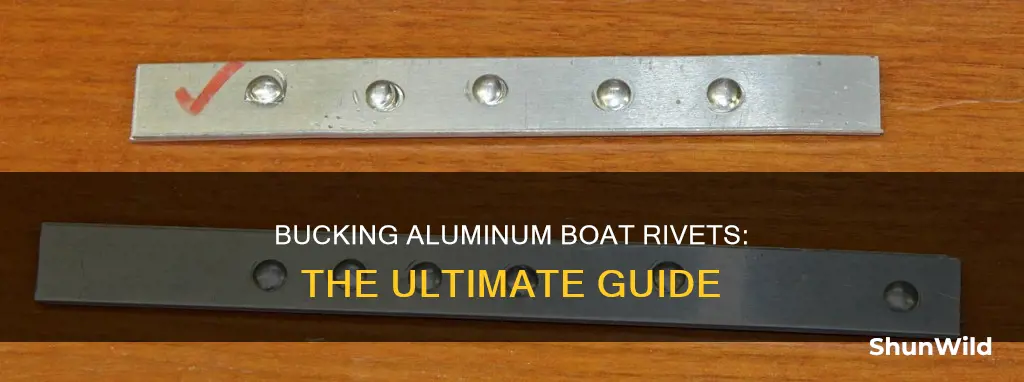
Bucking rivets on an aluminium boat is a DIY-friendly task that can be done to fix leaky rivets. To rebuck or tighten a rivet, you will need a helper or long arms. One person will hold the buck, a hunk of steel, tightly against the flat side of the rivet, while the other hammers the crimped end. An automotive bodywork dolly can be used as a buck, and a ball-peen hammer can retighten the rivet head. It is important to avoid too much hammering, as old aluminium rivets can split or break under heavy force.
Characteristics | Values |
---|---|
Tools required | Air hammer, bucking bar, 2 hammers (one heavy), ball-peen hammer, carpenter's hammer, automotive bodywork dolly, sledgehammer |
Rivet type | Solid rivets |
Rivet material | Aluminium |
Rivet size | 3/16" brazier head, 3/16" blind rivets, 1/4" |
Rivet length | 3/8", 1/2" |
Rivet quantity | 100-pack, 50-pack |
Adhesives | 5200 marine adhesive, JB Weld, JB Weld Marine, marine epoxy, flexible marine epoxy or sealant |
Other tools | Rivet gun, air compressor, pneumatic riveter, pneumatic air hammer, 2-handled rivet tool, mini sledge, bucking bar, heavy axe head, brass punch, pneumatic chisel |
What You'll Learn
Rebucking (tightening) a rivet
Prepare the Necessary Tools:
You will need a ball peen hammer or a regular hammer, a heavy object like a bucking bar or an anvil, safety glasses, and ear protection. If you have access to an air hammer, you can use that instead of a manual hammer.
Assess the Rivet:
Inspect the rivet to determine if it is suitable for rebucking. If the rivet is just seeping or slowly leaking, then rebucking is a good option. However, if the rivet is stretched or loose, rebucking may not be effective, and replacement might be necessary.
Position the Bucking Bar:
Place the bucking bar or anvil on the flat side of the rivet, which is the backside of the rivet head. This will provide a solid surface for the rivet to be tightened against.
Strike the Rivet:
Using your hammer, strike the head of the rivet firmly but with controlled force. It is recommended to use a heavier hammer, such as a 4-pound hammer, for striking the rivet head, and a lighter hammer, such as a 2-pound hammer, to hold the bucking bar in place. Two solid strikes are usually sufficient to create a flat spot on the head of the rivet, indicating that it has been successfully rebucked.
Work in a Rhythm:
If you are rebucking multiple rivets, it is helpful to work out a rhythm with your tools and strikes. This will make the process faster and more efficient, especially if you have assistance from another person.
Inspect and Repeat:
After striking the rivet, inspect the area to determine if the leak has been addressed. If the rivet is still leaking, you may need to strike it again or consider replacing it entirely.
Rebucking a rivet is a useful technique for addressing minor leaks in aluminum boats. However, if the rivet is severely damaged or loose, replacement might be the best course of action to ensure a watertight seal.
