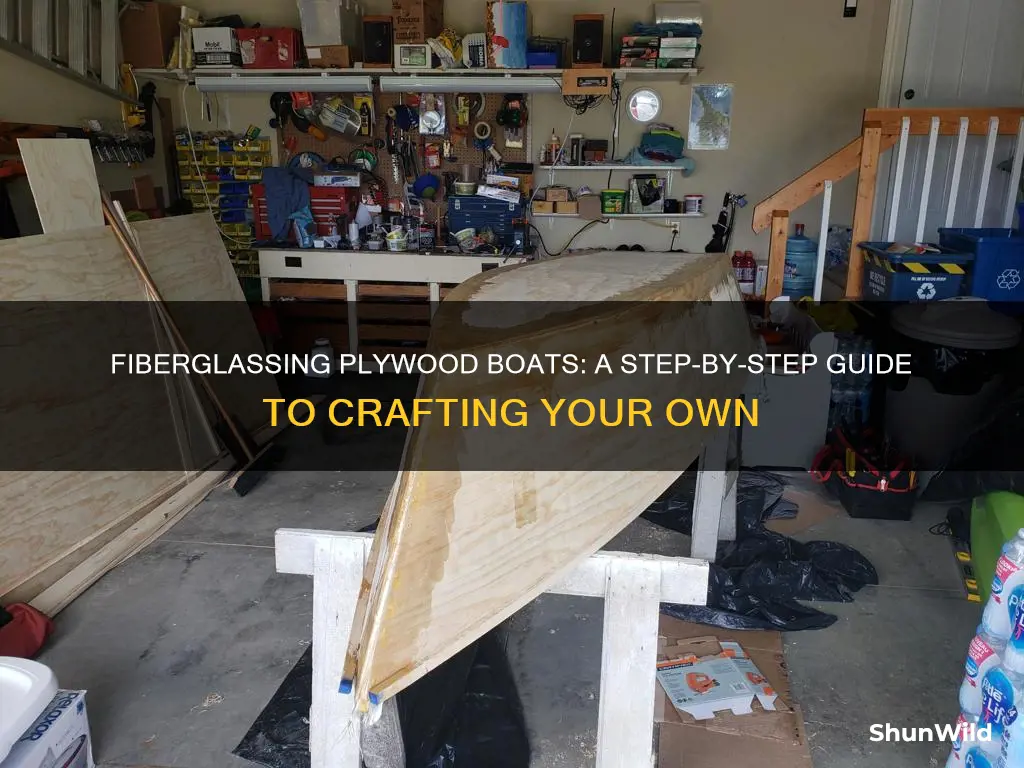
Fiberglassing a plywood boat is a crucial step in the boat-building process, allowing for a sturdy and durable vessel. This process involves applying a layer of fiberglass over the plywood hull to create a smooth, waterproof surface. It's essential to prepare the plywood surface by cleaning it, ensuring it's free of debris and old glue, and then applying a primer to create a strong bond for the fiberglass. The fiberglass is then laid over the hull, using a resin and cloth combination to create a seamless, strong shell. Proper techniques, such as using a rolling pin to smooth out bubbles and ensuring a consistent layer, are vital to the boat's structural integrity. This process requires patience and attention to detail, but the result is a beautiful, long-lasting boat.
What You'll Learn
- Prepare the Plywood: Sand and clean the surface for optimal bonding
- Choose the Right Fiberglass: Select the appropriate type and thickness for the job
- Apply the First Coat: Use a thin layer to create a smooth base
- Build Layers: Add multiple layers of fiberglass for strength and durability
- Finish and Sand: Smooth the surface and sand for a professional finish
Prepare the Plywood: Sand and clean the surface for optimal bonding
Preparing the plywood for fiberglassing is a crucial step to ensure a strong and durable bond between the two materials. This process involves sanding and cleaning the surface of the plywood to create a smooth, even, and roughened texture that will allow the fiberglass to adhere properly. Here's a detailed guide on how to achieve this:
Start by inspecting the plywood to identify any imperfections, such as protruding nails, screws, or splinters. Remove these potential hazards to prevent damage during the sanding process. Use a utility knife or a small saw to carefully cut away any sharp edges or protruding particles. This initial step ensures a safer and more thorough sanding experience.
