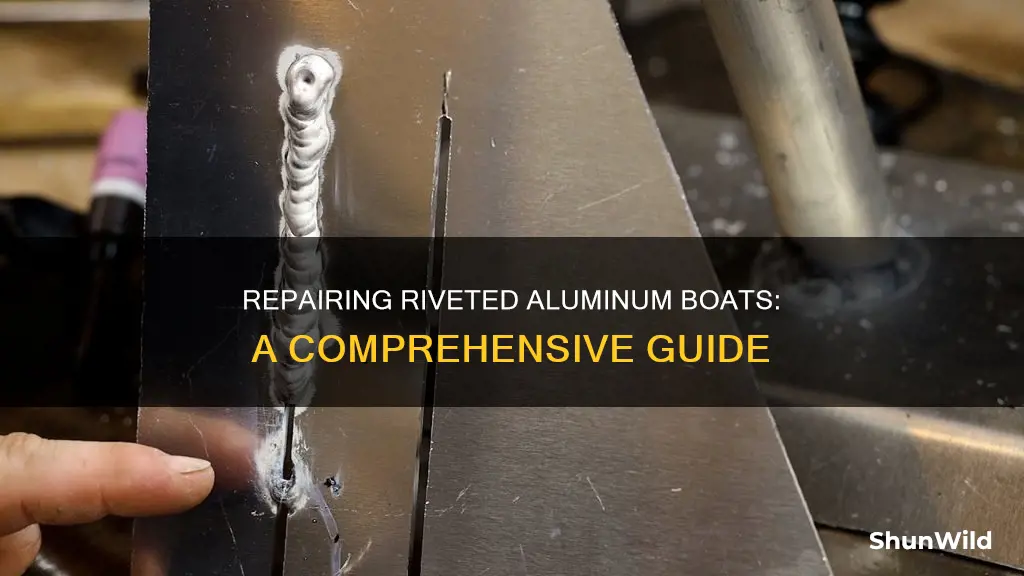
Owning an aluminum boat can be a lot of fun, but it also comes with its fair share of maintenance and repairs. One of the most common issues with aluminum boats is leaking rivets. Over time, the aluminum flexes and springs back to accommodate loads and impact, causing the rivets to loosen or break, resulting in leaks. While it may seem daunting, fixing a riveted aluminum boat is a manageable task with the right tools and knowledge. In this discussion, we will explore various methods and techniques to repair leaking rivets and ensure your boat remains seaworthy. From identifying leaks to choosing the appropriate repair materials, we will provide a comprehensive guide to help you confidently tackle this DIY project. So, whether you're an experienced boat owner or a novice, join us as we navigate through the process of fixing a riveted aluminum boat.
Characteristics | Values |
---|---|
Reason for rivets leaking | Wear and tear over time |
How to find leaking rivets | Fill the boat with water and mark leaking rivets, use a suction cup-type dent puller, or beach the boat and gradually slide it into the water |
How to fix leaking rivets | Rebuck (tighten) the rivet using a hammer and a buck (an anvil-like hunk of steel), replace the rivet, or use an epoxy-based sealer |
Tools required | Hammer, buck, angle grinder with a sanding disc, wire wheel, wire brush, handheld propane torch, heat gun, epoxy syringe, paper towels, epoxy |
Example products | Super Alloy 5, Muggy Weld, G/flex 650, WEST SYSTEM 650-K Aluminum Boat Repair Kit, TotalBoat FlexEpox, TotalBoat Aluminum Boat Leak Sealer |
What You'll Learn
Finding the leak
Before you can fix a leak in your aluminium boat, you need to find the source. There are a few ways to do this. Firstly, you can fill the boat with water, either partially or up to the waterline, and use a marker to circle any rivets that are leaking. If you don't want to fill the boat with water, or it's not possible, you can use a small suction cup-type dent puller. Place it over a rivet and pull a vacuum; if the rivet is leaking, it won't hold the vacuum seal.
If you want to avoid filling the boat with water, you can beach it and slide it into the water foot by foot, marking the leaking rivets as you go. Alternatively, get the boat off the ground and fill it with water, marking the leaks.
Once you've found the leaking rivets, you can start to repair them.
Glastron Boat Serial Number: Where to Find It
You may want to see also
Fixing the leak with epoxy
Fixing a riveted aluminium boat with epoxy is a straightforward process, but it requires the right tools and materials. Here is a detailed, step-by-step guide:
Identify the Leak:
First, you need to find the source of the leak. This can be done by filling the boat with water up to the waterline. If possible, fill one end and then the other to reduce the risk of damage or distorting the shape. Once you've identified the leaks, mark them with a waterproof marker.
Prepare the Surface:
Flip the boat over and prepare the surface around the leaks. For leaking seams, clean out any debris. For leaking rivets, clean the area and use a wire brush to roughen the surface, making it easier for the epoxy to adhere.
Mix the Epoxy:
Create a well-mixed blend of epoxy resin and hardener in a measuring container. For this project, a strong and flexible epoxy such as WEST SYSTEM G/flex® is recommended. The resin and hardener should be mixed in a 1:1 ratio.
Apply the Epoxy:
Extract the mixed epoxy into a syringe, such as the WEST SYSTEM® 807 Syringe. For larger repairs, you may need to cut off the tip of the syringe to create a larger opening. Dry out the area to be repaired by heating it to between 80-100°C using a handheld propane torch or a heat gun. This removes moisture and thins out the epoxy, allowing it to flow more easily into the seams and rivets. Use one hand to apply the epoxy from the syringe, while using a heat gun in the other hand to maintain the necessary heat. Ensure that all seams and rivets in the heated area are filled with epoxy.
