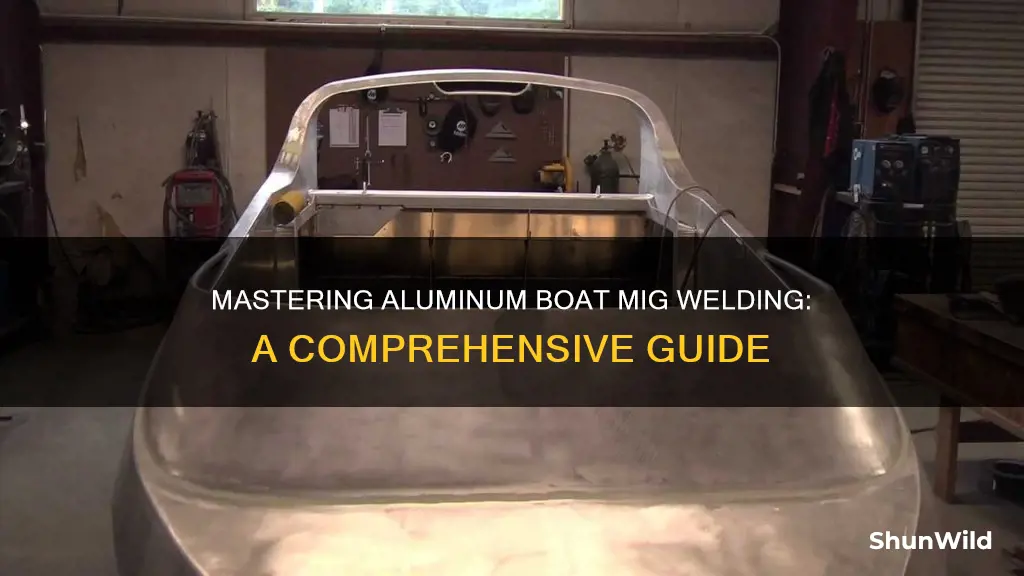
Welding an aluminium boat requires specific tools and expertise. Aluminium boats are popular because they are durable, sturdy, affordable, and lightweight. However, they require different maintenance compared to fibreglass boats, as the material can corrode if not properly maintained. When welding aluminium, it is essential to choose the right equipment, prepare the aluminium surface by cleaning it thoroughly, control the heat input, select the appropriate filler material, weld in a clean and controlled environment, and practice proper welding techniques.
Characteristics | Values |
---|---|
Welding equipment | MIG or TIG welder |
Welding surface preparation | Clean the aluminium thoroughly to remove dirt, grease, or oxide layers |
Heat input | Control heat input with short welds and allow the material to cool between passes; preheat the aluminium slightly to manage heat flow |
Filler material | Filler rod or wire should match the base material to ensure compatibility and strength; for most marine-grade aluminium, 5356 and 4043 filler materials are commonly used |
Welding environment | Weld in a clean, controlled environment to prevent contaminants; use a portable welding shelter when welding outdoors |
Welding technique | Maintain a consistent travel speed for even heat distribution; practice steady hand movements and keep a close watch on the weld pool; use a push technique instead of pull to keep shielding gas in the weld pool and reduce contamination |
What You'll Learn
Choosing the right welding equipment
If you are new to welding aluminium, it is recommended to use a MIG welder with a spool gun. This setup is more comfortable and reduces the risk of bird nesting, which is common with soft aluminium wire. Look for a machine with HF and a push-pull gun if you plan to do a lot of aluminium welding. A Lincoln Powermig 350MP with the pulse-on-pulse feature is a good option, though it may be more machine than you need. The Millermatic 252 with a spool gun or the Millermatic 350P with a push-pull gun are also suitable choices.
If you have more welding experience and are looking for a neat appearance, a TIG welder may be a better option. TIG welding offers greater control and is good for pretty handrail welds and fuel tanks. However, it is slower and puts more heat into the metal, which can lead to warping.
In addition to the welder itself, you will also need a bottle of pure argon gas and a flowmeter/regulator to weld aluminium. Set the flow rate to 15-20 CFH for indoor welding or 25-30 CFH if you are welding outdoors. A wind screen can help maintain a stable welding environment by blocking wind, dust, and moisture.
Finally, you will need the right welding wire. Use .030" ER5356 wire for marine applications. Avoid 4000-series wire, as it is not rated for marine use and is much softer, leading to liner jams.
Exploring the Norse Term for 'Boat Dock
You may want to see also
Preparing the aluminium surface
Firstly, it is important to thoroughly clean the aluminium surface to remove any dirt, grease, or oxide layers. Use a stainless steel brush designed specifically for aluminium to scrub the surface. This step is crucial as it ensures that the weld pool is clean and free from any contaminants that could weaken the weld.
Next, use a solvent to clean off any remaining oil or grease. This step will ensure that the surface is completely free of any substances that could interfere with the welding process.
