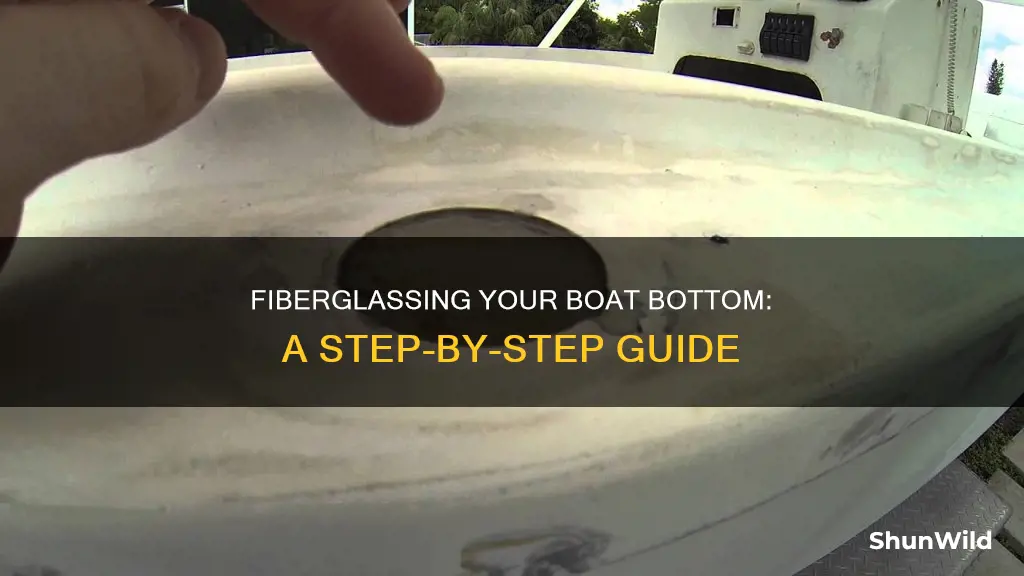
Fiberglassing a boat bottom is a crucial process for enhancing the boat's structural integrity, durability, and aesthetics. It involves applying a layer of fiberglass to the bottom of the boat, providing a smooth and sturdy surface that protects against wear and tear from water, UV rays, and other environmental factors. This process requires careful preparation, including cleaning the surface, applying a primer, and using the right type of fiberglass and resin to ensure a strong and long-lasting bond. By following a step-by-step guide and using the appropriate materials, you can achieve a professional-looking finish that will keep your boat in top condition for years to come.
What You'll Learn
- Prepare the hull: Clean, sand, and etch the surface for optimal bonding
- Choose the right resin: Select a suitable epoxy resin for the job
- Lay the cloth: Apply fiberglass cloth in a controlled manner for strength
- Apply resin and cloth: Spread resin evenly, then lay the cloth
- Finish and sand: Smooth the surface, then sand for a professional finish
Prepare the hull: Clean, sand, and etch the surface for optimal bonding
Preparing the hull is a crucial step in the process of fiberglassing a boat bottom, as it ensures optimal bonding and a smooth finish. Here's a detailed guide on how to tackle this task:
Cleaning the Hull: Begin by thoroughly cleaning the hull surface. This step is essential to remove any dirt, grime, or old paint that could interfere with the bonding process. Use a pressure washer or a high-pressure hose to rinse the entire hull, ensuring you remove any loose debris. For a more thorough clean, consider using a marine cleaner or a mild detergent mixed with water. Scrub the hull surface with a stiff brush to dislodge any stubborn dirt, especially in areas where dirt tends to accumulate, like the waterline and crevices. Rinse the hull again to remove any cleaning solution residue.
Sandblasting (Optional): For a truly smooth and uniform surface, consider sandblasting. This process involves propelling small abrasive particles onto the hull surface, which effectively removes any remaining paint, rust, or old fiberglass. Sandblasting can be done by professionals or with the help of a sandblaster machine. It provides a clean, smooth canvas for the fiberglass, ensuring better adhesion. If you opt for sandblasting, make sure to wear protective gear and follow all safety guidelines.
