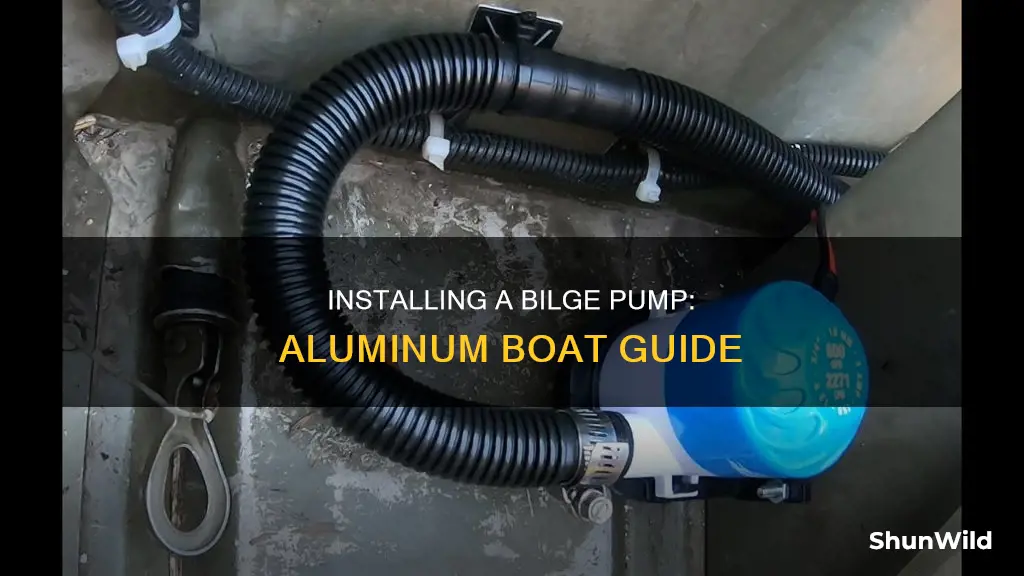
Installing a bilge pump in an aluminium boat is a straightforward process, but it's important to get it right. The pump must be fastened down to prevent it from sucking air and burning out, and the float switch must also be fastened. When it comes to the hoses, it's best to use smooth hoses with minimal bends and running. The discharge fitting should be placed above the waterline to prevent water from entering during surges and waves.
How to install a bilge pump in an aluminium boat
Characteristics | Values |
---|---|
Preparation | Clean and dry the boat, mark the water line, pre-measure the length of hose needed |
Mounting the pump | Fasten the pump to the boat to prevent it from pumping air instead of water. Use a bracket or base to avoid drilling into the hull directly. |
Connecting the hoses | Use smooth hoses with minimal bends and running. Avoid corrugated hoses. |
Discharge fitting | Ensure the discharge is above the water line to prevent water entering during surges and waves. |
Discharge fitting approach | Depends on the boat's materials. If replacing an existing pump, fit the new pump to the existing discharge hole. |
What You'll Learn
Fastening the pump
Firstly, decide on a suitable fastening method. One option is to use a bracket or base to attach the pump to a stringer or other vertical feature. This method avoids the need to drill directly into the hull. Brackets are available for purchase, or you can create your own using a piece of aluminium or stainless steel. Alternatively, you can epoxy a couple of bolts to the bottom of the bilge to serve as mounting studs.
If you opt for a bracket or base, ensure that it is securely attached to the pump. Some pumps have a side mount option, which can be screwed onto the bracket. Another option is to use a heavy-duty zip tie to secure the pump to the bracket. If you are using a base, you can glue the pump to it with marine adhesive/sealant or silicone.
When fastening the pump, it is important to consider the weight of the pump and whether it will need to be removed for maintenance or replacement. For example, if you use an adhesive to attach the pump, you may need to chisel it off later. In this case, consider using a less permanent adhesive or one that is easier to remove.
Additionally, if your boat is made of aluminium, be mindful of the materials you use for the bracket or base to avoid issues with galvanic corrosion, especially if your boat is exposed to salt water. Consider using a non-corrosive material such as aluminium or stainless steel.
Finally, don't forget to fasten the float switch as well, following the instructions provided with your pump.
Navigate Trove's Seas: Boat Driving Basics
You may want to see also
Hose configuration
The configuration of your hoses is essential to a proper install of a bilge pump on your boat and the overall efficiency of your bilge pumping system. You’ll want smooth hoses with as little bending and running as possible. The straighter you can get the hoses to work and dispense the water outside, the better.
Corrugated hose reduces pump output by as much as 30%, so always connect the pump to the discharge fitting with a hose that has a smooth interior surface. Bends and long runs also reduce pump output, so make the hose run as straight and as short as possible. That may mean discharging the pump through the side of the hull rather than through the transom.
When configuring the hose, try to avoid using corrugated hoses as these can sometimes get in the way of proper water flow even if you do have a straight hose system. However, don’t let your commitment to a straight hose force you to run it through vital components on your boat, either. Do your best for optimal efficiency and safety. Typically, this will mean trying a configuration with the hose before you install it on the pump.
When it comes to the discharge fitting, it is important to ensure that it remains consistently above the waterline. With your water line marked during your preparation phase, you’ll have no trouble ensuring that the bilge pump discharge comes from above the water line. You don’t want your system to bring in water during surges and waves, so it’s important to give your discharge enough space. Don’t let the fitting of the discharge go below the water line.