Next, grab your sandpaper and begin the sanding process. It's essential to use a fine-grit sandpaper (e.g., 120-grit) to create a smooth base for the fiberglass. Start sanding in the direction of the wood grain, applying gentle pressure to avoid tearing the plywood. Work in small sections, ensuring you cover the entire surface evenly. As you progress, gradually switch to a finer grit (e.g., 180-grit) to refine the surface further and achieve a consistently smooth finish.
After sanding, the plywood should feel smooth to the touch, but it's crucial to create a slightly rough surface for optimal bonding. This can be achieved by using a slightly coarser sandpaper (e.g., 150-grit) or by lightly sanding in the direction opposite to the grain. This technique, known as cross-sanding, helps create a textured surface that will provide better adhesion for the fiberglass. Ensure you follow the direction of the grain to avoid damaging the wood.
Once you've completed the sanding, it's time to clean the surface. Use a tack cloth or a damp cloth to wipe down the plywood, removing any dust or debris. This step is vital as it ensures a clean and dust-free surface, free from any contaminants that could hinder the bonding process. Make sure to wipe the entire surface, paying attention to all edges and corners.
Finally, inspect the plywood once more to ensure it is free from any remaining dust or debris. At this point, the surface should be smooth, slightly textured, and clean, providing an ideal foundation for the fiberglass application. This meticulous preparation process will significantly contribute to the overall success and longevity of your fiberglass boat project.
Bulls Bay Boats: Worthy Watercraft or Not?
You may want to see also
Choose the Right Fiberglass: Select the appropriate type and thickness for the job
When it comes to fiberglassing a plywood boat, selecting the right type and thickness of fiberglass is crucial for a successful and durable repair or build. Here's a guide to help you make the right choice:
Understanding Fiberglass Types:
Fiberglass comes in various forms, each with unique characteristics. The two primary types are E-glass and S-glass. E-glass is the most common and affordable option, known for its strength and flexibility. It is ideal for structural applications and boat hulls due to its ability to withstand tension and compression forces. S-glass, on the other hand, offers higher strength and stiffness, making it suitable for specialized projects or areas requiring extra reinforcement. Choose E-glass for most boat applications to balance cost and performance.
Considering Thickness:
Fiberglass thickness is a critical factor in ensuring structural integrity. Thicker fiberglass provides more strength and impact resistance, making it ideal for load-bearing areas like the hull bottom and sides. For example, a 1/8-inch thick fiberglass cloth is commonly used for the hull, offering a good balance between strength and flexibility. In contrast, thinner cloths (around 1/16 inch) are suitable for non-structural areas, such as deck panels or interior components. Always refer to the manufacturer's guidelines and the specific requirements of your boat project to determine the appropriate thickness.
Fiberglass Weaving and Cloth Selection:
The weaving pattern of the fiberglass cloth can impact its performance. For boat construction, a plain weave or a glass cloth with a moderate weave count (around 4 to 6 ounces per square yard) is often recommended. This type of weave provides a balanced combination of strength and flexibility, allowing the fiberglass to conform to the shape of the plywood. Avoid highly textured or twill weaves, as they may not adhere well to the plywood and can lead to delamination issues.
Environmental Considerations:
The marine environment can be harsh, so choose fiberglass that is resistant to UV rays, chemicals, and saltwater. Some fiberglass types are treated with additives to enhance their durability. For example, UV-resistant fiberglass is ideal for exposed areas, ensuring the material doesn't degrade over time. Additionally, consider the temperature range of your project; some fiberglass types perform better in specific climate conditions.