Sanding the Hull: After cleaning, it's time to sand the hull surface. Start with a coarse-grit sandpaper (e.g., 40-grit) to remove any remaining imperfections and create a rough surface for the fiberglass to adhere to. Work in small sections, sanding with the grain of the hull. Once you've smoothed out the surface, progress to a finer grit (e.g., 80-grit) to refine the texture. This step ensures that the fiberglass will bond securely and prevents the formation of a smooth surface that might not adhere well.
Etching the Surface: Etching the hull surface is a critical step to enhance bonding. It involves using a mild acid solution to roughen the surface further. You can purchase etching solutions specifically designed for marine applications. Apply the etching solution to the hull, following the manufacturer's instructions. Allow the solution to sit for the recommended time, which will vary depending on the product. This process will create a microscopic roughness on the surface, providing an excellent base for the fiberglass to bond. Rinse the hull thoroughly after etching to remove any acid residue.
By following these steps, you'll create a clean, smooth, and etched hull surface, ensuring a strong and durable bond for the fiberglass. This preparation process is key to the long-term success of your boat bottom fiberglassing project.
Fogging Malibu Boat Engines: What, Why, and How?
You may want to see also
Choose the right resin: Select a suitable epoxy resin for the job
When it comes to fiberglassing a boat bottom, choosing the right resin is a critical step that can significantly impact the strength, durability, and overall success of the project. Epoxy resins are commonly used in boat building due to their exceptional bonding capabilities and ability to create a strong, lightweight structure. Here's a guide to help you select the appropriate epoxy resin for your boat bottom fiberglassing endeavor:
Understanding Epoxy Resins: Epoxy resins are a type of polymer that, when mixed with a hardener, undergoes a chemical reaction, forming a hard, durable material. This process is known as curing, and it results in a strong bond between the fibers and the resin. There are various types of epoxy resins available, each with unique properties and applications. The key is to match the resin to the specific requirements of your boat bottom project.
Factors to Consider:
- Strength and Durability: For boat bottoms, you'll want a resin that offers excellent mechanical strength and resistance to wear and tear. Look for resins with high tensile and compressive strength, ensuring your boat can withstand the rigors of the water.
- Chemical Resistance: Boat bottoms are exposed to various chemicals, including saltwater, fuel, and cleaning agents. Choose an epoxy resin that is resistant to these chemicals to prevent degradation and maintain the integrity of the structure.
- Flexibility and Impact Resistance: Consider resins that provide a balance between rigidity and flexibility. This ensures that the boat bottom can absorb minor impacts without cracking or breaking, especially in areas prone to collisions or grounding.
- Viscosity and Application: Resins come in different viscosities, affecting their application. Thinner resins are easier to work with and can penetrate into the fibers better, while thicker resins might be more suitable for thick layers or structural repairs.
Types of Epoxy Resins:
- Aliphatic Epoxy: Known for their excellent resistance to chemicals and UV light, aliphatic epoxy resins are ideal for outdoor applications like boat building. They offer high strength and flexibility, making them a popular choice.
- Epichlorohydrin (ECH) Epoxy: This type of resin is commonly used in marine applications due to its excellent adhesion and chemical resistance. ECH resins provide good strength and are often used in combination with other resins for enhanced performance.
- Polyester-Modified Epoxy: These resins offer a balance between strength and ease of use. They are less brittle than pure epoxy resins and can provide good impact resistance, making them suitable for boat bottom applications.
Mixing and Application: Once you've chosen the right epoxy resin, follow the manufacturer's instructions for mixing and application. Proper mixing ensures a consistent and strong bond. Apply the resin in a controlled manner, allowing for adequate curing time between coats. This process may require multiple layers and careful attention to detail to achieve a smooth and durable boat bottom.
Remember, selecting the appropriate resin is a crucial step in the fiberglassing process, ensuring your boat bottom is not only aesthetically pleasing but also structurally sound and long-lasting.