Lubricating Paddle Boat Pedals: A Step-by-Step Guide
You may want to see also
Removing an old rivet
Removing old rivets from an aluminium boat can be a tricky process, but with the right tools and techniques, it can be done successfully. Here is a step-by-step guide on how to remove old rivets:
Identify the Type of Rivet
Before starting the removal process, it is important to identify the type of rivet you are dealing with. There are two common types of rivets used in aluminium boats: solid "driven" rivets and blind rivets. Solid rivets have a head on each end, while blind rivets are installed with a puller and have a core and a locking ring. Identifying the type of rivet will help you choose the appropriate removal method.
Gather the Necessary Tools
The tools you will need depend on the type of rivet you are removing. For solid rivets, you will need a centre punch, a drill, and a bit that matches the size of the rivet. For blind rivets, you will need a punch to remove the core and locking ring, as well as a drill and bit. It is recommended to use a sharp, high-quality drill bit to prevent breakage during the process. Additionally, you may need a grinder or angle grinder with a sanding disc to remove the heads of the rivets.
Prepare the Rivets for Removal
If you are dealing with blind rivets, start by centre-punching the head of the rivet and then drilling it out. You can also use a grinder to grind off the head and expose the core. For solid rivets, use the centre punch to mark the centre of the head, then drill straight through the rivet. It is important to drill slowly and maintain a straight up-and-down motion to avoid tempering or breaking the bit.
Remove the Rivets
Once the rivets are prepared, you can begin the removal process. For blind rivets, knock out the core and locking ring using a punch. Then, drill out the head of the rivet, being careful not to enlarge the original hole. For solid rivets, simply drill out the head of the rivet. In some cases, you may need to use a punch to remove any remaining portions of the rivet.
Clean and Prepare the Area
After removing the rivets, it is important to clean and prepare the area for the new rivets. Use a wire brush or angle grinder with a sanding disc to remove any residual silicone or epoxy that may have been used in previous repair attempts. This step will ensure a clean surface for the new rivets.
Install New Rivets
Finally, you can install the new rivets following the manufacturer's instructions. It is recommended to use high-quality rivets and tools specifically designed for aluminium boat repairs to ensure a watertight seal.
Remember to work slowly and carefully during the removal process to avoid damaging the boat or enlarging the rivet holes. With the right tools and techniques, you can successfully remove old rivets from your aluminium boat and restore its watertight integrity.
Your Personality's Perfect Boat: Setting Sail in Style
You may want to see also
Choosing the right rivet length
When bucking rivets on an aluminium boat, it is important to select the correct rivet size. The rivet should be long enough to securely fasten the materials together, but not so long that it protrudes excessively or weakens the joint. Here are some factors to consider when choosing the right rivet length:
Material Thickness:
The rivet length depends on the thickness of the materials being joined. Measure the total thickness of the materials at the point where the rivet will be inserted. This measurement is known as the grip range or grip thickness. For example, if you are joining two pieces of aluminium with a thickness of 0.050 inches each, the total grip range would be 0.10 inches.
Rivet Diameter:
The rivet diameter plays a crucial role in determining the required length. As a general rule, the rivet diameter should be at least three times the thickness of the thickest sheet being joined. In the previous example, a rivet with a diameter of 0.150 inches (3 times the sheet thickness) or larger would be suitable.
Military Standard:
According to military standards, the bucked counter head diameter of the rivet joint must be larger than 1.4 times the diameter of the rivet shank. Additionally, the height of the rivet should extend to 0.3 times the diameter of the shank. These proportions ensure a strong and secure joint.
Allowance:
When calculating the rivet length, it is common to add an allowance to the total thickness of the materials. The allowance is typically around 1.5 times the rivet diameter (1.5D). This extra length ensures that the rivet can be bucked properly and provides some leeway for variations in material thickness.
Hole Preparation:
Before selecting the rivet length, it is important to consider hole preparation. The drill diameter for the hole should be slightly larger than the rivet diameter, typically by about three-thousandths of an inch. Mark the hole locations with a centre punch to ensure accurate drilling.
Practice and Testing:
It is always recommended to practice on scrap materials or similar joints before working on your boat. This allows you to test different rivet lengths and diameters to find the optimal combination for your specific application.
By considering these factors and referring to rivet size charts or calculations, you can choose the right rivet length for bucking rivets on your aluminium boat. Remember to use high-quality rivets and tools for the best results.