Remember, the goal is to create a strong and durable bond between the fiberglass and the plywood. Proper preparation of the plywood surface, using the right adhesives, and following a meticulous lamination process are essential to achieving a successful fiberglass boat. Always refer to manufacturer guidelines and seek expert advice if needed to ensure the best results.
The Benefits of V-Hull Boats: A Comprehensive Overview
You may want to see also
Apply the First Coat: Use a thin layer to create a smooth base
Before you begin the process of applying the first coat of fiberglass to your plywood boat, it's crucial to ensure that the surface is clean, smooth, and free from any debris or imperfections. Start by thoroughly cleaning the plywood surface with a mild detergent and water solution. This initial step is essential to remove any dirt, grease, or old paint that might interfere with the bonding process. After cleaning, use a fine-grit sandpaper (around 120-150 grit) to gently sand the surface. This will create a slightly rough texture, providing better adhesion for the fiberglass. Be careful not to apply too much pressure, as you want to maintain the integrity of the plywood.
Once the surface is prepared, it's time to apply the first coat of fiberglass. This initial layer serves multiple purposes: it provides a smooth base for the subsequent layers, fills in any minor imperfections, and starts building the structural strength of the boat. Use a high-quality fiberglass resin and a suitable catalyst, mixed in the correct proportions as per the manufacturer's instructions. The key here is to use a thin, even layer. You want to create a smooth, continuous surface without any visible brush marks or lumps. A thin coat also allows for easier application and ensures that the fiberglass can easily conform to the shape of the plywood.
To apply the thin layer, use a small brush or a spray gun, depending on your preference and the size of the boat. If using a brush, ensure it is clean and slightly damp to avoid leaving any brush marks. Start in a small section and work your way across the plywood, keeping the coat thin and even. If using a spray gun, practice in an area away from the boat to get a feel for the pressure and coverage. Allow the first coat to cure according to the resin's instructions, which is typically a few hours or overnight.
After the first coat has cured, inspect the surface. It should be smooth and glossy, with no visible brush marks or imperfections. If there are any areas that require additional material, carefully reapply a thin layer to those spots, ensuring it blends seamlessly with the existing coat. This process of applying thin, even layers will continue for each subsequent coat, building up the strength and durability of the fiberglass boat. Remember, taking the time to apply each coat carefully will result in a high-quality, long-lasting boat.
Transferring Boat Ownership: Illinois Title Guide
You may want to see also
Build Layers: Add multiple layers of fiberglass for strength and durability
When building a fiberglass boat from plywood, adding multiple layers of fiberglass is a crucial step to ensure the structure's strength and durability. This process involves carefully applying fiberglass cloth and resin in several layers, creating a robust and lightweight composite material. Here's a detailed guide on how to achieve this:
Start by preparing your workspace and ensuring you have all the necessary materials. Clean the plywood surface thoroughly to remove any dirt or debris. Apply a suitable primer to the plywood, which will help the fiberglass adhere better and provide a smooth base for the resin. Allow the primer to dry completely according to the manufacturer's instructions.
Next, cut your fiberglass cloth to the appropriate size, ensuring it covers the entire area you intend to reinforce. Typically, you'll want to overlap the cloth slightly to create a seamless bond. Lay the first layer of fiberglass cloth over the prepared plywood, smoothing out any wrinkles or bubbles using a wet cloth or a tool like a putty knife. This initial layer provides a foundation for the subsequent layers to bond to.
Now, it's time to add the additional layers. Each layer should be applied at a slight angle to the previous one, creating a crisscross pattern. This technique, known as 'planking,' adds strength and prevents the boat from becoming too stiff in one area. As you apply each layer, ensure the cloth is fully saturated with the resin, and use a wet cloth to wipe away any excess. This process requires patience and a steady hand to achieve a smooth, bubble-free surface.
For added strength, consider incorporating carbon fiber or kevlar cloth into your layers. These materials offer excellent tensile strength and can be used in strategic areas like the hull's bottom or sides. Remember to cut the carbon fiber or kevlar cloth to size and apply it in the same manner as the regular fiberglass. Each additional layer will contribute to the boat's overall rigidity and impact resistance.
