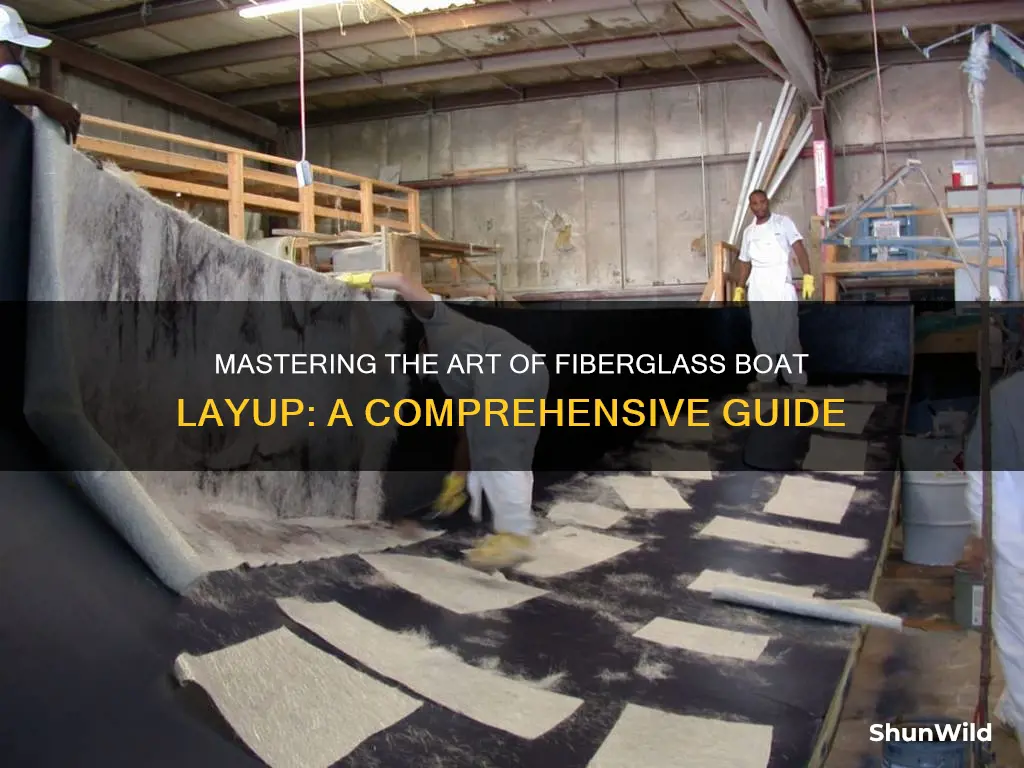
Laying up a fiberglass boat is a meticulous process that requires skill, patience, and attention to detail. It involves carefully applying layers of fiberglass cloth and resin to create a sturdy and lightweight hull. This technique is often used in boat construction to reinforce structural integrity and enhance the boat's performance on the water. The process begins with preparing the boat's mold, ensuring it is clean and free of debris. Then, the craftsman meticulously applies the first layer of fiberglass, followed by multiple layers of cloth and resin, each requiring precise placement and careful smoothing to eliminate any air bubbles. This labor-intensive task demands a steady hand and a keen eye for detail to achieve a smooth, seamless finish that will withstand the rigors of the marine environment.
What You'll Learn
- Prepare the Hull: Clean, sand, and prime the boat's surface for fiberglass application
- Choose the Right Resin: Select a suitable resin for the specific boat type and conditions
- Laying Up Process: Apply layers of fiberglass cloth and resin, ensuring proper bonding and reinforcement
- Molding and Shaping: Use molds to shape the fiberglass, creating a smooth and durable hull
- Finishing Touches: Sand, fair, and paint the boat to achieve a professional and attractive finish
Prepare the Hull: Clean, sand, and prime the boat's surface for fiberglass application
Before you begin the process of laying up a fiberglass boat, it's crucial to ensure that the hull is prepared meticulously. This initial step is vital as it sets the foundation for a strong and durable fiberglass structure. Here's a comprehensive guide on how to prepare the hull:
Cleaning the Hull:
The first step is to give the boat's hull a thorough cleaning. This process involves removing any dirt, grime, or old paint that might be present on the surface. Start by using a pressure washer to remove any loose debris and contaminants. If there's existing paint or gelcoat, it's essential to scrape it off carefully to ensure a clean base. For stubborn stains or old paint, consider using a chemical paint remover, but always follow the manufacturer's instructions to avoid any damage to the hull. Rinse the hull thoroughly after cleaning to remove any residue.
