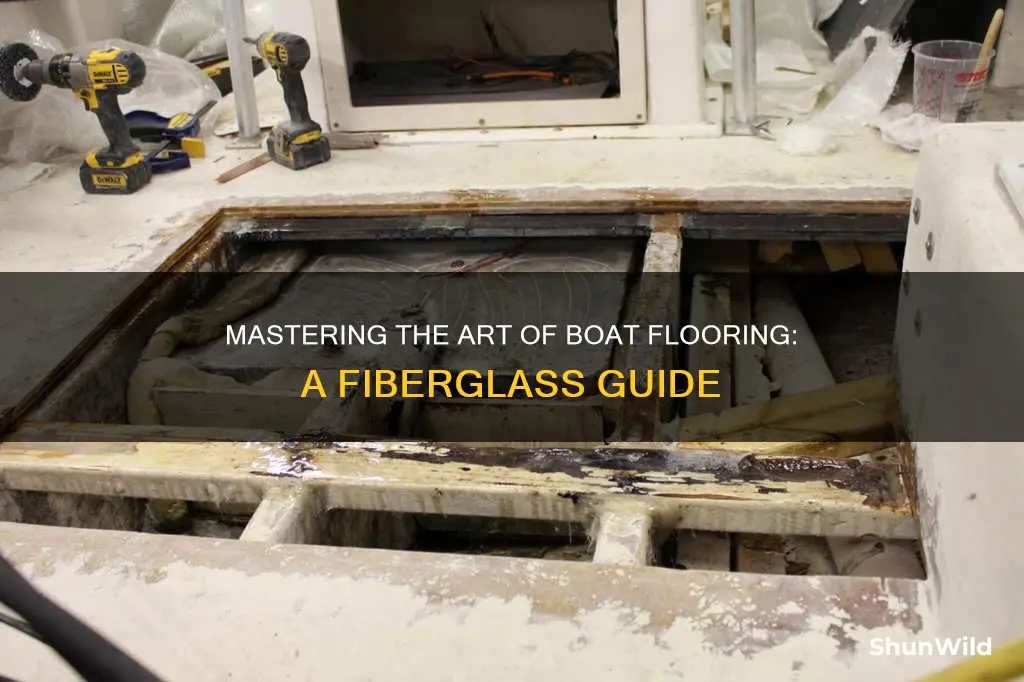
Fiberglassing a boat floor is a crucial step in restoring or customizing your vessel, ensuring both durability and aesthetics. This process involves applying a layer of fiberglass to the existing boat floor, which can be a challenging task but is achievable with the right tools and techniques. It's essential to prepare the surface properly, ensuring it's clean, smooth, and free of any debris. You'll need to gather the necessary materials, including fiberglass cloth, resin, and a suitable primer, and follow a step-by-step approach to achieve a professional finish. This guide will provide a comprehensive overview of the process, from surface preparation to the final curing, ensuring your boat floor is not only sturdy but also looks great.
What You'll Learn
- Prepare the Boat: Clean, sand, and prime the existing floor for a smooth base
- Choose Materials: Select the right fiberglass resin and cloth for a durable finish
- Lay the Cloth: Apply the fiberglass cloth in layers, following a pattern for strength
- Mix and Apply Resin: Mix the resin and hardener, then spread it over the cloth
- Finish and Sand: Smooth the surface, sand it, and apply a final coat for a professional look
Prepare the Boat: Clean, sand, and prime the existing floor for a smooth base
Preparing the existing boat floor is a crucial step before you begin the process of installing a new fiberglass floor. This initial preparation ensures a smooth and durable base for your new flooring, enhancing the overall appearance and longevity of the boat. Here's a detailed guide on how to tackle this task:
Cleaning the Floor: Begin by thoroughly cleaning the existing floor. Remove any dirt, grime, or debris that might be present. You can use a mild detergent mixed with water and a soft-bristled brush to scrub the floor. Ensure you reach every nook and cranny, paying extra attention to areas where dirt tends to accumulate, such as corners and beneath seating or storage compartments. Rinse the floor thoroughly with clean water to eliminate any soap residue. Allow the floor to dry completely before proceeding.
Sanding the Surface: Once the floor is clean, it's time to smooth out any rough patches or imperfections. Use a power sander or a handheld sander with a fine-grit sandpaper (around 120-150 grit). Start by gently sanding the entire floor, following the direction of the grain (if there is one). This process will help remove any old paint, stains, or rough spots. After sanding, use a damp cloth to wipe away the dust and ensure a clean surface. For a more refined finish, consider using a finer grit sandpaper (220-240 grit) to achieve a smoother base.