Cure the Epoxy:
After applying a sufficient amount of epoxy, place the used syringe on a paper towel to catch any excess. Continue applying heat to the treated area with the heat gun until the epoxy has gelled. Then, you can either lower the heat setting and continue curing or allow it to cure slowly at room temperature.
Test the Repair:
Repeat the above process for each leak repair area, ensuring sufficient heat is maintained. Once the epoxy has completely cured, you can test your boat on the water. If applied correctly, the epoxy will not only stop the leak but also protect your boat for years to come.
Kick-starting an Old Boat: Simple Tricks to Try
You may want to see also
Using a rivet gun
Once you have identified the leaking rivets, you will need to remove the old ones. To do this, file or grind off one head, or drill it out, making sure not to enlarge the hole. When removing the old rivets, you will need to use a buck (an anvil-like hunk of steel) and a hammer. Hold the buck against the flat side of the rivet while you hammer the crimped end.
Now you are ready to use the rivet gun. Place the new rivet in the hole, with the unpeened (headless) end protruding by about 2/3 of its diameter. Use the rivet gun to set the rivet, ensuring that the metal sheets are in tight contact.
It is important to note that standard pop rivets are not suitable for use below the waterline, as they have a hole through them. Instead, look for closed-end pop rivets, which are specifically designed for this purpose.
Additionally, always follow the manufacturer's instructions and safety guidelines when using a rivet gun and make sure to wear the appropriate protective gear.
Understanding House Batteries: Powering Your Boat's Electrical System
You may want to see also
Removing old rivets
To remove old rivets from an aluminium boat, you will need to identify the type of rivet used. If it is a blind rivet, it will have a special "core" that needs to be knocked or punched out before drilling. It will also have a locking ring that will need to be pried out. Once you have removed the core and locking ring, drilling out the rest of the rivet should be relatively easy.
If you are dealing with a solid "driven" rivet, the process is slightly different. Start by centre-punching the head of the rivet to create a divot, which will help keep your drill bit in place. Use a drill bit that matches the size of the rivet shank and drill straight into the centre of the rivet head. Drill only deep enough to remove the head; if you go too deep, you risk enlarging the hole. Once the head is removed, you can punch or drive out the rest of the rivet.
Take your time and work slowly when drilling out old rivets. High speeds can cause the drill bit to heat up and temper the rivet, making it stronger and more difficult to remove. Use a sharp drill bit and go at a slow speed, gradually increasing as needed. Ensure that your drill is perfectly straight and stable to avoid enlarging the hole or damaging the surrounding material.
Alternatively, you can use a grinder to remove rivets. A grinder will cut through aluminium quickly, so go lightly and use a metal grinding wheel. You can also use a blowtorch to heat up and blow out the rivets, but this method may be less precise and could potentially damage the surrounding material if you are not careful.
Once the old rivets have been removed, you can proceed to install the new rivets. It is important to use the correct type and size of rivets for a secure and watertight fit.
Boat Tarp Materials: Choosing the Best Fabric
You may want to see also
Tightening loose rivets
To fix a riveted aluminum boat, you need to tighten loose rivets or replace them. Here are some methods to tighten loose rivets:
The Hammer and Buck Method:
This method requires two people (or long arms!). One person holds a buck (any anvil-like hunk of steel) tightly against the flat side of the rivet, while the other hammers the crimped end with a ball-peen hammer. A sledgehammer can also be used as the buck, along with a carpenter's hammer for tightening. It is important to avoid excessive hammering, as old aluminum rivets can split or break under heavy force.
The Rivet Gun Method:
This method involves using a rivet gun to tighten the rivets. However, it is important to note that a rivet gun may not work on all types of rivets, particularly solid rivets, which require force to set.
The Epoxy Method:
As a temporary solution, epoxies such as JB Weld or Glovit can be used to seal the rivets and prevent leaks. This method is useful if you cannot access the rivets from the top. However, it is important to note that epoxies are not a permanent solution, and replacing the rivets is generally a better option.
The Soldering Gun and Plastic Method:
This method involves using a gas soldering gun to heat the rivet area and then applying a melted plastic, such as a 2-liter plastic Coke bottle, to create a seal. This method is fast and effective but may not be suitable for all types of repairs.
The Super Alloy 5 and Oxyacetylene Torch Method:
This method involves using Muggy Weld's Super Alloy 5 rod and flux, applied with an oxyacetylene torch with a size 1 tip, to repair the leaky rivets. This creates a water-tight and air-tight seal, preventing further leaks.
Exploring Paddle Boat Rental Costs and Options
You may want to see also
Frequently asked questions
Fill the boat with water and circle any rivets that leak with a marker. If you are unable to fill the boat with water, use a small suction cup-type dent puller. Place it over a rivet and pull a vacuum. If the rivet holds the vacuum seal, it's good; if it doesn't, it will leak.
You can either rebuck (tighten) the rivet or replace it. To rebuck, get a friend to hold a buck (a hunk of steel) against the flat side of the rivet while you hammer the crimped end. To replace, first, source solid aluminum rivets from a marine supply house or sheet metal vendor. File or grind off one head of the old rivet, or drill it out, then insert the new rivet.
You can use an epoxy-based sealer such as West System G/Flex 650-K Aluminum Boat Repair Kit, TotalBoat FlexEpox, or TotalBoat Aluminum Boat Leak Sealer. Alternatively, you can use Muggy Weld's Super Alloy 5 and an oxyacetylene torch.