Boat Insurance and Lightning: What You Need to Know
You may want to see also
Lay the cloth: Apply fiberglass cloth in a controlled manner for strength
When laying the fiberglass cloth, precision and control are key to ensuring a strong and durable boat bottom. Here's a step-by-step guide to achieving this:
Prepare the Surface: Before applying the cloth, ensure the boat bottom is clean and free of any debris. Use a sharp blade to carefully remove any old paint or gelcoat, creating a smooth and even surface. This preparation step is crucial for the fiberglass to adhere properly.
Apply the First Layer: Start by cutting a piece of fiberglass cloth slightly larger than the area you need to cover. Dip the cloth in the resin, ensuring it's well-saturated but not dripping. Begin at a corner or edge, and apply the cloth in a controlled manner, using a steady hand and a steady pace. Keep the cloth tensioned and smooth, avoiding any wrinkles or bubbles. Use a small brush or a trowel to gently work out any air pockets and ensure a tight bond.
Build Layers for Strength: For added strength, especially in high-stress areas, apply additional layers of fiberglass cloth. Each subsequent layer should be applied at a slight angle to the previous one, creating a crisscross pattern. This technique, known as 'cross-plying', enhances the structural integrity of the boat bottom. Allow each layer to cure slightly before applying the next, following the manufacturer's instructions for curing times.
Use a Mold or Form: To maintain a consistent shape and prevent the cloth from sagging, consider using a mold or form. This can be a simple wooden or plastic shape that fits the contours of your boat bottom. Secure the cloth to the mold using tape or clamps, ensuring it's taut and free of wrinkles. This method provides a more controlled application, especially for complex shapes.
Practice Precision: The key to a successful fiberglass job is attention to detail. Take your time and work in small sections, ensuring each layer is applied neatly and accurately. Use masking tape or painter's tape to outline the edges of the cloth, helping to prevent overspray and ensuring a clean finish. Precision in this step will result in a stronger and more aesthetically pleasing boat bottom.
Wiring Tower Speakers: Drilling Holes in Your Boat's Hull
You may want to see also
Apply resin and cloth: Spread resin evenly, then lay the cloth
When applying resin and cloth to the bottom of your boat, it's crucial to follow a systematic approach to ensure a smooth and durable finish. Start by preparing your workspace; a clean, well-ventilated area is essential for a safe and efficient process. Gather all the necessary materials, including the resin, cloth (preferably a suitable fiberglass cloth), a spreader or brush, and any additional tools you may need.
The first step is to spread the resin evenly across the prepared boat bottom. Use a spreader or a brush to ensure a consistent layer. Start in one corner and work your way across, maintaining a steady hand to avoid any uneven patches. Apply a thin, even coat, being careful not to overload the surface with resin. Allow the initial coat to set slightly, just enough for the resin to become tacky but not fully cured. This initial tackiness will help the cloth adhere better.
Once the resin is tacky, it's time to lay the cloth. Carefully position the fiberglass cloth over the resin, ensuring it is centered and smooth. Start at the center of the boat bottom and work outward, using a rolling motion to smooth out any bubbles or wrinkles. Apply firm pressure as you roll the cloth to ensure proper contact with the resin. Continue this process, overlapping the cloth slightly as you go, to create a seamless and strong bond.
After laying the cloth, inspect the surface for any imperfections or areas that require additional attention. Use a putty knife or a similar tool to gently remove any air bubbles that may have formed. If necessary, apply another thin layer of resin and repeat the cloth-laying process to build up the strength and smoothness of the fiberglass. Allow sufficient curing time between each layer to ensure proper bonding.
Remember, patience and precision are key during this stage. Take your time to achieve an even spread of resin and a smooth, bubble-free cloth application. This meticulous approach will result in a high-quality fiberglass job that will protect your boat's bottom and provide a long-lasting finish.