Priming the Floor: Priming is an essential step to ensure better adhesion of the new fiberglass flooring. Use a marine-grade primer suitable for the type of material you plan to use. Apply the primer evenly across the entire floor using a paintbrush or a small roller. Make sure to follow the manufacturer's instructions regarding drying times between coats. Typically, you'll apply two thin coats of primer, allowing sufficient time for drying between applications. This step creates a protective base and ensures that the new fiberglass floor adheres properly to the existing surface.
By completing these preparation steps, you'll create a smooth and ready-to-use base for your new fiberglass floor. This process is vital to ensure a professional-looking installation and to guarantee the long-term success of your boat flooring project. Remember, taking the time to properly prepare the existing floor will pay off in the end, resulting in a beautiful and durable finish.
Sanding Boat Hulls: Best Practices for Smooth Sailing
You may want to see also
Choose Materials: Select the right fiberglass resin and cloth for a durable finish
When it comes to fiberglassing a boat floor, choosing the right materials is crucial for a durable and long-lasting finish. The key components here are the fiberglass resin and the cloth, also known as the fiberglass cloth or mat. These materials work together to create a strong, lightweight, and corrosion-resistant surface.
Resin Selection:
Fiberglass resin is the binding agent that holds the fiberglass cloth together and provides structural integrity to the boat floor. There are two main types of resins to consider: epoxy and polyester. Epoxy resins offer superior strength, flexibility, and resistance to chemicals and UV light, making them ideal for marine environments. They also have a longer working time, allowing for easier application and shaping. Polyester resins, on the other hand, are more affordable and easier to work with, but they may not be as durable in the long term, especially in harsh marine conditions. For a boat floor, epoxy resin is generally the preferred choice due to its superior performance and longevity.
Fiberglass Cloth:
The cloth, or fiberglass mat, is available in various weights and weaves. The weight refers to the thickness of the cloth, with heavier weights providing more structural support. For a boat floor, a medium-weight cloth (typically around 4 to 6 ounces per square yard) is recommended for a balance between strength and ease of application. The weave refers to the pattern of the cloth fibers, with a random or mat weave being the most common for boat flooring. This type of weave provides a smooth, even surface for the resin to bond to. Avoid using a woven cloth, as it can create a visible pattern on the finished surface.
Additionally, consider the color of the cloth. While it might seem insignificant, using a white or light-colored cloth can make it easier to identify any imperfections or voids in the application, ensuring a more professional finish.
Combining Resin and Cloth:
The choice of resin and cloth should complement each other for optimal results. For example, using an epoxy resin with a polyester cloth can lead to a weaker bond due to the incompatibility between the two materials. Always refer to the manufacturer's guidelines and recommendations when combining these materials.
In summary, selecting the right fiberglass resin and cloth is essential for achieving a durable and aesthetically pleasing boat floor. Epoxy resins offer superior performance, while medium-weight, random-weave fiberglass cloth provides the necessary strength and ease of application. By carefully considering these materials, you'll create a robust and long-lasting finish for your boat's interior.
Bending Timber for Boat Hulls: Techniques for Shipwrights
You may want to see also
Lay the Cloth: Apply the fiberglass cloth in layers, following a pattern for strength
When laying the fiberglass cloth, it's crucial to follow a pattern that ensures strength and structural integrity. This process involves careful planning and execution to create a sturdy and durable boat floor. Here's a step-by-step guide to help you achieve this:
Start by preparing the area you'll be working on. Ensure the boat floor is clean and free of any debris or old material. If there are any existing layers of fiberglass, carefully remove them to create a smooth and clean surface. This preparation step is essential to ensure proper adhesion and a seamless finish.
Now, it's time to begin laying the fiberglass cloth. Start with a small section at a time, typically working in a grid pattern. Cut the fiberglass cloth to fit the shape of the boat floor, ensuring you have enough material to overlap and create a strong bond. Begin at one corner and apply the cloth, using a rolling pin or a similar tool to smooth out any wrinkles or bubbles. Apply light pressure to ensure the cloth adheres well to the surface. Allow the first layer to cure slightly, following the manufacturer's instructions for curing times.
For the next layer, carefully align the fiberglass cloth with the previous layer, overlapping it by a few inches. This overlapping technique creates a stronger bond and adds to the overall structural integrity. Again, use a rolling pin to smooth out any creases and ensure a tight fit. Continue this process, adding layers in a crisscross pattern, allowing each layer to cure before applying the next. This pattern provides strength and stability to the boat floor.
Remember, when laying the cloth, it's important to maintain a consistent pattern and ensure each layer is properly bonded. Take your time and be meticulous in your work. You can use a spray gun or brush to apply the resin, ensuring an even coat. Allow sufficient curing time between layers to avoid any issues with adhesion. By following this pattern, you'll create a robust and durable boat floor that can withstand the rigors of marine environments.
