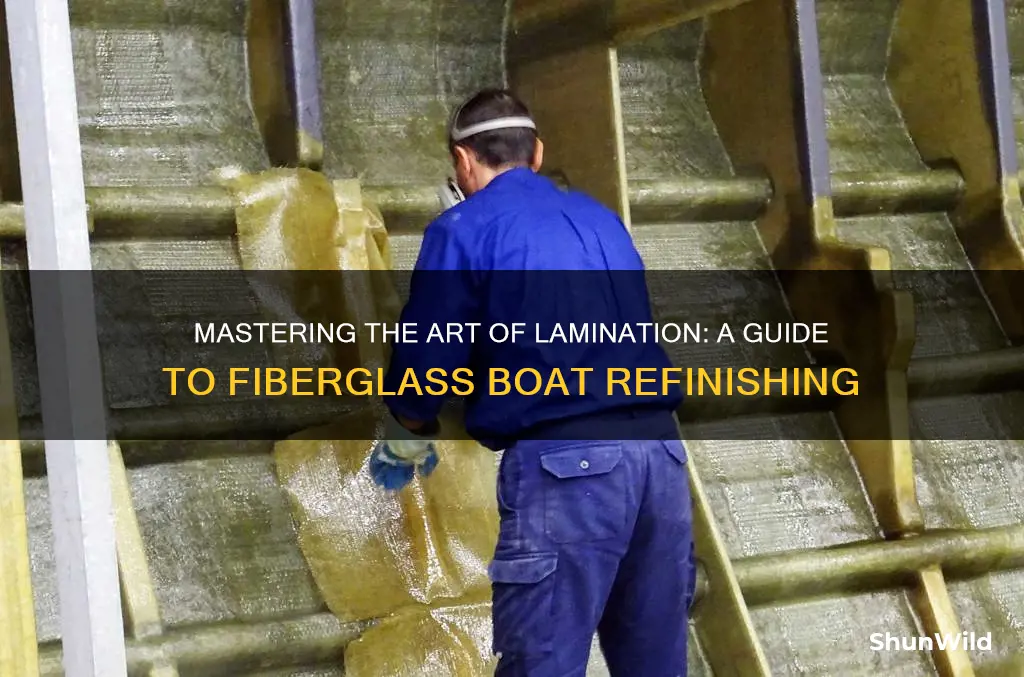
Laminating a fiberglass boat is a crucial process that involves bonding layers of fiberglass cloth with a resin to create a strong, lightweight hull. This technique is widely used in boat building due to its ability to provide structural integrity and resistance to water damage. The process requires careful preparation, including cleaning the surface, applying a primer, and ensuring proper mixing and application of the resin. It is essential to follow specific techniques, such as using a vacuum bag to create a uniform bond and avoiding air bubbles, to achieve a high-quality, durable boat. This guide will provide a step-by-step overview of the lamination process, offering valuable insights for boat enthusiasts and builders.
What You'll Learn
- Prepare the Hull: Clean, dry, and inspect the boat's surface
- Apply Primer: Use a suitable primer to ensure adhesion
- Laminate Application: Spread the laminate evenly, following manufacturer's instructions
- Molding and Shaping: Use molds to shape the laminate and create curves
- Curing and Finishing: Allow proper curing time and sand for a smooth finish
Prepare the Hull: Clean, dry, and inspect the boat's surface
Preparing the hull of your fiberglass boat is a crucial step in the lamination process, as it ensures a smooth and durable finish. Here's a detailed guide on how to get this task done effectively:
Cleaning the Hull: Start by thoroughly cleaning the entire surface of the boat. Fiberglass is a porous material, so any dirt, grime, or old laminating film must be removed. Use a mild detergent mixed with water and a soft brush to scrub the hull. Pay attention to all areas, including the bottom, sides, and any intricate details. Rinse the boat thoroughly with clean water to remove any soap residue. Ensure that the surface is completely dry before proceeding, as moisture can affect the bonding process.
Drying and Inspection: After cleaning, allow the hull to dry completely. You can speed up the process by using a fan or a hairdryer on a low setting, ensuring you don't overheat the fiberglass. Once dry, inspect the surface for any imperfections, such as small holes, scratches, or imperfections in the gelcoat. These issues should be addressed before lamination. You can use a fine-grit sandpaper (600-800 grit) to smooth out any rough areas and create a smooth, even surface for the laminate.
Removing Old Laminate (if applicable): If your boat already has an existing laminate layer, you'll need to remove it carefully. Use a sharp knife or a specialized laminate removal tool to carefully peel off the old laminate. Be cautious not to damage the fiberglass beneath. Ensure that all traces of old laminate are removed, as any residue can affect the new laminate's adhesion.
Final Inspection: Before proceeding with lamination, give the hull a final inspection. Check for any remaining dirt, dust, or debris that may have settled during the cleaning process. Ensure that the surface is completely dry and free from any contaminants. This step is essential to guarantee a successful bond between the new laminate and the hull.
