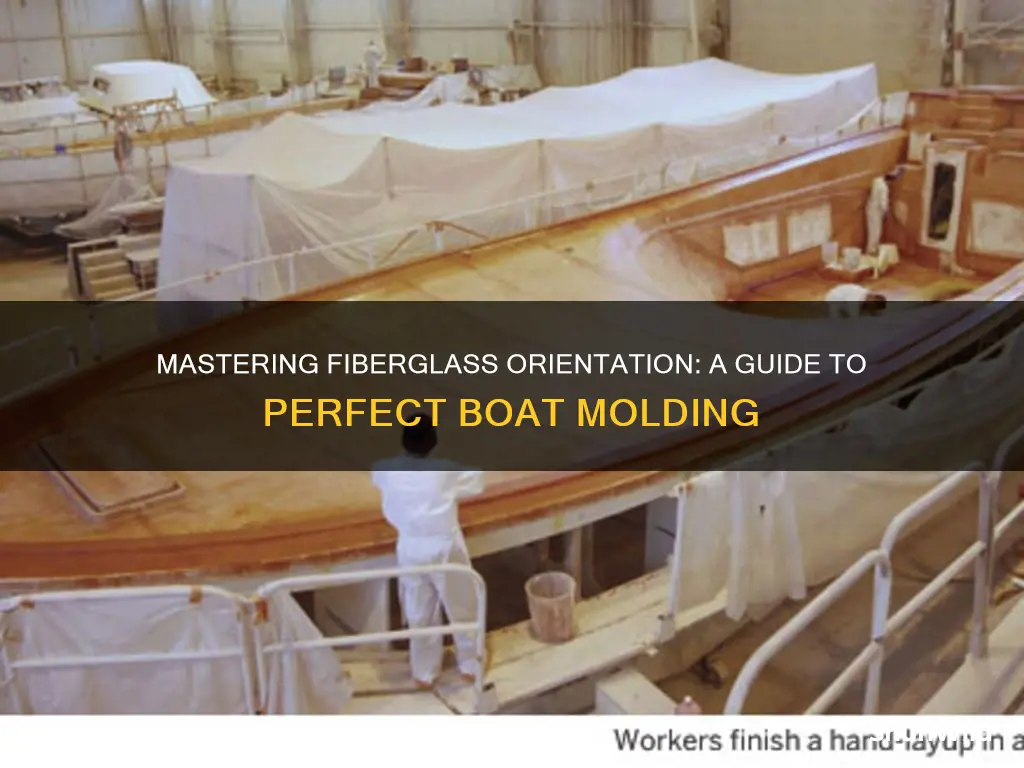
When building a boat mold, proper orientation of fiberglass is crucial for the structural integrity and performance of the vessel. This process involves carefully placing the fiberglass layers in a specific pattern to ensure optimal strength and durability. The orientation of the fiberglass can vary depending on the boat's design and intended use, but it generally involves a combination of unidirectional and random mat layers to create a strong and lightweight structure. Understanding the principles of fiberglass orientation is essential for any boat builder to create a sturdy and reliable vessel.
What You'll Learn
- Mold Design: Plan mold shape and size for optimal fiberglass orientation
- Fiberglass Types: Choose appropriate fiberglass cloth and resin for boat structure
- Layup Techniques: Apply fiberglass layers with proper techniques for strength and durability
- Mold Support: Use temporary supports to maintain mold shape during fiberglass application
- Curing Process: Control temperature and pressure for proper curing of the fiberglass boat
Mold Design: Plan mold shape and size for optimal fiberglass orientation
When designing the mold for a boat, the goal is to ensure optimal fiberglass orientation for strength, durability, and aesthetics. The mold shape and size play a crucial role in achieving this. Here's a detailed guide on how to plan the mold for optimal fiberglass placement:
- Understand Fiberglass Orientation: Fiberglass, when used in boat construction, is typically laid in layers with specific orientations. The most common orientations include unidirectional (uni-directional) and random or woven (random-woven) patterns. Uni-directional fiberglass provides excellent strength in one direction, making it ideal for areas requiring structural integrity, such as the hull bottom and sides. Random-woven fiberglass offers better all-around strength and is commonly used for the deck and interior panels. Understanding these orientations is key to designing the mold.
- Mold Shape and Size: The mold should be designed to accommodate the specific fiberglass orientation requirements. For unidirectional fiberglass, the mold should have a flat or slightly curved surface to facilitate the layup process. The width of the mold should match the desired width of the fiberglass layer, ensuring that the material is applied evenly. For random-woven fiberglass, the mold can have a more complex shape, mimicking the woven pattern. This might involve creating a mold with a series of small, interconnected cells or a grid-like structure to guide the fiberglass layup.
- Consider Mold Depth: The depth of the mold is critical for fiberglass orientation. For unidirectional fiberglass, a deeper mold is often preferred to ensure the material is properly embedded and to allow for the creation of a smooth surface. In contrast, random-woven fiberglass may require a shallower mold to accommodate the woven pattern and still provide adequate thickness. The mold's depth should be carefully calculated to match the desired fiberglass thickness and layup technique.