Sailing Shallow Waters: Choosing the Right Draft Boat
You may want to see also
Finish and sand: Smooth the surface, then sand for a professional finish
After the fiberglass application, the process of finishing and sanding is crucial to achieving a smooth and professional-looking boat bottom. This step ensures that the surface is not only visually appealing but also durable and ready for further customization. Here's a detailed guide on how to achieve a flawless finish:
Step 1: Inspect and Clean
Before beginning the sanding process, thoroughly inspect the fiberglass surface. Look for any imperfections, such as bubbles, runs, or uneven areas. These issues should be addressed and repaired if possible. If there are any remaining gelcoat imperfections, consider using a gelcoat repair kit to fill and smooth them out. Once the surface is inspected and any necessary repairs are made, ensure it is clean and free of dust, debris, or any remaining residue.
Step 2: Smooth the Surface
Start by using a medium-grit sandpaper (e.g., 60-grit) to create a smooth base. Work in small sections, gently rubbing the sandpaper over the fiberglass surface. This initial sanding helps to remove any remaining roughness from the application process. After the medium-grit sanding, move on to a finer grit (e.g., 80-grit) to further refine the surface. This step ensures that the final finish will be smooth and even. Take your time and use gentle, even pressure to avoid scratching the gelcoat.
Step 3: Wet Sanding for a Smooth Finish
For an exceptionally smooth and glossy finish, consider wet sanding. This technique involves lightly dampening the sandpaper with water, which helps to cool the sandpaper and create a smoother surface. Use a fine-grit sandpaper (e.g., 120-grit or higher) and gently rub the sandpaper over the fiberglass, ensuring the water remains on the paper. Wet sanding can be particularly useful for removing any fine scratches or imperfections that may have appeared during the initial sanding.
Step 4: Final Sanding and Preparation
Once you've achieved a smooth surface, it's time for the final sanding to prepare the fiberglass for sealing and painting. Use a very fine-grit sandpaper (e.g., 220-grit or higher) to create a smooth, glossy base. This step ensures that the gelcoat is ready to accept a sealant or paint without any rough texture. After sanding, wipe away any dust with a damp cloth to remove all debris.
Step 5: Edge and Detail Sanding
Pay close attention to the edges and details of the boat bottom. These areas require careful sanding to ensure a seamless finish. Use a finer grit sandpaper (e.g., 400-grit) to gently sand the edges, corners, and any intricate details. This step helps to create a smooth transition between the fiberglass and other components, such as the hull or transom.
By following these steps, you'll be able to achieve a professional-grade finish on your boat bottom, ensuring a smooth and durable surface that is ready for further customization and protection. Remember, patience and attention to detail are key during the sanding process to avoid any unwanted marks or imperfections.
Fixing Vapor Lock: A Guide for Boat Owners
You may want to see also
Frequently asked questions
Fiberglassing a boat bottom involves several steps to ensure a durable and smooth finish. First, prepare the surface by cleaning and smoothing any rough areas. Then, apply a layer of gelcoat to create a protective and aesthetic layer. Next, lay up the fiberglass cloth, ensuring proper overlap and tension. After that, sand the surface to achieve a smooth finish and remove any excess material. Finally, apply a topcoat to enhance the appearance and protect the fiberglass.
Selecting the appropriate fiberglass depends on various factors. Consider the boat's design, intended use, and environmental conditions. For a boat bottom, a suitable option is a woven fiberglass cloth, often in the form of a mat or cloth, which provides strength and flexibility. You can choose from different weights and weaves, such as 4 oz. or 6 oz. cloth, depending on the level of reinforcement needed.
To fiberglass a boat bottom, you'll need several tools and materials. Essential items include a respirator mask for safety, gloves, and safety goggles. You'll require a suitable fiberglass resin, a catalyst to mix with the resin, and a fiberglass cloth or mat. Additionally, have a spray gun or brush for applying the resin, a putty knife for spreading and shaping, and sandpaper for smoothing. Don't forget the necessary cleaning supplies and a primer to ensure proper adhesion.