The Best Name for My Boat: A Creative Guide
You may want to see also
Apply Primer: Use a suitable primer to ensure adhesion
When preparing to laminate a fiberglass boat, applying a suitable primer is a crucial step to ensure the adhesion of the laminate and create a strong, long-lasting bond. The primer acts as a base layer, providing a smooth surface for the laminate to adhere to and enhancing the overall structural integrity of the boat. Here's a detailed guide on how to apply the primer effectively:
Surface Preparation: Before applying the primer, ensure the fiberglass surface is clean, smooth, and free from any contaminants. Use a mild detergent or a specialized fiberglass cleaner to remove dirt, grease, and any existing coatings. Rinse thoroughly and allow the surface to dry completely. Inspect the fiberglass for any imperfections, such as small holes or scratches, and fill them with a suitable fiberglass repair compound. Smooth out the surface with a fine-grit sandpaper to create a uniform and level base for the primer.
Choosing the Right Primer: Select a primer specifically designed for fiberglass applications. These primers are typically epoxy-based and are formulated to provide excellent adhesion to the fiberglass substrate. Consider the environmental conditions and the type of laminate you will be using. For outdoor applications, a primer with UV resistance may be beneficial to prevent yellowing and degradation over time. Always follow the manufacturer's instructions for mixing and application ratios to ensure optimal performance.
Application Technique: Start by applying a thin, even coat of primer using a brush, roller, or spray gun. Ensure complete coverage, paying attention to edges, corners, and any complex contours. For a brush application, use long, even strokes, and for a roller, apply in a consistent pattern. If using a spray gun, maintain a steady distance and overlap the application to avoid gaps. Allow the primer to dry according to the manufacturer's guidelines, which may vary depending on the product and environmental factors. Typically, a second coat may be necessary for optimal coverage and adhesion.
Ventilation and Safety: When working with primers and other chemicals, ensure proper ventilation in the workspace. Wear appropriate personal protective equipment, including gloves, eye protection, and a respirator if necessary. Follow all safety instructions provided by the primer manufacturer to prevent any health risks.
By carefully preparing the surface, choosing the right primer, and applying it with precision, you can establish a strong foundation for the laminate, ensuring the boat's structural integrity and long-term performance.
Montgomery Boat Tragedy: What Happened?
You may want to see also
Laminate Application: Spread the laminate evenly, following manufacturer's instructions
When applying laminate to a fiberglass boat, ensuring an even and precise spread is crucial for a successful repair or customization project. Here's a step-by-step guide to achieving this:
Preparation: Before you begin, ensure the surface is clean and free of any debris. Use a mild detergent and water solution to wash the area, then rinse thoroughly. Allow the surface to dry completely; this is essential as any moisture can affect the laminate's adhesion. Gather all the necessary tools and materials, including the laminate sheet, a spreader or squeegee, and any additional equipment recommended by the manufacturer.
Application Technique: Start by cutting the laminate sheet to the appropriate size, slightly larger than the area you need to cover. This allows for a neat finish. Lay the laminate on the prepared surface, ensuring it is positioned correctly according to the manufacturer's guidelines. Begin spreading the laminate using a spreader or squeegee. Apply firm, even pressure to the tool, following the direction of the laminate's grain or pattern. Work in small sections, ensuring you cover the entire area without any wrinkles or bubbles. The key is to maintain consistency and avoid any gaps or overlaps.
Evenness and Adhesion: Pay close attention to the edges and corners, as these areas can be tricky to manage. Use the spreader or squeegee to carefully smooth out any excess laminate, ensuring a tight bond. If you encounter any air bubbles, gently press them out using a damp cloth or a similar tool. Allow the laminate to set according to the manufacturer's instructions, which may vary depending on the type of laminate used. This setting time is crucial to ensure the laminate hardens properly and adheres firmly to the fiberglass.
Finishing Touches: Once the laminate has set, inspect the application for any imperfections. If needed, carefully lift the edges and smooth out any creases or uneven areas using a damp cloth. This step ensures a professional finish. Allow the laminate to cure completely before handling the boat or applying any additional layers. Following the manufacturer's instructions for curing time is essential to avoid any issues with the laminate's integrity.
Remember, practice and patience are key when learning to laminate a fiberglass boat. Each project may require slight adjustments, so always refer to the specific guidelines provided by the laminate manufacturer for the best results.
The Mystery of Hasna's Boat Ownership Unveiled
You may want to see also
Molding and Shaping: Use molds to shape the laminate and create curves
When it comes to laminating a fiberglass boat, molding and shaping the laminate to create curves and contours is a crucial step to ensure a smooth and aesthetically pleasing finish. This process involves using molds to guide the laminate application and achieve the desired shape. Here's a detailed guide on how to approach this technique:
Understanding Molds:
Molds are essential tools for shaping the laminate and can be made from various materials such as wood, aluminum, or even custom-made plastic forms. The choice of mold material depends on the complexity of the boat's design and the desired level of detail. For simple curves, a wooden mold can be a cost-effective option, while more intricate designs might require a custom-made aluminum or plastic mold.