Boat Batteries: Self-Recharging or Manual?
You may want to see also
Using pop rivets
Pop rivets are a good option if you can only access one side of the hull. However, standard pop rivets are useless below the waterline as they have a hole through them. If you can't reach both sides, you can try a closed-end pop rivet, which is not a typical hardware store item.
To install pop rivets, you will need a pop rivet gun. This tool is designed to securely set the rivet in place. Pop rivets typically come in different sizes, so make sure to select the appropriate size for your boat.
- Identify the location where you need to install the pop rivet. Ensure that the area is clean and free of debris.
- Select the appropriate size of pop rivet for the hole. The rivet should fit snugly without being too tight or too loose.
- Insert the pop rivet into the rivet gun. The rivet gun will have a nose piece that holds the rivet in place.
- Position the rivet gun so that the rivet is aligned with the hole. Squeeze the handles of the rivet gun together firmly and hold them in place.
- As you continue to squeeze the handles, you will feel resistance as the rivet is set. Keep squeezing until you hear a distinct "pop" sound, indicating that the rivet has been securely fastened.
- Release the handles of the rivet gun and check that the rivet is properly installed. The rivet should now have a mushroom-shaped head on one side, indicating that it has been set correctly.
- If you need to remove a pop rivet, you can use a drill to grind off the head or a rivet removal tool.
Pop rivets are a convenient option for fastening materials when you have limited access to one side. However, it is important to select the appropriate type of pop rivet for your specific application, especially if it is below the waterline.
Penn Yan Boat Engine: Mercury Marine Options for 1958 Model
You may want to see also
Repairing with epoxy
Repairing leaks in an aluminium boat with epoxy is a straightforward process. The first step is to identify the source of the leak, which is usually a result of loose or leaky rivets. Once the leaky rivets have been identified, they can be tightened or replaced. If the rivets are accessible from both sides, they can be re-bucked using a rivet gun or an air hammer with a rivet setting tool. Alternatively, if the rivets are only accessible from one side, they can be tightened using a heavy hammer and a bucking bar or another heavy object to hold the rivet in place.
After tightening or replacing the rivets, an epoxy adhesive can be applied to seal the leaks. It is important to clean and dry the surface around the rivets before applying the epoxy. The TotalBoat Aluminium Boat Leak Sealer is a popular choice for repairing leaks in aluminium boats. It comes in a convenient cartridge that fits most standard caulk guns and includes mixing tips for easy application. The epoxy is sag-resistant and can be applied to vertical and overhead surfaces. It is also waterproof and forms high-strength, permanent bonds that can absorb contraction, expansion, vibration, and shock.
Another option for repairing leaks in aluminium boats is to use a repair kit such as the WEST SYSTEM Aluminium Boat Repair Kit. This kit includes G/flex 650 Toughened Epoxy, an adhesive filler, application syringes, mixing cups, reusable mixing sticks, and protective gloves. The kit also comes with detailed, illustrated instructions on how to repair leaking seams and rivets in aluminium boats.
When working with epoxy, it is important to follow the manufacturer's instructions and take the necessary safety precautions, such as wearing gloves and eye protection. Additionally, it is crucial to allow the epoxy enough time to cure before sanding or painting over it.
Jimmy's Boat Adventure: What Happened Next?
You may want to see also
Frequently asked questions
You will need a buck (an anvil-like hunk of steel), a ball-peen hammer, a carpenter's hammer, and a helper with long arms. Optionally, you can use an automotive bodywork dolly as a buck and a sledgehammer.
First, identify the leaking rivets by letting water in from outside or letting it out from inside. Then, one person holds the buck against the flat side of the rivet, while the other hammers the crimped end. Avoid heavy hammering as old aluminum rivets can split or break.
You can use pop rivets, closed-end pop rivets, or small stainless steel machine screws with acorn nuts as a stopgap solution. Additionally, flexible marine epoxy or sealant can be applied to the hole before tightening for a longer-lasting repair.
It is recommended to use solid aluminum rivets that are 3/16 x 7/16 inches in most areas, including the bottom. However, some spots may require 1/4-inch rivets. Ensure that the rivets are not too long or too short and that there is enough room for compression.