Once the surface is clean, it is important to ensure that it is free of any aluminium oxide. Use a stainless steel brush or a flap wheel to remove any traces of aluminium oxide left over from grinding. Aluminium oxide can compromise the integrity of the weld, so it is important to ensure that the surface is thoroughly cleaned.
After cleaning, it is essential to prepare the area for welding. Set up a portable welding shelter to shield the area from wind, dust, and moisture if welding outdoors. This will help maintain a stable welding environment and improve the overall quality of the welds.
Additionally, ensure that you are wearing appropriate safety gear, including protective eyewear and clothing, to shield yourself from any sparks or debris during the welding process.
By following these steps, you will ensure that the aluminium surface is properly prepared for MIG welding, resulting in strong and durable welds for your boat project.
Repairing Leaks in Your Porta Boat: A Step-by-Step Guide
You may want to see also
Controlling heat input
Aluminium's high thermal conductivity can make welding challenging. It is important to control heat input to avoid warping or burn-through. Here are some tips to help you manage the heat flow and create consistent welds:
Use short welds: To prevent overheating, keep your welds short and allow the aluminium to cool between passes. This gives the material time to dissipate heat and reduces the risk of warping or burn-through.
Preheat the aluminium: Preheating the aluminium slightly can help manage the heat flow. It ensures a more consistent temperature throughout the material, reducing the risk of warping.
Use the right equipment: Choose a welder designed for aluminium welding, such as a MIG or TIG welder. These machines provide a stable wire feed and reduce the risk of contamination, which is crucial for achieving solid and clean welds.
Maintain a consistent travel speed: When welding, move at a steady pace to ensure even heat distribution along the weld. Practice steady hand movements and keep a close eye on the weld pool.
Use a push technique: When welding aluminium, use a push technique instead of a pull technique. This helps keep the shielding gas in the weld pool, reducing the risk of contamination.
Practise proper technique: Refine your welding technique through consistent practice. This will improve the quality and appearance of your welds, making it easier to control the heat input.
By following these tips, you can effectively control the heat input when MIG welding aluminium boats, resulting in strong and durable welds.
Docking an Inboard Boat: A Step-by-Step Guide to Success
You may want to see also
Choosing the right filler material
For most marine-grade aluminium, 5356 and 4043 filler materials are the most commonly used. 5000-series wire is rated for marine use, whereas 4000-series wire is not. 5356 filler wire is often selected for its superior strength and corrosion resistance, making it ideal for boat welding. It is suitable for welding in all positions and can handle the challenging conditions that boats often face.
On the other hand, 4043 filler wire is softer and more prone to jamming in the liner. It is also more susceptible to contamination, which can lead to weld issues. However, it is still a suitable option for aluminium boat welding, especially if you are working with thinner aluminium sheets.
When selecting your filler material, it is crucial to check the specifications of your aluminium and choose a filler that complements it. This will ensure the best results and help you avoid issues such as warping or burn-through.
Additionally, consider the equipment you are using. If you are using a MIG welder, you may need to invest in a spool gun to feed the soft aluminium wire more effectively and reduce the risk of bird-nesting. Alternatively, a push-pull gun can be used for greater comfort and control, but it is a more expensive option.
Remember, taking the time to choose the right filler material will pay off in the long run, ensuring strong and durable welds on your aluminium boat.
Don Hume's Fate: A Boy in the Boat
You may want to see also
Practicing proper technique
Start by setting a consistent travel speed for your welding torch. This ensures even heat distribution along the weld, preventing warping or burn-through. Practice steady hand movements and maintain a close watch on the weld pool to avoid any mishaps.
Use a push technique instead of a pull technique when welding aluminium. This helps to keep the shielding gas in the weld pool, minimising the risk of contamination. Always ensure you have a straight gun lead to prevent bird-nesting of the soft aluminium wire.
Before welding, thoroughly clean the aluminium surface with a stainless steel brush designed for aluminium. This removes any dirt, grease, or oxide layers and ensures a clean weld pool, preventing weak welds.
When welding, focus on keeping the weld area clean and free from contaminants. Environmental factors like wind, dust, and moisture can affect the quality of your welds, so consider using a portable welding shelter if working outdoors.
Additionally, control your heat input by using short welds and allowing the aluminium to cool between passes. Preheating the aluminium slightly can also help manage heat flow and create more consistent welds.
Finally, practice makes perfect. Consistently refine your technique through regular practice to significantly improve the quality and appearance of your welds.
Overtaking Power-Driven Boats: Safe Action Steps to Take
You may want to see also
Frequently asked questions
You will need a MIG welder with a spool gun and a push-pull gun. You will also need a stainless steel brush, a teflon liner in the MIG gun, and a wind screen if you are working outdoors.
Clean the aluminium thoroughly to remove any dirt, grease, or oxide layers. Use a stainless steel brush to clean the surface just before welding.
The best way to fix a hole or a split seam is to use a metal-to-metal bond. You can use a product like Super Alloy 5, which is a permanent solution with a bonding strength of 30,000 psi.