Sandblasting (Optional but Recommended):
For an even more thorough preparation, consider sandblasting the hull. This process involves using a high-pressure stream of abrasive material to remove any remaining paint, old gelcoat, or imperfections. Sandblasting provides a smooth and uniform surface, ensuring better adhesion of the fiberglass. If you decide to sandblast, use a suitable abrasive material like aluminum oxide or silicon carbide, and follow the safety guidelines for operating sandblasting equipment.
Sanding the Hull:
After cleaning, it's time to sand the hull's surface. Start with a coarse-grit sandpaper (e.g., 40-60 grit) to remove any remaining imperfections and create a rough surface for the primer to adhere to. Gradually move to finer grits (e.g., 80-120 grit) for a smoother finish. Pay attention to all areas, including the stringers, bulkheads, and any other structural components. Ensure that the sanding is even and consistent to avoid any uneven primer application.
Priming the Hull:
Priming is a critical step to ensure the fiberglass adheres properly and provides a smooth surface for the gelcoat. Use a high-quality marine primer suitable for fiberglass applications. Apply the primer in thin, even coats, allowing each coat to dry thoroughly before applying the next. Start from the bottom of the hull and work your way up, ensuring complete coverage. The primer will help fill in any minor imperfections and create a uniform base for the fiberglass.
Once the priming process is complete, inspect the hull for any remaining imperfections or uneven areas. These can be filled with a suitable filler material, sanded again, and then re-primed if necessary. Proper preparation of the hull is key to a successful fiberglass layup, ensuring a strong and long-lasting boat.
Boat Ramps in Naples: Open for Launch?
You may want to see also
Choose the Right Resin: Select a suitable resin for the specific boat type and conditions
When it comes to laying up a fiberglass boat, choosing the right resin is a critical step that can significantly impact the boat's performance, durability, and overall success of the project. The resin acts as a binding agent, holding the fiberglass cloth and other materials together, so selecting the appropriate type is essential. Here's a guide to help you make an informed decision:
Understanding Resin Types: Resins can be broadly categorized into two main types: polyester and epoxy. Polyester resins are known for their ease of use and fast curing properties, making them a popular choice for beginners. They are generally less expensive and offer good adhesion to various substrates. However, polyester resins may not provide the same level of strength and flexibility as epoxy resins. Epoxy resins, on the other hand, are renowned for their exceptional strength, durability, and resistance to chemicals and UV light. They create a strong, rigid bond and are often used in high-performance applications.
Boat Type and Conditions: The choice of resin should be closely tied to the specific type of boat you are building or repairing. For recreational boats, such as sailboats or powerboats, epoxy resins are often preferred due to their superior strength and longevity. These boats may be exposed to various environmental conditions, including saltwater, so a resin with excellent chemical resistance is crucial. For smaller, lightweight boats or those used in freshwater, polyester resins can be a suitable and cost-effective option. Consider the boat's intended use, expected loads, and the environmental factors it will encounter.
Environmental Factors: The conditions in which the boat will operate play a vital role in resin selection. If the boat is intended for saltwater environments, epoxy resins with added UV stabilizers and salt spray resistance are ideal. These resins provide enhanced protection against corrosion and degradation caused by saltwater exposure. For boats operating in freshwater or those with limited exposure to harsh elements, standard epoxy or polyester resins may suffice. Always consider the local climate and the potential for extreme weather conditions when making your choice.
Mixing and Application: Once you've chosen the appropriate resin, it's essential to follow the manufacturer's instructions for mixing and application. Proper mixing ensures the resin and hardener are combined in the correct ratio, which is critical for optimal curing and performance. Always wear protective gear, including gloves and respirators, when handling resins to avoid skin irritation and inhalation risks.