Securing Your Paddle Board to a Boat Dock: Easy Steps
You may want to see also
Mix and Apply Resin: Mix the resin and hardener, then spread it over the cloth
When it comes to fiberglassing a boat floor, one of the most crucial steps is mixing and applying the resin. This process requires precision and attention to detail to ensure a smooth and durable finish. Here's a step-by-step guide to help you master this technique:
Mixing the Resin and Hardener: Begin by gathering the necessary materials. You'll need the epoxy resin and its hardener, along with a mixing container and a suitable mixing tool, such as a plastic or metal spatula. Always wear protective gear, including gloves and a respirator, to avoid skin irritation and inhalation of fumes. Carefully measure the required amounts of resin and hardener according to the manufacturer's instructions. Typically, the resin and hardener are mixed in a 1:1 ratio, but it's essential to follow the specific guidelines for your chosen epoxy system. Use a clean, dry mixing container to avoid any contamination.
Preparing the Resin: Before mixing, ensure the resin and hardener are at room temperature. Stir the mixture gently to combine the components thoroughly. Over-mixing can lead to a stringy consistency, so be gentle and efficient with your stirring. The goal is to create a smooth, lump-free mixture. If you notice any clumps, gently warm the mixture and stir again until it becomes homogeneous.
Applying the Resin: Now, it's time to apply the mixed resin to the prepared cloth or fabric. Use a smooth, wide spatula or a similar tool to spread the resin evenly across the surface. Start from one edge and work your way to the other, ensuring complete coverage. Take your time with this step, as rushing can lead to uneven application. Aim for a thin, even layer, as multiple coats can be applied later to build up the desired thickness. Remember to work in a well-ventilated area or outdoors to ensure proper ventilation during the process.
Spreading Technique: When spreading the resin, maintain a consistent thickness by using gentle, overlapping strokes. This technique helps create a seamless and smooth finish. If you encounter any air bubbles, gently press them out with your spatula or a similar tool. Allow the applied resin to set for a short period, typically a few minutes, to ensure it becomes tacky before adding the next layer of cloth or fabric. This tacky surface will help the new layer adhere properly.
By following these steps, you'll be able to mix and apply the resin effectively, setting the foundation for a successful fiberglass boat floor installation. Remember, practice and patience are key to achieving professional results in this process.
Haunted St. Mary: A Ghost Ship?
You may want to see also
Finish and Sand: Smooth the surface, sand it, and apply a final coat for a professional look
To achieve a smooth and professional finish on your boat floor after fibreglassing, the following steps are essential. Firstly, ensure that the fibreglass surface is completely dry and free from any excess resin or debris. This is crucial as any remaining material can affect the final appearance and durability of the floor. Use a sharp knife or a utility blade to carefully remove any excess resin, being mindful not to scratch the surface.
Once the surface is prepared, it's time to smooth it out. This step is critical to the overall finish and appearance of the boat floor. Use a putty knife or a similar tool to gently spread a thin layer of fibreglass resin over the entire area, ensuring complete coverage. Allow this layer to set for a short period, typically around 15-20 minutes, depending on the ambient temperature and humidity. This initial layer acts as a bonding agent and provides a smooth base for the final finish.
After the initial layer has set, it's time to sand. Use fine-grit sandpaper (e.g., 400-grit or higher) to gently sand the entire surface. This process will help to refine the texture and ensure a smooth, even finish. Work in small sections, applying light pressure to avoid removing too much material. Once you've sanded the entire floor, wipe away any dust or debris with a damp cloth to prepare the surface for the final coat.
For the final coat, you can use a clear epoxy or a specialised marine varnish. These products provide a protective layer and enhance the appearance of the fibreglass. Apply the final coat using a brush or a spray gun, ensuring an even and thin layer. Allow it to set according to the manufacturer's instructions, and then sand again with finer grit sandpaper to achieve a smooth, glossy finish. This final sanding step is key to ensuring the surface is smooth and ready for any additional installations or use.
Remember, patience and attention to detail are vital during this process. Taking the time to properly prepare and finish the fibreglass floor will result in a high-quality, long-lasting boat interior.
Boat Batteries: Series or Parallel Configuration?
You may want to see also
Frequently asked questions
The initial step is to thoroughly clean the surface, ensuring it is free from dirt, grease, and any existing debris. Use a mild detergent and a soft brush to scrub the area, then rinse and allow it to dry completely before proceeding.
Achieving a smooth finish is crucial. Start by applying a thin layer of resin, followed by a layer of cloth or weave, ensuring it is evenly distributed. Use a roller or a trowel to smooth out any bubbles or wrinkles, and work quickly before the resin sets. Repeat this process until you achieve the desired thickness and strength.
For boat flooring, a lightweight epoxy resin is commonly used, which provides strength and durability without adding excessive weight. Choose a cloth or weave suitable for the resin; a woven glass cloth is ideal for adding strength and structure. Consider using a cloth with a higher glass content for added rigidity, especially if the floor will bear heavy loads.