- Drafting and Venting: Proper drafting, or the angle of the mold's surface, is essential for easy removal of the boat hull after curing. The draft should be designed to match the boat's design, ensuring a smooth transition from the mold to the final product. Additionally, consider adding vents to the mold to release air bubbles during the fiberglass layup process. These vents should be strategically placed to avoid interfering with the fiberglass orientation.
- Mold Material and Maintenance: Choose a mold material that is suitable for the boat's construction and can withstand the curing process. Silicone rubber molds are commonly used for their flexibility and ease of use. Regular maintenance of the mold is crucial to ensure its longevity and performance. This includes cleaning, repairing any damage, and periodically re-surfacing the mold to maintain its shape and quality.
By carefully planning the mold shape, size, and depth, you can create an optimal environment for fiberglass orientation, resulting in a strong, durable, and aesthetically pleasing boat hull. This process requires a deep understanding of both the boat's design and the properties of fiberglass, ensuring a successful and efficient construction process.
Honey's Departure: Fresh Off the Boat Mystery Explained
You may want to see also
Fiberglass Types: Choose appropriate fiberglass cloth and resin for boat structure
When it comes to building a boat using fiberglass, selecting the right materials is crucial for a strong and durable structure. The two primary components to consider are the fiberglass cloth and the resin, each serving distinct purposes in the boat-building process.
Fiberglass cloth, often referred to as fiberglass fabric or weave, is a woven material made from glass fibers. The choice of cloth type depends on the specific requirements of the boat's structure. For structural elements that need to be strong and rigid, a cloth with a higher glass fiber content is ideal. This could be a 50/50 or 60/40 glass-epoxy blend, providing excellent strength and stiffness. For areas requiring flexibility and impact resistance, a cloth with a lower glass fiber content, such as a 35/65 or 40/60 blend, can be used. This type of cloth offers more give and is less prone to cracking under stress.
The resin, on the other hand, is a crucial binding agent that holds the fiberglass cloth together and provides structural integrity to the boat. There are various types of resins available, each with unique properties. For boat building, the most common resin is epoxy, known for its excellent bonding capabilities and ability to withstand harsh marine environments. Epoxy resins can be further categorized into different grades, such as interpenetrating network (IPN) resins, which offer superior mechanical properties and resistance to chemical degradation. For smaller boats or projects, a less expensive option like polyester resin can be used, but it may not provide the same level of durability in harsh conditions.
In addition to the resin type, the choice of catalyst is essential. Catalysts are added to the resin to initiate the curing process, and they come in various forms, such as liquid or powder. The catalyst-to-resin ratio is critical, as an incorrect ratio can lead to poor bonding or premature curing. It is recommended to follow the manufacturer's guidelines for the specific resin and catalyst combination you are using.
When selecting fiberglass cloth and resin, consider the specific requirements of your boat's design. Factors such as the load-bearing capacity, flexibility needed, and environmental exposure will influence your material choices. Properly oriented and applied fiberglass, with the right combination of cloth and resin, will result in a boat that is not only aesthetically pleasing but also structurally sound and capable of withstanding the rigors of marine environments.
Bass Boat Engine Longevity: How Many Hours Are Optimal?
You may want to see also
Layup Techniques: Apply fiberglass layers with proper techniques for strength and durability
When it comes to layup techniques for fiberglass in boat molding, precision and attention to detail are key. The goal is to create a strong, durable structure that can withstand the rigors of marine environments. Here's a breakdown of the process:
Preparation: Before beginning the layup, ensure the mold is clean and free of debris. Prepare the fiberglass cloth or mat by cutting it to the appropriate size and shape for the specific area of the boat you're working on. This step is crucial as it ensures the fiberglass is applied in the right proportions and directions for optimal strength.
Resin and Catalyst: Use a high-quality epoxy resin and its corresponding catalyst in the correct ratio as per the manufacturer's instructions. Proper mixing is essential to achieve a consistent and strong bond. Apply the mixed resin and catalyst to the mold, ensuring an even coating. This layer acts as a bonding agent and provides structural integrity to the fiberglass layers.
Fiberglass Application: Start laying the fiberglass cloth or mat over the prepared area, ensuring it overlaps the previous layer by a few inches. Use a rolling pin or a similar tool to smooth out any wrinkles or air bubbles. The direction of the fiberglass weave should be considered; typically, a crisscross pattern is used to create a strong, load-bearing structure. Apply additional layers, maintaining the proper overlap and using a smoothing technique to eliminate any gaps.
Sanding and Inspection: After each layer, inspect the work for any imperfections. Use fine-grit sandpaper to smooth the surface, ensuring a seamless transition between layers. Pay close attention to corners and edges, as these areas require extra care to avoid weak spots. Proper sanding techniques will result in a smooth, glass-like finish.