Remember, the right resin selection is a fundamental aspect of fiberglass boat construction or repair, ensuring the boat's structural integrity and long-term performance. It requires careful consideration of the boat's purpose, environmental conditions, and the specific properties offered by different resin types.
Charging Boat Batteries: Keep Your Boat Afloat
You may want to see also
Laying Up Process: Apply layers of fiberglass cloth and resin, ensuring proper bonding and reinforcement
The laying-up process is a crucial step in building a fiberglass boat, as it involves creating a strong, lightweight structure that will form the hull and other components. This methodical process requires precision and attention to detail to ensure a durable and aesthetically pleasing boat. Here's a step-by-step guide to applying layers of fiberglass cloth and resin for optimal bonding and reinforcement:
Preparation: Before beginning, ensure you have all the necessary materials, including fiberglass cloth (also known as cloth or weave), epoxy or polyester resin, a catalyst to initiate the curing process, and a release agent to prevent the cloth from sticking to the surface. Prepare your workspace by laying down a tarp or drop cloth to catch any spills and protect your surroundings. Wear appropriate safety gear, such as gloves, goggles, and a respirator, to protect yourself from resin fumes.
Surface Preparation: Start by cleaning the surface where the fiberglass will be applied. Remove any dirt, grease, or old paint using a mild detergent and water solution. Rinse thoroughly and allow the surface to dry completely. This step is vital to ensure proper adhesion of the resin to the substrate.
Cloth Application: Begin laying up the fiberglass by cutting the cloth into manageable pieces. Start with a base layer, applying the resin to the surface and then carefully placing the cloth, ensuring it is smooth and free of wrinkles. Use a roller or a brush to gently press the cloth onto the resin, creating good contact. Continue this process, adding multiple layers of cloth, allowing each layer to cure slightly before applying the next. This technique, known as 'wet-laying,' creates a strong, bonded structure.
Reinforcement and Bonding: To reinforce critical areas, such as the hull stringers and ribs, apply additional layers of cloth and resin. Use a higher concentration of resin in these areas to create a stronger bond. Ensure that each layer is properly bonded to the previous one by overlapping the cloth slightly and allowing the resin to flow between the layers. This technique, known as 'lamination,' adds structural integrity to the boat.
Curing and Finishing: After the final layer of cloth and resin is applied, cover the boat with a plastic bag or a curing cloth to protect it from dust and moisture. Allow the boat to cure according to the resin manufacturer's instructions, typically overnight. Once cured, inspect the boat for any imperfections and make necessary repairs or touch-ups. This process ensures a smooth, seamless surface ready for further customization and finishing.
Remember, the key to a successful lay-up is patience and attention to detail. Take your time, follow the resin manufacturer's guidelines, and seek guidance from experienced boat builders if needed. Properly applied layers of fiberglass cloth and resin will result in a sturdy and long-lasting boat.
McCook Lake's Boat Launch: A South Dakota Gem
You may want to see also
Molding and Shaping: Use molds to shape the fiberglass, creating a smooth and durable hull
When it comes to building a fiberglass boat, molding and shaping the hull is a critical step that requires precision and attention to detail. This process involves using molds to create a smooth and durable structure, ensuring the boat's overall quality and performance. Here's a step-by-step guide to mastering this technique:
Mold Preparation: Begin by selecting or designing a mold that suits the desired shape of your boat's hull. The mold should be made from a suitable material, such as wood, plastic, or aluminum, ensuring it is sturdy and can withstand the fiberglass resin. Create a detailed pattern or template to guide the molding process, ensuring all curves and contours are accurately represented.
Fiberglass Application: Start by laying a base layer of fiberglass cloth or mat onto the mold. This initial layer provides a strong foundation and helps distribute the resin evenly. Use a brush or roller to apply the resin, ensuring complete coverage and avoiding any air bubbles. Allow the resin to set slightly, making it easier to work with.
Building Up Layers: Continue the process by adding more layers of fiberglass, gradually building up the thickness. Each layer should be carefully positioned and smoothed out to maintain the desired shape. Use a wet cloth or a tool to smooth out any wrinkles or imperfections, ensuring a seamless surface. Remember, the goal is to create a smooth, continuous shell that mimics the mold's shape.