Preparing the Mold:
Before applying the laminate, ensure the mold is clean and free from any debris. You can use a mild detergent and water solution to clean the surface. Additionally, consider applying a release agent or a thin layer of petroleum jelly to the mold's interior to prevent the laminate from sticking. This step is crucial for easy removal of the shaped laminate later.
Applying the Laminate:
Now, it's time to work with the laminate. Start by carefully brushing the laminate resin onto the mold's surface, ensuring an even and thin layer. Pay close attention to the edges and corners, as these areas require precise handling. Use a small brush or a paintbrush to apply the resin, allowing it to penetrate the fiberglass cloth or fabric. Once the resin is applied, carefully place the fiberglass cloth or fabric onto the mold, ensuring it aligns with the desired shape.
Creating Curves:
To achieve curves, you'll need to manipulate the mold and the laminate. Gently press and shape the laminate around the mold's curves, using your hands or a soft tool to smooth it out. Take your time with this step, as rushing can lead to imperfections. For more defined curves, you might need to add layers of laminate and build up the shape gradually. Remember to maintain a consistent thickness to avoid any bulging or warping.
Curing and Removal:
After shaping the laminate, allow it to cure according to the manufacturer's instructions. Once cured, carefully remove the laminate from the mold. This process may require some patience, as you want to avoid damaging the shaped laminate. Gently peel or pry the laminate away from the mold, being mindful of any delicate areas.
Mastering the art of molding and shaping will enable you to create a fiberglass boat with smooth curves and a professional finish. Practice and precision are key to achieving the desired results.
Boating and Beer: Drinking Laws on the Water
You may want to see also
Curing and Finishing: Allow proper curing time and sand for a smooth finish
When laminating a fiberglass boat, the curing and finishing process is crucial to ensure a strong, durable, and aesthetically pleasing result. Proper curing time and sanding techniques are essential steps that should not be overlooked.
After applying the fiberglass cloth and resin, it's important to allow sufficient curing time. This process involves the chemical reaction between the resin and hardener, which creates a strong bond between the layers of fiberglass. The curing time can vary depending on the type of resin and hardener used, as well as the ambient temperature and humidity. As a general guideline, it is recommended to follow the manufacturer's instructions for curing time, typically ranging from 24 to 48 hours for each layer. During this period, the boat should be kept in a controlled environment, away from direct sunlight or extreme temperatures, to ensure optimal curing.
Once the curing process is complete, the boat will still have a rough surface due to the inherent texture of the fiberglass. This is where sanding comes into play. Before sanding, it's crucial to inspect the boat's surface for any imperfections or voids that may have formed during the lamination process. These issues should be addressed and filled with a suitable filler material to ensure a smooth finish. After filling and allowing it to cure, the sanding process can begin. Start with a coarse-grit sandpaper (e.g., 80-grit) to remove any excess resin and create a smoother surface. Gradually progress to finer grits (e.g., 120-grit, 180-grit) to achieve a fine, even finish. Take your time and be thorough, as this step significantly contributes to the overall appearance and feel of the boat's surface.
Sanding is a delicate process, and it's important to work in the direction of the fiberglass weave to avoid creating scratches. After sanding, the boat's surface should be smooth and ready for further finishing. At this stage, you can choose to apply additional layers of clear coat or paint to enhance the boat's appearance and provide additional protection. Remember, the goal is to create a seamless and professional-looking finish, so patience and attention to detail are key during the curing and finishing stages.
Boat Deck Essentials: What You Need to Know
You may want to see also
Frequently asked questions
Lamination is a process of bonding multiple layers of materials together, typically using a resin or adhesive. In the context of fiberglass boats, lamination is essential to create a strong, durable, and lightweight structure. It enhances the boat's structural integrity, making it more resistant to impact, corrosion, and UV damage. This process also improves the boat's overall finish and appearance, providing a smoother and more professional look.
Preparation is key to a successful lamination process. Start by thoroughly cleaning the fiberglass surface to remove any dirt, grease, or old glue residues. Ensure the surface is smooth and free of any imperfections. Repair any existing damage, such as holes or cracks, using appropriate fiberglass repair techniques. Once the surface is ready, apply a primer to create a uniform base for the laminate. This step ensures better adhesion and a more professional finish.
The lamination process for boats typically involves using a combination of materials. The primary material is a specialized epoxy resin, which acts as the bonding agent. This resin is mixed with a hardener and applied in layers, creating a strong and flexible bond. Other materials include fiberglass cloth or roving, which provides strength and structure, and a release film or backing material to protect the laminate during the curing process. The choice of materials depends on the specific requirements of the boat's design and intended use.