Curing and Reinforcement: Allow the layup to cure according to the resin manufacturer's guidelines. During this time, the fiberglass layers bond together, forming a strong and durable structure. Consider adding additional reinforcement, such as carbon fiber or glass tape, in critical areas like the hull stringers or deck beams, to further enhance strength and prevent delamination.
Mastering these layup techniques is essential for creating a high-quality boat with a robust fiberglass structure. It requires practice and attention to detail, but the results will be a vessel that can handle the demands of marine environments with ease.
Bass Boat Basics: Mastering Take-Offs
You may want to see also
Mold Support: Use temporary supports to maintain mold shape during fiberglass application
When working with fiberglass in a boat mold, ensuring the mold's shape and integrity is crucial for a successful and smooth application process. One effective technique to achieve this is by utilizing temporary supports, which play a vital role in maintaining the desired form of the mold during the fiberglass application. These supports are particularly essential when dealing with complex or curved surfaces, as they provide the necessary structure and stability to the mold.
The process begins with carefully selecting the appropriate support materials. Common choices include wooden strips, foam boards, or even lightweight metal frames. The key is to choose materials that are easy to work with and can be easily removed after the fiberglass is cured. Wooden strips, for instance, can be cut and shaped to fit the mold's contours, providing a sturdy framework. These strips should be positioned strategically to support the areas that require the most attention, such as the hull's bottom or the sides, where the fiberglass needs to maintain a smooth and even surface.
Once the supports are in place, the next step is to ensure they are securely attached to the mold. This can be achieved through various methods, such as clamping, taping, or using small screws or nails. The goal is to create a temporary, yet firm, attachment that will hold the mold's shape without causing any damage to the fiberglass during the application process. It is essential to be gentle and avoid excessive force when securing the supports to prevent any unwanted marks or indentations on the mold's surface.
After the fiberglass is applied, the temporary supports become even more critical. They help maintain the mold's shape during the curing process, preventing any unwanted warping or distortion. The supports should remain in place until the fiberglass is fully cured and hardened, ensuring the final product retains the intended design. Once cured, carefully removing the supports is necessary, and this process should be done with caution to avoid any damage to the newly formed fiberglass structure.
In summary, using temporary supports is an essential step in the process of orienting fiberglass in a boat mold. These supports provide the necessary structure and stability, ensuring the mold's shape is maintained during the application and curing of the fiberglass. By carefully selecting and securing the supports, and then removing them after the curing process, boat builders can achieve high-quality, precise results in their fiberglass projects. This technique is a valuable tool for creating smooth, curved surfaces and overall enhancing the craftsmanship of the boat's structure.
Essential Tools for Aluminum Fishing Boats
You may want to see also
Curing Process: Control temperature and pressure for proper curing of the fiberglass boat
The curing process is a critical phase in building a fiberglass boat, ensuring the material's strength, durability, and structural integrity. Proper temperature and pressure control are essential to achieving a successful cure, as they influence the material's final properties and the overall quality of the boat. Here's a detailed guide on managing these factors:
Temperature Control:
Maintaining the correct temperature is crucial during the curing process. Fiberglass resins typically cure through a chemical reaction, which is highly temperature-dependent. The ideal temperature range for curing fiberglass is usually between 68°F and 82°F (20°C and 28°C). Warmer temperatures accelerate the cure, reducing the time required but potentially affecting the material's final properties. Conversely, cooler temperatures slow down the reaction, allowing for more precise control over the cure, especially in complex shapes. It's important to note that temperature variations can lead to inconsistencies in the cured material. Therefore, a consistent temperature environment is essential. Use heating blankets, radiant heaters, or temperature-controlled molds to ensure the fiberglass remains within the optimal temperature range throughout the curing process.
Pressure Application:
Applying the right amount of pressure is another critical aspect of curing fiberglass. Pressure helps to expel air bubbles and ensures proper resin distribution, especially in thick laminations. The pressure required can vary depending on the thickness of the fiberglass layer and the specific resin system used. Generally, a pressure of 10-20 psi (pounds per square inch) is applied during the initial stages of curing, gradually increasing to 20-30 psi as the process progresses. This controlled pressure application ensures that the fiberglass layers bond tightly together, creating a strong and rigid structure. It's important to use a pressure-sensitive adhesive or tape to secure the layers, ensuring they remain in place during the curing process.
Curing Time and Monitoring:
The curing time will depend on the specific fiberglass system and the environmental conditions. Curing should be allowed to proceed without interruption to ensure a complete reaction. Regularly monitor the curing process to ensure it is proceeding as planned. Check for any signs of incomplete curing, such as tackiness or soft spots, and adjust the temperature or pressure accordingly. Proper curing can take several hours to a full day, depending on the size and complexity of the boat mold.
Post-Curing Care:
After the initial cure, allow the fiberglass to cool to room temperature. This gradual cooling process helps to prevent thermal shock, which can cause stress and potential damage to the cured material. Once cooled, inspect the boat for any defects or areas requiring additional attention. Proper curing and post-curing care will result in a high-quality fiberglass boat with excellent structural integrity.
How Much Is a 1978 Ranger Bass Boat Worth?
You may want to see also