Reinforcement and Strength: Incorporate reinforcement materials such as fiberglass tape or rovings at strategic points to enhance strength and durability. These reinforcements are especially important in areas prone to stress, like the boat's sides and bottom. Carefully lay the tape or rovings over the mold, ensuring proper alignment and coverage.
Finishing and Smoothing: Once the final layer of fiberglass is applied, allow the resin to cure completely. After curing, inspect the hull for any imperfections and use a variety of tools, including files, sandpaper, and putty, to smooth out any rough spots. Achieving a smooth surface is crucial for the boat's aesthetics and functionality.
By following these steps and paying close attention to detail, you can create a beautifully molded and shaped fiberglass boat hull. This process requires practice and a keen eye for precision, but the results will be a sturdy and visually appealing vessel.
Pasco County Boat Ramps: Open or Closed?
You may want to see also
Finishing Touches: Sand, fair, and paint the boat to achieve a professional and attractive finish
The final steps of your fiberglass boat project are crucial to achieving a smooth, professional finish. Here's a detailed guide to the finishing touches:
Sandblasting:
- This is essential for creating a smooth surface for paint adhesion. Use a sandblaster with an abrasive material like aluminum oxide or silicon carbide. Focus on the areas where the fiberglass cloth shows through the gelcoat, as these areas need to be thoroughly prepared.
- Start with a coarse grit (40-60) to remove any remaining gelcoat imperfections and roughen the surface. Then, switch to a finer grit (80-120) for a smoother finish.
- Be careful not to over-sand, as this can damage the fiberglass. Work in small sections and follow the direction of the layup.
Fairing:
- Fairing is the process of smoothing out the boat's surface using putty, filler, or specialized fairing compounds. This step is crucial for a professional-looking finish.
- Use a high-quality two-part epoxy putty or filler, following the manufacturer's instructions for mixing and application.
- Fill in any gaps, imperfections, or tool marks left by the layup process. Work carefully and sand between coats to ensure a smooth surface.
- For best results, use a fairing block or a smooth, rounded tool to shape the filler and create a seamless transition between panels.
Painting:
- Choose a marine-grade paint suitable for fiberglass surfaces. Acrylics and epoxies are popular choices.
- Prepare the boat's surface by cleaning it thoroughly and ensuring it is free of dust and debris.
- Apply a primer specifically designed for marine environments to provide optimal adhesion.
- Follow the paint manufacturer's instructions for the number of coats and drying times. Typically, multiple thin coats are better than a few thick ones.
- Consider adding a clear coat for added protection and a glossy or matte finish, depending on your preference.
Additional Tips:
- Practice good ventilation when using sandblasters, fairing compounds, and paints.
- Wear protective gear, including gloves, goggles, and a respirator.
- Take your time and be meticulous in your work. A well-finished boat will reward your effort.
- If you're unsure about any step, consider consulting a professional or seeking guidance from experienced boat builders.
The Mystery of Missing Bums on a Boat
You may want to see also
Frequently asked questions
Begin by ensuring the boat is clean and free of any dirt, grime, or old paint. Rinse the surface with water and allow it to dry completely before proceeding.
The choice of cloth depends on the specific application and structural requirements. For structural repairs, use a woven fiberglass cloth with a high-modulus glass fiber for strength. For cosmetic repairs or fairing, a non-woven or mat glass cloth is often preferred for its smooth finish.
Gelcoat is a clear or colored epoxy resin that provides a protective layer and a smooth finish to the boat's surface. It is applied after the fiberglass cloth to create a seamless and durable exterior. Gelcoat adds color, protection against UV rays, and helps prevent osmosis.
Cleaning the surface thoroughly is crucial for bonding. Use a sharp blade to remove any old gelcoat or paint, ensuring a rough surface for the fiberglass to adhere to. Prime the area with a suitable epoxy primer to enhance bonding and provide a strong foundation for the layup.
You will need a variety of tools including a sharp utility knife or blade for cutting the cloth, a putty knife for applying resins and cloths, a spray gun or brush for resin application, and a heat gun or hairdryer for curing. Additionally, ensure you have the necessary safety gear like gloves, respirators, and protective eyewear.