Fresh Off the Boat: Where to Stream the Show
You may want to see also
Discharge fitting
To ensure the bilge pump discharge comes from above the water line, it is important to mark the water line of your boat during the preparation phase. This will ensure that the discharge remains consistently above water during surges and waves. The discharge fitting must never go below the waterline.
The approach to the discharge fitting will depend on the boat's materials. If you are replacing an existing bilge pump, your boat will already have a discharge system in place. In this case, you can simply fit your new pump to the existing discharge hole.
If you are cutting a new hole, you can use a hole saw to cut a clean hole in the side of your aluminium boat. The size of the hole saw will depend on the size of the hole you need, but it is recommended to use a 3/4" metal hole saw. It is important to take your time and not put too much pressure on the hole saw to ensure a nice clean cut. After cutting the hole, use clear silicone (RTV) cement or 3M5200 to seal both sides.
When installing the discharge fitting, it is important to use a thin-wall fitting with the largest possible opening to minimise restrictions and maximise pump capacity. The discharge hose can be mounted over the transom or, if you cut a hole in the hull, ensure it is well above the waterline. Double clamp the hose at the through-hull fitting.
Boat Launches in Oregon: Open or Closed?
You may want to see also
Preventing corrosion
Aluminium boats are not entirely corrosion-proof, so it is important to take preventative measures to protect your boat from the effects of oxidation and corrosion. Here are some tips to prevent corrosion when installing a bilge pump in an aluminium boat:
- Use Sacrificial Zinc Anodes: Attach sacrificial zinc anodes to protect the aluminium. Zinc is less active than aluminium, so it will corrode first. However, avoid using too many zinc anodes, as this can cause the zinc to develop a crust and become ineffective.
- Proper Boat Maintenance: Always rinse your boat with freshwater after use, especially if it has been in saltwater. Repair any cracks or scratches that expose the bare aluminium, and avoid using an automotive battery charger on the boat.
- Coatings and Paint: Only use paint and coatings specifically designed for aluminium boats. Nyalic, for example, offers a coating system that covers repairs and helps to halt further corrosion.
- Avoid Corrosive Electrical Currents: Ensure that all electrical circuits are two-wire and fully insulated, with a separate insulated common earth lead or busbar. Do not ground any part of the electrical system to the vessel's fittings, as this invites corrosion.
- Battery Storage: Isolate storage batteries when not in use by removing both leads or using a suitable heavy-duty double-pole isolating switch.
- Avoid Stray Currents: Install a galvanic isolator in series with the AC grounding conductor of the shore power cable. This device helps prevent corrosion caused by electrolysis and stray currents found in moorings.
- Use Recommended Anodes: The American Boat and Yacht Council (ABYC) recommends using zinc anodes for aluminium boats in saltwater and magnesium anodes for freshwater applications. Aluminium anodes are also becoming popular as they work in both saltwater and freshwater.
- Bottom Paint: Apply bottom paint as an additional protective measure. However, note that copper-based bottom paints can react severely with stray electrical currents.
- Clean Regularly: Regularly clean your boat to remove any contaminants that could contribute to crevice corrosion. Use products specifically designed for aluminium boats, such as Salt-Away, CRC Salt Terminator, Starbrite Salt Off, Un-Duz-It, or the Salt Wash system from Salty Captain.
- Avoid Galvanic Corrosion: When joining different metals during installation, understand the galvanic relationship between them. Some metals, when joined, will create a galvanic couple, with one metal becoming the anode (less noble metal) and the other the cathode. This will result in a galvanic response, with the anode corroding faster. Refer to the anionic scale to determine the tendency of different metals to interact galvanically.
- Use Nylon Isolators: When using boat-top snaps made from plated steel, use nylon isolators to help curb corrosion.
- Avoid Crevice Corrosion: Ensure that your boat design does not have crevices or joints that might collect and trap water. Promote moisture drainage and ventilation to prevent crevice corrosion.
- Use Smooth Hoses: When installing the bilge pump, use smooth hoses with minimal bends and running. Corrugated hoses can reduce pump output and hinder proper water flow.
Show Boat's Ocean Liner Set: Authentic or Not?
You may want to see also
Connecting to the battery
When connecting the bilge pump to the battery, it is important to ensure that the pump remains active even when the boat is unattended. Therefore, you should connect an automatic bilge pump directly to the battery, bypassing the distribution panel.
It is also crucial to fuse the positive wire as close to the battery as possible. If your switch panel includes a fuse, you can use that. Otherwise, attach an in-line fuse holder to the battery end of the positive wire using a crimp butt connector.
For the terminal fittings, avoid stripping the ends of the supply wires and looping them under the battery terminal wing nuts. Instead, install crimp-on ring terminals that fit the threaded posts on your battery. Use a copper washer between the wing nut and the ring terminal—not a steel one.
If your bilge pump has a separate float switch, consider wiring it to a three-way switch, allowing you to choose between automatic, on, or off settings. Support all wire runs at least every 18 inches using cable clamps or ties.
The Ultimate Guide to Non-Marking Boat Shoes
You may want to see also
Frequently asked questions
You should clean and dry the boat, mark the water line, and pre-measure the length of the hose you will need.
You should fasten the pump to the boat using a bracket or base to avoid drilling into the hull directly. If you are using screws, coat them with duralac to prevent corrosion.
You should use smooth hoses with minimal bends and running. Avoid using corrugated hoses as these can get in the way of proper water flow.
The discharge fitting should be placed above the water line to prevent water from entering the boat during surges and waves.