Finally, once all the layers are applied, allow the fiberglass to cure according to the resin manufacturer's guidelines. This process may take several days, depending on the type of resin used. After curing, sand the surface to create a smooth finish, ready for further customization or painting. Building multiple layers of fiberglass is an art that requires practice and attention to detail, but the result will be a sturdy and long-lasting boat.
The Open Boat: Theme of Man vs Nature
You may want to see also
Finish and Sand: Smooth the surface and sand for a professional finish
The finishing and sanding process is crucial for achieving a smooth, professional-looking boat. Here's a step-by-step guide to ensure a flawless surface:
Step 1: Prepare the Surface
Before sanding, ensure the fiberglass and plywood are thoroughly cleaned. Remove any dust, debris, or old adhesive residue. Use a mild detergent and water solution to clean the surface, then rinse and allow it to dry completely. This step ensures that the sanding process is effective and that the final finish adheres well.
Step 2: Apply a Primer
A primer is essential to create a smooth base for the final coat. Choose a marine-grade primer suitable for the type of fiberglass you're using. Apply the primer evenly across the entire surface, following the manufacturer's instructions. This step helps to seal the wood and fiberglass, providing a uniform base for the final sanding.
Step 3: Sanding Technique
Start with a coarse-grit sandpaper (e.g., 80-grit) to remove any imperfections and create a smooth canvas. Work in small sections, sanding with the grain of the wood and fiberglass. Once you've smoothed the surface, progress to a finer grit (e.g., 120-grit) to refine the texture. Pay close attention to corners and edges, as these areas require extra care and precision. Use a block or pad to apply consistent pressure and ensure an even sanding action.
Step 4: Fine Finishing
For an exceptionally smooth finish, consider using a power sander or a random-orbit sander. These tools provide a more aggressive sanding action, quickly removing any remaining imperfections. After sanding with the power tool, finish with a finer grit sandpaper by hand to achieve a smooth, scratch-free surface.
Step 5: Final Inspection and Touch-Ups
Once you've completed the sanding, inspect the boat's surface closely. Look for any remaining imperfections or uneven areas. Touch up these spots with additional sanding or a small amount of filler to ensure a seamless finish. This step is crucial for a professional appearance.
Remember, patience and attention to detail are key during the sanding process. Take your time, and don't rush the steps. Each sanding stage will bring you closer to a beautiful, durable boat finish.
Positioning Rod Holders: Aluminum Boat Optimization
You may want to see also
Frequently asked questions
Fiberglassing a boat involves applying a layer of fiberglass cloth or mat over a wet epoxy resin to reinforce and protect the underlying structure. Start by cleaning the plywood surface, ensuring it's smooth and free of debris. Apply a layer of epoxy primer to the plywood, let it cure, and then lay the fiberglass cloth, wetting it with epoxy to create a strong bond. Multiple layers may be required for added strength.
The choice of fiberglass depends on the specific requirements of your boat. For structural reinforcement, use a woven fiberglass cloth (e.g., 6 oz. or 8 oz. cloth) over multiple layers of epoxy. For cosmetic purposes, a lighter-weight cloth like 4 oz. or 5 oz. can be used. Always refer to the manufacturer's guidelines for your boat's construction.
Essential tools include a roll of fiberglass cloth, epoxy resin, a catalyst to mix with the resin, a spray gun or brush for application, a heat gun or hairdryer for curing, and safety gear like gloves, goggles, and a respirator. You'll also need a suitable primer, sandpaper, and a mask to cover the area you're working on.
Yes, fiberglass kits are available and can simplify the process. These kits typically include pre-mixed epoxy, fiberglass cloth, and sometimes a mold or pattern. They provide a structured approach, ensuring proper coverage and bonding. However, always follow the kit instructions and consider seeking guidance from experienced boat builders for complex projects.